Welding wires come in various types to suit different welding processes. The most common are solid wires, used in MIG welding, providing stable arcs and minimal spatter. Flux-cored wires are versatile, offering good penetration, and are suitable for outdoor work due to their shielding gas production.
Metal-cored wires combine the advantages of solid and flux-cored wires, enhancing productivity and weld quality. Finally, TIG welding tungsten electrodes provide precise and clean welds, ideal for thin materials and non-ferrous metals. Each type is selected based on the specific requirements of the welding task.
Aluminum Welding Challenges
Aluminum welding faces numerous challenges. Here are some common ones explained:
Oxide Layer Formation: Aluminum naturally forms an oxide layer on its surface, with a higher melting point than the base metal. This layer must be removed or penetrated to ensure a clean weld, often requiring specialized techniques and tools.
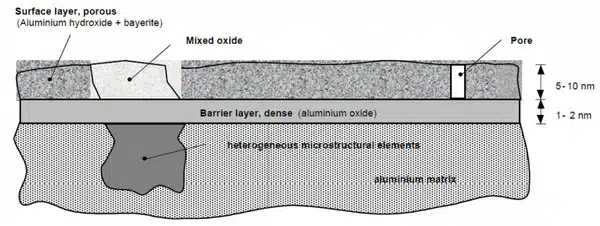
Source: https://www.materialwelding.com/how-to-clean-aluminum-oxide-layer-before-welding-easy-steps/
High Thermal Conductivity: Aluminum dissipates heat quickly, making it challenging to maintain a stable temperature during welding. This characteristic can lead to warping and distortion, especially in thinner sections.
Porosity Issues: Contaminants like moisture and oils can easily be absorbed by aluminum, leading to porosity in the weld. Proper cleaning and handling are crucial to avoid these defects.
Softness and Lack of Color Change: Aluminum is softer than other metals, making it prone to burn-through, especially in thin sheets. Additionally, it doesn’t change color when heated, making it difficult for welders to gauge the temperature and avoid overheating.
Traditional Aluminum Welding Methods
Traditional methods for welding aluminum include Tungsten Inert Gas (TIG) welding, which is preferred for its precision and control. TIG welding operates on a non-consumable tungsten electrode and a shielding gas, typically argon, to protect the weld area from contamination. This process is ideal for thin materials and provides clean, high-quality welds. In TIG welding, solid aluminum wire is commonly used as filler material. Solid wire ensures consistent composition and reduces the risk of impurities. This method is particularly useful for critical applications with crucial weld appearance and integrity.
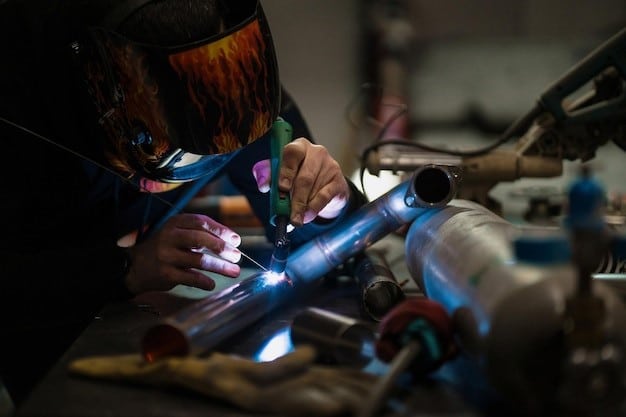
The Myth of Aluminum Flux-Cored Welding Wire
Aluminum flux-cored welding wire is a topic often surrounded by confusion and misinformation. Unlike steel, aluminum does not support the effective use of flux-cored wires due to several technical challenges. The primary issue lies in aluminum’s properties, including its low melting point and high thermal conductivity. Flux-cored wires containing flux within a metal casing are designed to create a shielding gas and slag system that protects the weld. However, aluminum’s high thermal conductivity dissipates heat too quickly, making it difficult to maintain
Aluminum does not form a stable oxide easily managed by a flux system, as in other metals. The oxide layer on aluminum is tenacious and has a much higher melting point than the metal itself, making it challenging to control during welding. As a result, flux-cored wires for aluminum are not commercially available because they cannot provide the necessary protection and stability in the weld pool. This limitation makes solid aluminum wire, used with inert gas shielding, the preferred choice for aluminum welding processes.
Can FCAW Weld Aluminum
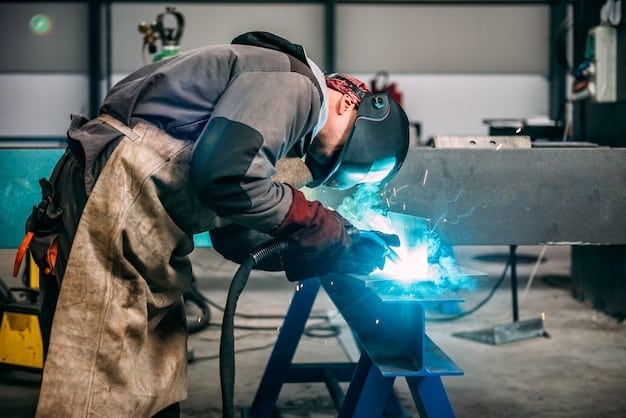
Flux-Cored Arc Welding (FCAW) is not typically used for welding aluminum. The primary reason is that flux-cored wires, essential for FCAW, do not exist for aluminum due to specific challenges. Here are the key issues:
- Oxide Layer: Aluminum has a persistent oxide layer with a high melting point, which flux cannot adequately manage. This layer complicates the welding process and prevents the formation of a strong, clean weld.
- Heat Management: Aluminum’s high thermal conductivity dissipates heat rapidly, making it difficult to maintain the required temperature for the flux to function effectively. This rapid heat loss can lead to incomplete fusion and weak welds.
- Chemical Properties: The flux in FCAW wires is to react with certain metals to create shielding gases and slag. However, aluminum’s chemical properties do not support these reactions, rendering the flux ineffective in providing the necessary protection during welding.
- Weld Quality: Aluminum welds can suffer from contamination and porosity without proper shielding and slag formation. These defects compromise the weld’s structural integrity and appearance, making FCAW unsuitable for aluminum.
- Lack of Commercial Wires: Due to these challenges, flux-cored wires for aluminum are not commercially available. The inability to create an effective flux system for aluminum welding means that FCAW remains impractical for this metal.
Alternatives for Welding Aluminum
Aluminum presents unique welding challenges, including issues with its oxide layer, high thermal conductivity, and difficulty achieving clean, strong welds with conventional methods like FCAW. These challenges necessitate the usage of specialized techniques to ensure quality and efficiency. Traditional methods often fall short, making exploring alternative welding methods that cater to aluminum’s distinct properties essential.
MIG Welding Aluminum
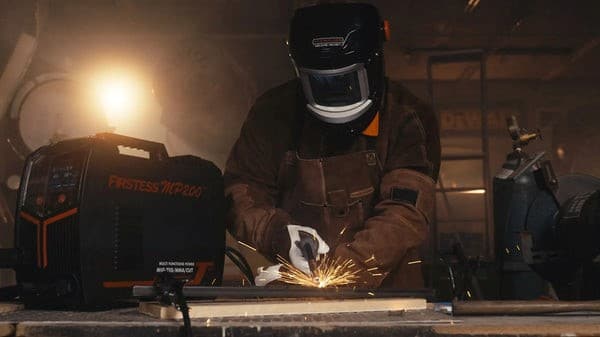
MIG (Metal Inert Gas) welding is a famous alternative for welding aluminum, offering several benefits and techniques to overcome aluminum’s challenges.
- Teflon/Graphene Liner: A Teflon or graphene liner is used in the MIG welding gun to reduce friction and prevent the soft aluminum wire from deforming as it feeds through the gun. This is crucial for maintaining a consistent wire feed and preventing jams.
- Pulse MIG: Pulse MIG welding involves modulating the current to create a pulsing effect. This technique helps control the heat input, reducing the risk of burn-through, especially in thin aluminum sheets. It also enhances the overall quality and appearance of the weld.
- Wire Drawing Welding Gun: A wire drawing welding gun ensures smooth feeding of the aluminum wire. This type of gun helps maintain a steady arc and consistent weld bead, which is essential for achieving high-quality welds.
TIG Welding
TIG (Tungsten Inert Gas) welding is another excellent alternative for aluminum. It is known for its precision and high-quality results.
- Non-Consumable Tungsten Electrode: TIG welding uses a non-consumable tungsten electrode, providing a stable arc and precise control. This is crucial for welding aluminum, where maintaining a clean weld pool is essential.
- Inert Gas Shielding: Argon is a kind of shielding gas to cover the weld area from atmospheric contamination. This is especially important for aluminum, which is prone to oxidation.
- Foot Pedal Control: Many TIG welders use a foot pedal to control the current, allowing for fine adjustments during welding. This feature is valuable when working with varying thicknesses of aluminum, providing better control over the heat input.
Resistance Spot Welding
Spot Welding Process: This method involves joining two pieces of aluminum by applying pressure and passing an electrical current through the contact points. The heat causes the metal to melt, forming a weld.
Laser Welding
Precision and Speed: Laser welding uses a focused laser beam to melt and join materials. It offers high precision and can weld very thin aluminum sections without distortion.
Friction Stir Welding (FSW)
Solid-State Welding: FSW is a solid-state welding process, meaning the material does not melt during welding. Instead, a rotating tool generates frictional heat, softening the aluminum and allowing the materials to be stirred together.
Each of these alternative methods offers unique advantages, depending on the thorough requirements of the welding task. They are crucial in overcoming the challenges of welding aluminum, ensuring strong, clean, and reliable joints.
Aluminum Welding options and their Benefits
Welding Option | Benefits | Applications |
MIG Welding | High deposition rates, suitable for thicker materials, relatively easy to learn. | Used in automotive, construction, and heavy machinery for thick aluminum parts. |
TIG Welding | High precision, clean welds, ideal for thin sections, minimal spatter. | Common in aerospace and automotive industries for high-quality and aesthetic welds. |
Resistance Spot Welding | Quick and efficient, suitable for high-volume production, minimal distortion. | Primarily used in automotive for body panels and assemblies. |
Laser Welding | High precision, capable of welding very thin sections, clean welds. | Used in electronics, medical devices, and other industries requiring precision. |
Friction Stir Welding (FSW) | Strong, defect-free welds, suitable for joining long panels, no melting involved. | Applied in shipbuilding, aerospace, and rail industries for long, continuous welds. |
Conclusion
Choosing a reliable welding wire supplier ensures high-quality and consistent welding results. YesWelder is a reputable supplier offering a range of welding products and accessories. Flux-cored aluminum welding wire does not exist due to aluminum’s unique properties, which make flux ineffective. Instead, YesWelder provides alternative options like MIG and TIG welding equipment, which are suitable for welding aluminum. These methods offer better control and quality, making them the preferred choice for aluminum welding applications.
FAQs
Why doesn’t flux-cored aluminum welding wire exist?
Due to aluminum’s properties, such as its oxide layer and high thermal conductivity, flux-cored wires are impractical because they cannot provide the necessary shielding and control.
What are the best methods for welding aluminum?
MIG and TIG welding are preferred for aluminum because they can handle its specific challenges and provide high-quality welds.
What equipment is needed for MIG welding aluminum?
Essential equipment includes a MIG welder, a Teflon or graphene liner, a pulse MIG setup, and appropriate shielding gas like argon.
Can FCAW be used for aluminum?
No, FCAW is unsuitable for aluminum as no flux-cored wires are designed.