A welding machine is a significant investment and an important tool for hobbyists and professionals. It’s designed to do demanding welding jobs with precision. It helps bring perfection to your everyday subtle tasks. After a certain time, this tool shows signs of wear and tear, and the performance you start to get is not satisfactory.
With careful attention and timely maintenance, you can enhance your welding machine life expectancy. This article provides a guide to the essential practices for maintaining your welding machine, ensuring it remains in excellent condition for years.
What Affects Welding Machine Life Expectancy?
The lifespan of a welding machine depends on various factors. Understanding these factors helps maintain equipment and maximize overall performance. The following are the key elements that impact the machine’s life expectancy.
- Use Frequency
- Welding Process Types
- Welding Machine Quality
- Storage Environment
- Maintenance Practices
- Voltage Fluctuations
1. Use Frequency
The more frequently used machines tend to decrease their performance and lifespan quickly. Machines used in fabrication shops or high-production environments experience heavier loads. These machines face overheating, which causes premature failure.
2. Welding Process Types
High-impact processes such as TIG welding require longer operating times, which stresses the power supply. This increases heat and affects welding machine life expectancy. Low-impact processes like MIG welding operate at moderate power sources and impact life expectancy less.
3. Welding Machine Quality
The best-quality machine lasts longer than welders from cheaper brands. A reputed brand maintains the highest standards to meet consumer needs. So, products from a well-known brand are suitable for long-term use in any condition.
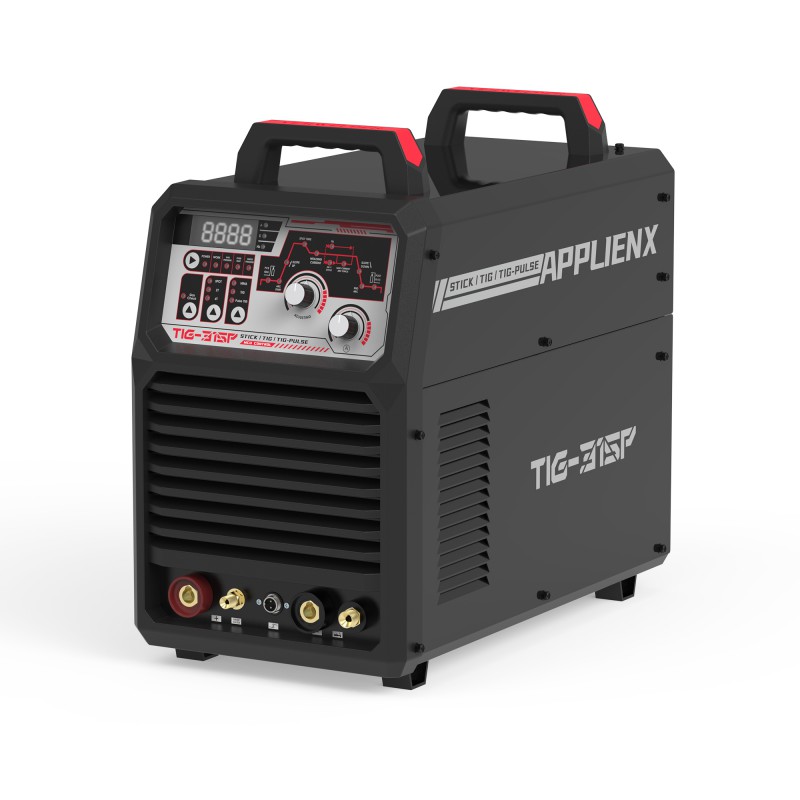
4. Storage Environment
Store your welding machine in a dry, clean, and temperature-controlled space. An environment that contains moisture and humidity can cause corrosion, rust, and electrical short circuits. Dirt can clog vents and impact the machine’s cooling systems.
5. Maintenance Practices
Operators need to follow the maintenance guidelines to enhance the equipment’s lifespan. Regular inspection and cleaning keep the machine in top condition, allowing it to run longer. Follow other procedures for a quick solution to any problem your machine experiences.
6. Voltage Fluctuations
Voltage dips or spikes can damage the machine’s electronic parts. Voltage fluctuations lead to inconsistent power supply to the welding machine. It causes reduced efficiency or circuit board failures.
How to Prolong Welding Machine Life Expectancy
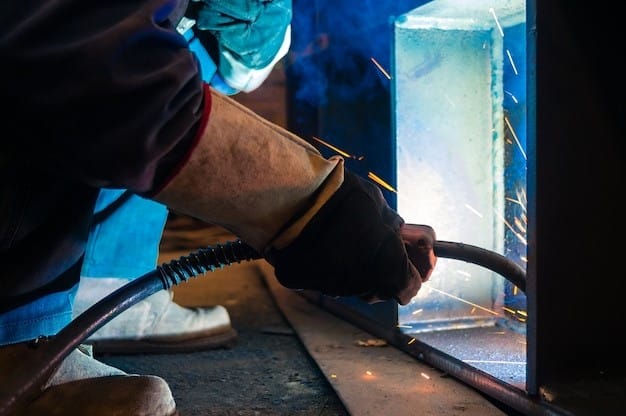
Increasing the lifespan of a welding machine involves some crucial factors. Maintaining them can extend the life of a machine. Below are actionable tips to keep your machine reliable for years.
- Ensure Regular Maintenance
- Store the Machine Correctly
- Choose the Right Machine for the Task
- Use Compatible Consumables
- Train Operators Properly
- Avoid Excessive Movement
1. Ensure Regular Maintenance
Remove dust and spatter after every use. Keeping the machine clean improves its performance. Inspect the physical appearance, cables, power source, and other components for damage. Replace any worn parts, such as liners and brushes, immediately.
2. Store the Machine Correctly
Store your welding machine in a clean, dry, and cool environment. Use a protective cover for the machine. Don’t store it in areas with high humidity and fluctuating temperatures.
3. Choose the Right Machine for the Task
Use the right machine for a particular welding job. Ensure the machine’s specifications match the task requirements. Overloading the tool beyond its power can cause component failure.
4. Use Compatible Consumables and Accessories
Choose top-quality consumables designed for a specific machine. Avoid using incompatible accessories because they can reduce efficiency and total lifespan of your machine.
5. Train Operators Properly
Operating the machine correctly extends its functional life beyond the welding machine depreciation life. Trained operators can use a machine in the right way for more outcomes, so ensure that operators are trained properly.
6. Avoid Excessive Movement
You may need to move your machine from one place to another. Transport the welding machine carefully to avoid any damage. Apply stable mounts for machines operating in industrial environments.
Signs that a Welding Machine Needs Replacement
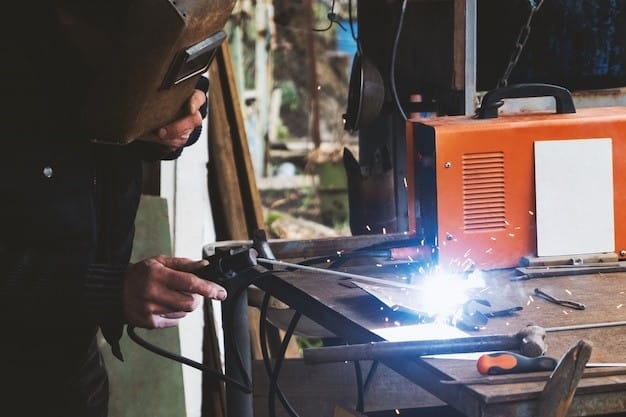
Like any equipment and heavy-used tool, a welding machine doesn’t last forever. It loses its strength and capability over time. The following are the clear signs that your welding machine might need replacement.
- Declining Performance
- Consistency Issues
- Increased Repair Frequency
- Outdated Technology
- Visible Damage
Declining Performance: If your machine fights to deliver the same power as before, it’s a warning sign. At this time, welding results will be poor and uneven. These issues ensure that the tool is no longer performing at its best.
Consistency Issues: A reliable welding machine should produce steady results. If the weld is not consistent and always appears different, you need to be careful that internal components are not in good condition.
Increased Repair Frequency: Frequent breakdowns and spending a lot on repairs can be provoking. If you need to repair your welding machine frequently, replace it because it can be cheaper than frequent repairs.
Outdated Technology: Old machines lack upgraded features to match current welding needs. Upgrading might be wise if your machine doesn’t support newer welding materials and techniques.
Visible Damage: Inspect for cracks, rust, or frayed cables. Physical damage warns you to take quick steps; it reduces performance reliability. It’s advisable to replace damaged parts before an accident occurs.
TIG vs. MIG vs. Stick Welding Machines: Which Lasts Longer?
The welding machine you’ll use may have several factors to consider for its longevity. We’ll be helping you understand which one among the TIG, MIG, and Stick welding machines has better longevity.
Here’s a comparison table for better understand:
Factors | TIG | MIG | Stick |
Weld Quality | Very clean | Medium | Low |
Skill Level | Advanced Level | Moderate level | Low level |
Weld Speed | Slowest | Fast | Slow |
Shielding Gas | Argon or helium | CO2, argon, or mixture | Electrode |
Weld Applications | Automotive, pipe, pressure appliances | Agro equipments, shipbuilding, structures | Construction, manufacturing, field repair |
Overall Lifespan | Long when properly maintained | Moderate, depending on usage | Longest, in rough conditions |
The core factor regarding longevity in either welding machine is how you use it. Among them, TIG welding machines have more durable components as they are required to do more complex tasks.
Proper weld setup requires precise control over the TIG welding machine that evenly distributes the stress. As a result, less heat is generated, and there is no chance of overheating.
On the other hand, MIG welding from reliable MIG welding suppliers produces moderate levels of welds in much less time than TIG. The faster process eventually leads to the wearing of consumable wire, which needs regular maintenance. Otherwise, the machine’s lifespan shrinks.
The Stick welding machine is excellent for thin-material applications and requires much less setup time outdoors. Due to its heavy exposure outdoors for strenuous work, it lasts less than the other two.
Lastly, if you have to choose one machine for lost lastingness, go for a TIG welding machine. Its robust components handle the high-yielding output, making it a very good choice.
Mistakes That Shorten Welding Machine Lifespan
Your welding machine can wear off way earlier than expected if you don’t avoid particular mistakes. Here are the top 3 that you should know and avoid:
Overheating: Welder overheating means there are the highest chances of wearing or burning off the components. It happens when clogging is present and does not let the cooling process function. Cleaning out these clogged blockages often is a viable solution.
Breaking Duty Cycle Limitations: The duty cycle is the percentage unit a welding machine can perform before you put it to cool down. If you exceed and don’t maintain the cycles, it will reduce the machine’s performance. The most common scenario is the failure of circuit boards and rectifiers.
Improper Maintenance: If you don’t inspect the worn parts regularly or monitor the coolant levels, your welding machine will last less than usual. Regularly cleaning the fans and vents, help a lot in easy maintenance.
Get Quality Welding Machines from a Reliable Supplier
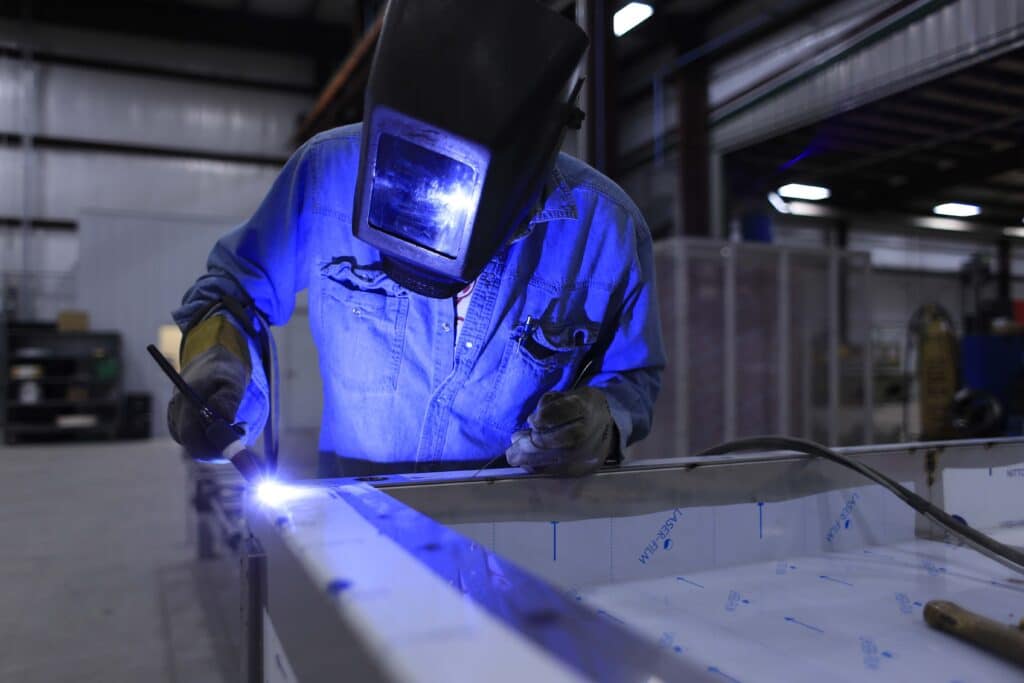
Buying a welding machine from a reliable supplier influences many things, including the machine’s quality, safe usage, and confidence while working. Here’s why this is important.
Durability and Performance: Top-quality welding machines are built to last. A reliable supplier ensures their products meet high standards. This means fewer repairs and consistent performance in any harsh conditions. So, buying from a trusted source protects your investment and enhances your confidence to work.
Wide Range of Options: Popular brands offer various welders to meet different needs. They have everything you need, including a MIG, TIG, or Stick welder. They also help you choose the best welding machine based on your requirements and budget.
Safety Assurance: Welding is a challenging task with various safety issues. A trusted supplier offers welding machines that meet safety standards and certifications to decrease the chance of accidents.
Technical Support and Guidance: Reliable suppliers help with setup, troubleshooting, and required maintenance. If you face issues, they offer prompt support to get you back to the workshop. Many companies provide necessary training on how to use their machines safely.
Spare Parts and Warranties: The reputed brands offer warranties and a steady supply of spare parts. To fix your machine if needed, you can easily find parts. It makes repairs easier and ensures the machine remains in good condition.
YesWelder: Your Professional Welding Machine Partner
In general, the life expectancy of a welding machine depends on build quality but maintenance affects it greatly. A high-quality machine that goes under maintenance after every use can last longer.
YesWelder, a trusted supplier offers high-quality welding machines for wholesale buyers and distributors. The company provides reliable and cost-effective welding equipment for every consumer looking for quality and durability.
FAQs
What is the average life expectancy of a welder?
A welder or welding machine doesn’t have a fixed lifespan. It can vary from 5 to 15 years, and high-quality machines can last longer. However, the life expectancy depends mostly on proper maintenance, usage frequency, and the machine’s structure.
Does the brand of a welding machine affect its life expectancy?
A well-known brand manufactures high-end welding machines with top-quality components. These machines can last longer than machines from cheaper and lesser-known brands.
Does maintenance impact a welder’s life expectancy?
Proper maintenance can significantly improve a welder’s performance and life expectancy. It can also prevent breakdowns and ensure optimal machine performance. The key steps in maintenance are regular inspection, cleaning, and replacement of work components.
Does the type of welding impact the machine’s lifespan?
The most commonly used welding types are MIG, TIG, and Stick. TIG welding requires finer equipment to ensure precise welding. It may wear differently than MIG or Stick welding machines. However, regular maintenance can reduce these effects.