The automotive industry relies heavily on welding to assemble vehicles. As automakers seek lighter, stronger, and more efficient cars, modern welding technologies are transforming manufacturing. New techniques like laser welding and friction stir welding enable more versatility in design and materials. At the same time, automation and robotics boost precision and productivity on the factory floor. Artificial intelligence and augmented reality also open new possibilities for optimizing the welding process.
This article explores the innovations in welding technology in the automotive industry, from equipment to techniques to smart solutions.
Welding in Automotive Manufacturing
Welding is an essential process in auto manufacturing. As automakers push for lighter, more efficient vehicles, they are turning to advanced welding techniques that enable new designs and materials. Let’s explore the critical role welding plays across automotive production.
Modern vehicles contain thousands of welded parts. Welding fuses components to create durable, lightweight structures from the chassis and powertrain to exterior panels and interior features. It also joins dissimilar metals and allows flexible designs not possible with other fastening methods. From concept to assembly line, welding enables automakers to build the cars of the future.
Welded Vehicle Components
Virtually every part of a car contains welds, from small welded brackets to structural unibody frames. Common components joined by welding include:
- Body panels – Doors, hoods, trunk lids, and exterior body panels consist of sheet metal welded together into intricate shapes. Welding allows curved designs and mixed materials.
- Chassis and suspension – The chassis frame, suspension arms, and subframes rely on welds for durability under load. Welding assembles custom tubular shapes from steel alloys.
- Powertrain and drivetrain – Engine blocks, transmission cases, drive shafts, and exhaust components are welded for leak-proof, robust structures. Welds withstand vibration and torque stress.
- Interior features – Seats, seatbelts, consoles, and trim panels use welds for seamless assembly and installation. Welding joins rails, brackets, hinges, and hardware.
- Electrical systems – Battery trays and junction boxes are welded to protect sensitive electronics. Welded seams prevent corrosion that could cause electrical failure.
In short, welding touches nearly every part of a vehicle. It creates optimized designs combining strength, efficiency, style, and functionality.
Welding Processes in Vehicle Production
Automotive welding utilizes various techniques tailored to different components and materials. Common methods include:
- Resistance spot welding – Joins overlapping sheet metal with an electric current. Widely used for high-speed body assembly.
- Laser beam welding – A focused laser melts and fuses metal with minimal heat input. Ideal for fragile electronics.
- Arc welding – Uses an electric arc to melt an electrode and base metal. Versatile for metals of different thicknesses.
- Friction stir welding – A rotating tool generates heat to bond materials without melting them. Suitable for lightweight alloys.
- Robotic welding – Programmable robots boost precision and productivity in high-volume welding.
Automakers combine these processes strategically based on part size, material properties, production volume, and design needs. For example, aluminum alloys may require friction stir or laser welding, while high-strength steels are joined with arc or resistance welding. Optimized welding maximizes manufacturing efficiency.
Importance of Welding for Vehicles
Welding is indispensable for building safe, robust, and lightweight vehicles with lower environmental impact. Benefits of welding include:
- Strength – Welding creates continuous bonds stronger than mechanical fasteners like bolts. Welds maintain integrity under crash forces.
- Lightweight – Welded designs minimize weight while preserving strength. This improves fuel efficiency and handling.
- Flexible design – Welding enables complex shapes and mixed material construction not possible otherwise.
- Speed – Automated welding stations join components faster than mechanics with hand tools.
- Safety – Robotic welding removes workers from hazardous fumes and sparks in the factory.
- Sustainability – Advanced techniques like laser welding minimize waste and energy use.
- Cost-effectiveness – Welding helps reduce expenses for materials, labor, and maintenance over a vehicle’s lifetime.
In short, welding facilitates the engineering feats necessary for manufacturers to thrive in an innovative and competitive automotive industry. Mastering the latest techniques unlocks new realms of possibility in vehicle design.
Modern Welding Technologies in the Automotive Industry
The automotive industry relies on advanced welding technologies to manufacture vehicles efficiently, safely, and cost-effectively. New techniques enable automakers to work with innovative materials, achieve precise welds, and automate production. This section explores key welding processes transforming auto manufacturing.
MIG Welding
MIG (metal inert gas) welding, sometimes known as GMAW (gas metal arc welding), is a versatile process suitable for high-volume vehicle production. An electric arc forms between a consumable wire electrode and the workpiece metal, melting both to create the weld. An inert shielding gas protects the weld from contamination.
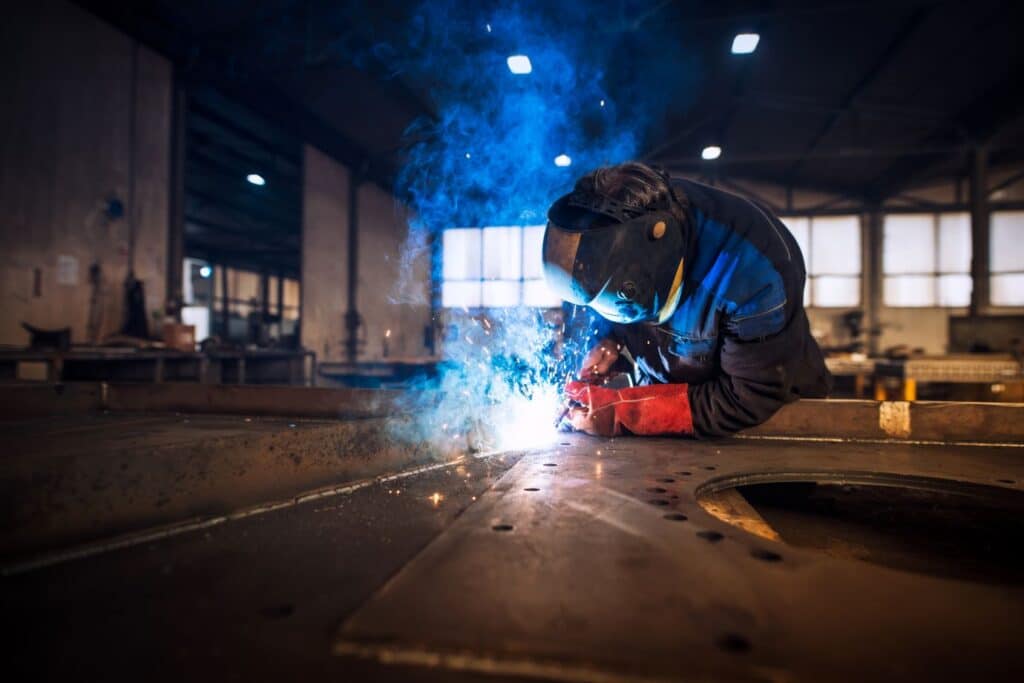
Benefits of MIG welding include:
- Speed – Deposition rates are higher than manual welding methods.
- Adaptability – A MIG welder can weld thin sheet metal to thick plates of varying materials.
- Ease of use – Operator skill requirements are moderate compared to other welding processes.
- Quality – MIG produces strong, clean welds when performed correctly.
In automotive plants, MIG welding joins body panels, frames, and components where speed and flexibility are priorities. Automation systems with MIG torches can rapidly weld high volumes of parts consistently.
FCAW Welding
Flux-cored arc welding (FCAW) is a variant of GMAW. It uses a wire electrode containing flux materials to shield the weld, instead of an external gas. The flux produces slag that must be chipped away post-weld.
Advantages of FCAW include:
- Thicker welds – The flux-cored wire supports higher deposition rates.
- Portability – External shielding gas is not required.
- Out-of-position use – Gravity has less impact on the molten weld pool.
- Cost – No need to get shielding gases.
FCAW is ideal for welding thicker chassis components and fabricating frames. The high deposition rate and portability suit field construction conditions. Automakers use FCAW for subframes, suspensions, hitches, and structural reinforcements.
GTAW Welding
Gas tungsten arc welding (GTAW), also known as TIG welding, uses a non-consumable tungsten electrode and inert gas shielding to produce precise, high-quality welds. An electric arc heats the workpiece while a filler rod adds material to the joint.
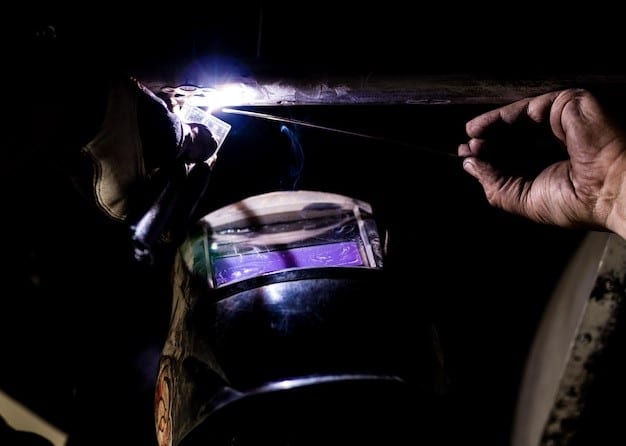
Benefits of GTAW include:
- Precision – The concentrated arc enables narrow, deep welds even on thin metals.
- Quality – A TIG welder produces the cleanest, strongest welds of any welding process.
- Versatility – It can weld stainless steel, aluminum, magnesium, titanium, and other metals.
- Appearance – GTAW makes attractive bead profiles ideal for visible welds.
In vehicle fabrication, GTAW creates leak-proof seals on pressure vessels, airbags, radiators, and hydraulic components. It is also used for roll cages, chassis, suspension arms, and other structural parts where weld strength is critical.
Resistance Spot Welding
Resistance spot welding is the primary joining method for sheet metal auto bodies. Two shaped copper alloy electrodes clamp the metal sheets under pressure. A strong electrical current flows through the sheets, heating and fusing them at the spot. The typical weld takes under a second to complete.
Benefits of resistance spot welding include:
- Speed – Modern spot welders produce over 600 welds per minute.
- Automation – Robotic spot welding stations create extremely high weld rates.
- Adaptability – Spot welding readily joins coated, multi-metal, and lined panels.
- Cost-effectiveness – No filler material is required during the process.
Resistance spot welding assembles nearly all exterior vehicle panels. Thousands of spot welds bond hoods, doors, and body sides into lightweight unified structures. Laser-enhanced and medium-frequency variants further improve process flexibility.
Laser Welding
Laser welding focuses a high-power density laser beam onto the joint area to melt and fuse metal. The laser can produce narrow, deep welds in seconds without contact or force.
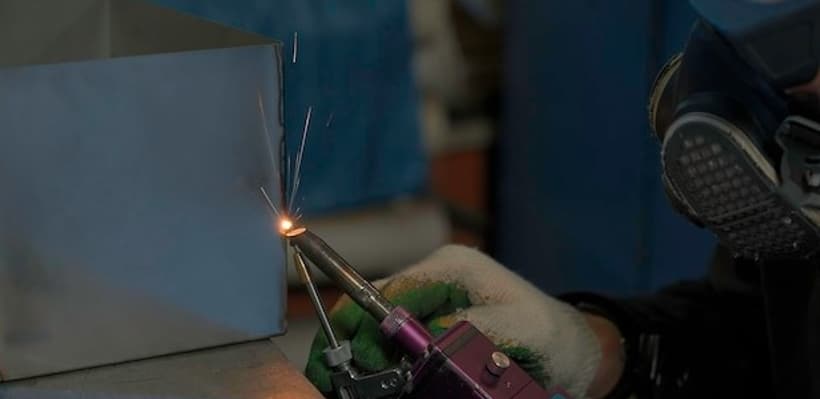
Laser welding benefits include:
- Precision – The laser achieves smaller, more intricate welds than traditional welding.
- Speed – Laser welding is up to 10 times faster than conventional spot welding.
- Quality – Laser welds have less distortion and warping due to the concentrated heat input.
- Appearance – Laser welding minimizes the visible heat-affected zone around welds.
Laser welding is advantageous for sensitive electrical components and closures. Applications in vehicles include battery packs, electric modules, door and hood seals, fuel tanks, tailor-welded blanks, and tailored tubes. Automated laser welding stations help manufacturers reduce cycle times.
Friction Stir Welding
Friction stir welding (FSW) uses a rotating tool pressed into the joint to generate frictional heat that plasticizes and consolidates the materials. Unlike fusion welding, FSW does not melt the base metals. Benefits include:
- Material versatility – FSW can weld lightweight alloys like aluminum and magnesium not easily joined by other methods.
- Strength – FSW produces welds as strong as or stronger than base metals.
- Quality – The solid-state process minimizes defects such as porosity and cracking.
- Environmentally friendly – FSW does not use filler material, flux, or shielding gas.
Automakers use FSW for aluminum panels and structures in doors, hoods, trunks, and liftgates. The aerospace industry also relies on FSW for joining lightweight alloys. The process accommodates the auto industry’s growing use of aluminum to reduce vehicle weight.
Hybrid Welding
Hybrid welding combines two or more welding processes, such as GMAW and laser welding, to benefit from the strengths of each. The combined energy sources penetrate deeper and faster than either process alone.
Advantages of hybrid welding include:
- Speed and penetration – Hybrid lasers boost arc welding speed while maintaining penetration.
- Gap tolerance – The laser helps bridge gaps the arc alone cannot.
- Quality – The hybrid process enhances arc stability and control.
- Cost – More affordable laser heads reduce capital investment.
Hybrid welding is ideal for doors, liftgates, and autobody panels over 1 mm thick. Automakers can modify existing MIG or spot welding systems by adding a lower-power laser for a low-cost productivity upgrade.
The optimal welding technology depends on factors like materials, part size, production volume, and quality needs. By utilizing the latest welding advances, automakers gain flexibility in manufacturing reliable, innovative vehicles. With improved speed, precision, and adaptability, modern welding processes drive the future of automotive fabrication.
Future Trends of Welding Technology
The welding industry is constantly evolving to meet the demands of manufacturers worldwide. As materials, designs, and production needs change, new welding techniques emerge. Here we explore two rising trends that will shape the future of automotive welding: automation & artificial intelligence (AI), and sustainable welding processes.
Automation and AI Integration
Automating welding operations with robotics boosts shop floor productivity, while AI software enhances control and quality assurance. Robotic welding systems can rapidly and consistently join components once laboriously welded manually. With AI-powered analytics, these networks detect imperfections and optimize procedures on the fly.
Robotic welding offers advantages like:
- Higher production with 24/7 operation
- Improved precision and consistency over human welders
- Scalable capacity by adding modular stations
- Reduced strain injuries for workers
- Stronger welds due to advanced sensing and process refinements
Meanwhile, AI analyzes real-time vision and thermal data to identify weld defects immediately. Adaptive algorithms then tune the equipment settings to correct and prevent issues. This self-optimizing approach minimizes rework and downtime.
AI-guided welding automation enables automakers to manufacture better vehicles faster. As the technology matures, such networks will become more prevalent across auto plants.
Sustainable Welding
With rising environmental awareness, manufacturers are adopting eco-friendly welding processes. This sustainability trend has two key aspects:
1. Energy efficiency – Modern welding machines conserve electricity during idle periods. Some recover and recycle excess heat using thermoelectric generators. Efficient robotic cells also outpace manual welding’s energy use.
2. Waste and emission reduction – Processes like laser welding and friction stir welding minimize consumable use and hazardous fumes. Closed-loop water systems conserve water. Robots improve material utilization and reduce overspray.
Other green welding initiatives include:
- Recycling expended electrodes and wire stubs
- Using renewable energy sources for welding operations
- Investment casting to reduce waste from subtractive machining
- Training personnel on sustainability best practices
By optimizing energy, water, materials, and emissions, automakers can enhance environmental performance while saving on production costs. Sustainable welding will only grow more vital as global eco-awareness increases.
Conclusion
The automotive industry relies heavily on welding, which has become significantly more advanced in recent years. New techniques like MIG, TIG, laser, and friction stir welding enable lightweight, high-strength designs critical for vehicles today. Meanwhile, automation and AI drive efficiency and quality control on the factory floor. Eco-friendly processes also reduce environmental impact.
With innovative welding technologies, automakers can manufacture revolutionary products that meet the demands of the future – from EVs to self-driving cars. The meteoric rise of welding has transformed auto fabrication, and even greater possibilities lie ahead as research continues to push boundaries. Advanced welding equips automakers to build the next generation of vehicles.
FAQs
Q: How has robotic welding improved consistency in auto manufacturing?
A: Robotic welders perform repetitive tasks identically every time, eliminating human errors and fatigue that can cause weld defects. Their precision optimizes quality control.
Q: Which auto parts are the best candidates for laser welding?
A: Laser welding is ideal for small, intricate components like battery tabs, electronic modules, medical devices, and jewelry found in vehicle interiors.
Q: How does MIG welding minimize environmental impact?
A: MIG’s wire electrode causes less waste and fumes than a stick welding machine. Combined with cleaner shielding gases like argon, MIG is more eco-friendly.
Q: What safety benefits does automated welding offer?
A: Robots perform dangerous welding tasks in hot, sparking environments, keeping workers further from hazards and improving factory safety.
Q: How does welding benefit electric vehicle design?
A: Laser and friction stir welding enables lightweight aluminum and magnesium structures that lower EV weight to extend battery range.