Welding is an indispensable process in industries from construction to automobiles. While the notion of welding involves essentially joining two materials metals by applying heat and cooling, what occurs internally is much different.
Understanding the metallurgy of the science of how metals behave during and after welding can greatly enhance the quality of your welds by reducing defects. This manual will outline the basic concepts of welding metallurgy and break them down into more recognizable pieces for a beginner to understand.
What is Welding Metallurgy?
The welding metallurgy forms the study of the effects that heat and processes have on metals involved in the welding process. Actually, when someone welds a metal, it isn’t only melting and joining the pieces. Changes also occur in the inside structure. All this changes everything from strength and resistance to corrosion or cracking.
Metallurgically, the heat of welding will melt, induce phase transformations, or cause changes in the grain structure of metals in distinct zones around the weld. Each zone reacts differently, so it is important to understand some metallurgical principles.
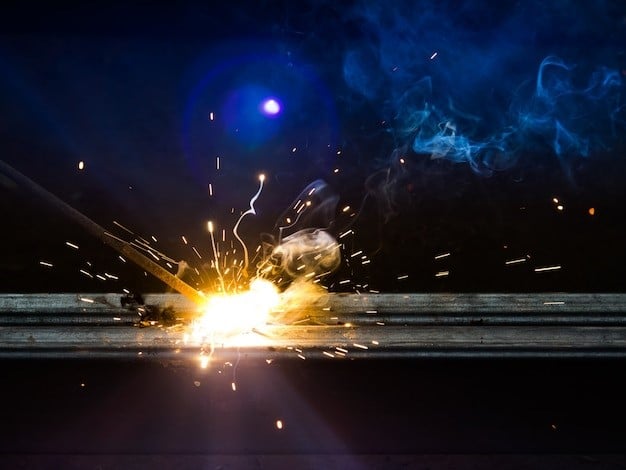
Basic Welding Metallurgy Terms
To adequately understand welding metallurgy, several terms are in common usage to understand. Understanding these basic terms is important in analyzing how welding affects metals.
Base Metal: The base metal is the one you should weld. The base metal may be steel, aluminum, or other metals. The composition and microstructure of the base metals determine the reaction upon heating.
Fusion Zone (FZ): This is the area where the melting and fusing of the base metals have been done to create the weld. The microstructure in this zone is altered considerably because of heat.
Heat-Affected Zone (HAZ): HAZ is the area of base metal that doesn’t melt but is under high temperatures. Change in microstructure and mechanical properties is quite common within this zone, and it is usually subjected to defects if proper care is not taken.
Grain Structure: The structure of metals consists of small crystals called grains. The size and orientation of these crystals affect the strength and other properties of a metal. The heat from welding may change the grain structure and usually leaves the metal more brittle or weaker.
Phase transformation: The base metals may undergo phase transformation on heating. Depending on the composition, steels may undergo crystalline transformation between definite temperatures that may affect the hardness and toughness of welded joints.
Microstructures: It deals with the grain structure and phases which may be entirely different in base metals, fusion zones, and HAZs.
Recrystallization: On cooling, new grains can develop and replace the deformed ones due to heat. This process will restore ductility to the metal but can be applied to strength as well.
Metal Structures
The metallurgy involved with welding includes a basic understanding of metal microstructures. This includes grains, crystal structures, phases, and so on. A proper understanding of grain and phase changes during welding helps in predicting the behavior of the metal in service.
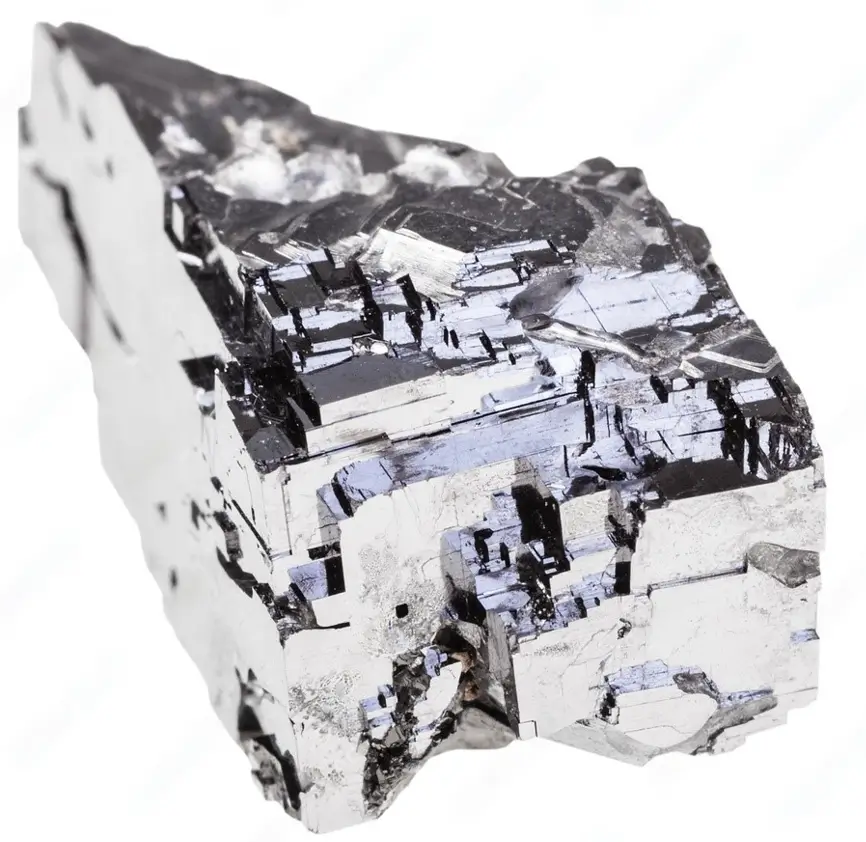
Grains
Metals are not homogenous to the level of microscopic examination. They consist of small crystals called grains, affecting their properties according to their size and shape.
The finer the grain, the more resistant and tough the material is, and vice if it has coarser grains, it may become brittle.
Crystal Structure
Metals have several crystal structures. Some of these structures include the body-centered cubic and the face-centered cubic.
In the crystal structure, it is indicated how atoms will be packed in a metal. The crystal structure further dictates several other properties including ductility and strength. These sorts of crystal structures alter when you apply heat through welding.
Phases
A phase is a homogeneous region in a material, like a liquid or solid. It needs to be pointed out that depending on temperature and composition, metals can exist in one or more phases.
During steel welding, depending on the cooling rates, the metal may pass through different phases like austenite and martensite with different mechanical properties.
Types of Welding Alloys and Their Properties
Metals and their alloys have different properties, which affect the type of welding processes applicable to them. Some of the common metals and alloys welded are below.
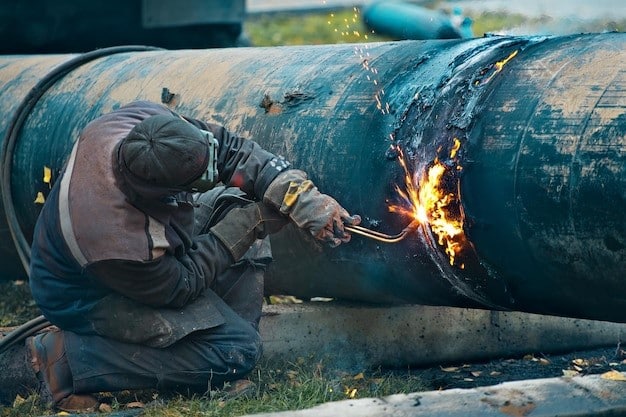
Steel
Steel is the most commonly welded metal. The carbon content has the most profound effect on the weldability of steel. Low-carbon steels are easily weldable, whereas high-carbon steels are brittle and tend to crack.
Stainless Steel
Stainless steel has chromium in its composition, offering good resistance to corrosion. However, it is more susceptible to distortion and warping during the welding process because of its greater thermal expansion.
Aluminum
Aluminum has a lighter mass and is a good conductor, which indicates that it will heat up and cool off quite rapidly while welding. Due to this rapid cycle of heating, there can be a possibility of cracking and other defects if precautionary measures are not taken.
Copper and Copper Alloys
Copper is also an excellent conductor. It needs to be treated specially to avoid overheating during welding. Also, it finds applications in places that desire the electrical conductivity of the material.
Common Alloy Properties
Strength: Varies based on the type of alloy and its heat treatment.
Ductility: Metals like aluminum are more ductile than high-carbon steels.
Thermal Conductivity: Thermal conductivity affects how quickly heat dissipates during welding, influencing cooling rates and potential for defects.
Metallurgical Defects in Welding
Welding will introduce a variety of metallurgical defects that can affect the weld integrity.
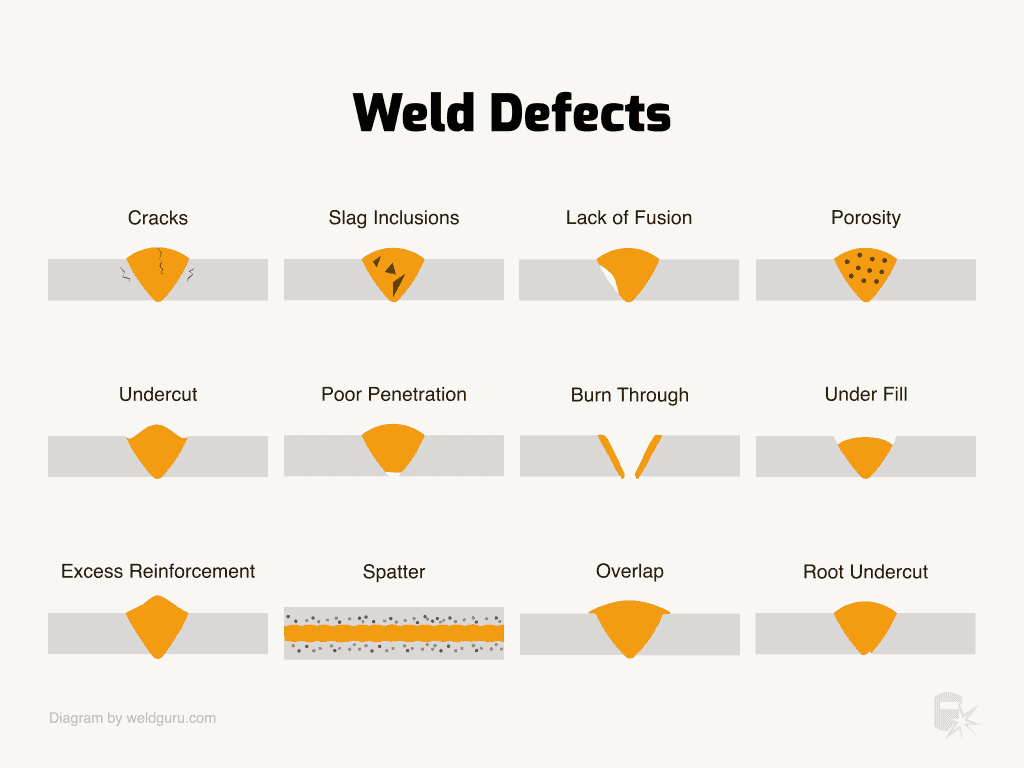
Cracks
These occur when the metal is subjected to tensile stress during cooling. Cracks can form in the fusion zone or heat-affected zone. The problems are often the result of poor weld design, improper cooling rates, or contamination.
Porosity
The entrapped gas in weld metal creates small voids or pores that weaken the weld. It generally happens because of impurities (moisture or grease) on the base metal or the filler material.
Distortion
Excess heat causes warping of the metal, causing dimensional inaccuracies. This is more common in metals having high thermal expansion, such as stainless steel and aluminum.
Insufficient Penetration
Insufficient welding heat to join the base metals will cause poor joints. This generally occurs due to insufficient heat input, improper welding parameters, or inadequate welding technique.
Oxidation
Most metals (like aluminum and stainless steel) form oxides upon being welded. All these oxides are brittle and can build a layer on the surface of the weld. The application of proper shielding gases can prevent oxidation.
Influence of Welding on Metallurgy
The welding technique to be adopted would have a manifold effect on the microstructural characteristics and the property profile of the metal.
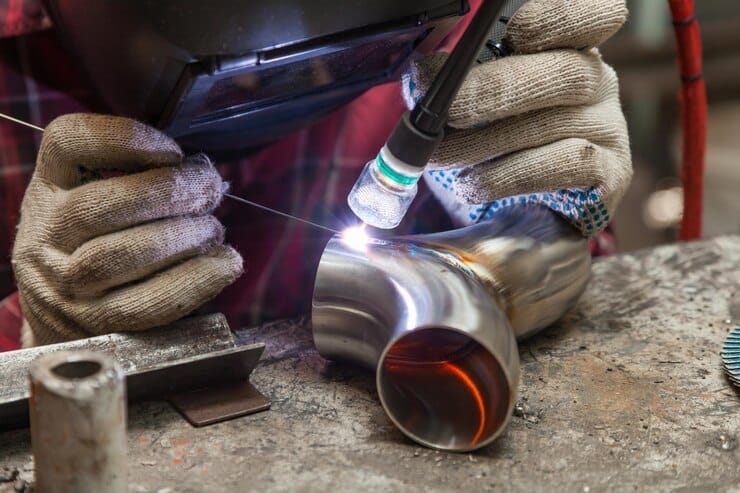
TIG Welding
TIG welding is attributed to clean, high-quality welds. Due to the relatively lower input heat, the area affected by heat can be restricted in size and minimize grain growth. TIG welder suppliers have proven this technique useful for welding materials that easily warp or crack.
MIG Welding
In MIG welding, the MIG welding wire feed continuously acts like filler material. A welding MIG machine can have a faster rate than TIG because of continuous filler metal feeding. However, this higher heat input may create larger grains in the heat-affected zone, which can reduce the weld toughness.
Stick Welding
Shielded Metal Arc Welding (SMAW), known as stick welding, is flexible and suitable for outdoor conditions. However, high input heat may create larger areas of heat influence, and the possibility of distortions will be bigger.
Other Specific Techniques
Cooling rate, heat input, and the particular technique determine the development of the metal microstructure during welding. Good control of these factors usually results in a strong and durable weld.
Closing Thoughts
Basic welding metallurgy is the first skill of any welder who wants to enhance his skills. Heat would result in changes in the metal microstructure and understanding these changes would help appropriately modify the welding process for minimum defects.
Also, using reliable welding equipment from reliable welding machine suppliers is another important factor. To achieve a quality weld, consider more details to make a success.
FAQ
What is the heat-affected zone in welding?
Heat Affected Zone (HAZ) is an area of base metal. Here the microstructure and mechanical properties have changed as a result of the welding heat. This can include under-gradations of grain structure and phase transformation, and changing mechanical properties, which may reduce its strength.
Why do cracks form in welds?
Cracks usually appear because of tensile stresses and cooling. Poor joint design, inappropriate cooling rates, contamination, and too much heat input can lead to cracking.
How do I prevent porosity in my welds?
Making contaminants (moisture, grease, or rust) kept away from the base metal and the filler material. Applying the proper shielding gas may also prevent porosity.
Which is the best of the following welding processes for welding aluminum?
TIG Welding is the most recommended since it allows better control of the heat input, minimizing distortion and cracking in the metal.