Underwater welding presents unique challenges due to the harsh and unpredictable underwater environment. Water pressure, temperature fluctuations, and limited visibility make this task highly complex and risky. However, it is essential for maintaining and repairing marine structures, pipelines, and ships.
To address these challenges, underwater welding has evolved with specialized techniques and equipment, ensuring divers can perform tasks safely and efficiently. These advancements have enabled professionals to work in challenging conditions, providing crucial solutions for the maritime and offshore industries.
What Is Underwater Welding?
Underwater welding is a specialized process that joins metal components while submerged in water. It is crucial for repairing and maintaining marine infrastructure, such as ships, oil rigs, and pipelines. This process involves using arc welding techniques similar to those used on land but adapted to work underwater. Divers trained in welding are required to perform these tasks, combining their welding skills and diving expertise. Underwater welding can be classified into two main types: wet and dry, each with unique techniques and applications.
Types of Underwater Welding
Wet Welding
Wet welding occurs directly underwater, with no protective enclosure. The welder performs the task while fully submerged, using specialized electrodes designed to work in water. This method is often chosen for its speed and cost-effectiveness. However, it carries risks such as exposure to electric shock, poor visibility, porosity, hydrogen embrittlement, and rapid cooling, making it challenging to achieve high-quality welds.
Dry Welding (Hyperbaric Welding)
Dry welding, also known as hyperbaric welding, is performed inside a sealed chamber filled with gas to create a dry environment. This method allows more control over the welding process, producing higher-quality welds. Although safer and more precise, dry welding is more expensive and time-consuming than wet welding, making it suitable for complex or critical tasks.
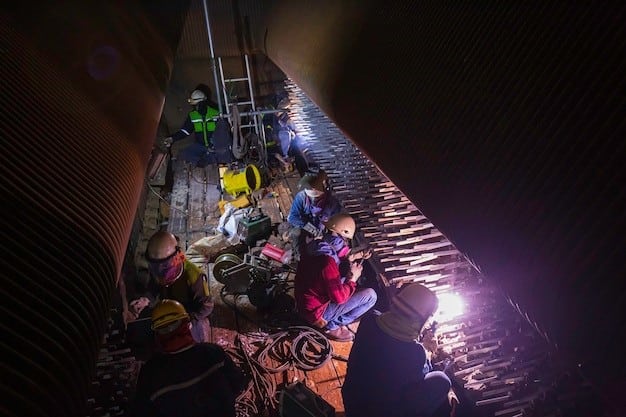
Comparison between wet and dry welding
Criteria | Wet Welding | Dry Welding |
Environment | Performed directly underwater, no enclosure. | Performed in a dry chamber underwater (hyperbaric). |
Cost | Cost-effective due to less equipment and setup. | More expensive due to specialized equipment and setup. |
Equipment | Uses water-resistant electrodes, basic diving gear. | Requires sealed chamber, gas supply, and advanced welding tools. |
Quality of Weld | Lower quality due to water contamination, reduced visibility. | Higher quality weld due to controlled environment. |
Safety | Higher risk of electric shock and environmental hazards. | Safer with better control over conditions and reduced risks. |
Application | Suitable for quick repairs and temporary fixes. | Used for complex, critical, or permanent repairs. |
Time Efficiency | Faster as it does not require setting up an enclosure. | Slower as it involves setting up a chamber. |
How Does Underwater Welding Work
Underwater welding is a process that combines both welding and diving skills to repair or construct metal structures submerged underwater. The process uses various types of equipment depending on the technique applied and the job’s specific needs. Here’s an overview of how it works:
Underwater Welding Equipment
- Shielded Metal Arc Welding (SMAW): This is the most commonly used method in underwater welding. It involves using a consumable electrode coated in flux to create an arc that melts the metal. It is adaptable and suitable for wet welding.
- Flux-Cored Arc Welding (FCAW): A type of arc welding similar to SMAW, using a continuous MIG welding wire feed instead of a stick electrode. This method is preferred for dry welding inside chambers because of its high efficiency and precision.
- Tungsten Inert Gas (TIG) Welding: A TIG welder uses a non-consumable tungsten electrode and is known for producing high-quality welds. It is more time-consuming and generally used for dry welding.
Specialized Equipment
- Electrodes: Specialized water-resistant electrodes are essential for wet welding. These electrodes are designed to withstand the pressure and water around them, allowing welders to create a stable arc underwater.
- Diving Gear: Divers wear specialized suits that protect them from cold water and pressure while allowing them the mobility to perform welding tasks. They also use special welding helmets with communication systems to stay in contact with the surface team.
- Remotely Operated Vehicles (ROVs): For more dangerous or inaccessible underwater welding tasks, ROVs can be used. These are controlled from the surface and equipped with welding tools to perform tasks in extreme conditions, such as deep-sea environments.
Underwater Welding Methods
Welding Method | Description | Usage |
Shielded Metal Arc Welding (SMAW) | Common arc welding method using consumable electrodes. | Wet welding, general repairs |
Flux-Cored Arc Welding (FCAW) | Uses a continuous wire feed for efficient welding. | Dry welding, precision tasks |
Tungsten Inert Gas (TIG) Welding | High-quality welding with a non-consumable tungsten electrode. | Specialized tasks, dry environments |
Plasma Arc Welding (PAW) | Uses a concentrated plasma arc for high-quality, deep welds. (Less commonly used due to the complexity of maintaining a stable arc in submerged environments) | Specialized underwater applications |
Applications of Underwater Welding
Underwater welding is critical in maintaining and repairing structures in aquatic environments. It is widely used in several industries that require work to be done beneath the water’s surface. Here are some key applications:
Marine and Offshore Industry
In the marine and offshore industries, underwater welding is used to maintain and repair ships, oil platforms, oil rig pipelines, and other offshore structures. Welders often fix damaged hulls or support structures to ensure vessels’ and rigs’ safety and operational efficiency. This method is essential for avoiding downtime, as repairs can be made without needing to dock the ship or bring platforms out of the water.
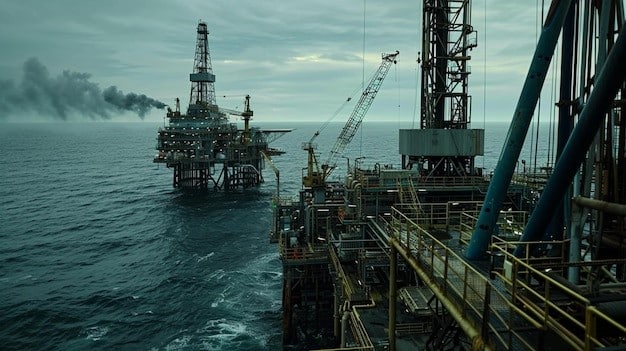
Underwater Infrastructure
Underwater welding is crucial for building and maintaining underwater infrastructure such as bridges, pipelines, and dams. These structures are often subjected to harsh underwater conditions that can cause wear and tear. Regular maintenance and emergency repairs are necessary to prevent failures. Welding is used to fix cracks, leaks, or broken sections, ensuring the longevity and safety of critical infrastructure.
Emergency Repairs
In situations requiring immediate action, underwater welding is the go-to solution for emergency repairs. It allows damaged structures to be quickly fixed without needing to be removed from the water, saving time and preventing further damage. This is especially important for pipelines and marine vessels, where delays in repair can result in severe financial and environmental consequences.
Why Is Underwater Welding So Hard and Dangerous?
Underwater welding is challenging due to the combination of dangerous working conditions and the complexity of the tasks involved. Several factors make this job both difficult and risky.
Safety Challenges
Underwater welding carries significant safety risks. The most prominent danger is the risk of electric shock due to using electrical equipment in water. Also, the potential for underwater explosions is high if gas pockets form near the welding arc. Additionally, divers face the potential for drowning, decompression sickness, and hypothermia. Working in low-visibility environments can also increase the chances of accidents. These factors make it critical for welders to adhere strictly to safety protocols.
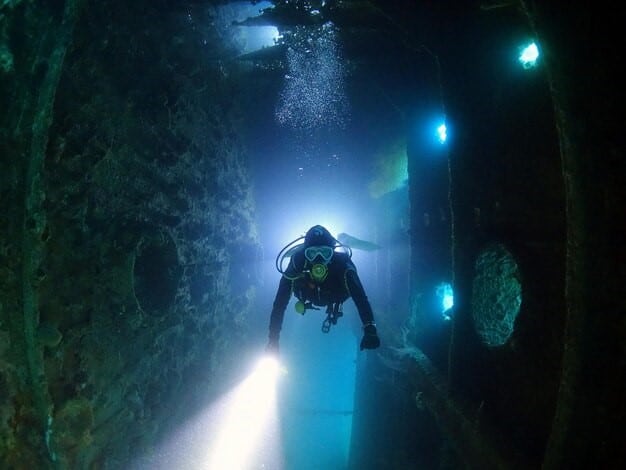
Technical Challenges
Underwater welding involves advanced technical skills. Maintaining a stable arc underwater is difficult due to water movement and pressure variations. Wet welding, in particular, can lead to poor-quality welds due to the presence of water, which affects the welding process. Divers must manage complex equipment, such as electrodes and welding tools while contending with environmental factors like currents and limited visibility.
Health and Safety Regulations
Strict health and safety regulations are in place to mitigate the risks associated with underwater welding. Welders must have specialized certifications in both diving and welding. Additionally, safety protocols, including personal protective equipment (PPE), communication devices, and routine inspections, are mandatory to ensure the safety of workers.
Environmental Factors
The underwater environment adds another layer of complexity. Welders must contend with cold temperatures, varying water pressure, and difficulty working at great depths. These environmental factors can significantly affect the weld quality and increase the risks of equipment failure or personal injury.
Underwater Welding Qualifications & Requirements
Underwater welding requires a unique combination of skills and certifications. Both welding expertise and diving proficiency are essential to succeed in this profession. Below are the qualifications and certifications required for underwater welding.
Required Qualifications
- Diving Certification: A commercial diving certification is mandatory. This certifies that the welder can safely operate in various underwater environments, including deep-sea conditions.
- Welding Expertise: Welders must have strong knowledge and experience in welding techniques such as Shielded Metal Arc Welding (SMAW) and Flux-Cored Arc Welding (FCAW). This ensures they can perform high-quality welds underwater.
- Physical Fitness: Due to the demanding nature of the job, underwater welders must maintain good physical health and endurance. They should be able to handle heavy equipment and perform tasks under high pressure.
- Technical Skills: Besides welding skills, knowledge of diving equipment and underwater tools is essential. This includes using specialized electrodes and managing welding tasks in low-visibility environments.
Certification Requirements
- Commercial Diver Certification: Welders must earn an industry-recognized commercial diving certification from an accredited organization, such as the Association of Diving Contractors International (ADCI).
- Underwater Welding Certification: Specific underwater welding certifications, such as those from the American Welding Society (AWS D3.6), ensure that the welder is qualified to perform welds in challenging underwater conditions.
- Specialized Certifications: Some jobs may require additional certifications in non-destructive testing (NDT) or other specialized techniques to ensure weld integrity in underwater environments.
- Continual Training: Welders must also regularly train to keep up with industry standards and safety regulations, which evolve to address new technologies and risks.
Final Thoughts
Underwater welding is vital for maintaining marine and offshore structures, yet it comes with significant challenges and risks. The combination of technical expertise in welding and diving and strict safety measures is essential for success in this field. With the right qualifications and adherence to industry standards, underwater welders can ensure the safety and functionality of critical infrastructure.
Meanwhile, high-quality welding equipment from welding machine suppliers is crucial for underwater welding. As technology advances, the techniques and equipment used in underwater welding will continue to improve, making the profession more efficient and safer for workers.
FAQs
Is underwater welding dangerous?
Yes, it poses risks like electric shock, decompression sickness, and drowning. Safety protocols and specialized training help reduce these dangers.
How much do underwater welders earn?
Underwater welders earn between $40,000 and $100,000 annually, depending on experience and job location.
What qualifications are needed to become an underwater welder?
You need a commercial diving certification, welding expertise, and specialized underwater welding certifications like those from the AWS.