Welding cast metals presents a unique challenge due to their brittle nature and the risk of cracks forming during the process. These issues often lead to frustration and failed projects, especially when dealing with materials like cast iron, steel, and aluminum. To overcome these challenges, it’s essential to use the correct techniques and preparation methods tailored specifically for each type of cast metal.
One can achieve a strong, durable weld by selecting the right welding approach, preheating the metal, and using the appropriate welding machine. This guide will provide clear, step-by-step instructions to help you weld various cast metals successfully, ensuring a professional finish every time.
Types of Cast Metals
Cast Iron
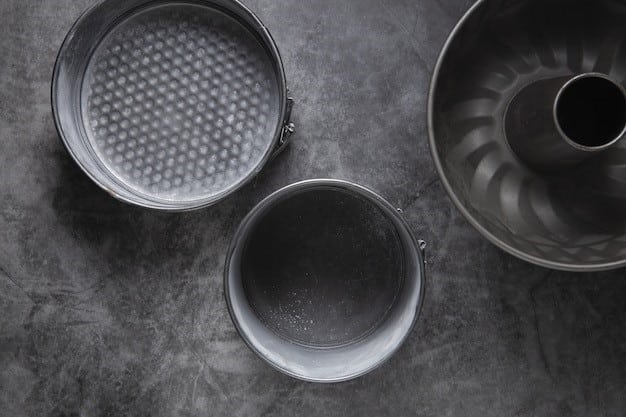
Cast iron is widely used in manufacturing due to its excellent casting properties and high wear resistance. However, its high carbon content makes it brittle and prone to cracking during welding. To weld cast iron effectively, careful preheating and controlled cooling are necessary to prevent these issues. Cast iron is commonly found in engine blocks, pipes, and cookware, where its durability is valued.
Cast Steel
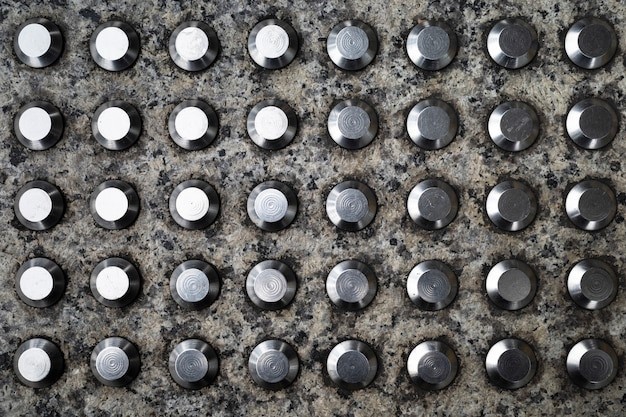
Thanks to its lower carbon content, cast steel is more malleable than cast iron. This makes welding easier and allows it to withstand higher stress levels without cracking. Cast steel is often used in heavy machinery, automotive parts, and construction equipment. The welding process for cast steel typically requires less preheating, but careful control of the welding parameters is still essential to avoid defects.
Cast Aluminum
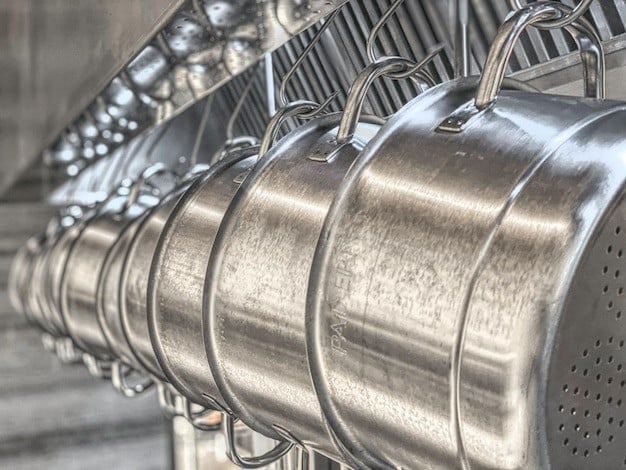
Cast aluminum is known for its lightweight and resistance to corrosion, making it a popular choice in the automotive, aerospace, and consumer goods industries. However, welding cast aluminum requires precise technique due to its high thermal conductivity and tendency to form oxide layers. Pre-welding preparation, including thorough cleaning and appropriate filler materials, is crucial to achieving a strong weld. Special attention is needed to avoid overheating, leading to warping or other weld defects.
Property | Cast Iron | Cast Steel | Cast Aluminum |
Composition | High carbon content (2-4%) | Lower carbon content (< 2%) | Primarily aluminum with small amounts of silicon, iron, etc. |
Brittleness | High, prone to cracking | Lower, more ductile | Moderate, can be brittle in certain conditions |
Thermal Conductivity | Low | Moderate | High |
Weldability | Challenging due to brittleness and cracking risk | Easier to weld, requires control | Requires precise technique to avoid defects |
Common Uses | Engine blocks, pipes, cookware | Heavy machinery, automotive parts, construction equipment | Automotive, aerospace, consumer goods |
Preheating Requirement | High, to reduce cracking | Moderate, to prevent defects | Essential, to prevent warping and defects |
Corrosion Resistance | Moderate, can rust easily | Variable, often treated with coatings | High, naturally resistant |
Weight | Heavy | Moderate | Light |
Considerations of Cast Metals in Welding
Due to their unique properties, welding cast metals presents several challenges. Understanding these challenges is crucial for achieving a strong and durable weld. Below are some common issues faced when welding different cast metals and practical tips to overcome these challenges.
Challenges in Welding Cast Iron
Brittleness and Cracking
One of the most significant challenges in welding cast iron is its brittleness. Cast iron’s high carbon content makes it prone to cracking during welding. The material can easily develop cracks when exposed to rapid heating and cooling, leading to a weak weld.
Porosity
Porosity is another issue that arises when welding cast iron. The material’s high carbon content can cause gas pockets to form during welding, resulting in porous welds. These pockets weaken the weld and can lead to failure under stress.
Thermal Expansion and Contraction
Cast iron has a low tolerance for thermal expansion and contraction. During welding, the intense heat causes the metal to expand and contract rapidly, leading to warping or cracking if not properly managed.
Tips for Welding Cast Iron
- Preheat the Metal: Preheating the cast iron before welding can reduce the risk of cracking. It helps to evenly distribute the heat and minimize thermal stress.
- Use Nickel-Based Filler Rods: Nickel-based filler rods are recommended for welding cast iron as they have a lower expansion rate and help reduce the risk of cracking.
- Control the Cooling Rate: After welding, allow the metal to cool slowly to prevent thermal shock and minimize the chances of cracking.
Challenges in Welding Cast Steel
Heat Affected Zone (HAZ) Hardening
In cast steel, the heat-affected zone (HAZ) can become hardened due to rapid cooling after welding. This hardening can lead to brittleness and reduced toughness in the welded area.
Distortion
Due to its moderate thermal expansion, cast steel is prone to distortion during welding. If not managed properly, this can lead to part misalignment and structural integrity issues.
Weld Defects
Common defects such as porosity, slag inclusion, and incomplete fusion can occur when welding cast steel, affecting the weld quality.
Tips for Welding Cast Steel
- Preheat if Necessary: Preheating is recommended for thicker sections of cast steel to avoid HAZ hardening and reduce the risk of defects.
- Use Controlled Welding Parameters: Maintain a steady heat input and control the welding speed to minimize distortion.
- Post-Weld Heat Treatment: Consider using post-weld heat treatment to relieve stress and reduce hardness in the HAZ.
Challenges in Welding Cast Aluminum
Oxide Layer Formation
One of the primary challenges in welding cast aluminum is forming an oxide layer on the surface. This layer can prevent proper fusion during welding, leading to weak joints.
High Thermal Conductivity
Cast aluminum has high thermal conductivity, so it absorbs and dissipates heat rapidly. This can make maintaining a consistent welding temperature difficult, leading to incomplete fusion or overheating.
Warping
Due to its lightweight nature and high thermal expansion, cast aluminum is prone to warping during welding. This can result in misaligned parts and poor weld quality.
Tips for Welding Cast Aluminum
- Clean the surface Thoroughly: Remove the oxide layer and any contaminants from the surface before welding to ensure proper fusion.
- Use an AC Welding Machine. AC welding machines break the oxide layer, allowing for better weld penetration.
- Control Heat Input: To prevent warping, apply heat evenly and avoid overheating. To manage heat better, use shorter weld passes.
Pre-Welding
Clean the Cast Metal Surface
Before starting the welding process, it’s crucial to thoroughly clean the cast metal surface. Any contaminants, such as oil, rust, or dirt, can lead to poor weld quality by introducing impurities into the weld pool. Use a wire brush or grinder to remove these contaminants, ensuring a clean and smooth surface for welding. Proper cleaning enhances the weld’s integrity and reduces the risk of defects.
Preheating
Preheating the cast metal before welding is essential, especially for materials like cast iron. This process reduces the thermal gradient between the weld area and the rest of the metal, minimizing the risk of cracking. Preheating also helps achieve a more even heat distribution, making the welding process smoother and more controlled. The preheating temperature depends on the type of metal and its thickness.
Choosing The Right Welding Technique for Cast Metals
The appropriate welding technique is crucial for achieving strong and reliable welds on cast metals. Each cast metal type—iron, steel, and aluminum—requires specific welding methods to address its unique properties and challenges. Below is a discussion of the best techniques for welding these materials.
Welding Cast Iron
Stick Welding
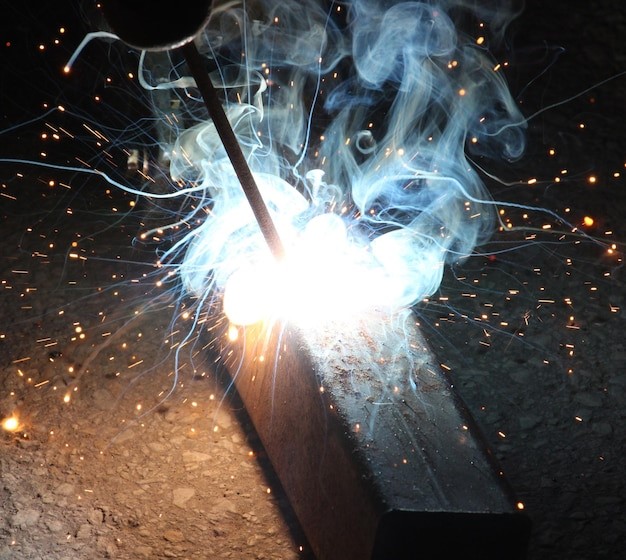
Stick welding, or Shielded Metal Arc Welding (SMAW), is commonly used for welding cast iron. It’s effective because it provides deep penetration, essential for cast iron’s thick and brittle nature. The process involves using a flux-coated electrode that melts and fuses the metal. However, stick welding requires careful control of the heat input to avoid cracking, especially when working with high-carbon cast iron.
MIG Welding
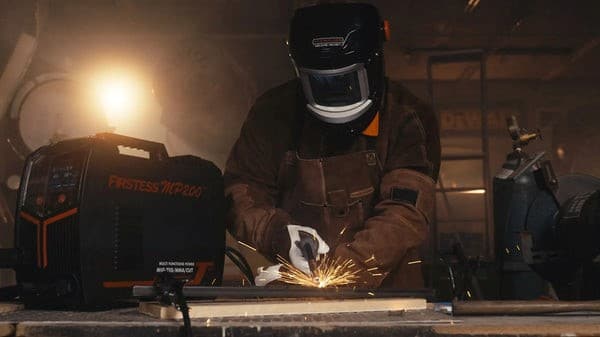
Metal Inert Gas (MIG) welding is another option for welding cast iron, particularly when dealing with thinner sections. Compared to stick welding, a MIG welding machine offers better control over the heat input, reducing the risk of thermal stress and cracking. It’s suitable for repair work on cast iron components, such as engine blocks and manifolds. However, proper preheating and slow cooling are essential for a successful weld.
TIG Welding
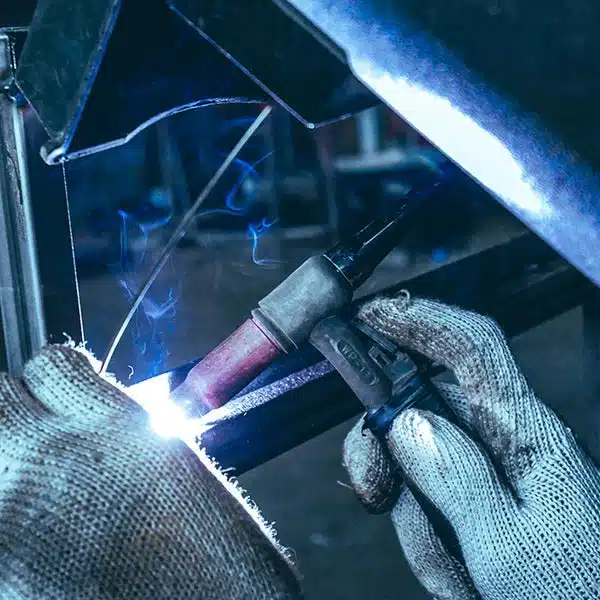
Tungsten Inert Gas (TIG) welding is the most precise casting iron method. TIG welding allows better control over the welding process, making it ideal for delicate or intricate work. Using a non-consumable tungsten electrode and an inert gas shield helps prevent contamination and improves the quality of the weld. TIG welding is particularly useful for small repairs or detailed work on cast iron, but it requires a skilled operator to manage the heat input and avoid cracking.
Welding Cast Steel
MIG Welding
MIG welding is widely used for welding cast steel due to its efficiency and ease of use. The process involves feeding a continuous wire electrode through a welding gun, which melts and fuses the steel. MIG welding is suitable for both thin and thick sections of cast steel, and it offers good control over the heat input, reducing the risk of distortion. It’s often used in automotive and heavy machinery applications requiring strong and durable welds.
TIG Welding
TIG welding is another effective method for welding cast steel, especially when high precision is needed. A TIG welding machine provides excellent control over the weld pool, making it ideal for intricate or delicate work. Using an inert gas shield, usually argon, prevents oxidation and ensures a clean weld. TIG welding is preferred for applications where the appearance of the weld is important, as it produces smooth and aesthetically pleasing welds.
Welding Cast Aluminum
TIG Welding
TIG welding is the preferred technique for welding cast aluminum due to its ability to handle the metal’s high thermal conductivity. The process uses a non-consumable tungsten electrode and an inert gas, typically argon, to create a clean and controlled weld. TIG welding is ideal for cast aluminum because it allows precise control over the heat input, reducing the risk of warping or cracking. This method is commonly used in the automotive and aerospace industries, requiring lightweight and corrosion-resistant welds.
Method | Cast Metals | Benefits |
Stick Welding (SMAW) | Cast Iron | Provides deep penetration, essential for thick and brittle cast iron; effective for high-carbon cast iron. |
MIG Welding | Cast Iron | Offers better control over heat input, reducing thermal stress and cracking; suitable for repair work. |
TIG Welding | Cast Iron | Allows precise control, ideal for delicate or intricate work; prevents contamination with inert gas shield. |
MIG Welding | Cast Steel | Efficient and easy to use; suitable for both thin and thick sections; reduces distortion risk. |
TIG Welding | Cast Steel | Provides excellent control over the weld pool, ideal for intricate work; prevents oxidation. |
TIG Welding | Cast Aluminum | Handles high thermal conductivity well; allows precise control over heat input, reducing warping or cracking. |
Choose the Right Manufacturer
When selecting welding equipment for cast metals, it’s crucial to choose a reliable manufacturer that offers a variety of machines suited to your specific needs. YesWelder is a trusted supplier that provides high-quality welding machines for different cast metals. Whether you are working with cast iron, steel, or aluminum, YesWelder has a range of welders that deliver consistent performance and durability.
Their machines are user-friendly and have features that help manage the unique challenges of welding cast metals, such as precise heat control and compatibility with different welding techniques. Opting for YesWelder ensures you have the tools to achieve strong, reliable welds in your projects.
Final Thoughts
Welding cast metals can be challenging, but with the right techniques and preparation, it is possible to achieve strong and reliable welds. Understanding each metal’s specific needs, whether cast iron, steel, or aluminum, is crucial for success. You can prevent common cracking and warping by following the recommended practices, including proper preheating, careful selection of welding methods, and controlled cooling. Using high-quality welding equipment, as YesWelder offers, ensures you have the tools to manage these challenges effectively. YesWelder’s machines are designed to handle the unique demands of welding cast metals, making your work more precise and reliable.
FAQs
Can you weld cast iron?
Yes, cast iron can be welded, but its brittleness requires careful preparation, including preheating and slow cooling, to prevent cracking.
What is the best method to weld cast aluminum?
TIG welding is the preferred method for welding cast aluminum, as it offers precise control over heat input, reduces the risk of warping, and ensures a clean weld.
Do you need to preheat cast steel before welding?
Preheating cast steel is recommended for thicker sections to prevent hardening in the heat-affected zone and reduce the risk of defects.
What filler rod should be used for welding cast iron?
Nickel-based filler rods are commonly used for welding cast iron as they minimize the risk of cracking and ensure a stronger weld.
Can MIG welding be used on cast metals?
Yes, MIG welding can be used on cast metals like cast steel and cast iron, particularly for repair work, but proper preheating and controlled cooling are essential for success.