Industrial operations often face challenges in achieving precise and reliable welding for heavy-duty applications. Inefficiencies in welding processes can lead to compromised structural integrity, increased downtime, and higher operational costs.
These issues pose significant risks to productivity and safety for industries like construction, automotive, and shipbuilding.
Adopting advanced heavy-duty welding machines designed specifically for industrial use is the solution. These machines provide robust performance, enhanced durability, and the ability to handle demanding tasks with precision.
By investing in the right welding equipment, businesses can streamline operations, ensure quality, and meet stringent industry requirements. This article explores heavy-duty welding machines’ key features, types, and benefits to guide industries toward informed purchasing decisions.
Types of Heavy-Duty Welding Machines for Industrial Use
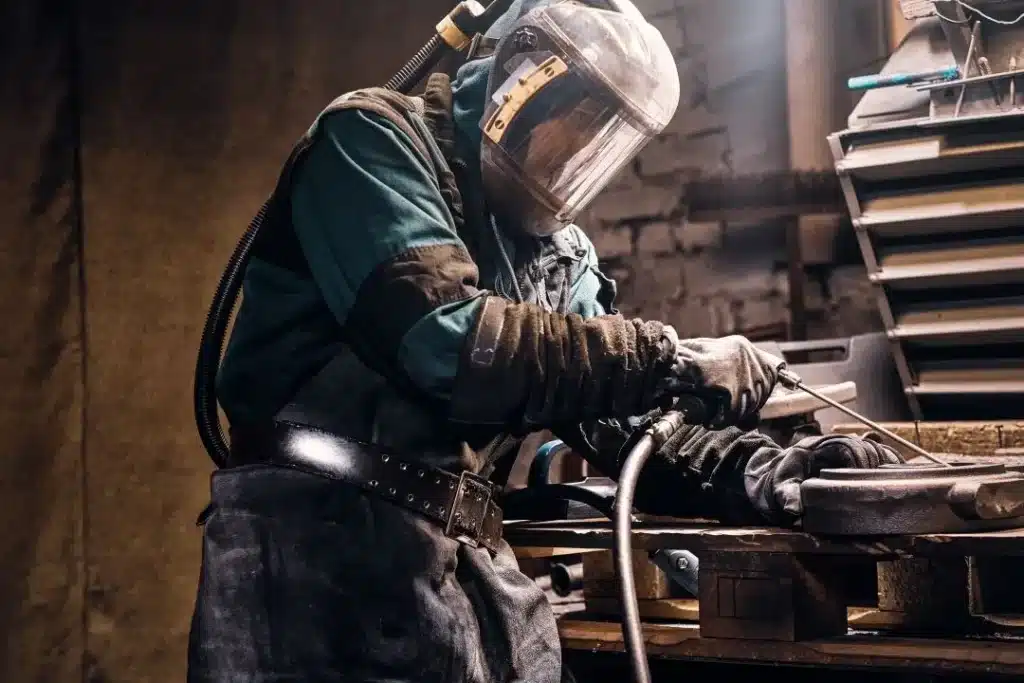
MIG Welders
MIG welders, or Metal Inert Gas welders, are highly versatile machines widely used in industrial settings. These welders use a continuous wire feed and shielding gas to produce clean and precise welds. They are ideal for high-volume projects and can handle a variety of materials, including steel and aluminum.
MIG welders from reliable MIG welding suppliers are known for their ease of use, making them suitable for experienced welders and newcomers.
TIG Welders
TIG welders, or Tungsten Inert Gas welders, are preferred for tasks requiring exceptional precision. These machines use tungsten welding electrodes and shielding gas to create high-quality welds.
TIG welders from TIG welder suppliers are commonly used for thin materials like stainless steel and aluminum. They offer excellent control over welding, making them ideal for intricate projects and industries demanding superior finishes.
Stick Welders
Stick welders, or Shielded Metal Arc Welders (SMAW), are robust and suitable for outdoor applications. These machines use an electrode stick to create welds and perform well even in challenging conditions, such as windy or damp environments. Stick welder suppliers recommend them since they are versatile and effective for heavy-duty tasks, particularly construction and repair work.
Multi-Process Welders
Multi-process welders combine the capabilities of MIG, TIG, and Stick welders into a single unit. These machines provide flexibility and efficiency, allowing operators to switch between welding processes based on project requirements.
Multi-process welders are highly valued in industries where diverse welding tasks are common, reducing the need for multiple machines and saving time and costs.
What to Look for in Industrial Welding Machines
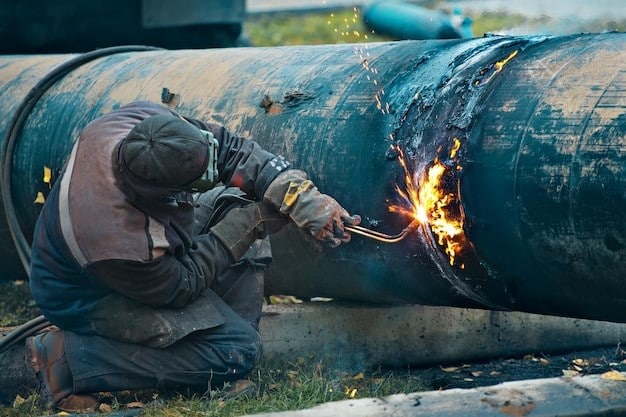
Power Output
Power output is a critical factor for businesses selecting an industrial welding machine. It determines the machine’s capability to handle various material thicknesses and industrial-scale welding tasks.
Higher power output is essential for heavy-duty applications common in large-scale projects, while adjustable settings enable customization for diverse operational needs. Choosing a machine with adaptable power ensures efficiency across different production demands.
Durability and Build Quality
Durability is paramount for industrial welding machines, which must withstand rigorous use in demanding environments. Machines built with industrial-grade materials, such as reinforced steel frames, are reliable for uninterrupted operations.
High build quality reduces the risk of frequent repairs, minimizing downtime and ensuring consistent productivity. Investing in a durable machine supports long-term business operations and reduces the total cost of ownership.
Portability
Portability is an important consideration for businesses requiring welding equipment for multiple job sites or on-site projects. Lightweight designs and features like built-in wheels and ergonomic handles facilitate easier transport and setup.
Portable machines enable distributors and contractors to quickly adapt to different locations without sacrificing performance. This flexibility can be a significant advantage in industries like construction and repair.
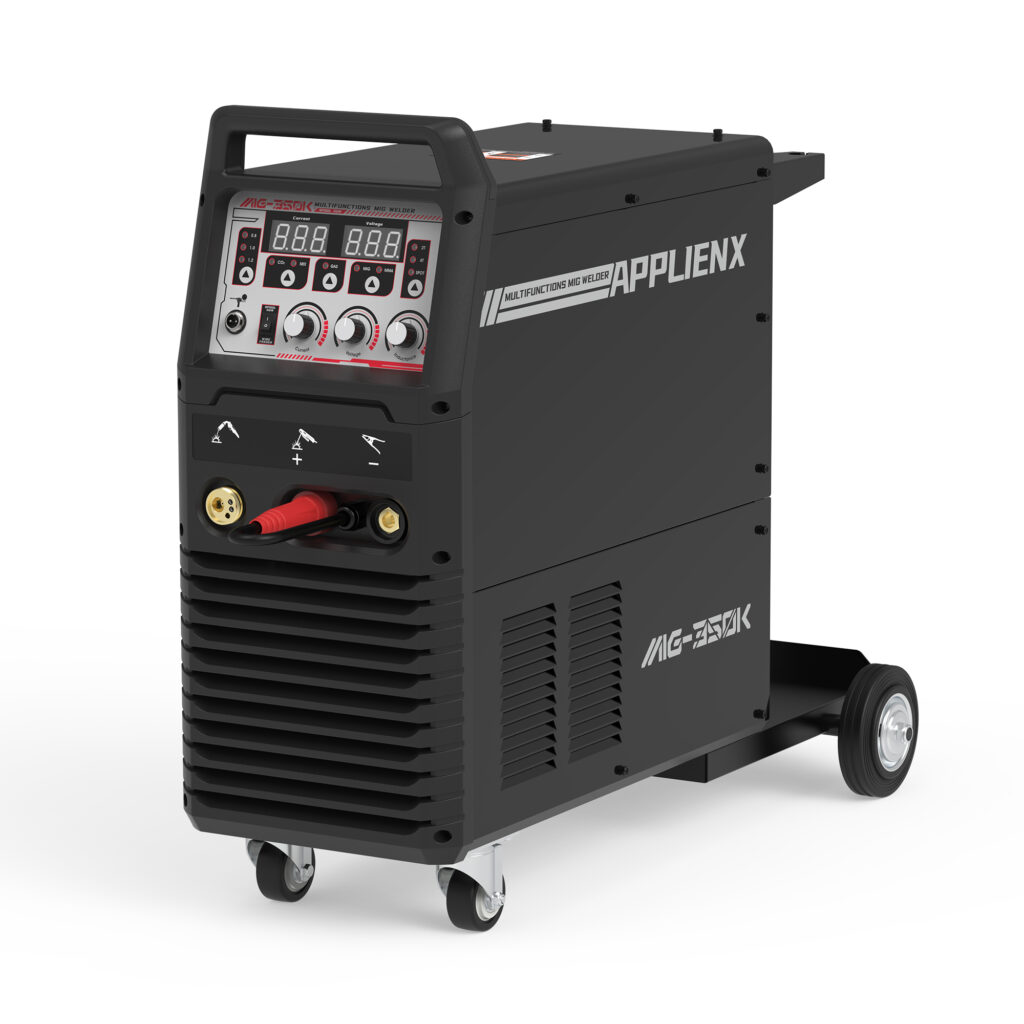
Advanced Control Features
Advanced control features are essential for achieving precision and operational efficiency in industrial welding. Digital interfaces, programmable settings, and stability controls enable operators to maintain consistent results across various projects.
These features streamline workflows, particularly for high-volume production environments. Machines with user-friendly controls allow distributors to offer equipment that meets the diverse needs of their industrial clients.
Energy Efficiency
Energy efficiency is a growing priority for businesses seeking to reduce operating costs and meet sustainability goals. Machines with energy-saving technology offer substantial savings on electricity while maintaining top-tier performance.
For B2B buyers, offering energy-efficient welding solutions aligns with market demands for eco-friendly operations. This ensures both cost-effectiveness and compliance with environmental regulations.
Key Features to Look for in Industrial Welding Machines
Feature | Description | Advantages |
Power Output | Determines ability to handle various material thicknesses and industrial tasks. | Essential for thick materials in heavy-duty applications; adjustable settings for versatility. |
Durability | High-quality construction reduces downtime and enhances long-term reliability. | Minimizes repairs, ensures consistent productivity, and reduces total ownership cost. |
Portability | Lightweight designs and wheels enable easy transport for on-site work. | Facilitates mobility across job sites and supports flexible operations in confined spaces. |
Advanced Controls | Digital interfaces and programmable settings improve precision and workflow efficiency. | Ensures consistent results, simplifies operation, and enhances process control. |
Energy Efficiency | Reduces electricity consumption while maintaining performance, lowering costs. | Lowers operational expenses and aligns with sustainability goals. |
Specific Industry Requirements
Construction and Infrastructure
Welding machines must handle heavy-duty tasks under challenging conditions for construction and infrastructure projects. Equipment should be capable of joining thick steel beams and durable materials used in bridges, buildings, and frameworks.
Portability is critical for on-site applications, while reliability ensures uninterrupted operations in demanding environments. Machines with advanced controls enhance precision, especially in large-scale projects.
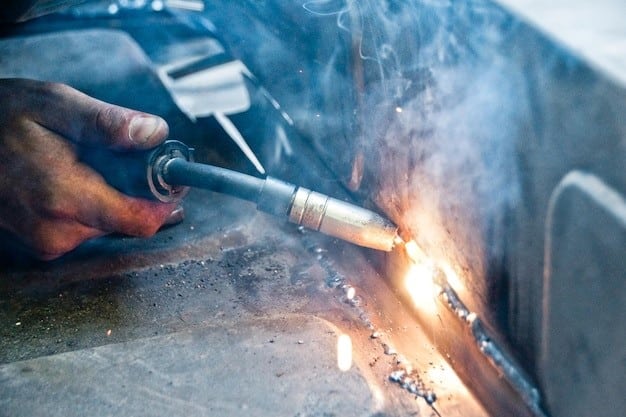
Automotive and Aerospace
The automotive and aerospace industries require welding machines that deliver precision and versatility. Lightweight materials like aluminum and specialized alloys are commonly used, necessitating machines with adaptable settings.
High accuracy is vital for assembling critical components like vehicle frames and aircraft parts. Machines designed for repeatable performance support consistent quality in high-volume production.
Oil and Gas
Oil and gas industries demand welding machines with robust performance for high-pressure and high-temperature applications. Equipment must handle thick pipes, storage tanks, and offshore platforms with precision and durability.
Portability is often needed for on-site repairs and installations. Machines with advanced features ensure consistent results even in extreme environmental conditions.
Shipbuilding
Shipbuilding projects require welding machines capable of working on large and complex structures. Durability is key to handling marine-grade materials and prolonged use in shipyards. Machines must offer high power output to join thick plates and structural components.
Flexibility in welding processes, such as MIG and Stick welding, is essential to accommodate various tasks in ship construction and repairs.
Industry-Specific Welding Requirements
Industry | Key Requirements | Recommended Features |
Construction | Machines for thick materials, durability in harsh environments, portability for on-site operations. | High power output, rugged build quality, portable designs with easy handling. |
Automotive/Aerospace | Precision and versatility for lightweight materials like aluminum and alloys. | Adjustable power settings, TIG capabilities for intricate welding tasks. |
Oil and Gas | Robust machines for high-pressure, high-temperature tasks with field portability. | Stick welders for durability, advanced controls for precise operation in extreme settings. |
Shipbuilding | High-power machines for large structures and flexibility in welding processes. | MIG and multi-process welders for varied tasks, corrosion-resistant materials. |
Benefits of Heavy-Duty Welding Machines
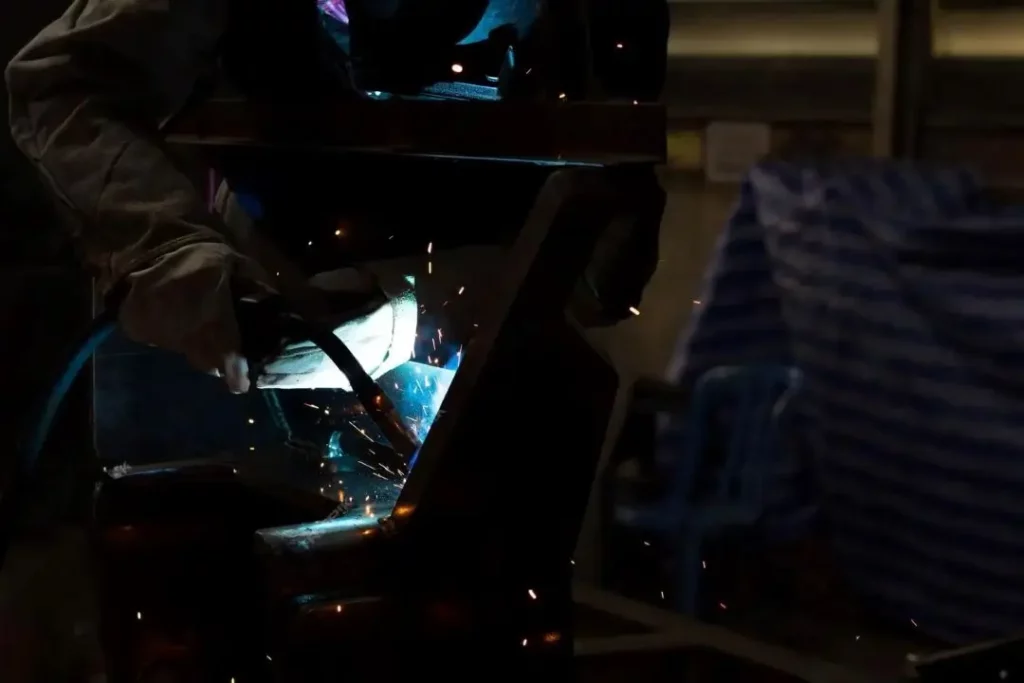
Enhanced Performance
Heavy-duty welding machines are designed to meet the demands of industrial applications. They deliver consistent performance when welding thick materials and handling complex tasks.
High power output ensures seamless operations, reducing the risk of errors and rework. Reliable performance enhances productivity and minimizes downtime, supporting efficient business operations.
Versatility
The versatility of heavy-duty welding machines allows them to handle a range of materials and tasks. From steel to aluminum, these machines can adapt to different project requirements.
Multi-process machines provide added flexibility, enabling operators to switch between MIG, TIG, and Stick welding. This adaptability is valuable for distributors catering to diverse industry needs.
Durability and Longevity
Industrial welding machines are built to withstand harsh environments and prolonged use. Their durable construction ensures a longer lifespan, reducing the need for frequent replacements.
Machines with reinforced frames and high-quality components can perform reliably over time. For B2B buyers, durability translates to cost savings and dependable performance in demanding conditions.
Cost Efficiency
Investing in heavy-duty welding machines offers long-term cost benefits for businesses. Their efficiency and reliability reduce maintenance and operational costs.
Energy-efficient models further decrease electricity expenses, making them an economical choice. These machines help businesses avoid costly delays and production issues by ensuring consistent performance.
Industry Compliance
Many heavy-duty welding machines are designed to meet specific industry standards and regulations. This ensures that businesses can maintain compliance with safety and quality requirements.
Machines with advanced features and high precision support adherence to industry guidelines. Compliance enhances trust with clients and partners, strengthening business relationships.
Why YesWelder is the Right Choice for Industrial Welding Solutions
YesWelder is a trusted supplier of industrial welding equipment, offering reliable solutions tailored for wholesale buyers and distributors. Their product range includes high-performance MIG, TIG, and Stick welders designed to meet industrial-scale demands.
Construction, manufacturing, and infrastructure businesses can rely on YesWelder for durable and cost-effective equipment.
YesWelder supports distributors with a unique trial sale model, allowing them to test market demand without significant initial investment.
Their machines are built for industrial use, combining power and precision to handle complex welding tasks efficiently. Advanced features, such as adjustable settings and energy-saving technology, ensure the equipment meets diverse operational needs.
YesWelder’s MIG welders are ideal for high-volume projects, offering consistent performance for various materials. Their TIG welders deliver exceptional precision, making them suitable for intricate tasks requiring fine control.
Stick welders from YesWelder are durable and effective, performing reliably in outdoor and challenging environments. These machines provide distributors with versatile options to cater to their client’s requirements, ensuring customer satisfaction and business growth.
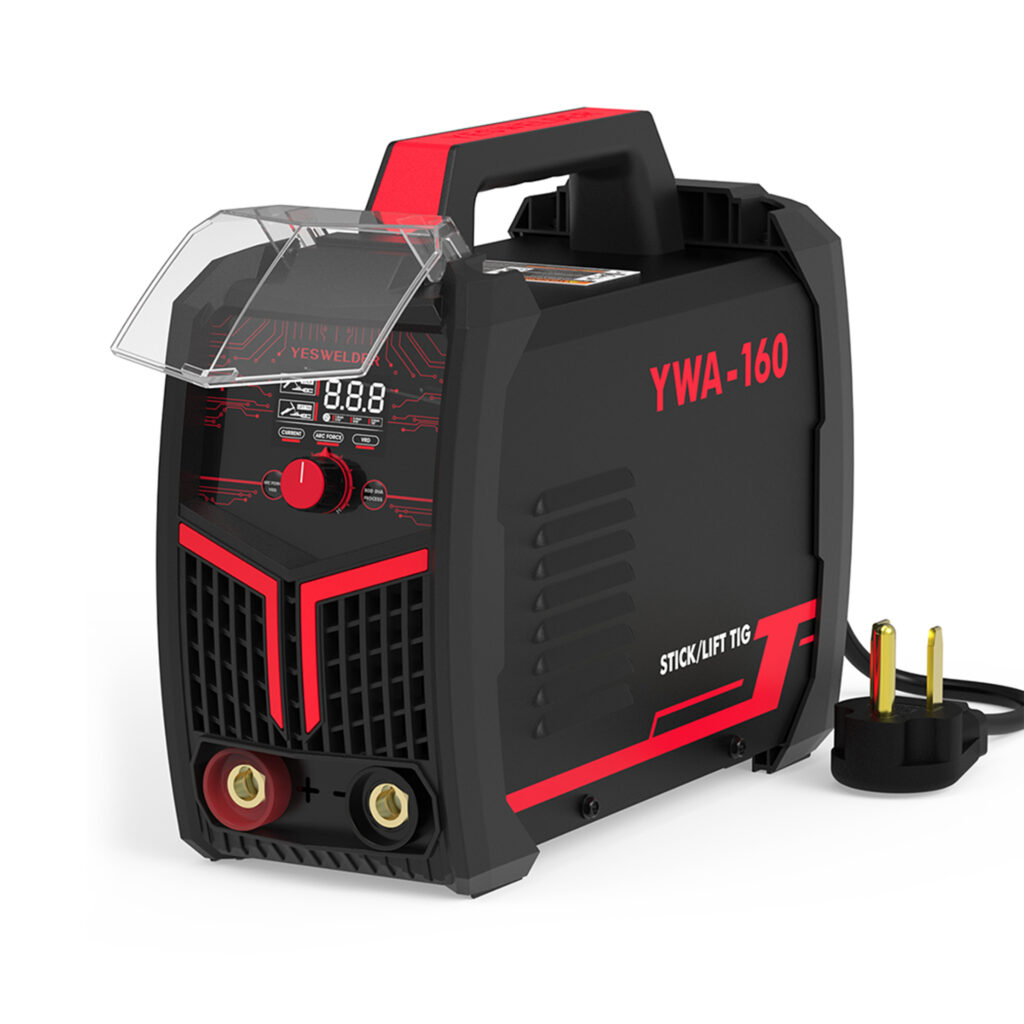
FAQs
What types of welding machines are best for industrial use?
MIG, TIG, Stick, and multi-process welders are popular for their versatility and precision.
How do I choose the right machine for my industry?
Match machine features to material types, precision needs, and work environments.
Are energy-efficient machines suitable for heavy tasks?
Yes, they combine performance with reduced energy consumption, lowering costs.
What support does YesWelder offer distributors?
Trial sales, wholesale pricing, and direct shipping ensure smooth operations.
Why are multi-process machines valuable?
They combine multiple welding capabilities in one unit, saving costs and increasing flexibility.