Welding in the field presents unique challenges, especially due to environmental factors, equipment limitations, and inconsistent power sources. Poor weld quality can lead to weak structures, posing significant safety risks in construction and infrastructure projects. Ensuring proper techniques and the right welding method is key to overcoming these hurdles.
Field welding offers a solution, enabling work to be performed in remote or challenging locations. By utilizing specialized equipment and skilled operators, reliable welds can be achieved, ensuring durability and safety even under tough conditions. This article explores the essential aspects of field welding, including methods, challenges, and best practices.
What is Field Welding
Field welding refers to processes carried out directly at the construction site or a remote location. Unlike shop welding, field welding involves assembling and joining metal components in outdoor environments where conditions may be less controlled. This technique is commonly used in large construction projects, repairs, and installations where transporting materials for off-site welding isn’t feasible.
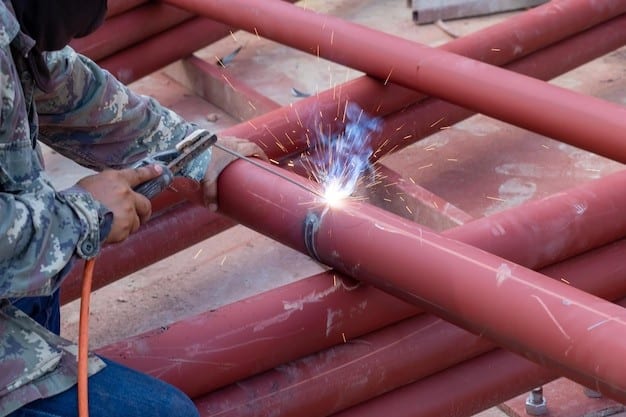
Applications of Field Welding
Field welding is used in various industries, such as construction, pipeline installation, shipbuilding, and heavy equipment repair. It allows for flexibility in assembling structures on-site, ensuring that large-scale projects can be completed without moving components back to a welding shop.
Pros
- Allows on-site repairs and assemblies
- Reduces transport costs and delays
- Offers flexibility in remote and hard-to-reach locations
Cons
- It is difficult to control environmental factors like wind or moisture
- Limited access to stable power sources
Field Welding Methods
Stick Welding
Stick welding, or Shielded Metal Arc Welding (SMAW), is commonly used in field welding due to its simplicity and portability. A stick welder uses a consumable electrode coated in flux, which creates a protective gas shield as it melts. Stick welding is highly effective for working in outdoor or windy conditions, but it can be slower and requires more skill to achieve clean welds, especially on thin metals.
MIG Welding
Metal Inert Gas (MIG) welding, or Gas Metal Arc Welding (GMAW), uses a continuously fed wire electrode and shielding gas to create the weld. Using a MIG welder is fast and efficient, making this method ideal for high-production settings. However, it is more sensitive to environmental conditions like wind, which can affect the shielding gas. As a result, it is less commonly used outdoors unless proper protection is in place.
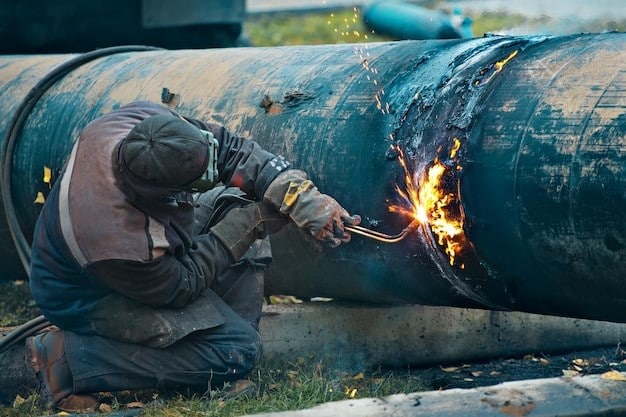
TIG Welding
Tungsten Inert Gas (TIG) welding, also known as Gas Tungsten Arc Welding (GTAW), produces high-quality welds. It uses non-consumable tungsten welding electrodes and a separate filler material. TIG welding allows precise control over the welding process, making the TIG welder ideal for thin materials or intricate work. However, it is slower than other methods and requires more skill, making it less suitable for fast-paced field projects.
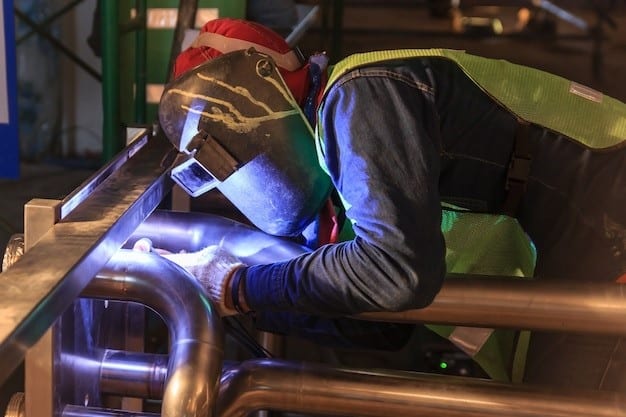
Flux-Cored Arc Welding (FCAW)
Flux-Cored Arc Welding (FCAW) is similar to MIG welding but uses a tubular wire filled with flux instead of a solid wire. This method offers welding flexibility in various environments, as it can be used with or without shielding gas. FCAW is well-suited for field welding because it handles thicker materials and outdoor conditions. However, it can produce more spatter, requiring post-weld cleanup.
Field Welding Method Comparison
Welding Method | Description | Pros | Cons |
Stick Welding | Uses a consumable electrode with flux coating | Portable, works well outdoors | Slower, requires skill for clean welds |
MIG Welding | Uses a continuously fed wire and shielding gas | Fast, high production rate | Sensitive to wind, less suited for outdoors |
TIG Welding | Non-consumable tungsten electrode | Precise, ideal for thin materials | Slower, more skill required |
Flux-Cored Arc Welding | Uses flux-filled tubular wire | Versatile, works in windy conditions | More spatter, requires cleanup |
Common Challenges in Field Welding
Weld Quality
One of the main challenges in field welding is maintaining consistent weld quality. Factors like varying temperatures, humidity, and dirt can affect the integrity of the weld. Inadequate control of these factors can lead to defects such as cracks, weak joints, or porous welds. Ensuring proper inspection and cleaning of surfaces is crucial to achieving strong and reliable welds in field conditions.
Power Sources
Field welding often occurs in remote areas where stable power sources are unavailable. Welders may have to rely on portable generators or battery-powered equipment, which can impact the quality of the weld. Inconsistent power can lead to fluctuations in heat, affecting the fusion of metals. A steady and adequate power supply is critical for producing strong, precise welds.
Environmental Factors
Environmental conditions like wind, rain, and extreme temperatures pose significant challenges for field welders. Wind can blow away shielding gases in gas-shielded welding processes, causing oxidation and weakening the weld. Rain or moisture can contaminate the welding area, leading to corrosion or poor adhesion between metals. Welders must take extra precautions, such as using tents or shelters, to minimize the impact of weather.
Mobility
Field welding requires moving equipment, materials, and sometimes the welders to various on-site locations. This presents logistical difficulties, especially in large construction projects or areas with difficult terrain. Limited mobility can slow down the process and make bringing all necessary tools and machinery to the worksite challenging. Portable welding equipment and efficient planning are essential to address these mobility issues.
Challenges in Field Welding and Solutions
Challenge | Impact | Solutions |
Weld Quality | Environmental factors can cause defects | Proper surface cleaning, weather protection |
Power Sources | Unstable power affects weld consistency | Use portable generators or reliable power sources |
Environmental Factors | Wind and moisture impact weld strength | Use protective covers or tents |
Mobility | Difficult to move equipment in some areas | Use portable, lightweight equipment |
Welding Symbols
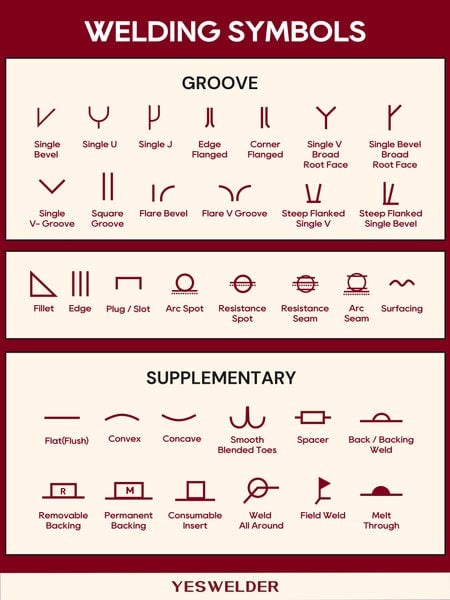
Welding symbols are essential in construction and engineering drawings to convey critical information about weld specifications. They provide details on the weld’s type, size, and orientation, ensuring welders understand how to execute the welds properly. Using standardized symbols makes communication between engineers, designers, and welders more precise and consistent. Below are key welding symbols used in the field:
- Arrow Line: Points to the location on the drawing where the weld needs to be made. Depending on the weld’s location, the arrow may point to either the joint or the opposite side.
- Reference Line: A horizontal line that carries additional welding instructions. The arrow connects this line to the joint, and specific symbols are placed above or below the reference line to indicate the type of weld.
- Tail: This is optional but used to include additional information such as welding procedures, specifications, or other instructions relevant to the weld.
- Contour Symbols: These symbols specify the shape of the weld face after completion. They indicate whether the weld should be flush, convex, or concave.
- Finish Symbols: If any post-weld finishing is required, such as grinding, machining, or polishing, a finish symbol is added to communicate this requirement.
- Weld Size and Length: The symbol indicates the weld size and length and provides information on how large and long it should be.
Field Weld Symbol
The Field Weld Symbol is a supplementary symbol used specifically for welds that must be carried out at the site rather than in a shop. The symbol is a flag attached to the reference line at an angle, indicating that the welding operation will occur outside a controlled environment. This symbol alerts welders to the potential need for adjustments based on environmental conditions.
- Flat Weld: This symbol indicates that the weld should be ground or finished to a flat surface.
- Convex Weld: Specifies a weld with a bulging or rounded contour.
- Concave Weld: This represents a weld with an inward curve, forming a slight depression.
- Spacer: Indicates using a spacer between the two parts being welded to ensure proper gap.
- Remove Backing: This shows that the backing material used during welding should be removed afterward.
- Grinding Required: This symbol indicates that the weld needs to be ground for a smoother finish.
- Back Weld: Represents a weld applied on the opposite side of the original weld for reinforcement.
Field Welding Considerations
Environment
Field welding often occurs in uncontrolled outdoor settings, bringing several environmental challenges. Wind can disrupt gas-shielded welding processes by blowing away shielding gas, leading to weld defects. Moisture from rain or humidity can cause rust or other contamination on the welded surfaces. Extreme hot or cold temperatures can affect the weld quality and operator performance. Welders must use protective covers, such as tents, to control the environment and ensure that welding conditions remain optimal.
Safety Precautions
Safety is a top priority in field welding. Welders are often exposed to hazards like sparks, fumes, and hot metal, so wearing proper personal protective equipment (PPE) is essential. This includes flame-resistant clothing, welding helmets with shields, welding gloves, and boots. Additionally, it is important to ensure that the work area is free from flammable materials and that there is proper ventilation to avoid harmful fume buildup. Regular safety checks of equipment and surroundings are crucial to minimize risks.
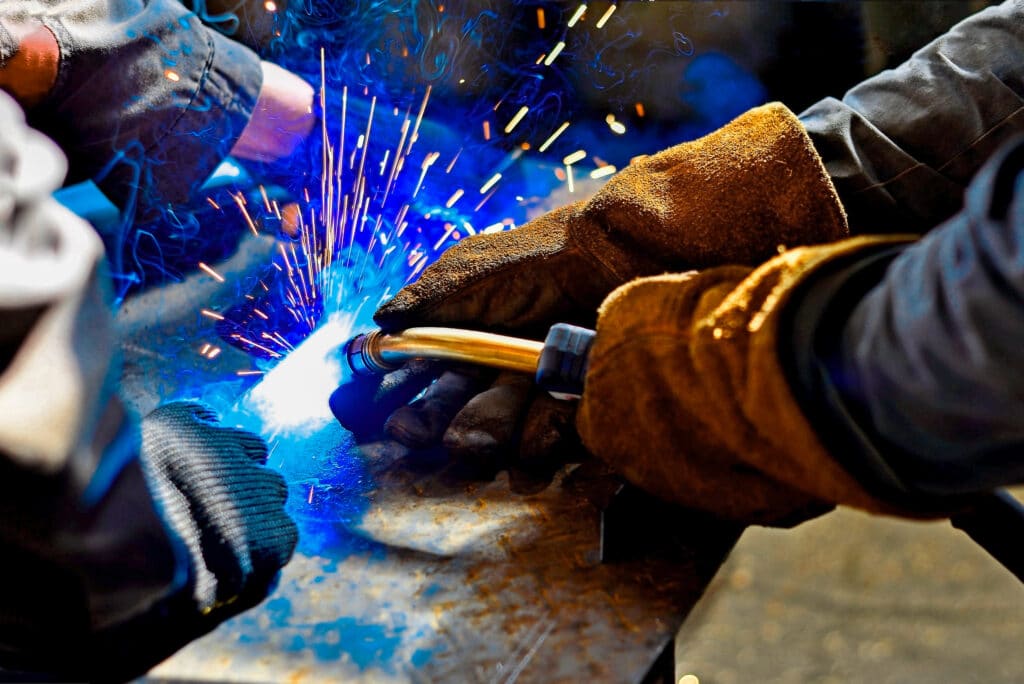
Welding Machines
The type of welding machines used in field welding plays a critical role in the operation’s success. Due to the nature of the work, field welders often rely on portable machines. These machines should be easy to transport and deliver consistent power even in remote areas. Portable generators or battery-operated machines are commonly used without a direct power supply. Proper machine maintenance is also vital, as malfunctioning equipment can lead to poor weld quality and potential safety risks.
Welding Standards
Adhering to welding standards ensures the structural integrity and safety of welded joints. Field welders must follow codes set by organizations such as the American Welding Society (AWS) or other regional regulatory bodies. These standards provide guidelines on acceptable weld quality, material selection, and testing requirements. Compliance with these standards ensures that welds are safe, durable, and meet the necessary quality levels for their intended application.
Final Thoughts
Field welding is an essential process that requires careful attention to various factors like environment, safety, and equipment. Field welders can produce high-quality, reliable welds after understanding and addressing challenges like power sources and environmental conditions. Using the right methods, a proper welder from welding machine suppliers, maintaining safety standards, and adhering to welding codes ensures successful outcomes. Proper planning and preparation are key to overcoming the complexities of field welding and achieving strong, durable joints in any situation.
FAQs
What is field welding, and how is it different from shop welding?
Field welding is performed on-site, while shop welding occurs in a controlled workshop. Field welding is used when transporting materials to a shop isn’t practical.
What are the common challenges in field welding?
Common challenges include maintaining weld quality, managing power sources, dealing with environmental conditions, and ensuring equipment mobility.
What welding methods are commonly used in the field?
Stick, MIG, TIG, and Flux-Cored Arc Welding (FCAW) are common methods.
What safety precautions should be followed during field welding?
Wear protective gear, ensure proper ventilation, and keep the workspace hazards-free.