Welding has been a reliable method in metal joinery since ancient times. During the Bronze Age, workers pressure-welded two joints together using a gold circular box. However, the days of using gold for welding are gone, and the method of welding metals by hammering, which started during the Middle Ages, has long faded from the mainstream.
Today, industrial welding has taken many new forms and its application has diversified a lot. Although, at its core, it’s still the process of joining two or more materials, often metals or thermoplastics, using heat and pressure.
Continue reading as this guide explores more of the basics of industrial welding today.
Basic Welding Principles
The main goal of welding is to join materials together in a way that’s just as strong, if not stronger, than the original material. During welding, the materials are melted at their melting points, then cooled and solidified to create a strong bond.
Beyond the general sense of welding, there are specific methods or principles that are distinct from one another. Two of the most commonly observed principles include pressure and fusion welding.
Pressure Welding

As the name suggests, pressure welding joins metals by pushing the materials together to form strong bonds. It can be used alone or with a vacuum or heat for stronger joinery. The pressure forces the materials into close contact, facilitating the joining process.
In welding methods like forge welding or friction welding, the materials get heated up and then are pressed together to create a solid bond. The heat softens the materials, and the pressure locks them in place, forming a strong connection once everything cools down.
Meanwhile, pressure and vacuum form cold-pressure welding, a technique used in industries where the prevention of heat distortion is critical.
Fusion Welding
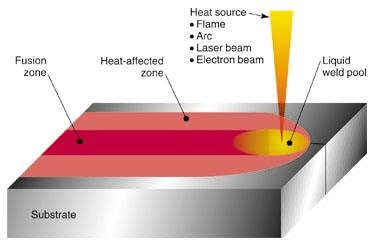
This is the principle behind most welding processes. Fusion is the process of melting the base materials and often a filler material, allowing them to fuse together upon cooling. The heat source (whether from an electric arc, gas flame, or laser) melts the edges of the materials being joined. When the molten metal cools and solidifies, the materials become fused, creating a permanent bond.
Welding Heat Sources
The heat source is one of the main aspects of welding; in fact, most welding methods wouldn’t be possible without heat. The heat source also determines how the metals are melted, distinguishing what method is best for a specific application.
Here are the different ways heat is generated in welding:
1. Electric arcs (MIG, TIG, SMAW)
An electric arc is basically a big spark of electricity that happens when a current flows through the air between two points, like two metal pieces. This spark gets extremely hot, making it suitable for melting and joining metals.
In welding, the arc is created between a special electrode (a metal rod or wire) and the metal you’re working on. The heat from the arc is so intense that it melts the metal, allowing the pieces to fuse together. Sometimes, special gases or materials are used around the arc to keep it clean and prevent contamination.
Electric arc has three sub-categories as described below:
- MIG (Metal Inert Gas) Welding: MIG welding suppliers recommend that MIG welding uses a continuous spool of wire that feeds into the weld. It creates an electric arc between the MIG welding wire and the metal you’re working on. The heat from the arc melts the wire and the metal, fusing them together.
- TIG (Tungsten Inert Gas) Welding: TIG welding is a bit different. Instead of using a wire that melts, TIG uses a special tungsten rod that doesn’t melt. The welder has to feed in extra metal (called filler) by hand to fill the gap in the weld.
- SMAW (Shielded Metal Arc Welding): SMAW, or stick welding, is one of the oldest and most common welding methods, especially for heavy-duty industrial jobs. You use a “stick,” or what’s often called a welding rod, that not only melts to fill the joint but also helps create the heat needed to weld.
2. Gas flames (oxy-acetylene welding)
Oxy-acetylene welding, also known as gas welding, uses a torch to mix oxygen and acetylene gases, creating an extremely hot flame. This flame can melt metals, making it useful for tasks like cutting, brazing, and welding thin materials. It may not be used as much in large-scale industrial jobs anymore, but it’s still a great option for smaller projects or repairs since it’s portable and easy to use.
3. Laser and electron beam welding
These are high-tech welding methods that use focused beams of light or electrons to melt and join metals. Both methods create extremely precise and controlled heat, which makes them perfect for industries that need top-notch accuracy, like aerospace or electronics. Think of them as super-precise lasers that weld materials together with almost perfect precision.
Industrial Welding Materials
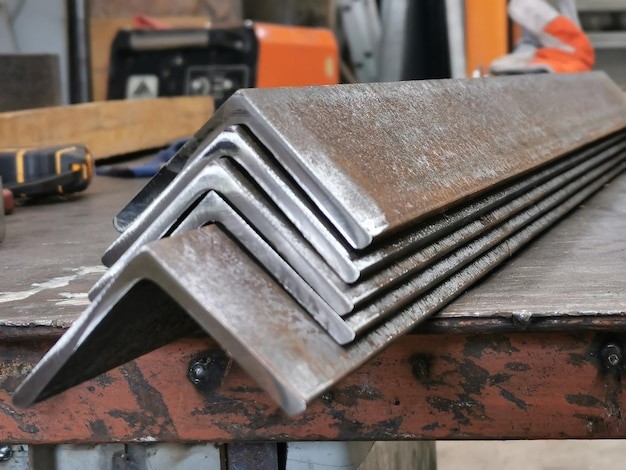
Like with the different welding methods, the choice of materials for welding is also integral in the process. Each metal offers unique qualities and results in welding, making one type best suited for a specific application while rendering it unsuitable in other works.
The same principle applies to different welding materials like fillers and gases. Here are the materials used in industrial welding:
Common Welded Materials
1. Steel: It is the most widely used metal in most applications and industry thanks to its strength and versatility.
2. Aluminum: In industries where strength and lightweightness are the standard, aluminum offers the best option. However, aluminum is a bit delicate when it comes to welding methods due to its low melting point and high thermal conductivity. A TIG welding machine remains the best for aluminum welding.
3. Copper: Similar to aluminum, copper also has high thermal conductivity and high risk of oxidation and at high temperatures. You’ll usually see copper used in plumbing and electrical uses.
4. Titanium: Titanium’s high strength-to-weight ratio makes it a go-to material for specialized industries like medical equipment manufacturing and aerospace, to name a few.
Filler Metals
Filler metals are used to fill the gap between two workpieces. The right choice of filler metal should relate to the base material being welded and the target, specific weld qualities. Here are the usual filler materials used:
- Electrode rods for stick welding.
- Filler wires for MIG and TIG welding.
- Brazing rods for gas welding.
Shielding Gases
The material’s weld pool can be contaminated, which is bad news for the weld result; hence, it needs protection. When the weld pool gets contaminated, it can result in bubble-filled welds or even blow holes, which altogether weakens the welded joint.
Shielding gases are essential to protect the weld pool from contaminants that can compromise the quality of the weld. Here’s a rundown of the common shielding gases:
- Argon: Used primarily in TIG and MIG welding, argon provides a clean, stable weld pool.
- Carbon Dioxide: Often used with MIG welding, carbon dioxide is cost-effective but can create spatter.
- Helium: Used in combination with argon for TIG welding, helium increases heat input and is ideal for thicker materials.
Industrial Welding Applications
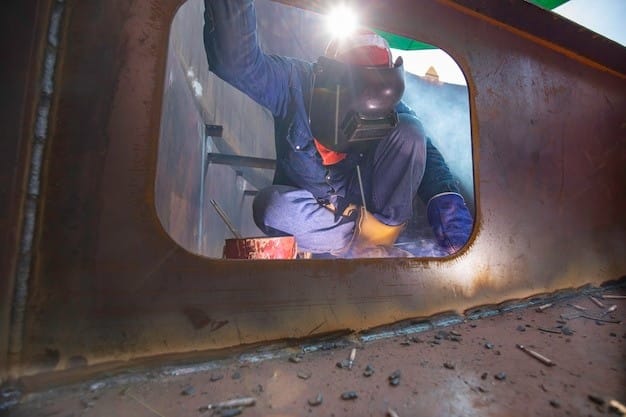
Here are a few key areas where welding is really important:
Aerospace
Welding is also integral in the aerospace industry, especially for building lightweight yet strong parts for airplanes and rockets.
Since the parts need to be really precise and strong, techniques like TIG welding and laser welding are used to create parts like turbine blades and fuel tanks. Aluminum remains the best material for this industry as it guarantees lightweightness without compromising strength.
Automotive Industry
In car manufacturing, welding is the best way for putting together parts like car bodies, frames, and exhaust systems. Different welding techniques, like arc welding and MIG welding, are used to join steel and aluminum parts, making sure cars are strong and safe.
Construction
In construction, welding is used to join big metal pieces, like steel beams and pipes, that make up buildings and other structures. Methods like stick welding (SMAW) and gas welding are fittingly used for these heavy-duty jobs.
Shipbuilding
When it comes to building ships, welding is essential for putting together the hulls and other large parts of the ship. MIG welding and arc welding are typically used to ensure the structure is strong enough to handle tough ocean conditions.
Sometimes, it also requires a more sophisticated welding process, hence employing advanced techniques like orbital TIG welding.
Industrial Welding Safety
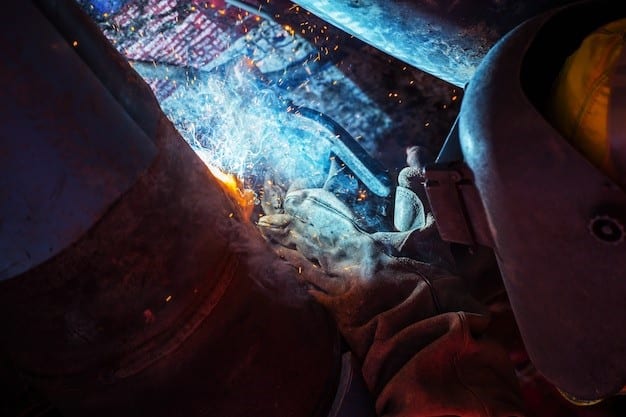
While welding techniques have advanced in great significance and in different aspects like efficiency, effectiveness, and even safety, the risk of workplace injuries still can’t be overlooked. Hazards like burns, electric shock, exposure to fumes, and eye injuries remain a considerable risk.
Hence, precautions must always be a top consideration to promote overall operation and workplace safety. Here are the most important welding precautions to always observe:
Personal Protective Equipment (PPE): Welders should wear flame-resistant clothing, gloves, protective eyewear, and face shields.
Worksite Safety: Ensuring proper ventilation, using fire-resistant blankets, and keeping a fire extinguisher nearby are in case of fire.
Training: Workers should receive proper training in welding techniques, safety protocols, and emergency procedures before getting their hands on welding machines.
Final Thought
Welding is an essential skill in the modern industrial world, and mastering the basics can lead to significant improvements in both quality and efficiency. From arc welding to gas welding, understanding the various techniques, materials, and applications is crucial for selecting the best welding method for a specific task.
By following the proper safety protocols and choosing the right equipment, businesses can maintain safe and productive environments while delivering high-quality welded products.
YesWelder: Your Professional Welding Machine Partner
When it comes to sourcing reliable and durable welding machines, YesWelder is your go-to supplier. Known for their high-quality, cost-effective machines, YesWelder offers bulk purchasing options, making it ideal for businesses seeking to equip their operations with top-tier welding equipment.
Whether you need MIG, TIG, or stick welders, YesWelder provides the tools you need to get the job done. Their commitment to reliability and customer satisfaction makes them the perfect partner for companies in need of durable, high-performance welding machines.
Contact YesWelder today to explore their product offerings and take your welding operations to the next level.