Whether in the aerospace, construction, or shipbuilding industries, high power welding machines can tackle the toughest welding tasks with ease. Their features offer extensive power, accuracy, and efficiency, enabling them to meet the challenges of large-scale operations.
This article highlights high-power welding machines and all other factors to understand why they’re reliable for industrial projects.
What Are High-Power Welding Machines?
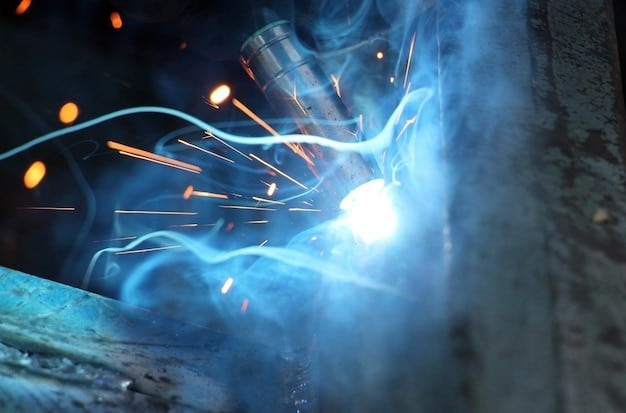
Generally, high-power welding machines are welders used in heavy-duty welding applications and deliver higher power than conventional welders. These machines are fabricated in a way so that they can perform the required welding work with higher heat output and efficiency. That’s why they require greater voltage and amperage than standard welders.
High-power welding machines are used in industrial manufacturing, large-scale industrial and construction welding, and pipeline welding. Another feature of these machines is high power ratings. A welding machine’s power rating means the measured amperes, and it represents a machine’s ability to deliver its maximum current.
Standard welders can deliver from 120 to 250 amperes, whereas high-power welders can deliver from 300 to over 1000 amperes to provide faster welding speed. These high-power units can also handle thicker materials in a shorter time.
If we compare high-power machines to standard ones, the main difference is their ability to maintain a stable arc. High-power welders can deliver greater heat for a longer time while maintaining a stable arc, which is necessary for welding thick materials.
These machines can also provide advanced cooling systems, which might prevent overheating during continuous welding, whereas standard machines don’t have this feature. However, high-power welding machines require high control during complex applications.
Types of High-Power Welding Machines
Welding machines can be of different types, and high-power machines are categorized according to welding techniques and applications. There are four main types of high power welding machine, each providing excellent features for specific applications.
High-Power MIG Welders
The Metal Inert Gas (MIG) welding process utilizes a continuous MIG welding wire. MIG welding suppliers said that MIG, as a high-power welder, provides higher amperage and produces stronger welds for thicker metal welding.
This welding method is an automatic or semi-automatic welding process which is suitable for high-speed welding. MIG welders are used in large-scale production, especially when working with aluminum and steel.
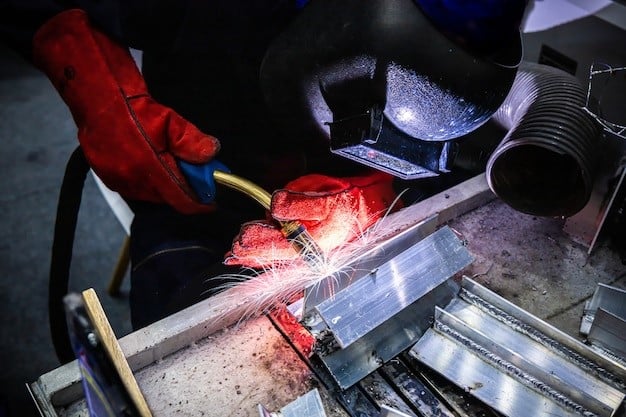
High-Power TIG Welders
Tungsten Inert Gas (TIG) welding is a well-known high-power welding process that utilizes a non-consumable tungsten electrode. A TIG welder provides high-quality welds and can weld thin materials. Moreover, these welders can be used to weld thick materials with high accuracy.
These machines are used in automotive and aerospace applications. They provide clean and controlled welds, which is why they are often used in stainless steel structures.
High-Power Stick Welders
Another high-power welder is a stick welder, which is generally used for thicker materials. Stick welding is considered to be one of the most versatile welding techniques because it can handle complex conditions. Stick welders are used in outdoor works and welding in windy environments.
These robust welders are also durable and are used in pipeline constructions and heavy-duty industrial welds. However, like other high-power welders, stick welders also provide higher amperage.
High-Power Multi-Process Welders
These welders are generally used to provide multiple processes, as the name implies. They can handle MIG, TIG, and Stick welding processes. These welders offer flexibility, allowing welders to switch between multiple modes required for a project.
For this flexibility, these welders are used in complex projects in industries where multiple modes are required. Welders can use a single machine that can simultaneously provide efficiency and versatility.
High-Power Welding Machine Key Features
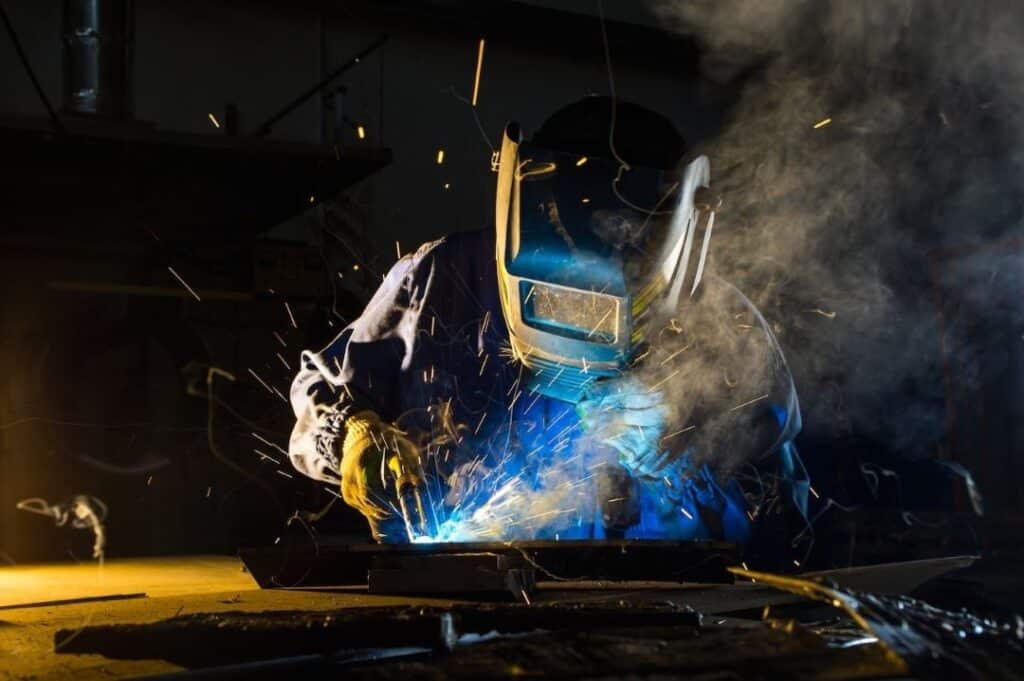
Together, the following features make high-power welding machines absolutely necessary for industrial use.
- Power Supply and Duty Cycle
- Advanced Cooling Systems
- Arc Stability and Precision
- Portability and Durability
1. Power Supply and Duty Cycle
High-power welders tackle heavy workloads that require a consistent power supply. The efficient power output from the units ensures smooth welding in industrial applications.
The duty cycle is measured in percentage, which indicates the successful operation time at its mentioned power without overheating the machine. The 50-80% duty cycle is crucial for long-term intensive welding works.
2. Advanced Cooling Systems
The cooling system prevents overheating during the welding process. A powerful welder generally produces significant heat, which can impact the machine’s lifespan. The proper airflow mechanism or water cooling system helps ensure enhanced longevity.
3. Arc Stability and Precision
Arc stability offers consistent weld quality while avoiding spatter and defects. Modern machines incorporate advanced arc control technology and pulse welding to enhance precision.
4. Portability and Durability
High-power machines seem big, but modern technologies have designed portable units with the same power output. Integrated handles, compact designs, wheels, and sturdy-small components make these machines portable while offering desired durability.
Applications of High-Power Welding Machines
We hear the roar of welding machines when any construction work goes on nearby. High-power welding machines are used in almost all important industrial and manufacturing sectors. Let’s see the usage:
1. Heavy-Duty Manufacturing: Joining thick steel plates and other components is a mandatory part of shipbuilding, construction, aerospace, etc. sectors. High-power welding machines make this easier. Their ability to join large components precisely and efficiently is the most unique feature to portray.
2. Heavy Metal Fabrication: High-power welders are used to fabricate steel beams, girders, and large-scale frameworks. These machines are also extensively utilized to manufacture custom parts for heavy industries.
3. Automotive and Rail Industries: Producing vehicles, railcars, and locomotives is nearly impossible without high-power welding machines. These machines are also used to design components like chassis, body panels, and structural reinforcements.
4. Oil & Gas Mining: Transportation is a key factor in oil and gas mining, and pipelines are needed for this industry. High-power welding machines are used for seamless welding of these pipelines. Welders are also a must for the construction of storage tanks, pressure vessels, and refineries.
Benefits of High-Power Welding Machines
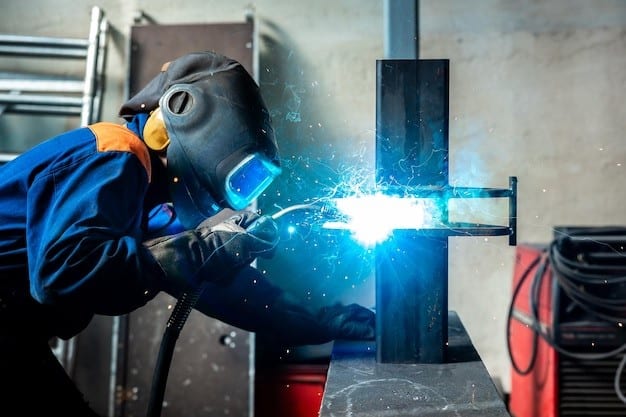
A high power welding machine offers various benefits that allow a professional to finish a complex weld without hassle. The benefits it provides:
- Increased Efficiency
- Enhanced Weld Quality
- Versatility
- Long-Term Durability
1. Increased Efficiency
High-power welding machines are heavy-duty, providing rapid performance and reduced time to complete a project. These machines boost productivity, streamline workflows, and minimize downtime with improved duty cycles and increased efficiency.
2. Enhanced Weld Quality
Precision is a desired feature of a high-power welder. Precise control over heat and arc stability results in clear welds with almost no defects. This type of weld quality is vital in industries where flawless welds are necessary.
3. Versatility
Highly powerful welding machines can perform on various materials such as aluminum, stainless steel, and titanium. These machines utilize different welding processes (MIG, TIG, and stick) simultaneously or separately. They can easily meet the project needs of different industries.
4. Long-Term Durability
Powerful welding machines are built with rugged materials and advanced components. They’re designed to last longer while working in demanding environments. Moreover, they don’t need frequent repairs and replacements.
Final Thoughts
A high-power welder ensures a flawless balance of power, quality welding, and reliability to work efficiently in industrial projects. This machine can weld on diverse materials, deliver maximum precision, and withstand large-scale operational demands. No matter how complex the welds, high-power welding machines are the best solution.
YesWelder Welding Machine Wholesale
YesWelder is a prominent supplier of professional welding machines, serving distributors and wholesale buyers worldwide. Its high-quality welding machines and equipment are designed for professional use and industrial projects.
Choose YesWelder to complete your projects successfully with modern, cost-effective, and durable welding solutions.
FAQs on High Power Welding Machine
1. What sectors benefit the most from high-power welding machines?
Industrial sectors such as automotive, construction, shipbuilding, aerospace, and heavy tools manufacturing benefit the most. These sectors require consistency, precision, and extensive welding ability.
2. What are the advantages of using high-power welders?
High-power welders are ideal for complex and large-scale projects. These machines ensure fast welding speeds, top-quality welds for thick materials, utmost durability, and reduced downtime.
3. What are the welding processes in high-power machines?
Depending on the project’s needs, high-power machines support various processes, including MIG, TIG, and Stick welding.
4. Are high-power welding machines energy-efficient?
Modern high-power welders utilize features like inverter technology, cooling systems, and reduced power consumption during operation. These features help to enhance the machines’ energy efficiency.
5. How to operate high-power welding machines safely?
Operators should follow manufacturer guidelines. They must wear protective gear and ensure adequate ventilation in the workshop. Regular maintenance of the equipment is also essential to prevent hazards.