Welding is one of the most important activities in industries like building, manufacturing, and shipbuilding. With technological development, remote control welding has appeared. It allows the performance of welding processes by an operator from a distance. The technique mainly appears in hazardous or unreachable environments, increasing safety and improving productivity. Now let’s examine remote control welding, its advantages and challenges.
What is Remote Control Welding
Remote control welding is a welding method. By using robotic arms or automated systems, operators can operate the welding activity remotely. It becomes crucial in areas where human intervention might be hazardous or inefficient. Advanced controls enable operators to manipulate welding equipment remotely in real-time or through pre-programmed actions.
Conventional welding requires the presence of a welder at the site. However, the work site is hard to access for welders. Remote welding plays well in underwater maintenance, space exploration, and hazardous industrial works in nuclear plants or chemical factories. Greater flexibility expands operation possibilities and accessibility to difficult environments without sacrificing safety.
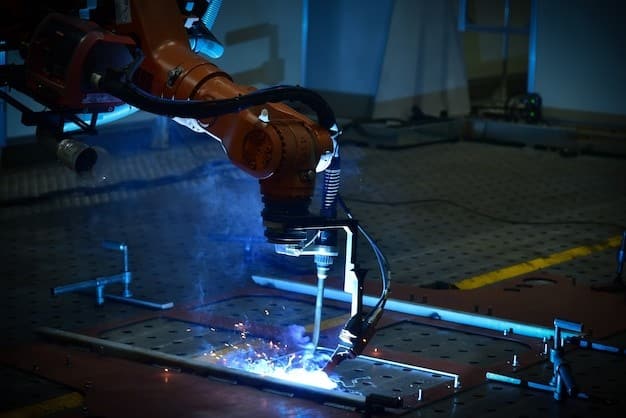
Why Remote Control Welding
Remote control welding is indispensable in various industries where manual welding with PPE (welding helmets, welding caps, welding gloves, and so on) may still be unsafe.
Dangerous Environments
Using remote control welding reduces human exposure to extreme heat, radiation, or toxic chemicals. This point is critical in industries dealing with oil and gas, mining, or nuclear power. Workers may be subjected to severe health hazards if brought into direct contact with the welding environment.
Difficult-to-Reach Locations
Welding tasks require access to areas impossible or hard to reach manually. That has been the case in high-rise construction, bridge repairs, and even welding underwater. Remote-operated devices can do such tasks without exposing a welder to an unsafe situation.
Increased Accuracy
Greater precision of the remote welding systems is mainly in repetitive work. Using sensors, response systems, and AI integration, these systems ensure better consistency in weld quality than manual methods.
Higher Productivity
Automation of repeated processes using remote welding systems translates to faster execution of tasks. That reduces the incidence of idle periods, increasing productivity. In fact, that is the case in manufacturing industries.
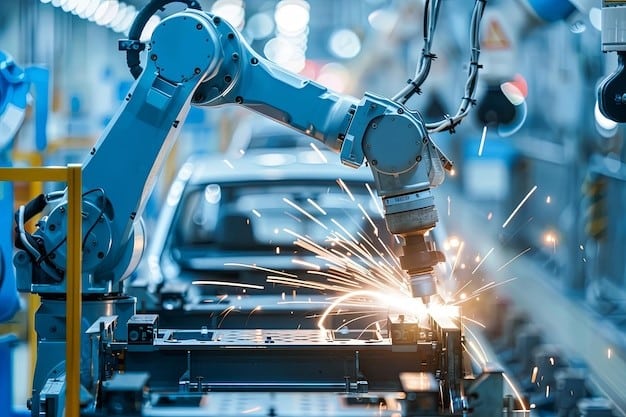
Key Remote Welding Technologies
The possibility of remote control welding depends on various technologies, which contribute to specific applications and environments.
1. Robotic Welding Systems
Robotic arms can execute welding tasks automatically or under the control of a remote operator. In this regard, robotic systems find wide applications in automotive manufacturing for high-level precision and repeatability.
2. Welding Drones
Drones with welding tools and equipment have accessibility to tall buildings, ships, or infrastructures. They undertake work demanding much agility, and flexibility. Also, they are to be carried out on high and dangerous sites.
3. Automated Welding Arms
Automated welding arms are a common sight in factories. They are for continuous welding of the same type with a lot of precision. They are ideal for jobs that require uniformity and repetition.
4. Advanced Controllers and Interfaces
The operators use a range of controllers to manage the remote welding tasks. These interfaces may range from handheld units to immersive virtual reality systems. They should allow the user to monitor and control the welding process in real time.
Types of Remote Welding Equipment
The remote welding equipment deployed depends on the complexity of the tasks to be performed, the environment in which it is expected to operate, and particular industry requirements.
Remote Welding Equipment | Pros | Cons |
Robotic Welding Arms | High precision, repetition | Requires skilled operators, maintenance-intensive |
Magnetic and Tracked Devices | Stable, adaptability to hostile environments | Limited flexibility, complicated rigging |
Portable Remote Units | Light, easy to transport | Only in small and mid-projects |
Robotic Welding Arms
Pros: High precision, good for repetition, suitable for industrial use where quality should be maintained.
Cons: Costly at the initial stage, requires skilled operators, and is maintenance-intensive.
Applications: Automotive, Heavy machinery, Mass production.
Magnetic and Tracked Devices
Pros: Stable, welding of flat surfaces, like ship hulls or pipelines; adaptability to hostile environments.
Cons: Limited flexibility of movement, complicated rigging, suitable for only specific applications, such as huge structures.
Applications: Shipbuilding, oil and gas, large construction projects.
Portable Remote Units
Advantages: light, flexible, easy to transport, good versatility in fieldwork and repairs.
Disadvantages: Low precision when compared to robotic systems, it cannot work on large projects.
Applications: Repairing at site, building, and remote sites.
In real life, the pros and cons of different types of equipment depend on the task and may vary in terms of location, welding machine suppliers, and environment.
Challenges in Remote Control Welding
Remote-controlled welding enables a lot of facilities to enjoy quite a number of benefits. However, certain obstacles must be conquered for the process to be as effective as possible.

Visibility
Poor visibility resulting from reliance upon cameras or sensors mounted elsewhere can hamper the ability to perform precise welds. This is especially common in constrained or darkly lit areas.
Control Accuracy
Control accuracy is difficult to achieve even when the delay between the controller and the robotic device is minimal. Delays of even a small magnitude may lead to impairment in weld quality in accurate tasks.
Lag Time
Latency can happen in communications between the operator and welding equipment, especially over long distances or high data, causing a lag that impairs real-time adjustments.
High Costs
The investment in welding equipment for remote control welding is especially high. This would limit accessibility to smaller companies or less resource-intensive sectors.
Skilled Operator Requirements
Remote welding systems require a great deal of technical expertise. The operators should get special training on how to handle the remote equipment and understand the software interfaces. This usually adds to the cost and time needed for the effective implementation of the systems.
Safety Benefits of Remote Control Welding
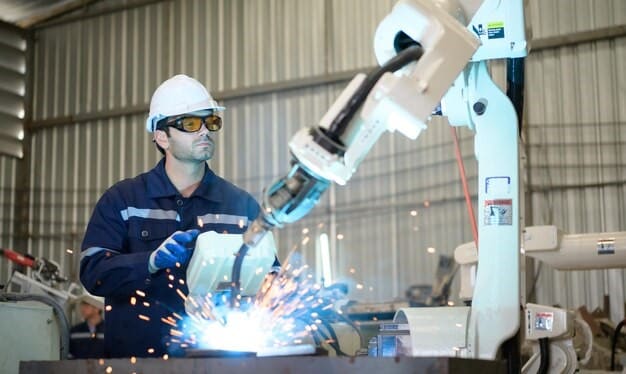
Among the general advantages offered by remote control welding are considerable improvements in safety. This method reduces direct exposure to hazardous environments such as intense heat, toxic fumes, high-pressure conditions, and radiation. This reduces the dangers of chronic illnesses and accidents in welders.
Welding operations conducted in confined or extreme conditions (underwater or at high altitudes) pose great risks to human operators. Remote systems make it possible to conduct such operations without hazardous risk to personnel.
To this end, remote control systems reduce the need for manual welding in hazardous areas, reducing the chance of burn injuries, falling object accidents, or equipment failure.
These safety benefits are one of the major reasons why remote welding technologies are becoming increasingly popular in risky industries.
Requirements for Remote Welding Operators
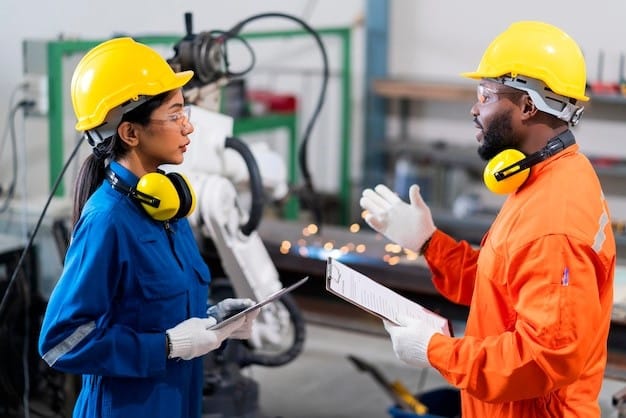
Operating remote welding equipment requires a unique skill set, other than the traditional training in welding itself. Operators should understand and manage advanced control systems like robotics, sensors, and computer interfaces. This requires technical expertise at the time of operation of the machinery while troubleshooting.
At the same time, the operator may be operating from a distance, but he must be conscious of the welding safety issues. This will involve understanding possible hazards of equipment and methods for mitigating these effectively.
Final Thoughts
Remote control welding facilitated a revolution in the welding industry, allowing operations in hazardous work sites without sacrificing safety. Although with some setbacks, advantages in terms of safety, precision, and efficiency make it truly useful in many other sectors.
As the technology continues to evolve, remote control welding systems will be more accessible and capable. Remote control welding allows companies to raise productivity and improve protection by dealing with tasks too difficult for manual completion.
FAQ
1. What is the remote control welding process?
Remote control welding describes the execution of welding from a distance by automated systems or robots, which are controlled and operated by an individual with remote controllers or computer interfaces.
2. Where does remote control welding apply?
The best application of remote control welding could be in hazardous or unreachable environments. In these situations, operators can comfortably and safely execute their activities without necessarily being at the site.
3. What are the major technologies adopted in remote control welding?
Key technologies include robotic welding arms, drones equipped with welding tools, automated welding systems, and improved operator interfaces for remote monitoring and control.
4. What are the challenges in remote control welding?
Some of the challenges are visibility issues, control accuracy, lag time, high equipment costs, and operations performed by skilled technical personnel.
5. How does remote control welding improve safety?
It reduces human exposure to hazardous environments in welding, such as high heat, radiation, and toxic chemicals. This allows operators working under confinement or extreme conditions greater safety.