In the welding industry, inefficiencies can lead to significant downtime, wasted materials, and increased operational costs. Welders often struggle with inconsistent weld quality, extended work hours, and the need for rework, all of which diminish productivity. To address these challenges, adopting strategies that enhance welding efficiency is crucial. Companies can significantly boost output by optimizing techniques, improving welder skills, and ensuring proper equipment maintenance while maintaining high-quality standards.
These practical steps reduce costs and enhance overall workflow, leading to a more efficient and effective welding process. Implementing these methods will ultimately drive better results and improve the bottom line.
Key Factors of Welding Efficiency
Welding Technique
The technique used in welding has a direct impact on efficiency. Proper technique ensures the welds are consistent and strong and require minimal rework. For example, proper arc length and angle of travel when using a MIG or a stick welder minimize spatter and defects. Poor welding techniques can lead to defects, which waste materials and increase the time needed to complete a project. Training and practice in effective welding methods are essential for maintaining high productivity and quality.
Welder Skill Level
The skill level of the welder is another critical factor. Experienced welders are more likely to produce high-quality welds quickly and with fewer errors. In contrast, less skilled welders may take longer to complete tasks and might produce work that requires more corrections. Investing in continuous training for welders can significantly enhance efficiency and reduce costs.
Equipment Performance
The performance of welding equipment plays a crucial role in determining overall efficiency. Well-maintained equipment operates more smoothly, reducing the likelihood of breakdowns that can cause costly delays. Regular maintenance and timely upgrades ensure that welding machines function optimally, contributing to a more efficient workflow. Properly functioning equipment also helps maintain consistent quality across all welds.
Welding Position
The position in which welding is performed can affect the weld’s speed and quality. Some positions are more difficult to weld in, which can slow down the process and increase the chance of defects. Optimizing the welding position, whenever possible, can lead to faster and more reliable welding. This includes proper workpiece positioning and ergonomic setups for welders.
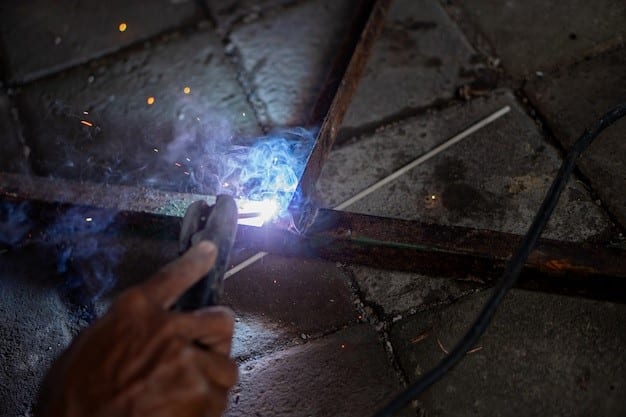
Material Selection
Choosing the right materials is vital for achieving welding efficiency. Different materials require different welding techniques, and selecting the most appropriate material can simplify the welding process. Using compatible materials reduces the likelihood of defects and ensures a smoother workflow. Material selection also affects the overall strength and durability of the weld, making it a crucial consideration in the welding process.
Table Explaining the Key Factors of Welding Efficiency
Factor | Description | Impact on Efficiency |
Welding Technique | Methods and procedures used in welding. | Affects weld quality and the need for rework. |
Welder Skill Level | Experience and training of the welder. | Influences the speed and quality of welds. |
Equipment Performance | Condition and maintenance of welding equipment. | Determines operational smoothness and reliability. |
Welding Position | The position in which welding is performed. | Impacts speed and ease of weld creation. |
Material Selection | Type and quality of materials used. | Affects weld strength and defect occurrence. |
Optimizing Welding Techniques
Focus on Proper Heat Control
Effective heat control is essential for optimizing welding techniques. Excessive heat can cause warping and weaken the welded joint, while insufficient heat may result in incomplete fusion. Welders can achieve better results by adjusting the heat input to match the material thickness and type. This adjustment minimizes the need for rework and ensures stronger, more reliable welds.
Use the Correct Welding Speed
Welding speed is another crucial factor in optimizing techniques. Welding too quickly can lead to insufficient penetration while welding too slowly can cause excessive heat buildup. Finding the right balance in welding speed ensures that the weld is strong and efficient. Consistent practice and monitoring help achieve the optimal speed for various materials and positions.
Optimize Electrode Selection
Selecting the appropriate electrode is vital for improving welding efficiency. The choice of electrode affects the weld’s quality, strength, and appearance. Using the correct electrode type and size for the specific welding task ensures a smoother welding process with fewer defects. This careful selection also enhances the overall efficiency and effectiveness of the welding operation.
Techniques | Guideline | Purpose |
Heat Control | Adjust heat levels based on material type and thickness. | Prevents warping and ensures strong welds. |
Welding Speed | Maintain an appropriate speed for the material and welding technique. | Achieves consistent penetration and reduces defects. |
Electrode Selection | Choose the correct electrode type and size for the specific weld. | Enhances weld quality and operational efficiency. |
Proper Arc Length | Maintain the correct arc length to ensure a stable welding arc. | Prevents arc instability and improves weld consistency. |
Use of Backing Bars | Employ backing bars for materials with thin sections or to prevent burn-through. | Supports welds and reduces defects in thin materials. |
Proper Shielding Gas Flow | Ensure correct shielding gas flow to protect the weld area from contamination. | Reduces the risk of defects like porosity and oxidation. |
Pre-Weld Material Preparation
- Clean Materials Thoroughly: Ensure all materials are free from contaminants like rust, oil, and dirt. Contaminants can interfere with the welding process and lead to weak welds.
- Proper Material Fit-Up: Align and fit materials accurately before welding. Proper fit-up reduces gaps and misalignment, which helps in achieving stronger and more consistent welds.
- Check Material Specifications: Verify that materials meet the required specifications for the welding process. This includes checking for appropriate thickness, type, and grade to ensure compatibility with the welding technique.
- Preheat When Necessary: Some materials require preheating to reduce thermal stress and improve weld quality. Follow guidelines for preheating based on material type and welding procedure.
- Remove Any Coatings: Remove any coatings, such as paint or galvanizing, from the welding area. Coatings can produce harmful fumes and affect weld quality.
- Ensure Proper Material Positioning: Position materials securely and correctly to avoid movement during welding. Proper positioning helps maintain weld consistency and reduces the risk of defects.
Minimizing Weld Defects
- Use Proper Welding Techniques: Applying correct welding techniques is essential for minimizing defects. Ensure consistent travel speed and appropriate heat settings for the material being welded.
- Select the Right Filler Material: Choosing the appropriate filler material helps enhance the quality of the weld. Ensure the filler is compatible with the base materials to prevent issues like porosity or cracks.
- Control Heat Input: Managing the heat input during the welding process is critical. Too much heat can lead to distortion, while too little can cause incomplete fusion, creating defects.
- Conduct Regular Inspections: Implement routine inspections of welds to identify defects early. Regular checks help recognize cracks or undercuts before they become significant problems.
- Ensure Proper Joint Preparation: Preparing joints adequately before welding can prevent defects. Clean, align, and fit joints tightly to reduce the chances of gaps that lead to weak welds.
- Provide Adequate Training: Investing in training for welders enhances their skills and knowledge. Well-trained welders are less likely to make mistakes that result in defects, promoting better overall quality.
Safety Considerations
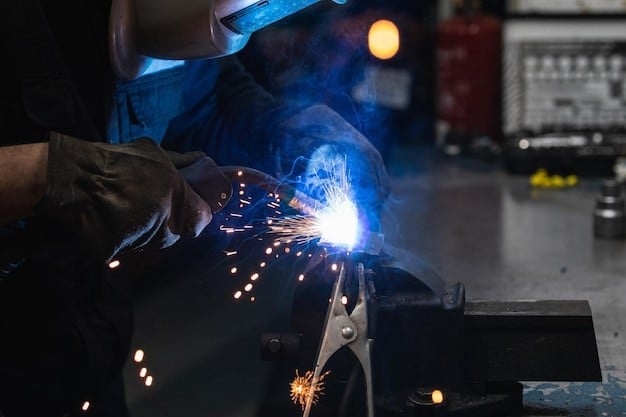
- Wear Proper Personal Protective Equipment (PPE): Use appropriate PPE, including welding helmets, welding gloves, and protective clothing. This gear protects against burns, UV radiation, and harmful fumes.
- Ensure Adequate Ventilation: Maintain good ventilation in the welding area to prevent the buildup of harmful gases and fumes. Proper airflow reduces the risk of respiratory issues and ensures a safer work environment.
- Handle Equipment Safely: Operate welding equipment according to the manufacturer’s instructions. Regularly inspect damaged equipment and perform maintenance to prevent malfunctions and accidents.
- Implement Fire Safety Measures: Keep a fire extinguisher accessible and ensure the welding area is clear of flammable materials. Take precautions to avoid sparks and molten metal from causing fires.
- Follow Electrical Safety Practices: Ensure that electrical connections are secure and that equipment is properly grounded. Avoid handling electrical equipment with wet hands to prevent electric shock.
- Maintain a Clean Work Area: Keep the welding area clean and organized to minimize trip hazards and accidents. A tidy workspace promotes better focus and reduces the risk of injuries.
Final Thoughts
Improving welding efficiency is crucial for enhancing productivity and reducing costs. By focusing on key factors such as technique, skill level, and equipment performance, welders can achieve better results with fewer defects. Optimizing welding methods and ensuring proper material preparation also play a significant role in boosting overall efficiency.
Maintaining safety and cleanliness in the work area is essential to prevent accidents and ensure high-quality welds. Make sure the welding machines are from a reliable welding equipment supplier. Implementing the strategies above will lead to a more effective welding process, contributing to a stronger bottom line and greater operational success. Emphasizing continuous improvement and adherence to best practices will drive long-term benefits and efficiency in welding operations.
FAQs
What are the main factors affecting welding efficiency?
Key factors include welding technique, welder skill level, equipment performance, welding position, and material selection. Optimizing these elements can significantly improve welding efficiency.
How can I improve my welding technique?
To enhance welding technique, practice consistently, receive proper training, and follow guidelines for heat control, welding speed, and electrode selection. Regularly review and adjust techniques based on performance and feedback.
What should I consider for material preparation before welding?
Ensure materials are clean, properly aligned, and meet specifications. Removing contaminants, checking fit-up, and preheating materials as needed can help achieve better weld quality and efficiency.
How can I minimize weld defects?
Minimize defects by controlling heat input, maintaining clean surfaces, monitoring welding speed, and selecting the correct electrode. Regular inspections during and after welding are crucial for identifying and addressing issues early.
What safety measures should be taken during welding?
Use proper personal protective equipment (PPE), ensure good ventilation, handle equipment safely, implement fire safety measures, and maintain a clean work area. Following these practices helps prevent accidents and ensures a safer welding environment.