In industries where precision and durability are paramount, poor-quality pipe welding can lead to catastrophic failures, compromising safety and incurring significant costs. Ensuring the structural integrity of welded pipes is essential to prevent leaks, corrosion, and system breakdowns. The solution lies in implementing rigorous quality control measures throughout the welding process.
Industries can achieve reliable and long-lasting welds by adhering to established standards, employing proper welding techniques, and conducting thorough inspections. This article explores the fundamentals of pipe welding, emphasizing the importance of quality control to ensure safety and efficiency in various applications.
Types of Pipe Material
Pipe welding involves various materials, each with specific properties influencing the welding process.
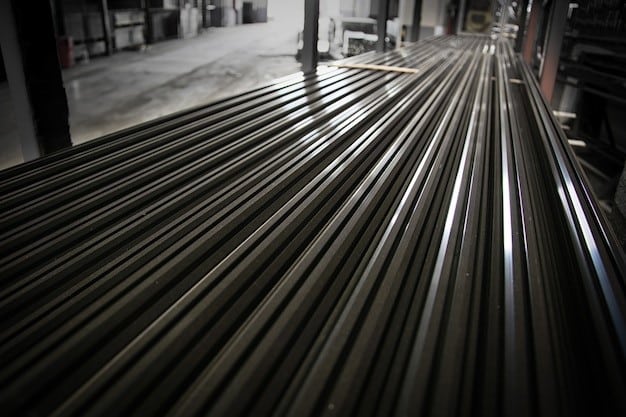
Carbon Steel
Carbon steel is one of the most commonly used materials in pipe welding. It is favored for its strength, durability, and cost-effectiveness. Carbon steel is versatile, making it suitable for various applications, including construction and manufacturing. However, it requires proper protection against corrosion, as it is prone to rust when exposed to moisture and air.
Stainless Steel
Stainless steel is known for its resistance to corrosion and high temperatures, making it ideal for applications in harsh environments. It contains chromium, which forms a protective oxide layer, preventing rust. Stainless steel is commonly used in food processing, pharmaceuticals, and petrochemicals, where cleanliness and corrosion resistance are crucial.
Alloy Steel
Alloy steel is a blend of carbon steel with other elements like manganese, nickel, or chromium to enhance its properties. These additions improve the material’s strength, toughness, and resistance to wear and corrosion. Alloy steel is often used in high-stress applications, such as automotive and aerospace industries, where enhanced performance is required.
Specialty Metals
Specialty metals, including titanium, nickel alloys, and aluminum, are used in pipe welding for specialized applications. These materials offer unique properties like exceptional strength-to-weight ratios, resistance to extreme temperatures, and chemical stability. Specialty metals are often employed in aerospace, nuclear power, and chemical processing industries, where standard materials would not suffice.
Pipe Material Type Properties and Their Applications
Material Type | Key Properties | Common Applications |
Carbon Steel | Strong, durable, cost-effective, prone to rust | Construction, manufacturing, pipelines |
Stainless Steel | Corrosion-resistant, high-temperature tolerant | Food processing, pharmaceuticals, petrochemicals |
Alloy Steel | Enhanced strength, toughness, corrosion-resistant | Automotive, aerospace, heavy industry |
Specialty Metals | Unique properties like high strength-to-weight ratio | Aerospace, nuclear power, chemical processing |
Advantages of Pipe Welding
Pipe welding is a crucial process in various industries. It offers several advantages that make it the preferred method for joining pipes.
Strength and Durability
Pipe welding provides a strong and durable connection between pipes, ensuring a reliable joint that can withstand high pressure and stress. Welded joints often exhibit strength equal to or greater than the base metal, making them ideal for critical applications in various industries, including oil and gas, water distribution, and power generation.
Versatility
Pipe welding is versatile, allowing different metals and alloys to join. This flexibility enables diverse materials to meet specific requirements, such as corrosion resistance, high-temperature tolerance, or lightweight construction. Welding also allows for the creation of complex piping systems, adapting to the unique needs of each project.
Cost-Effectiveness
Welded pipes are often more cost-effective than other joining methods, such as flanging or threading. Welding reduces the need for additional fittings and connectors, simplifying the pipeline design and reducing material costs. Additionally, welded joints require less maintenance over time, contributing to long-term savings.
Leak Prevention
A significant advantage of pipe welding is its ability to create a continuous, leak-proof joint. This is especially crucial in industries where the containment of fluids or gases is essential. Properly executed welds prevent leaks, reduce the risk of environmental contamination, and improve the safety of the overall system.
Comparison of Pipe Welding and Other Joining Methods
Advantage | Pipe Welding | Other Joining Methods |
Strength and Durability | Provides strong, durable joints suitable for high-pressure and stress conditions. | May not provide the same level of strength, often requiring additional reinforcement. |
Versatility | Can join various metals and alloys, accommodating different project needs. | Limited to specific materials, restricting flexibility in design. |
Cost-Effectiveness | Reduces material costs by eliminating the need for additional fittings. | Often requires additional components, increasing material costs. |
Leak Prevention | Creates a continuous, leak-proof joint, crucial for fluid and gas containment. | May require seals or gaskets, which can fail over time, leading to leaks. |
Industrial Applications
Pipe welding plays a critical role in various industrial sectors, where the integrity and reliability of piping systems are paramount. The ability to join pipes securely and efficiently makes welding an essential process in industries that rely on extensive networks of pipelines.
Energy Sector
In the energy sector, pipe welding is crucial for constructing and maintaining pipelines transporting oil, gas, and other fuels. These pipelines must withstand high pressures and extreme environmental conditions, making robust and reliable welding essential to ensure safe and efficient energy distribution.
Infrastructure Development
Infrastructure projects, such as water supply systems, sewage lines, and heating systems, also heavily depend on pipe welding. The durability and leak-proof nature of welded pipes ensure the long-term functionality of these critical systems, reducing the need for frequent repairs and maintenance.
Manufacturing Industry
In manufacturing, pipe welding creates complex piping systems for various processes, including chemical processing, food production, and machinery operation. Welding enables the construction of custom-designed systems that meet the specific needs of each manufacturing facility, enhancing overall efficiency and productivity.
Pipe Welding Methods
Pipe welding employs various techniques to achieve strong, reliable joints. Each method is suited to specific materials, conditions, and applications, ensuring the best results for different industrial needs.
Shielded Metal Arc Welding (SMAW)
SMAW, or stick welding, is widely used for its simplicity and versatility. It involves a consumable electrode coated in flux that melts and fuses the pipe material. A stick welder is effective for welding in various positions and environments, making it popular for fieldwork.
MIG Welding
Metal Inert Gas (MIG) welding uses a continuous wire feed as an electrode. Shielding gas protects the weld pool from contamination. A MIG welding machine is efficient and produces clean, high-quality welds with minimal spatter. It is suitable for both thin and thick materials.
Flux-Cored Arc Welding (FCAW)
FCAW is similar to MIG welding but uses a tubular wire filled with flux. This method is particularly effective in outdoor settings due to its wind resistance. FCAW is preferred for heavy-duty applications, offering deep penetration and high deposition rates.
TIG Welding
Tungsten Inert Gas (TIG) welding uses a non-consumable tungsten electrode. A TIG welder produces precise and high-quality welds, ideal for thin materials and critical applications. TIG welding is often used for stainless steel and non-ferrous metals, requiring skilled operators due to its complexity.
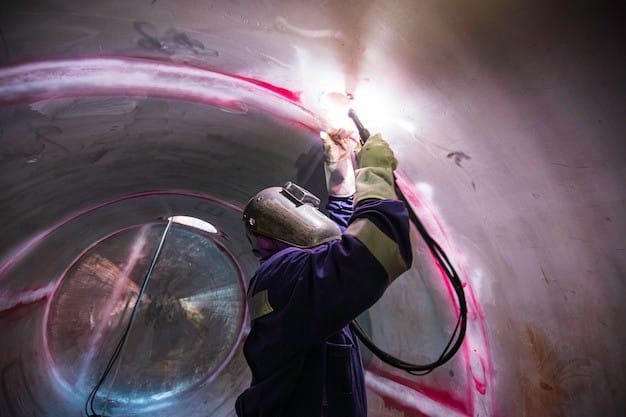
Quality Control and Inspection
Quality control in pipe welding is essential to ensure the integrity and safety of the welds. Inspection methods detect any defects or irregularities that could compromise the welding quality. Below are some key inspection methods:
- Visual Inspection: This is the most basic and immediate form of inspection. It involves examining the welds for surface defects such as cracks, porosity, or misalignment.
- Radiographic Inspection: This method uses X-rays or gamma rays to penetrate the weld and create an image of its internal structure, allowing for the detection of hidden flaws like voids or inclusions.
- Ultrasonic Inspection: Ultrasonic waves detect internal defects by measuring the reflection of sound waves within the weld. This method effectively identifies flaws that are not visible on the surface.
- Magnetic Particle Testing: This technique detects surface and slightly subsurface defects in ferromagnetic materials by applying magnetic fields and detecting leakage fields caused by discontinuities.
- Dye Penetrant Inspection: A liquid dye is applied to the weld’s surface to highlight surface defects. The dye penetrates any cracks or voids, making them visible under UV light or a developer.
Safety Protocols for Pipe Welding
Safety protocols are essential in pipe welding to protect workers and ensure a safe working environment. Key measures include:
- Personal Protective Equipment (PPE): Welders must wear appropriate PPE, including helmets, gloves, and fire-resistant clothing, to protect against burns, sparks, and harmful radiation.
- Ventilation: Proper ventilation is crucial to prevent the accumulation of hazardous fumes and gases in the welding area and ensure a safe breathing environment.
- Fire Safety: To reduce the risk of fires, fire extinguishers should be readily available, and the work area must be free from flammable materials.
- Equipment Maintenance: Regular inspection and maintenance of welding equipment prevent malfunctions that could lead to accidents. Ensuring all tools are in good working condition is vital for safety.
Final Thoughts
Pipe welding is a critical process in various industries, requiring careful attention to quality and safety. By understanding the types of materials, leveraging the advantages of welding, and adhering to stringent quality control and safety protocols, industries can ensure the longevity and reliability of their piping systems.
Effective welding practices prevent costly failures and contribute to industrial operations’ overall efficiency and safety. Proper training, excellent equipment from a reliable welding equipment supplier, and continuous inspection are essential for achieving high pipe welding standards.
FAQs
What are the most common materials used in pipe welding?
Carbon steel, stainless steel, alloy steel, and specialty metals like titanium and aluminum are commonly used in pipe welding.
What are the key advantages of pipe welding over other methods?
Pipe welding offers superior strength, durability, leak prevention, and cost-effectiveness compared to other joining methods.
What are the primary safety concerns in pipe welding?
Major concerns include proper use of PPE, ventilation, fire safety, and equipment maintenance.
Which industries rely most heavily on pipe welding?
The energy, infrastructure, and manufacturing sectors are the primary users of pipe welding.
What inspection methods are used to ensure weld quality?
Common methods include visual inspection, radiographic testing, ultrasonic testing, magnetic particle testing, and dye penetrant inspection.