Heavy-duty welding plays a vital role in industries where strength and durability are non-negotiable. This process is the backbone of projects like constructing buildings, repairing machinery, and fabricating large-scale equipment. Welding in these scenarios demands machines that can handle intense workloads without faltering.
Choosing a machine that is both durable and efficient ensures smooth operation even under demanding conditions. The right equipment saves time, reduces risks, and helps deliver high-quality results. Selecting the best heavy duty welding machine isn’t just about finding a tool—it’s about investing in reliable performance and long-term cost savings.
Common Challenges in Heavy-Duty Welding
Heavy-duty welding comes with unique challenges that demand reliable and durable equipment. Below are the most common obstacles welders face, along with insights on how to address them.
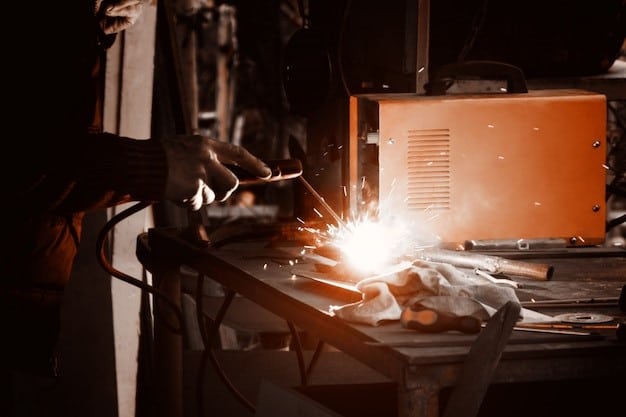
1. Managing High Heat and Long-Duty Cycles
Heavy-duty welding involves intense heat levels and extended operation times. Machines need to sustain high performance without overheating. Insufficient cooling systems or low-duty cycles can lead to frequent breaks, reducing productivity.
To overcome this:
- Look for machines with efficient thermal management systems.
- Opt for models with a high-duty cycle rating to handle prolonged usage.
2. Maintaining Precision for Intricate Projects
Achieving accuracy in heavy-duty welding isn’t always straightforward. Thick materials, detailed designs, and complex joints often require precise control over heat and technique. Even slight inconsistencies can compromise the quality of the weld.
For better precision:
- Choose welding machines with adjustable settings for power and speed.
- Consider equipment designed for specific tasks for fine, detailed work.
3. Resisting Wear and Tear in Harsh Environments
Welding in tough conditions, such as construction sites or industrial facilities, takes a toll on equipment. Exposure to dust, moisture, and physical stress can shorten the lifespan of a machine.
To ensure durability:
- Prioritize rugged builds with high-quality components.
- Select machines with protective coatings or enclosures to guard against environmental damage.
Addressing these challenges effectively will not only improve your welding results but also extend the life of your equipment.
What to Look for in a Heavy-Duty Welding Machine
Selecting the best heavy duty welding machine means understanding key features that directly impact performance. Here are the most important factors to consider.
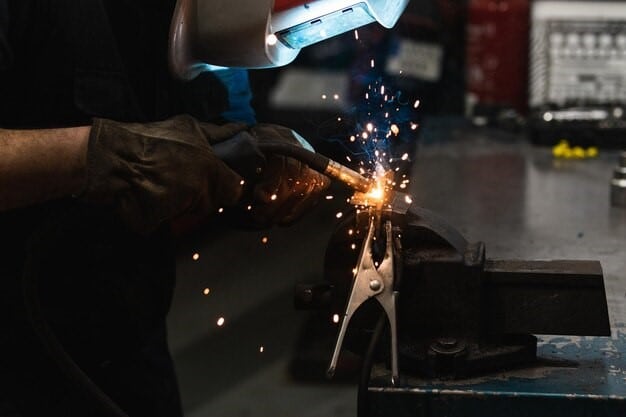
Power Output
A machine with high power output is necessary for handling tough jobs. Welding thick materials or working on industrial projects requires sufficient amperage to ensure deep, reliable welds. Machines with adjustable power settings offer flexibility for various tasks.
Duty Cycle
The duty cycle refers to the amount of time a welding machine can operate continuously without overheating. For heavy-duty applications, a high-duty cycle rating is vital. It allows extended operation during demanding tasks, minimizing downtime and boosting efficiency.
Material Compatibility
Different materials require specific welding techniques and settings. For example:
- A best heavy duty MIG welding machine is ideal for thicker materials like steel.
- A TIG machine from TIG welder suppliers works better for precise welding on thin metals or aluminum.
- Make sure the machine supports the materials you frequently work with.
Build Quality
Heavy-duty welding machines need to withstand harsh environments and long-term use. Durability depends on robust construction and high-quality components. Machines with sturdy frames and wear-resistant designs will perform reliably over time.
Advanced Features
Modern welding machines often include innovative features that improve usability and accuracy. Some helpful options include:
- Smart controls for real-time adjustments.
- Pre-programmed settings for common welding tasks.
- Digital displays for clear feedback and monitoring.
How to Choose the Best Heavy Duty Welding Machine
Selecting a welding machine isn’t just about picking the most popular model. Heavy-duty tasks demand equipment tailored to specific needs, from the materials you work with to the complexity of the welds. Choosing wisely ensures efficiency, reliability, and a smoother workflow. Here’s how to identify the right machine for your job.
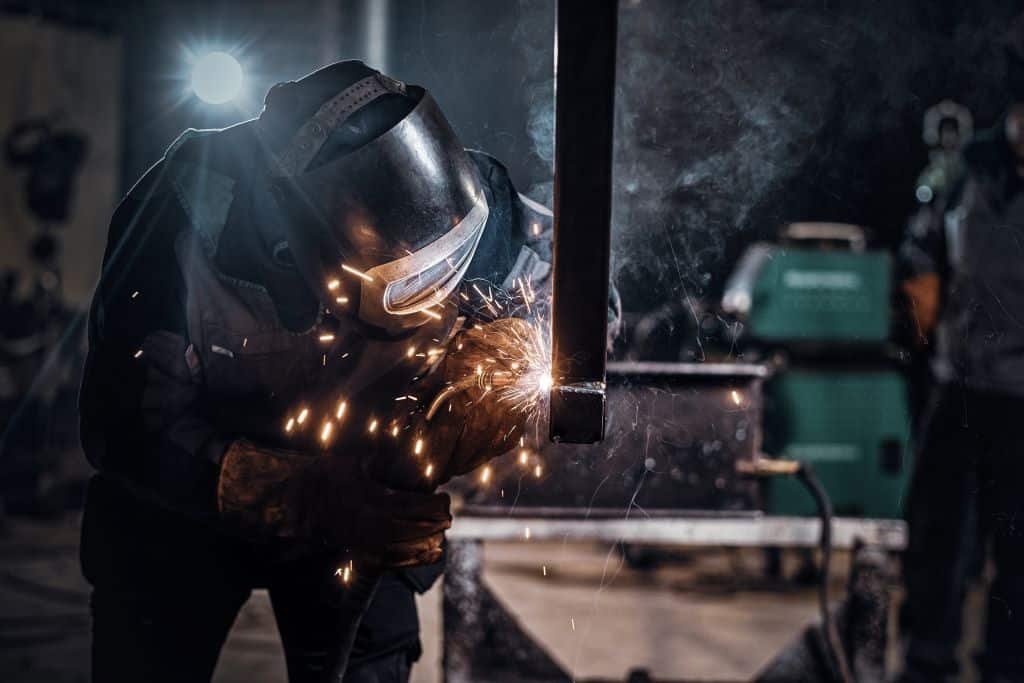
Assess Job Requirements
Your welding tasks should determine the type of machine you need. For industrial applications, a best heavy duty MIG welding machine from MIG welding suppliers handles thick metals like steel and provides high-speed performance. It’s ideal for projects requiring strong, consistent welds. On the other hand, a best heavy duty TIG welding machine offers precision and control, making it perfect for thin materials and intricate designs.
Consider these factors when evaluating your needs:
- Material thickness: Thicker metals often require higher power output.
- Project type: Fabrication projects might need MIG welding, while detailed craftsmanship benefits from TIG.
- Environment: Machines used outdoors or in rugged conditions should be durable and weather-resistant.
Set a Budget
Budget planning helps you avoid overspending while ensuring you invest in quality. Start by identifying your must-have features, then compare models within your price range.
Think about:
- Upfront costs vs. long-term savings: A durable machine may cost more initially but save you money on repairs or replacements.
- Essential features vs. add-ons: Focus on what you need for your tasks instead of paying for unnecessary extras.
A well-planned budget lets you prioritize value without compromising performance.
Cost vs. Performance
Balancing cost and performance is key to choosing the best heavy duty welding machine for your needs. A machine with excellent durability, a high-duty cycle, and advanced controls can make your work more efficient, even if it’s not the cheapest option.
Here’s how to weigh your options:
- Compare duty cycle ratings to minimize downtime during heavy workloads.
- Check material compatibility to ensure the machine can handle diverse projects.
- Look for warranties and after-sales support to protect your investment.
Focusing on your job requirements, budget, and performance needs can help you select a welding machine that delivers the best results and stands the test of time.
Innovations in Heavy-Duty Welding Technology
Advancements in welding technology continue to improve how professionals handle heavy-duty tasks. Modern welding machines offer features that enhance efficiency, precision, and sustainability, making it easier to achieve consistent, high-quality results.
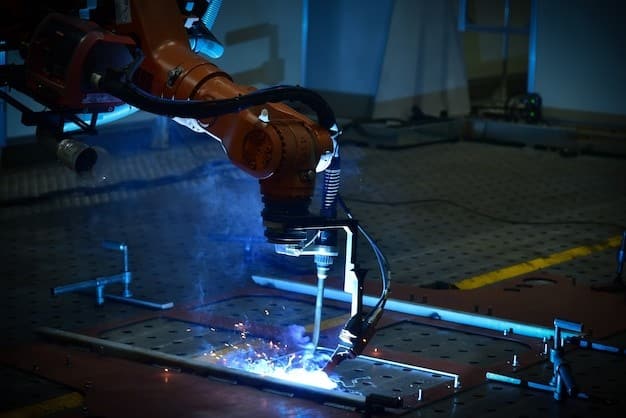
1. Smart Welding Systems
Smart welding systems use advanced software to assist operators by automating and fine-tuning settings. These systems analyze factors such as material type, thickness, and required weld strength to adjust power and speed automatically.
- Improve accuracy with real-time adjustments.
- Reduce the chance of errors, especially for complex projects.
- Machines equipped with these technologies can help you achieve reliable results with less effort.
2. Digital Controls
Digital displays and automated controls make operating heavy-duty welding machines more user-friendly. Features such as pre-programmed settings save time and reduce guesswork.
- Easily monitor settings like amperage, voltage, and duty cycle.
- Make adjustments quickly with intuitive interfaces.
- These controls are particularly helpful for tasks requiring consistency over long periods.
3. Energy-Efficient Designs
Energy-efficient welding machines are better for the environment and reduce operational costs. Innovations such as inverter-based technology use less power without sacrificing performance.
- Lower electricity consumption during extended use.
- Minimize heat loss for improved output.
- Investing in energy-efficient designs supports long-term savings while maintaining high performance.
4. Sustainability
Modern welding technology focuses on reducing environmental impact. Machines designed with sustainability in mind incorporate recyclable materials and eco-friendly features.
- Use components that are easier to recycle or reuse.
- Limit emissions to meet environmental standards.
- These advancements benefit industries aiming to adopt greener practices.
5. Enhanced Connectivity
Welding machines with connectivity features make it easier to monitor performance and troubleshoot issues. Wireless monitoring and cloud-based analytics allow operators to track machine health and usage patterns.
- Receive alerts for maintenance needs.
- Access performance data remotely for better decision-making.
- Connectivity ensures efficiency and keeps operations running smoothly.
These innovations shape the future of welding and make the best heavy duty welding machine more versatile and efficient than ever before.
YesWelder: Your Professional Welding Machine Partner
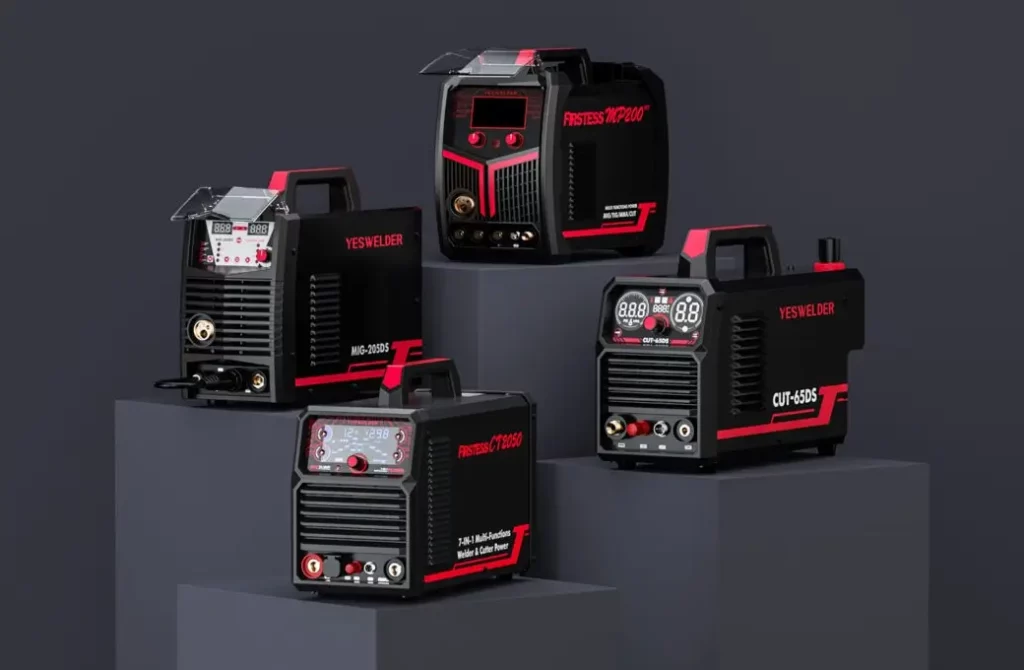
The right welding machine can make all the difference in heavy-duty tasks. For those seeking top-notch performance, it’s essential to consider factors like power output, material compatibility, and durability. Getting the best heavy duty welding machine means finding equipment that stands up to long hours, tough materials, and precise requirements.
YesWelder is a trusted partner in the welding industry, offering machines designed for both professional and industrial use. Their range includes the best heavy duty MIG welding machine and the best heavy duty TIG welding machine, tailored to meet the needs of various welding projects.
Why Choose YesWelder?
- Reliability: YesWelder’s machines are built to endure even the most demanding environments, ensuring longevity and stable performance.
- Cost-Effectiveness: Known for providing exceptional value, YesWelder delivers high-quality machines at competitive prices, perfect for businesses looking to maximize their investment.
- Tailored Solutions for Wholesale Buyers: YesWelder understands the needs of bulk buyers, offering customized solutions that fit the specific demands of your business.
Since 2006, YesWelder has been committed to providing durable, affordable, and innovative welding solutions. Their focus on customer feedback and industry insights has driven continuous improvements, making YesWelder a reliable partner for businesses and professionals alike.
FAQ
What is the best heavy duty welding machine for industrial use?
The best heavy duty welding machine for industrial use typically offers high power output, a high duty cycle, and compatibility with a wide range of materials. Look for machines with advanced features like digital controls, durability, and a solid reputation for reliability under long-term use.
How do I choose between a MIG and TIG welding machine for heavy-duty tasks?
For tasks that require high-speed welding and strong, durable welds, the best heavy duty MIG welding machine is ideal. For projects requiring precision and fine detail, such as thin materials or intricate designs, the best heavy duty TIG welding machine would be the better choice.
Are YesWelder machines suitable for both home and industrial use?
Yes, YesWelder machines are designed for both home and industrial use. They are highly versatile, offering excellent performance and durability for professionals and hobbyists alike.
Whether you need heavy-duty equipment for a workshop or compact machines for smaller jobs, YesWelder has options that fit both needs.