Stick welding is also known as Shielded Metal Arc Welding. This is a manual arc welding process that uses electrodes to lay the weld. These electrodes are coated in flux which gives off vapors during the welding process. An electric current from a welding power supply forms an electric arc between the electrode and the metals to be joined. This current can be either AC or DC, though DC is more commonly used due to its ability to provide a more stable arc and higher-quality welds.
The vapors serve as a shielding gas and protect the welding area from being contaminated. It is also important to note that stick welding is the only method that produces its own shielding gas. Other welding methods require getting this shielding gas which makes them costlier as compared to stick welding. Stick welding is most popular in construction, shipbuilding, and heavy maintenance.
Applications of Stick Welding
Stick welding is one of the most versatile forms of welding. As a result, it serves various applications across different industries. Here are some of the main applications of stick welding:
Shipbuilding Applications
Stick welding is heavily used in shipbuilding as it can create strong welds. These welds are known to be durable and long-lasting. This form of welding is ideal for outdoor applications. As a result, the windy conditions often seen in shipyards are best worked in using stick welding. Stick welding is used to weld structural components, repair hulls, and maintain ships so they remain safe and sound.
Construction Applications
Stick welding machine is popularly used in the construction industry for creating steel frameworks. This is important for the construction of buildings, bridges, and other infrastructure. The best thing about stick welding is that it’s portable which allows for on-site work. This can be done even in bad weather conditions. Stick welding is used in the assembly or repair of beams, columns, and girders.
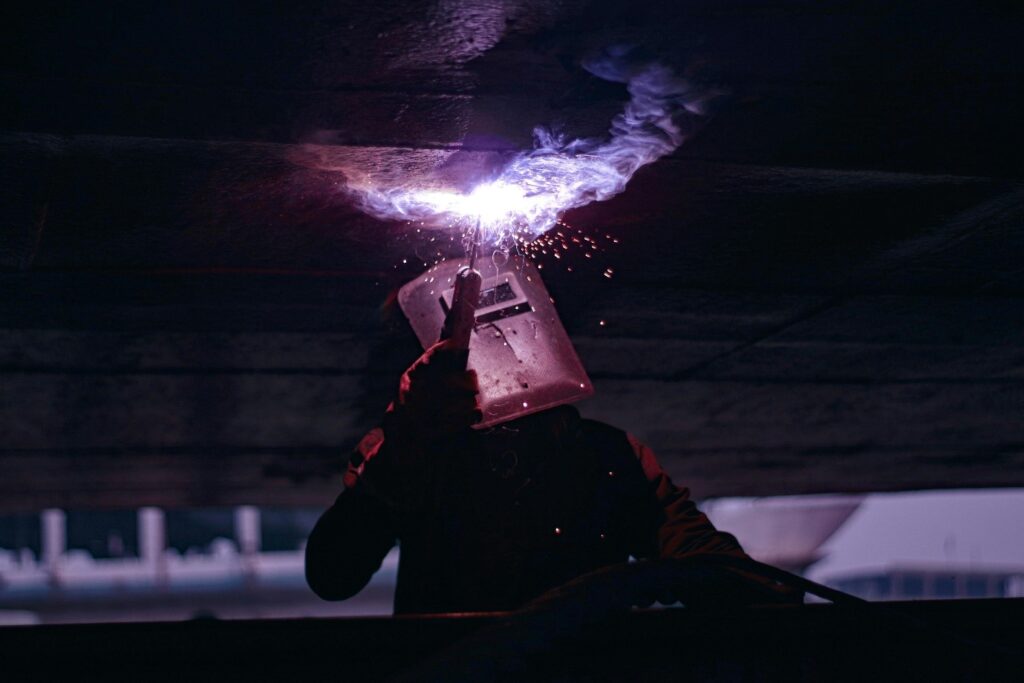
Manufacturing
Stick welding is often used in the manufacturing industry for producing and assembling heavy machinery and metal products. This industry prefers stick welding because it is able to join together a wide range of metals. This includes stainless steel and cast iron. Moreover, stick welding can create products with durability. It is popular in manufacturing for its simplicity and effectiveness.
Structural Welding
The structural welding process involves joining steel structures together. These structures include pipelines, tanks, pressure vessels, and others. Stick welding can produce high-quality welds in different positions and various environments. As a result, this makes it suitable for structural welding applications. It ensures that the structures maintain their integrity no matter the conditions.
Steel Fabrication
The steel fabrication process involves creating custom metal parts and structures. This can be anything from small brackets and supports to large and complex frameworks. Stick welding is popularly used in steel fabrication because it produces strong welds. These welds are reliable and adaptable which is why it is preferred in steel fabrication for creating custom structures.
Advantages of Stick Welding
Stick welding is popular among welders because it offers various advantages to different industries. This method is also versatile, cost-effective, and easy to use. It offers benefits to both beginners and professionals in this industry. Here are some of the key advantages of stick welding:
Versatility and Adaptability
Stick welding is heavily used because of its versatility and adaptability. This makes it compatible with a wide range of metals which include steel, stainless steel, cast iron, and aluminum. It is important to note that this method does not require an extra shielding gas. Stick welding produces a shielding gas of its own. This makes stick welding a suitable choice for various applications and environments.
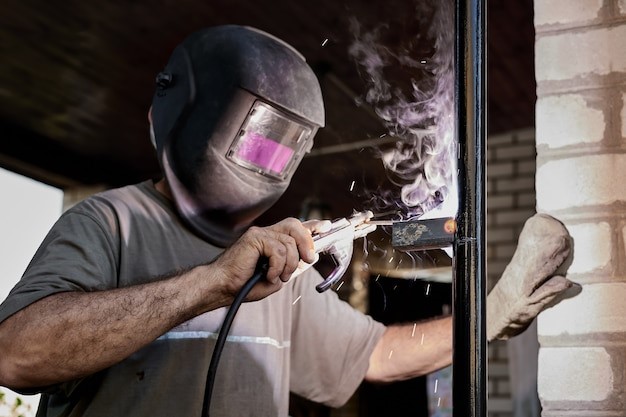
Ease of Use
Another popular feature of stick welding is that it is easy to use. Stick welding requires minimal equipment which makes it easy to set up. As a result, it is popular among the beginners of the industry. Stick welding consists primarily of a welding machine and electrodes. This method is ideal for quick repairs and small-scale projects because it is easy to set up anywhere in any environment.
Cost-Effectivity
Stick welding is often known as the most cost-effective type of welding. The equipment needed for this method is relatively inexpensive compared to other welding methods. Moreover, the consumable electrodes are affordable and there is no need for shielding gas in this process. Stick welding is a good budget-friendly option for individual welders who are looking to manage costs.
Disadvantages of Stick Welding
While stick welding boasts numerous advantages, it also comes with its own set of challenges and limitations. Understanding these disadvantages is crucial for determining when and where this welding method is most appropriate. Below, we delve into the operational challenges, safety concerns, equipment limitations, and performance drawbacks associated with stick welding.
Operational Challenges
Although stick welding is known to be versatile, it also has quite a few operational challenges. This welding method is relatively slower as compared to other welding methods such as MIG or TIG welding. As a result, it requires longer project completion deadlines. Moreover, the welds are not as clean and appealing as other methods. Finally, this method is not suitable for welding thin methods.
Safety Factors
One of the major concerns in stick welding is safety. This is because this welding method produces more splashes, sparks, and smoke than other welding methods. It is important to note that this process also releases toxic gases. As a result, it is best used in outdoor or ventilated areas. When stick welding indoors, you must wear appropriate protective gear to prevent safety risks.
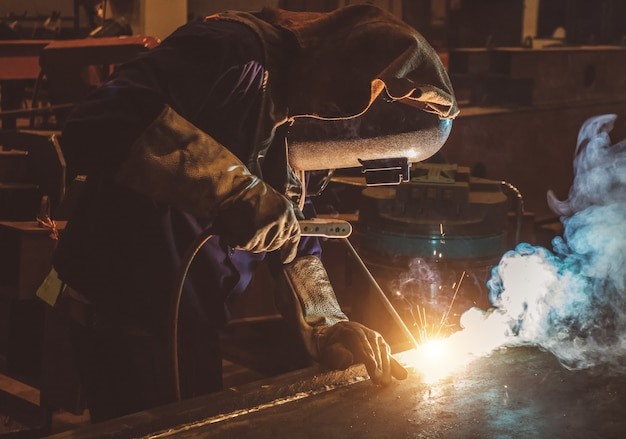
Equipment Limitations
As a manual process, stick welding has limitations when it comes to automation. A MIG welder or a TIG welder can easily be integrated into automated systems for high-volume production. However, stick welding relies heavily on the skill and precision of the welder. As a result, it is also not very suitable for beginners. Moreover, this also limits its ability to be efficient in large-scale manufacturing.
Performance Drawbacks
It is important to note that the stick welding process requires frequent electrode replacements. This can interrupt your workflow and reduce your overall productivity. Moreover, this welding process creates a lot of debris which also must be removed after the welding operation. This post-cleanup adds extra time and effort to the welding project which makes it less efficient than other methods.
Conclusion
Stick welding continues to be one of the most widely used welding methods in different industries. This is because of its versatility, ease of use, and cost-effectiveness. This welding technique has the ability to work with various methods without the need for shielding gas. As a result, it is an important tool in different industries including construction, shipbuilding, and manufacturing.
It is important to note that this process also has its drawbacks. These include slower operations, safety concerns, and equipment limitations. Stick welders must understand both the benefits and drawbacks of this welding process. This can help them make better-informed decisions about when to use this welding method so that they can get the most optimum results for their projects.
FAQ
To help you better understand stick welding, we’ve compiled a list of frequently asked questions. These brief answers address common inquiries about materials, suitability for beginners, safety precautions, comparisons with other welding methods, and equipment maintenance.
What materials can be welded using stick welding?
Stick welding is compatible with a wide range of metals, including steel, stainless steel, cast iron, and aluminum. This versatility makes it suitable for various applications, from industrial repairs to construction projects. However, it is less effective for welding thin metals, which may be prone to burn-through.
Is stick welding suitable for beginners?
Yes, stick welding is often recommended for beginners due to its simplicity and minimal equipment requirements. The process is relatively straightforward to learn, making it an excellent entry point for those new to welding. Additionally, its portability allows beginners to practice in different environments without needing extensive setup.
What are the safety precautions for stick welding?
Stick welding produces sparks, splashes, smoke, and toxic gases, necessitating the use of proper safety gear, such as welding helmets, gloves, and protective clothing. It is recommended to perform stick welding outdoors or in well-ventilated areas to minimize exposure to harmful fumes. When welding indoors, ensure adequate ventilation and use fume extraction systems.
How does stick welding compare to MIG and TIG welding?
Stick welding is generally slower than MIG and TIG welding and produces less aesthetically pleasing welds that may require additional finishing. However, it is more versatile and can be used in a wider range of environments, including outdoors. Unlike MIG and TIG, stick welding does not require shielding gas, making it more cost-effective.
What maintenance does stick welding equipment require?
Stick welding equipment requires regular inspection and maintenance to ensure optimal performance. This includes checking and replacing worn electrodes, cleaning the welding machine, and inspecting cables and connections for any damage. Proper maintenance helps prolong the lifespan of the equipment and ensures safe and efficient operation.