MIG welding is a versatile and quick welding process. It can be a real game changer if you need a cost-effective and fast welding solution. It conjoins metal parts using a consumable metal wire. If you want to know what is MIG welding, its working, equipment, and process, you are at the perfect place. In this article, you can learn also you need to about MIG welding.
What Is MIG Welding
As the name suggests, Metal Inert Gas (MIG) welding is a welding technique. It joins two metallic structures by melting consumable metal electrodes in the presence of an inert gas. A detailed description of what is MIG welding is below to give you a complete understanding.
The metal electrode is usually in the form of a wire that melts to create a strong and permanent bond between two metals. This wire acts both as the feeding material melted to create the join and also as the electrode.
Also called Gas Metal Arc Welding (GMAW) or simple Wire Welding, MIG welding is conducted with the shielding gas like an inert gas or Argon/CO2 gas mixture. This makes sure that oxygen or any other contaminant won’t reach the metal joint. It creates a strong joint that is suitable for the thinnest and thickest metal. The best part is that it is cost-effective, quick, and does not require any special training.
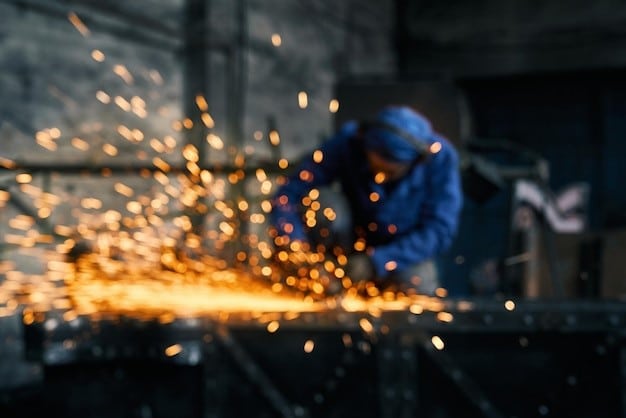
What Is MIG Welding Used For
Now that you are aware of the concept of MIG welding, you must be thinking what is MIG welding used for? Owing to its fast results, MIG welding widely appears in multiple industries. To name a few, here are some sectors that are using the MIG welding technique to get timely results.
- Automotive Industry: MIG welding is used for repairing damaged vehicle bodies, manufacturing auto parts including engine components, and in vehicle modification.
- HVAC: Metal ducts used for ventilation and heating/cooling systems are welded using MIG welding.
- Marine Industry: MIG welding serves to repair marine structures along with the assembly of some major components like decks and ship hulls.
- Construction Industry: MIG welding is used in the construction of pipelines, steel structures, and welding steel structures in concrete for a stable structure.
- Agriculture: From agriculture equipment to agriculture-related heavy machinery, MIG welding is used extensively in the agriculture sector.
- Arts: Mostly MIG welding is used in welding art structures for public display but some artists also use this welding technique for developing art through metals. Owing to its ease of use artists need no special training to apply MIG welding which makes it convenient for them to use it.
- Food industry: MIG welding serves the food industry in the manufacturing of stainless steel equipment and repairing of stainless steel components used in food processing.
- Oil and Gas industry: MIG welding serves oil refineries in welding pressure vessels, tanks, and other such essential components. It is also used to conjoin gas pipes for quick welding.
- Manufacturing Industry: MIG welding is used in manufacturing as well as repairing heavy equipment such as cranes, bulldozers, and tractors. It is also used in welding metal structures of industrial machines and repairing metal structures in the aerospace industry.
- Energy industry: From welding components of wind turbines to assembling solar panel structures, MIG welding is serving the energy sector and contributing to its superior performance.
MIG Welding Materials and Equipment
Now that you are familiar with what is MIG welding, it is time to learn about the related equipment and materials. MIG welding uses many materials and equipment. Here, we are focusing on the most essential and widely used materials and equipment.
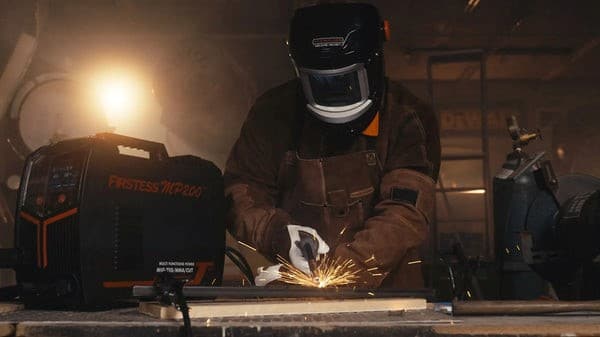
MIG Welder
The most critical equipment of MIG welding is the MIG welder. It is responsible for providing a power supply to run the welding process. It has a welding torch directed toward the weld joints to release shielding gas, welding wire, and direct electric current.
The control panel in the MIG welder is used to set the essential parameters including wire feed speed (which releases the wire at a pre-determined speed towards the welding joint), required voltage, and inert gas flow. The gas regulator releases the shielding gas when required to ensure the weld pool is secured from any sort of contamination. It also has a cooling system attached to it that cools down the machine in case of excessive usage.
Wire Feeding Mechanism
The wire feeding mechanism is very crucial and impacts the stability of the wire along with the overall reproductivity of MIG welding. Ideally, the wire feed rate should match the electric current flow for a seamless joint.
It ensures that feed rollers and liners are working perfectly at the needed pace. If the wire is fed at a considerably high speed then it can create a wide bead pool that looks aesthetically unpleasing and needs finishing. Not only that, it can also lead to cold laps where metal does not melt properly causing weak joints and can cause high spatter.
Welding Wire
The welding wire that melts to form the joint between two metals is available in multiple diameters and materials. The material and diameter are selected based on the base metal.
Commonly, solid wires are for welding aluminum, stainless steel, and steel. This wire is clamped to the welder machine and fed at an appropriate speed with the help of a wire feeding mechanism to create a stable arc, aesthetically pleasing bead pool, strong joint, and that too with the least possible spatter.
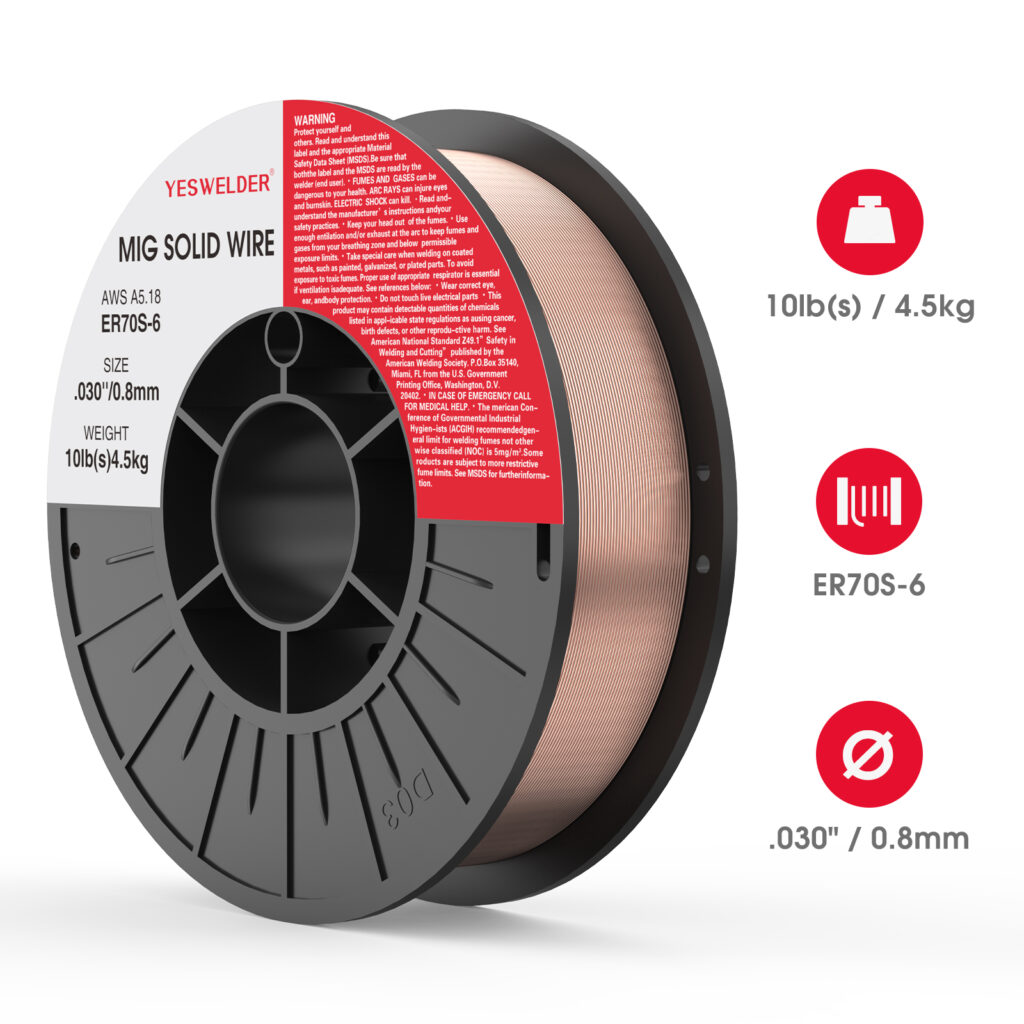
What Gas is Used for MIG Welding
Questions like what is MIG welding and what gas is used for MIG welding go hand in hand. The shielding gas is for shielding the weld pool from any sort of contamination. The gases for shielding gases are based on their application and base metal. The gases used for MIG welding are:
- Argon: It is great for welding copper and aluminum (non-ferric metals)
- CO2: Carbon dioxide gas is best for welding steel as it offers deeper penetration. But it roughens the bead quality and creates more spatters.
- CO2 and Argon mixture: A mixture of 25 %CO2 and 75% Argon gas is also used for welding. It offers great arc stability, better bead quality, penetration, and the least spatter.
MIG Welding Process
Without understanding the welding process in detail you cannot fully understand what is MIG welding. To get you acquainted with the entire process, here is a detailed overview of all the steps involved in the MIG welding process.
Pre-Welding and Setup
Before starting the welding process, you must set your welder properly. Select the welder best suited for the metal you are considering joining. Install the appropriate wire spool, and attach the welding torch/gun and shielding gas cylinder.
Once set up the machine, you now have to make sure that the metal/workpiece is placed properly. Clean the metal to remove any sort of contaminants, secure it using clamps on the welder, and attach it to the ground clamp to form the electrical circuit. Afterward, select all the appropriate parameters from wire rolling speed to gas flow rate as per the metal you are attending to.
Starting Welding
Once you are satisfied with the setup, initiate the welding process. Hold the gun at the appropriate angle, maintain the arc, and manage the head input to get the best welding results.
Post-Welding Inspection
After done with welding, inspect the metal visually and, if required, radiographically to locate any defects. If the weld seems fine then clean the metal with a brush to get rid of spatter and slag.
Safety Precaution for MIG Welding
To ensure safety during the welding process you should wear a personal protective equipment (PPE) kit. Make sure that the room has proper ventilation, fire safety materials (extinguishers), and electrical safety tools to protect you against any sort of danger from harmful gas emissions, fire eruption, and electrical breakdown.
MIG Welding Tips
Here are the tips that you should be familiar with to truly understand what is MIG welding.
Welding Gun Angle
The right welding gun angle can get consistent and high-quality results for MIG welding. The gun angle can be overhead, horizontal, vertical, or flat owing to the base metal. You also need to set work and travel angles appropriately.
Work angle stands for the position of the gun about the welding joint. Whereas, travel angle is the angle of a gun in a perpendicular position relative to the traveling welding gun which should ideally remain at 5 to 15 degrees.
The best welding gun angle depends upon the thickness of the metal you are dealing with, welding conditions, and welding speed.
As a thumb rule if you want to have butt ints then the push technique is appropriate for thin metal whereas the pull technique will serve you the best for thick metals. For lap joints and T joints, the push technique is the best whereas fillet joints require the push technique for better results.
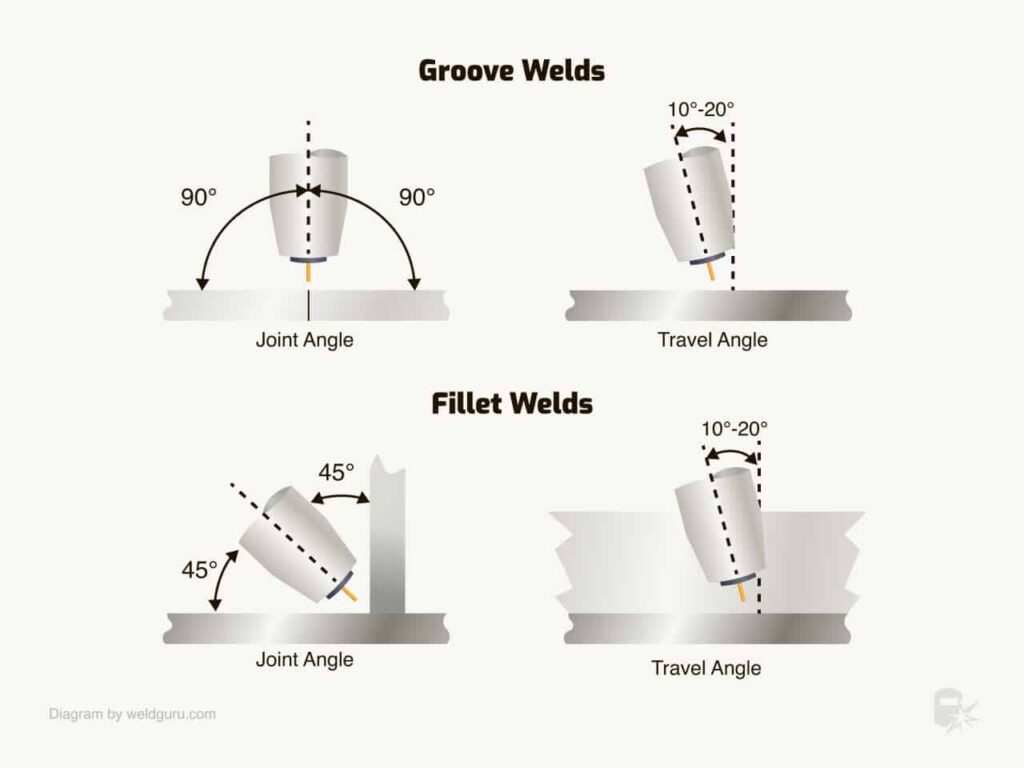
Metal Transfer Modes
Metal transfer modes exhibit the process and the filler wire (or electrode). The wire works through a welding arc into a weld pool. Here are the major modes along with the welding conditions considered the best mode option for welding:
1. Short-circuit welding: In this mode, the welding electrode creates a short circuit upon touching the metal. Afterward, the wire melts and becomes a part of the weld pool in the form of small drops.
Short-circuit welding is perfect when dealing with thin metals. Owing to its low heat input requirement, it suits overhead and vertical gun angle positions and is most suitable for filling gaps in materials with poor fit-up.
2. Globular transfer: The metal melts and connects with the electrode wire in the form of large droplets. This makes it part of the weld pool through the force of gravity. It can lead to a large amount of spatter which is why it is the best mode if you are using horizontal or flat gun angles. It is great to treat thick metals that require deep penetration.
3. Spray welding: The wire constantly melts in the form of tiny drops that attach to the metal as a fine spray in the weld pool. It requires high heat input which makes it suitable for flat and horizontal torch positions. Also, it is great to treat thick metals which require high deposition.
4. Pulsed pool: The current in this mode reaches a high peak and low background amperage. At high peak current, the metal melts and transfers its drops to the weld pool whereas the background current ensures to maintain arc.
It is the most versatile mode as it is suitable for all welding gun positions and both thick and thin metals. This model is perfectly suitable for treating materials that act sensitively against high heat input.
Pull or Push MIG Welding
The push welding technique moves the welding gun along the direction of the weld travel away from the weld pool. This technique shows better visibility of the weld pool and creates low spatter but results in shallow penetration. It is great to combine thin metals. In contrast, the Pull MIG welding technique requires moving the welding gun in a different direction than the weld travel towards the pool. It allows deeper penetration and forms a strong weld. It is appropriate for thick metals.
Conclusion
MIG welding is a pocket-friendly, fast, and effective welding technique. It melts a consumable wire electrode in the presence of high-voltage electricity to join two metals through a strong bond. MIG welding uses Argon, CO2, or a mix of both gases as a shielding gas to protect the weld from contamination.
The MIG welding process involves setting up the welder, metal piece, and parameters. Following is initiating welding, and inspecting the post-welded metal for any inspection while taking all safety precautions.
To get the best results from MIG welding, make sure that the welding gun angle is at an appropriate degree as per the metal you are dealing with. The most important is to choose the best MIG machine to get the desired weld quality. YesWelder provides high-quality MIG welding machines at affordable prices, making the welding project more efficient.
FAQ
What materials cannot be welded using MIG welding?
You cannot weld together dissimilar metals using MIG welding. For instance, you cannot weld together copper with aluminum. Also, nonmetallic structures like wood, plastic, and composites cannot be welded using MIG welding.
Why is MIG welding more pocket-friendly than TIG welding?
MIG welding is inexpensive in comparison to TIG welding. The needed machinery and supplies are low-cost and easily available in the market. Moreover, it doesn’t require any skilled training and requires less time whereby it consumes less voltage which makes it a pocket-friendly welding process.
Does MIG welding use AC or DC?
MIG welding uses the power source of DC (direct current) to weld the metals together owing to its constant supply of voltage. It helps in forming a stable arc, weld penetration, improves bead quality, and causes less spatter.