In the orbital welding process, an electrode moves in a circular path around a pipe or tube. A skilled person sets up the welder by programming the welding parameters. The key parameters include speed, voltage, amperage, and arc length, which help automate TIG welding for pipes and tubes.
Orbital welding utilizes precision welding technology that brings accuracy, consistency, and clarity to any welding project. We’ll learn here what orbital welding is, how it works, and why and when to use it as a game-changer for different applications.
What Is Orbital Welding?
Orbital welding refers to a process where the machine rotates around a pipe or tube 360°. It’s automated, so manual work disappears, and precision is achieved in the weld. It was developed to solve the manual operating issue of TIG welders from TIG welder suppliers. It creates a uniform weld around tubes and pipes, which was difficult in manual welding.
The TIG orbital welding is applied to complete repeatable welds using pre-programmed parameters. It mainly works for:
- Pipe-to-pipe joining
- Tube-to-tube welding
- Tube-to-tubesheet joining
- Narrow groove joining
- Weld overlay coating
- Filler welding
- Interior diameter welding
Components for Orbital Welding
Orbital welding does its best as a system but necessary components are needed to run it properly. Its key components are:
Power Supply: The power supply helps to convert electrical energy into the current for the weld. The AC power supply is ideal for aluminum. On the contrary, the DC power works efficiently for ferrous metals like stainless steel.
Weld Head: The weld heads rotate around the stationary materials. Different weld heads work for different materials considering types, thicknesses, and orientations. Large-diameter head works to weld pipes. Small-diameter head works more precisely for high-quality tube welding.
Tungsten Electrode: Tungsten welding electrodes are durable and heat-resistant, used for creating a suitable arc. It is a vital component in TIG (Tungsten Inert Gas) orbital welding.
Shielding Gas System: This system supplies inert gas like argon or helium to prevent imperfections in the weld area. It’s essential to ensure an oxidation-free weld.
Cooling System: It’s necessary to maintain the temperature of the equipment. During the long welding cycles, the system prevents overheating on the welding head.
How to Orbital Weld: Orbital Welding Process
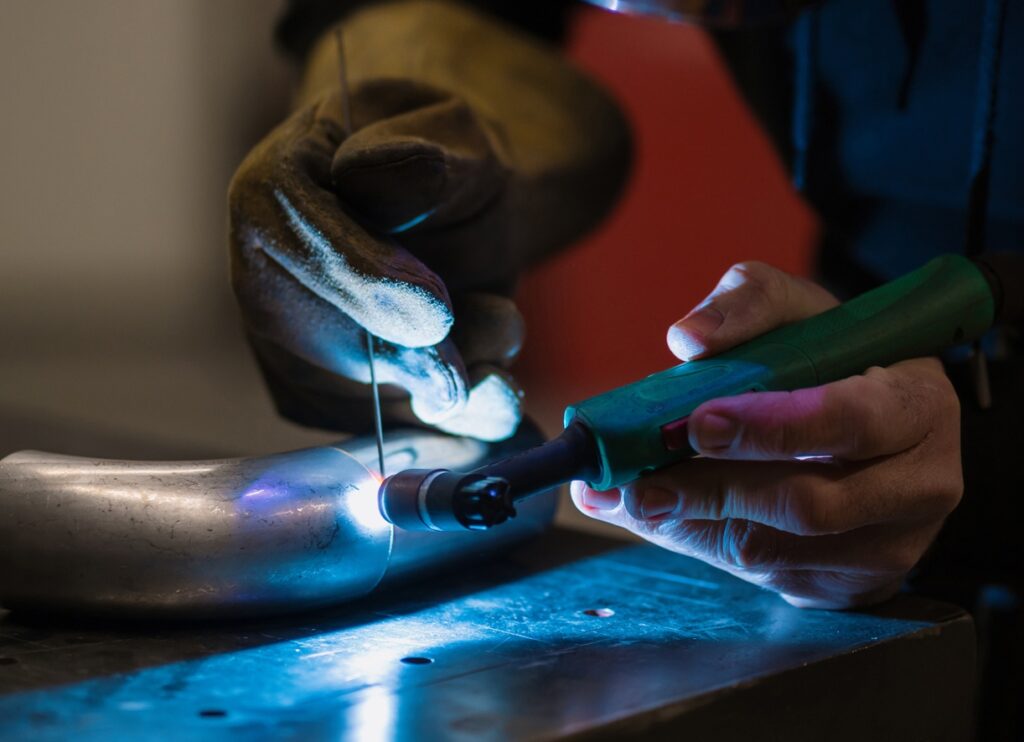
Orbital welding is an ideal welding method with minimal manual modification. It ensures repeatable and precise welds for applications like semiconductors, aerospace, and pharmaceuticals. This welding process can be done in the following steps.
- Preparing the Machine
- Surface Preparation
- Right Welding Method
- Selecting Parameters
- Time to Weld
- Careful Checking
1. Preparing the Machine
The welding machine should be programmed with the right parameters, including current, gas flow, speed, etc. For better welding on specific materials, tungsten electrodes are recommended.
Use a clamping system that can hold the pipe securely in place. Make sure it doesn’t damage the material.
2. Surface Preparation
Align the pipe accurately to avoid defective welding. Before it, cut the pipe to its length. Orbital saws can give you the best results when cutting the material. Prepare the material with the appropriate beveling tool.
Clean the pipe’s surface to remove dirt and grease. An abrasive tool or a cleaning solution can be handy at this stage.
3. Right Welding Method
There are various types of welding techniques available for precise welding. Gas tungsten arc welding (GTAW) is the most common orbital welding process. It’s ideal for thin-walled materials and provides precision.
Closed-head welding is used in enclosed areas. It helps to prevent contamination. Open-head welding is suitable for larger pipes.
4. Selecting Parameters
Depending on the pipe’s type and thickness, the welder needs to fix the welding current. Arc speed should also be optimized to confirm a consistent and perfect weld. To keep the weld area free from oxidation, apply a method to shield the gas flow rate. In this case, argon can work well.
5. Time to Weld
When starting the process, the TIG welding torch rotates around the material. It is managed by the pre-programmed parameter setting. Operator needs to monitor the welding progress. There might be some issues even though the whole process is automated.
After welding an area, allow it to cool naturally. Natural cooling will prevent cracking and ensure a uniform surface.
6. Careful Checking
Visual inspection is required after the first welding. Check carefully for uniformity, defects, and surface cracks. Implement any nondestructive testing (NDT) method to verify weld integrity. If necessary, take more steps to meet the project’s welding demands.
When to Use Orbital Welding?
Where traditional welding methods fail, orbital TIG welding becomes the go-to solution. There are some specific grounds when you need to apply orbital welding.
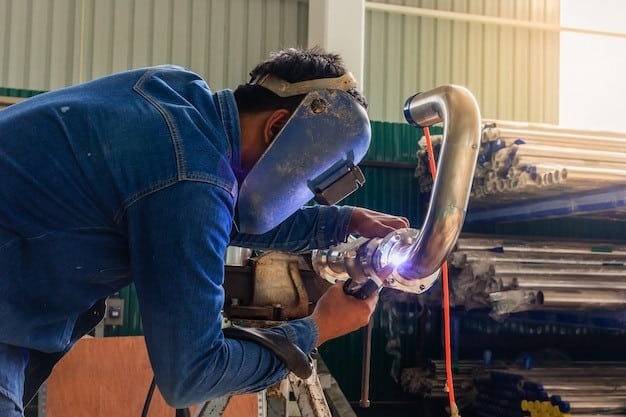
1. Welding with Consistency
Industries like aerospace, pharmaceuticals, and semiconductor manufacturing demand neat and clean, defect-free welds. These industries require welding that should meet strict quality standards. The automated nature of orbital welding minimizes inconsistencies that will happen for manual uses.
2. Welding in Hard-to-Reach Areas
Welding pipes or tubes in tight spaces is a challenge. Orbital welding offers a reliable solution; especially in areas that are hard to reach. The orbital head rotates 360 degrees around a stationary object. Thus, it can weld efficiently even in difficult positions.
3. High-Volume Production
Orbital welding is one of the fastest welding methods due to its pre-programmed feature. Once programmed, the machine can do welds repeatedly without making any difference. Therefore, it’s the best choice in industries where high-volume and repeated welding is a must.
4. Working with Particular Materials
Some metals like titanium and nickel alloys often require controlled heat input to avoid imperfections. Orbital TIG welding is preferred due to its ability to control heat and other parameters. It also properly maintains the integrity of the surface.
5. Clean Environments
The pharmaceutical and food processing industries need a high level of cleanliness. Orbital welding plays a vital role in achieving this. It creates smooth, crevice-free joints that prevent contamination and meet strict hygiene standards.
What Is Orbital Welding Used For?
The precision, cleanliness, and durability of orbital welding make it a trusted solution across several industries. Let’s explore its uses in some key fields.
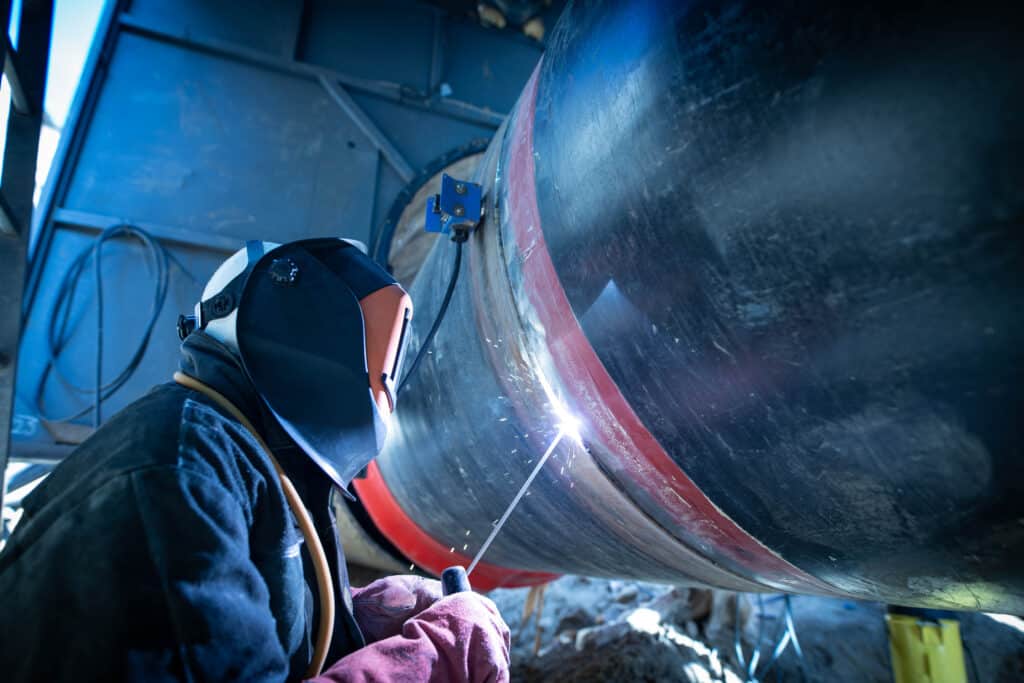
1. Pharmaceuticals and Biotechnology: Ensuring a contamination-free environment in pharmaceutical industries is essential. Orbital welding creates seamless, hygienic joints in pipes that transport sensitive fluids like important chemicals.
The perfect welds minimize gaps where bacteria can grow. It meets strict sanitary standards required for manufacturing medicines.
2. Aerospace: The aerospace industry requires lightweight but strong structures to face extreme conditions. Orbital TIG welding creates flawless welds on titanium and stainless steel that help make the suitable structure of the aerospace. The precision of the welds adds strength and safety to the structure.
3. Semiconductor Manufacturing: Semiconductor production needs a welding system that brings ultra-clean and leak-proof surfaces. Orbital welding is the go-to method for creating leak-proof joints. It ensures no imperfections during the sensitive manufacturing processes.
4. Food and Beverage: Hygiene is the key factor that needs to be considered in food and beverage production. Orbital welding builds crevice-free joints in stainless steel pipes and equipment. These are used in brewing, dairy production, and food processing.
The pure welds by TIG welder prevent bacterial growth. Moreover, its efficiency helps maintain high standards in manufacturing processes.
5. Power Generation: Power plants always rely on durable welds for piping systems that carry high-pressure steam, water, or gas. The orbital welding method fits perfectly here. It adds durability and reliability to pipelines.
This welding system is employed particularly in nuclear, thermal, and renewable energy sectors where safety is the top priority. The process ensures weld joining that can withstand high temperatures and pressure.
Pros and Cons of Orbital Welding
TIG orbital welding offers numerous benefits but it also comes with some challenges. Take a look at the pros and cons of orbital welding.
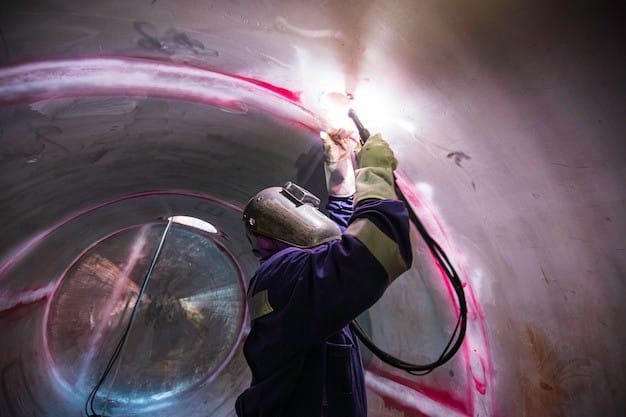
Pros of Orbital Welding
- Orbital welding is unique in offering top-quality and repeatable welds. It meets maximum quality standards by reducing human error. Precision and consistency are the outcomes of this exclusive welding process.
- It enhances safety as no manual intervention by the operator is needed. The operator just sets the parameters and monitors the process; he doesn’t need to operate the machine by hand in a potentially hazardous working area.
- Orbital welding offers clean and contamination-free welds. As it’s an automated process, it helps achieve smooth and hygienic surfaces. Therefore, this welding system is popularly employed in food processing and pharmaceutical industries.
- This welding method increases productivity. It applies automation, so repeating work can be done easily. As a result, it is used in large-scale projects without compromising on quality.
Cons of Orbital Welding
- TIG orbital welding is expensive because of its costly welding equipment wholesale. The initial investment can be higher for setting up the machine and additional tools. The system also requires regular maintenance.
- Running this welding process can be challenging without skilled technicians. A highly trained operator can program, monitor, and maintain the orbital welding properly.
- Manual welding works for different joint types, but orbital welding is primarily designed for pipe welds. This limitation makes orbital welding unsuitable for diverse welding necessities.
Final Thoughts
Orbital welding is a powerful industrial welding technology that offers the utmost precision and efficiency. Understanding and implementing it in different projects is an investment in long-term success. Besides this method, you need top-notch quality equipment.
YesWelder is committed to reliability and innovation. Wholesale buyers and distributors can confidently purchase their necessary welding machines from this supplier. YesWelder offers professional-grade welding equipment designed to meet your business’s demands.
FAQs
How is orbital welding different from manual welding?
Manual welding requires manually performing every step. Orbital welding is semi-automated or automated; it reduces errors and provides more consistent welding. All its features make it suitable for projects where maintaining strict quality standards is important.
What are the components of an orbital welding system?
An orbital welding system includes a power supply, welding head, controller, and cooling system. These components control current, gas flow, and rotation around the pipe, and prevent overheating during welding.
What materials can be welded using orbital welding?
Orbital welding is a versatile method that works with almost all commonly used materials including carbon steel, stainless steel, aluminum, titanium, etc. This method is effective in controlling heat, contamination, and defects. As a result, it offers the most precise welding for complicated joints.
Does shielding gas impact orbital welding?
Argon and helium as shielding gas protect the welded area from contamination. The gas flow rate controls the weld quality of the metals. So, it’s vital to fix the right flow rate, especially for reactive metals like titanium.