Welding stainless steel presents significant challenges due to its heat sensitivity, which can lead to warping, discoloration, or corrosion if not properly handled. These issues arise primarily from stainless steel’s low thermal conductivity and high expansion rate, making it more complex than welding other metals.
However, utilizing the correct types of stainless steel welding, such as TIG, MIG, or laser welding, ensures the process is efficient and durable. These techniques allow for precise control, minimize heat impact, and ensure high-quality results, making them ideal for industrial and specialized applications.
Stainless Steel Welding
Stainless steel welding is the process of combining stainless steel components by applying heat and pressure. Due to its unique properties, stainless steel is more difficult to weld than other metals. It requires careful temperature control to prevent warping and preserve its corrosion-resistant characteristics.
Depending on the type and thickness of the stainless steel, various techniques, such as TIG, MIG, and laser welding, are used. These methods ensure the structural integrity and longevity of the material in a wide range of industrial applications.
Applications for Stainless Steel Welding
Automotive Industry
Stainless steel welding is crucial for manufacturing exhaust systems, chassis components, and fuel tanks in the automotive industry. The material’s resistance to corrosion and high temperatures ensures durability, especially in harsh environments like engine compartments.
Food Processing Equipment
In food processing, stainless steel welding creates hygienic, corrosion-resistant surfaces for equipment such as conveyors, mixers, and storage tanks. Its smooth surface makes it easy to clean and maintain, which is essential for maintaining food safety standards.
Architectural and Structural Welding
Stainless steel is commonly used in architectural applications, including facades, roofing, and structural frameworks. Its strength, aesthetic appeal, and resistance to weathering make it an ideal choice for decorative and load-bearing structures.
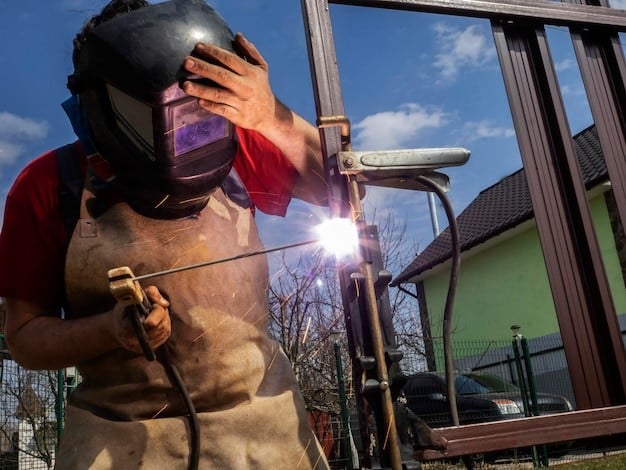
Marine Industry
In the marine industry, stainless steel is welded to construct ship components, such as rails, ladders, and hulls, that must withstand constant exposure to saltwater. Its anti-corrosive properties ensure a longer lifespan for maritime vessels.
Medical Equipment
Stainless steel welding is essential in the medical field for producing surgical instruments, hospital beds, and other medical equipment. The material’s biocompatibility and ease of sterilization make it ideal for healthcare environments.
Chemical and Petrochemical Industry
In chemical plants and refineries, stainless steel welding is used to manufacture pipes, tanks, and reactors that resist corrosive substances. Its ability to handle extreme temperatures and chemical exposure ensures the longevity of these critical components.
Energy Sector
The energy industry relies on stainless steel welding to construct parts used in power plants, pipelines, and renewable energy systems. Its durability and heat-resistant properties make it suitable for high-stress environments, such as oil refineries and nuclear reactors.
Types of Welding Methods for Stainless Steel
Stick Welding
Stick welding, also known as Shielded Metal Arc Welding (SMAW), is a versatile method suitable for welding stainless steel outdoors. It involves using a consumable electrode coated in flux, which protects the weld from contamination. A stick welder is widely used for construction and repair work, particularly in less controlled environments.
MIG Welding
Metal Inert Gas (MIG) welding is another popular method for stainless steel welding. It uses a continuous solid wire electrode fed through a welding gun. Shielding gas, such as argon or a mixture, prevents contamination. MIG welding suppliers often provide the machine with speed and efficiency in creating clean, strong welds.
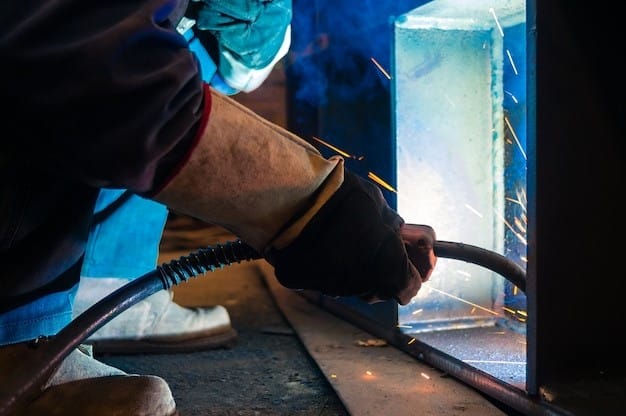
TIG Welding
Tungsten Inert Gas (TIG) welding is a precise method ideal for welding thin stainless steel materials. It utilizes a non-consumable tungsten electrode and a separate filler metal if needed. Hence, TIG welder suppliers provide the welder with greater control over the weld, making it perfect for intricate applications.
Laser Welding
Laser welding is a modern method used in high-tech industries for stainless steel applications. This technique uses focused laser beams to create fine, precise welds with minimal heat distortion. It’s ideal for delicate, small-scale projects where accuracy is paramount, such as in medical or electronic industries.
Comparison of Welding Methods for Stainless-steel
Welding Methods | Gases Used | Applications | Benefits |
Stick Welding | uses flux | Construction and repair work (outdoor environments) | Versatile and can be used in challenging environments |
MIG Welding | Argon, CO2, Argon/CO2 mix | Industrial manufacturing (clean, fast welds) | Fast and efficient, suitable for high-volume work |
TIG Welding | Argon, Helium mix | Precision applications (thin materials, intricate work) | Provides precise control for high-quality results |
Laser Welding | No gas needed | High-tech industries (medical devices, electronics) | Minimal heat distortion, ideal for delicate components |
Stainless Steel Welding Gas Types
Argon
Argon is the most commonly used gas in stainless steel welding. It provides a stable arc, ensuring smooth and clean welds. Argon is often used in TIG welding because it helps prevent oxidation and ensures minimal contamination during the process.
CO2
Carbon dioxide (CO2) is another commonly used gas in stainless steel welding, particularly in MIG welding. CO2 allows for deep penetration, making it ideal for thicker materials. However, it can produce more spatter compared to other gases.
Argon/Helium Mix
A mixture of argon and helium is often used in TIG welding for stainless steel. Helium increases the weld’s heat, allowing faster welding speeds and improved penetration. This mix is especially useful for thicker stainless steel applications.
Argon/CO2 Mix
The combination of argon and CO2 is frequently used in MIG welding. This mixture offers the benefits of both gases: Argon provides arc stability, while CO2 enhances penetration. The mix is effective for a wide range of stainless steel thicknesses.
Nitrogen
Nitrogen is sometimes added to the shielding gas when welding certain grades of stainless steel. It helps increase corrosion resistance, especially in austenitic stainless steel, often exposed to harsh environments. Nitrogen is commonly used in the food and chemical industries.
Stainless Steel Welding Gases and Their Effects
Gas Type | Application | Effect on Weld | Typical Use Cases |
Argon | TIG, MIG welding | Provides arc stability, reduces oxidation | Most stainless steel applications |
CO2 | MIG welding | Deeper penetration, more spatter | Thicker materials |
Argon/Helium Mix | TIG, MIG for thick materials | Increases heat and weld speed | Thick stainless steel |
Argon/CO2 Mix | MIG welding | Balance between penetration and arc stability | General welding tasks |
Stainless Steel Welding Rod Types
ER308/ER308L
ER308 and ER308L are widely used filler rods for welding 304 and 304L stainless steels. These TIG welding rods offer excellent corrosion resistance and are suitable for general-purpose applications. ER308L contains less carbon, which helps reduce carbide precipitation, making it ideal for applications requiring high corrosion resistance in low-temperature environments.
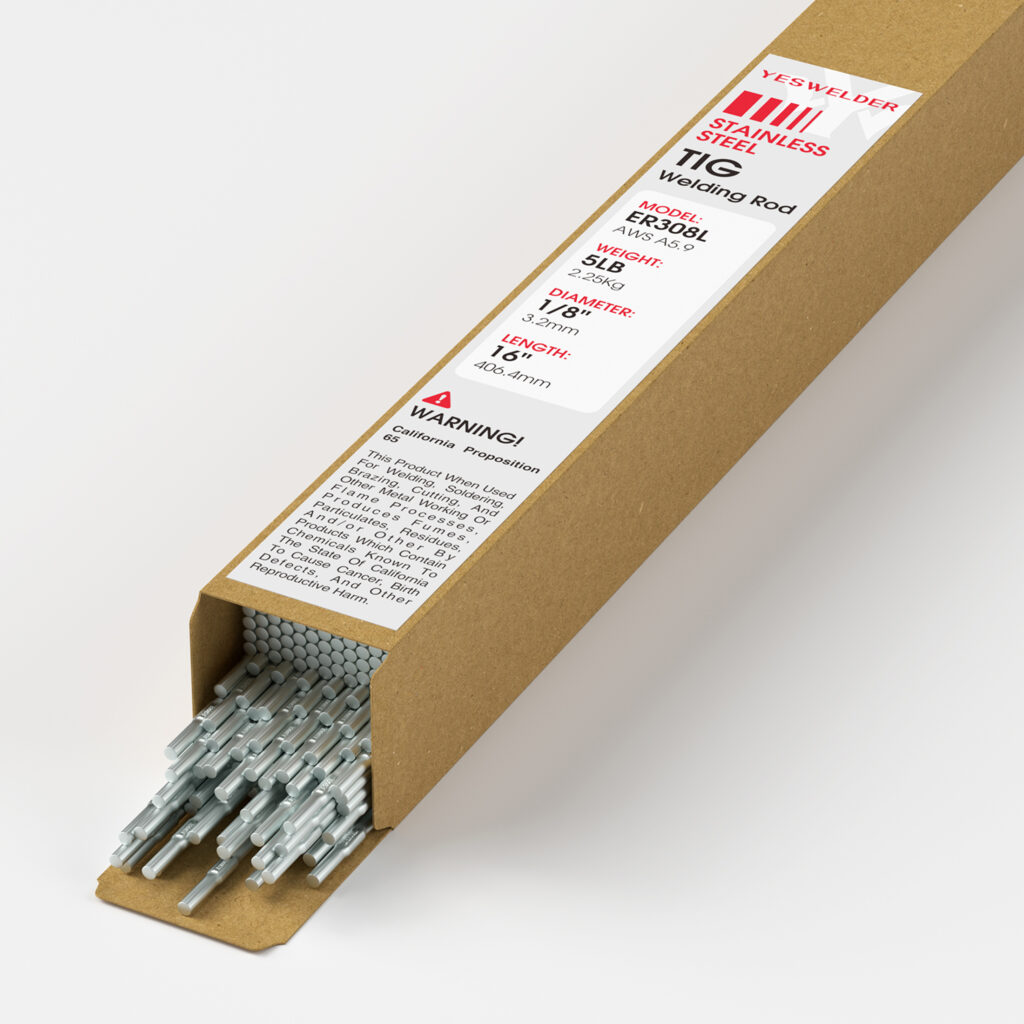
ER309/ER309L
ER309 and ER309L rods weld dissimilar metals like stainless steel and carbon steel. These rods are often employed when welding higher-alloy stainless steels, which require additional strength and corrosion resistance. The lower carbon content in ER309L helps minimize carbide precipitation, improving resistance to corrosion in high-heat environments.
ER316/ER316L
ER316 and ER316L rods are commonly used to weld 316 and 316L stainless steel. These filler rods provide excellent resistance to corrosion, especially in chloride environments. The low carbon content in ER316L minimizes the risk of carbide precipitation, making it suitable for applications in harsh conditions, such as chemical plants and marine environments. This rod type is ideal for industries where resistance to pitting and corrosion is critical.
Welding Rods and Their Applications
Rod Type | Suitable For | Corrosion Resistance | Best For |
ER308/ER308L | 304/304L stainless steel | High | General-purpose welding |
ER309/ER309L | Dissimilar metals | Moderate | Welding stainless to carbon steel |
ER316/ER316L | 316/316L stainless steel | Very High | Marine and chemical industries |
Stainless Steel Welding Considerations
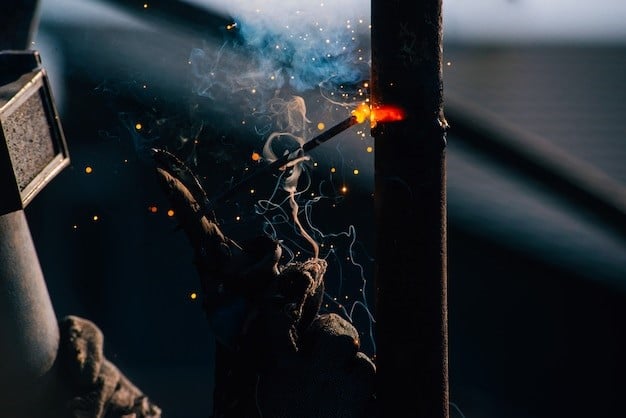
Heat Control
- Stainless steel is highly sensitive to heat, which can lead to warping or distortion.
- Control the heat input by reducing amperage and using short welding passes.
- Excessive heat can cause discoloration, affecting the corrosion resistance of the metal.
- Utilize cooling techniques such as water or air to minimize heat damage.
Pre-Weld Cleaning
- Proper cleaning is essential to remove contaminants like oil, dirt, and grease from the surface.
- Use stainless steel wire brushes or chemical cleaners to prepare the material.
- Failure to clean the surface may result in poor weld quality and potential corrosion.
- Clean both sides of the joint to ensure a strong weld.
Post-Weld Treatment
- Post-weld cleaning, such as pickling or passivation, restores the stainless steel’s corrosion resistance.
- Remove any heat discoloration using wire brushes or chemical treatments.
- Post-weld heat treatment may be necessary for certain grades to restore material properties.
- Inspection of the weld is essential to ensure it meets quality standards.
Shielding Gas Selection
- The type of shielding gas used affects the weld quality and appearance.
- For TIG welding, argon is commonly used due to its stable arc and minimal contamination.
- Mixed gases like argon/helium or argon/CO2 enhance penetration for thicker materials.
- Proper shielding gas prevents oxidation and enhances the weld’s durability.
Joint Design
- The design of the weld joint can impact the weld’s strength and overall quality.
- Consider the thickness and type of stainless steel when designing the joint.
- Ensure adequate space for penetration, particularly with thicker materials.
- Joint design should accommodate the welding method being used for optimal results.
Final Thoughts
Welding stainless steel requires careful attention to techniques, materials, and conditions. Proper heat control, cleaning, and post-weld treatment are critical to ensuring the quality and durability of the weld. The integrity of stainless-steel structures can be maintained by selecting the right welding method and considering factors like shielding gas and joint design.
Each process step, from preparation to final inspection, is crucial in achieving a reliable weld. Following best practices and working with reliable welding machine suppliers help ensure the longevity and performance of stainless steel in various industrial applications.
FAQs
What is the best method for welding stainless steel?
TIG welding is often considered the best method for welding stainless steel due to its precision and control, especially for thin materials. However, MIG welding is faster for thicker materials.
What gas is used for stainless steel welding?
Argon is the most commonly used gas for stainless steel welding. Sometimes, mixtures like argon/CO2 or argon/helium are used for specific applications to enhance penetration.
Why is heat control important in stainless steel welding?
Heat control is crucial during welding to prevent warping, discoloration, and damage to the material’s corrosion resistance.
What are the common types of stainless-steel welding rods?
ER308, ER309, and ER316 are the most commonly used stainless steel welding rods, each suitable for different grades and applications.