TIG welding is a versatile method used in many industries, including aerospace and automotive manufacturing. One important aspect of successful TIG welding is using the TIG welder with a proper argon regulator. An argon regulator helps control the flow and pressure of argon gas, which protects the weld from contamination and keeps the welding arc stable. This results in cleaner, higher-quality welds. In this guide, we’ll explain why regulators are important, explore the different types available, and provide tips on choosing the best one for your needs.
Shielding Gas for Welding
In TIG welding, shielding gas protects the weld area from contamination and oxidation. Different gases are used for various welding processes, and understanding their roles can help you buy the best regulator according to the required needs.
Inert Gases
Inert gases do not react with the weld pool or the surrounding atmosphere. Argon is the most commonly used inert gas in TIG welding. It provides a stable and consistent arc, which is crucial for producing clean, high-quality welds. Argon is effective because it creates a protective shield around the weld, preventing oxygen and other contaminants from affecting the weld pool. This results in smoother and stronger welds, making argon a preferred choice for many welders.
Reactive Gases
Reactive gases, such as oxygen and carbon dioxide, are not typically used in TIG welding. These gases can react with the weld pool, leading to oxidation and other unwanted effects. However, they are often used in different welding processes like MIG welding, which can help stabilize the arc and improve weld penetration. In TIG welding, using reactive gases can compromise the quality of the weld, so they are generally avoided.
Semi-Inert Gases
Semi-inert gases like helium can be used in certain TIG welding applications. Helium is not entirely inert, but it provides some benefits. It increases the heat input into the weld, which can help weld thicker materials or when deeper penetration is needed. Helium is often mixed with argon to balance the advantages of both gases. However, helium is more expensive than argon and can be harder to control. Therefore, it is used less frequently and typically only in specific situations where its benefits outweigh its drawbacks.
What Is an Argon Regulator
It is a device that controls the flow and pressure of argon gas from a cylinder to the welding torch. It ensures a steady and consistent supply of gas, which is important for high-quality welding. With a regulator, the gas flow would be more stable, leading to better welds.
The regulator connects directly to the gas cylinder. It reduces the high pressure of the stored gas to a usable level. Most regulators have a pressure gauge showing the cylinder’s gas pressure. This helps the welder know how much gas is left and when to replace the cylinder.
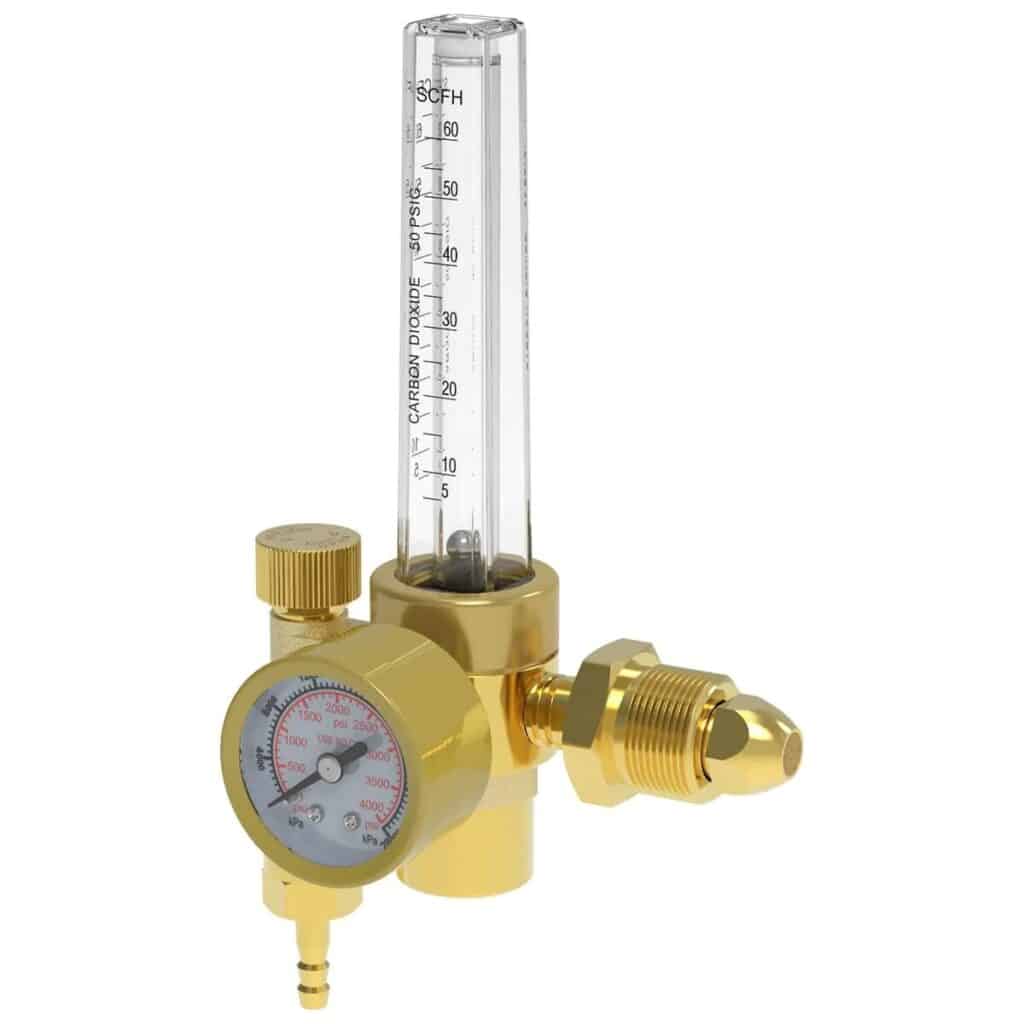
There are different types of argon gas regulators, each designed for specific needs. Single-stage regulators reduce the pressure in one step, making them simple and cost-effective. They are suitable for general welding tasks. However, dual-stage regulators are preferred for applications requiring more precision. They reduce the pressure in two steps, providing a more consistent flow.
Flow control is an important feature of gas regulators. Many regulators come with an integrated flowmeter, allowing welders to set and monitor the gas flow rate accurately. Proper gas flow protects the weld from contamination and ensures a stable arc.
A good regulator always has adjustability controls by default because Welders need to adjust the gas flow based on the specific requirements of their project. A regulator with precise adjustment capabilities helps achieve the best results.
Types of Argon Regulators
Regulators are essential for achieving optimal results in TIG welding, but various types of regulators are available, each designed to meet different needs and preferences. Understanding the differences between these types can help you select the best one for your welding projects.
Quick Table for the best selection
Type of Regulator | Advantages | Disadvantages |
Single-Stage Regulator | Cost-Effective, Easy to Use, Compact | Pressure Variations, Less Control |
Dual Argon Regulator | Precise Control, Consistent Output, Better Performance | Higher Cost, Complexity |
Argon Flowmeter Regulator | Accurate Flow Monitoring, Enhanced Control, Versatile | Cost, Size |
Argon Pressure Regulator | Consistent Pressure, Durability, Versatility | Cost, Complexity |
1. Single-Stage Regulator
A single-stage regulator is a common type of regulator. It reduces the high pressure from the gas cylinder to a usable level in one step. This type of regulator is cost-effective and straightforward, making it a practical choice for a range of welding applications in both small-scale and larger operations.
How It Works
In a single-stage regulator, gas flows from the cylinder through a valve that reduces its pressure. The regulator’s diaphragm responds to changes in pressure, maintaining a consistent flow of gas. While the output pressure can vary slightly as the cylinder pressure drops, single-stage regulators are generally sufficient for most basic welding tasks.
Advantages of Single-Stage Regulator
- Single-stage regulators are typically more affordable than dual-stage regulators.
- Their simple design ensures ease of use and is beneficial for operators at all levels of experience.
- They are smaller and lighter, making them easy to handle and transport.
2. Dual Argon Regulator
A dual argon or two-stage regulator provides more precise control by reducing the gas pressure in two steps. This ensures a steadier and more consistent flow of gas, which is critical for high-precision welding tasks.
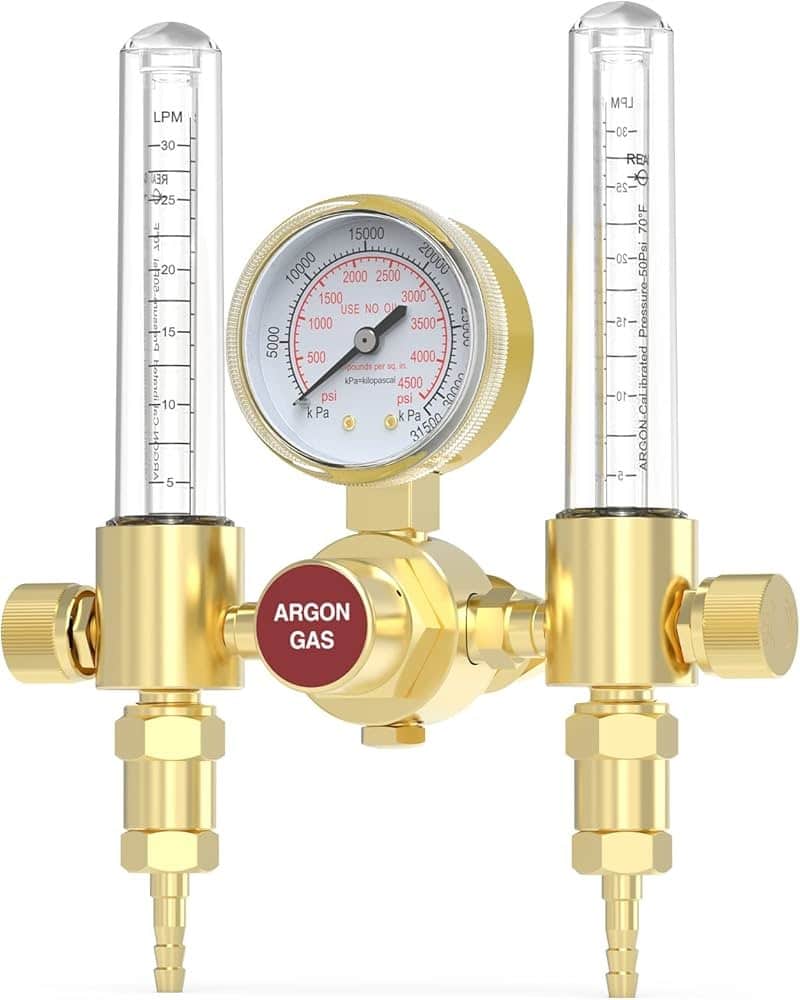
How It Works
The gas pressure is first reduced to an intermediate level in the first stage in a dual-stage regulator. Then, in the second stage, the pressure is further reduced to the desired working level. This two-step process minimizes pressure fluctuations, providing a more stable gas flow.
Advantages of Dual Argon Regulator
- Dual-stage regulators offer better control over gas flow, making them ideal for precision welding.
- They provide a more consistent output pressure, vital for maintaining weld quality.
- These regulators are well-suited for professional welders and industrial applications where accuracy is important.
3. Argon Flowmeter Regulator
An argon flowmeter regulator combines a pressure regulator with a flowmeter, allowing welders to accurately monitor and adjust the gas flow rate. This type of regulator is beneficial for TIG welding, where precise gas flow is critical to achieving high-quality welds.
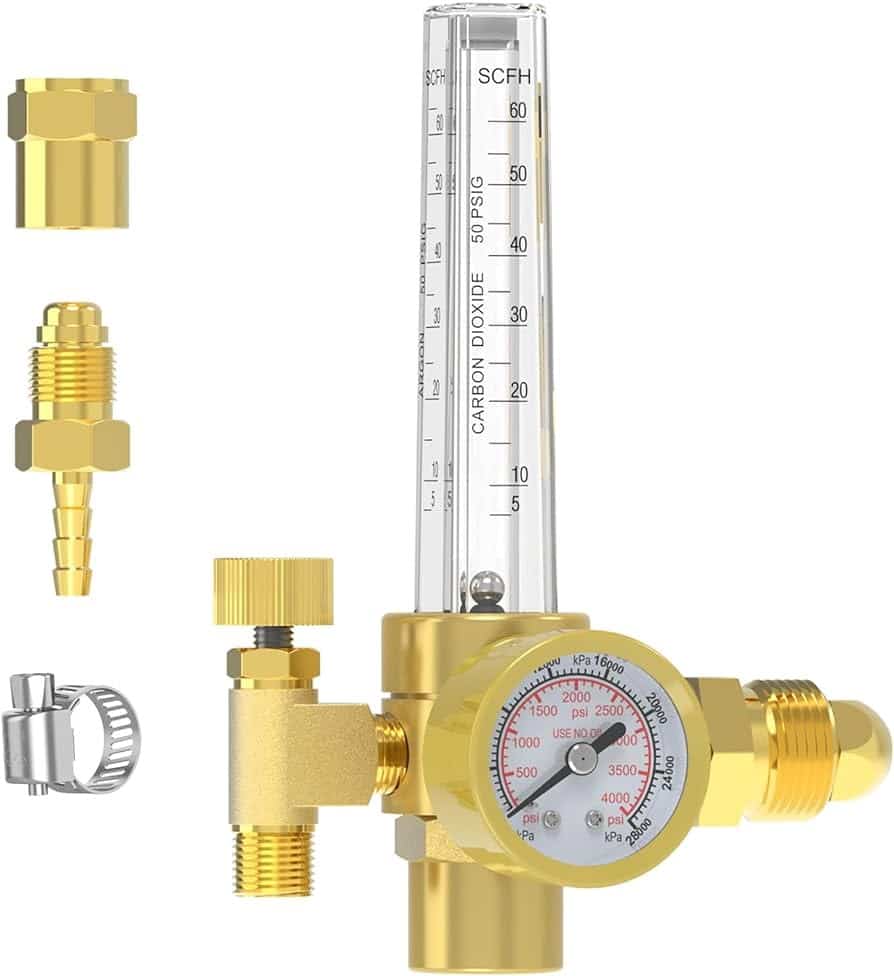
How It Works
The regulator’s flowmeter visually indicates the gas flow rate, usually measured in cubic feet per hour (CFH) or liters per minute (LPM). The welder can adjust the flow rate to match the specific requirements of the welding task, ensuring adequate shielding and protection of the weld pool.
Advantages of Argon Flowmeter Regulator
- The flow meter allows for precise monitoring and adjustment of the gas flow rate.
- This type of regulator provides greater control over the welding process, leading to better weld quality.
- Flowmeter regulators offer versatility, making them suitable for multiple welding processes.
4. Argon Pressure Regulator
An argon pressure regulator controls the pressure of argon gas, ensuring it remains within the desired range. Pressure regulators are essential for maintaining consistent welding conditions and preventing fluctuations that affect weld quality.
How It Works
Pressure regulators are designed to withstand the high pressures of gas cylinders. They reduce the gas pressure to a safe and usable level, allowing for precise control during the welding process. Some pressure regulators also come with an integrated flowmeter, offering pressure and flow control in one unit.
Advantages of Argon Pressure Regulator
- They maintain a consistent pressure, which is the key to high-quality welds.
- High-quality pressure regulators are built to last and have robust construction and materials.
- They can be used in various welding applications, providing flexibility for different projects.
How to Choose the Right Argon Regulator
Here are some essential factors listed step by step in the flow chart to help you select the best argon regulator:
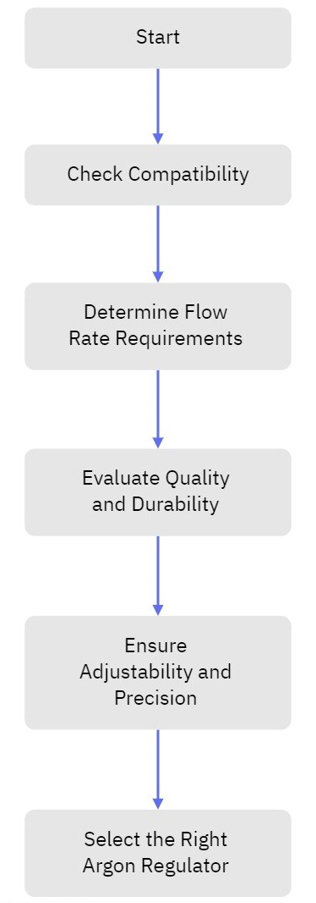
Compatibility
First and foremost, ensure that the argon regulator is compatible with your welding equipment and gas cylinder. Different regulators have different connection types, so matching the regulator with the fittings on your gas cylinder is essential. Check the pressure ratings to ensure the regulator can handle the pressure of your argon cylinder.
Using a regulator that isn’t compatible can lead to gas leaks or insufficient gas flow, which can compromise weld quality and safety. Most regulators are designed to fit standard connections, but double-checking compatibility is always a good practice. This simple step can prevent many potential issues down the line.
Flow Rate Requirements
Different welding tasks require different gas flow rates. For example, welding thicker materials or performing complex welds might require higher gas flow rates to ensure adequate shielding. On the other hand, welding thin materials might require lower flow rates to avoid excessive gas usage.
When choosing an argon regulator, look for one that allows you to adjust the flow rate to meet the specific needs of your welding projects and operational needs. Some regulators come with integrated flowmeters, which visually indicate the gas flow rate. This feature ensures precise control over gas flow, which is important for achieving consistent quality in welding tasks.
Quality and Durability
Investing in a high-quality argon gas regulator is essential for long-term reliability and performance. Look for regulators made from durable materials like brass or stainless steel. These materials resist corrosion and wear, ensuring the regulator will last through many welding projects.
A well-constructed regulator not only lasts longer but also provides more consistent performance. High-quality regulators maintain stable gas flow and pressure, which is essential for achieving clean and robust welds. Investing in high-quality regulators may involve a higher initial cost, but it results in long-term savings and superior weld quality, making it a wise choice for large-scale operations.
Adjustability and Precision
The ability to fine-tune the gas flow and pressure is essential for precise welding tasks. Look for a regulator with adjustable settings to make exact adjustments. This feature is vital for TIG welding, where consistent gas flow is crucial to prevent contamination and achieve high-quality welds.
Precision in gas flow and pressure adjustments help maintain a stable arc and avoid weld defects. Regulators with precise adjustability ensure that you can tailor the gas flow to the specific requirements of each welding project, leading to better control and improved results.
Why YesWelder can be your best choice?
YesWelder is a leading brand for argon and other gas regulators, known for delivering reliable and high-performance solutions suitable for various welding projects and solutions. YesWelder provides an extensive range of welding machines, equipment including rehulators, and accessories, all recognized for their exceptional quality and performance. Their regulators are engineered to deliver exceptional control and reliability, making them a preferred choice for professional welders seeking high-performance solutions in demanding welding projects.
YesWelder’s commitment to quality and innovation ensures that its products meet the high standards required for successful welding. Choosing YesWelder products means investing in equipment that enhances operational efficiency and delivers top-tier welding results.
Final Words
Selecting the proper argon regulator is essential for achieving optimal TIG welding results. Each type of regulator, whether single-stage, dual-stage, flowmeter, or pressure regulator, offers unique advantages. Understanding these differences helps you make in buying the regulator based on your welding needs. Buying a high-quality regulator ensures consistent gas flow and pressure, leading to superior weld quality. Reputable brands such as YesWelder offer reliable and durable regulators, designed to meet the rigorous demands of diverse welding applications. Choosing the appropriate regulator enhances your welding efficiency and overall performance, making your projects more successful.
FAQs
What is the primary function of an argon gas regulator in TIG welding?
A regulator controls the flow and pressure of argon gas to ensure a stable and consistent delivery, essential for protecting the weld pool from contamination and maintaining a stable arc.
Why is argon commonly used as a shielding gas in TIG welding?
Argon is inert and prevents oxidation, ensuring clean and strong welds. Its density effectively covers the weld area, providing optimal protection.
How do I choose between a single-stage and dual-stage argon regulator?
Single-stage regulators are suitable for general use. Dual-stage regulators offer precise control and consistent flow, ideal for professional applications requiring high accuracy.
What are the benefits of using an argon flowmeter regulator?
Argon flowmeter regulators accurately monitor and adjust the gas flow, which is crucial for achieving high-quality TIG welds through precise gas control.
Can I use the same regulator for different welding applications?
Yes, many regulators are versatile. For best results, ensure the regulator meets the specific requirements of each task, such as flow rate and equipment compatibility.