Aluminum welding carries with it some unique challenges and opportunities for the hobbyist, professional, and wholesale buyer alike. Mastery in welding aluminum is important because strong and durable joints depend on it in various applications.
This comprehensive guide will cover the basic techniques, necessary tools, common pitfalls to avoid, and expert tips to ensure successful welds of aluminum-either to refine your skills or source high-quality welding solutions.
What is Aluminum Welding?
Aluminum welding is a process of joining two or more aluminum components by the use of heat, pressure, or both. Unlike other metals, for example, steel, aluminum requires special techniques and equipment because of its peculiar properties. The main goal is to obtain a strong and durable bond without losing the integrity of the material.
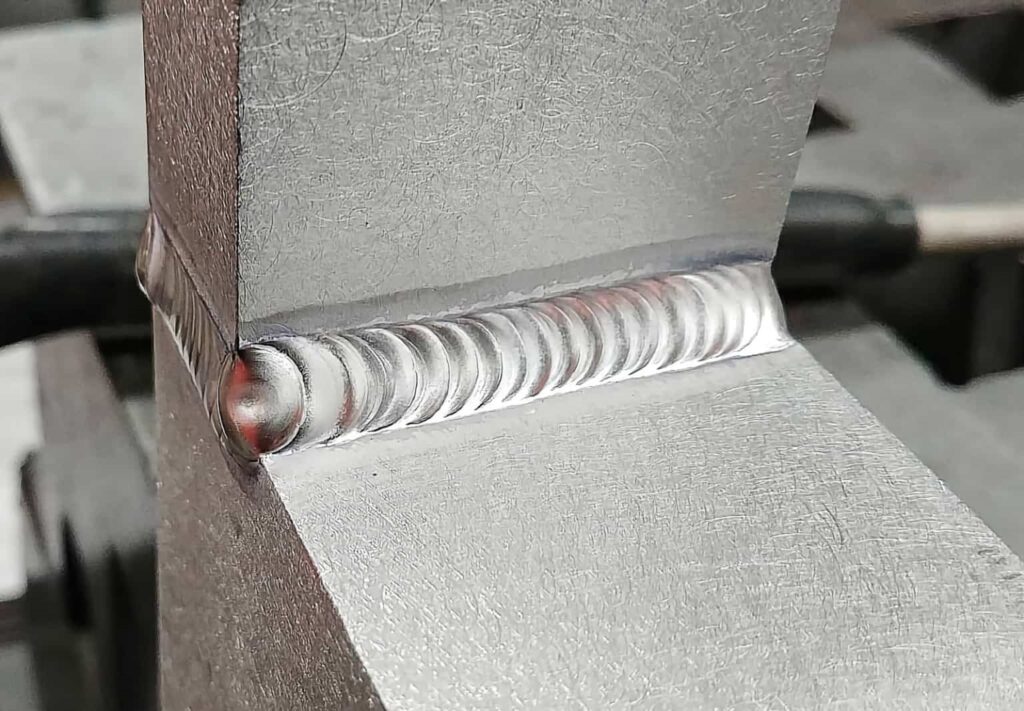
(Source: https://weldguru.com/aluminum-welding/)
Aluminum Properties that Affect Welding
Lightweight and Strength-to-Weight Ratio: Aluminum is a lightweight metal with an excellent strength-to-weight ratio, making it a material of choice for applications requiring weight reduction, such as in automotive and aerospace industries.
High Thermal Conductivity: Aluminum is a good conductor of heat; this may result in rapid dissipation of heat during welding. This property requires accurate control in the application of heat to avoid unwanted deformation.
Low Melting Point: Aluminum has a melting point of about 1,221°F (660.3°C), which is relatively low when compared with plenty of other metals. This necessitates good temperature control in order to prevent burn-through and ensure quality of the weld.
Common Challenges in Welding Aluminum
Oxide Layer: A thin, hard oxide layer forms on aluminum when it comes into contact with air rather fast. It has a considerably higher melting point than aluminum; thus, it resists welding processes.
Porosity and Contaminants: Impurities like moisture and hydrocarbons will generate porosity and weak welds. The area around the work should be free from dust and dirt.
Material Thicknesses: Aluminum is often welded in various thicknesses that will demand other techniques and equipment settings to achieve similar welding results.
How to Weld Aluminum?
Pre-Weld Preparation
The success of welding aluminum lies in the proper pre-weld preparation. The aluminum surface has to be cleaned of oil, grease, and water vapor using a solvent like acetone or mild alkaline solution. Let the aluminum dry out completely.
Next, remove the naturally occurring oxide layer, which could interfere with the welding process. Scrub the surface with a stainless-steel wire brush used exclusively for aluminum.
As an alternative, caustic, and water-based cleaners efficiently take away the oxide layer. Store cleaned aluminum in a dry cool place; this helps in avoiding oxidation. If not welding the aluminum piece right away, then cover the work to keep the contaminants away.
Choosing the Right Equipment
To have proper quality in the aluminum welds, the selection of correct equipment holds much significance. Select a compatible welding machine that can handle a selected welding type: TIG, MIG, or Stick, along with settings that will enable compatibility with all the peculiarities of aluminum.
Personal safety includes welding helmets, well-insulated gloves, protective outfits, and systems for proper ventilation that protect one from hazardous fumes and sparks. Also, employ cleaning tools such as stainless-steel wire brushes, grinders, and appropriate solvents for a clean welding surface.
Safety Precautions
There are several safety factors when welding aluminum metals because of the high temperature and danger involved. Always use personal protective equipment with safety glasses, welding helmets, welding gloves that are heat-resistant, and protective clothes to prevent burns and eye damage.
Ensure the work area is well-ventilated to dissipate toxic fumes and gases, which may cause respiratory problems. Fire hazard is another critical issue; thus, fire extinguishers should be available at all times, and all flammable materials should be kept away from the welding area to avoid any accidents.
Setting Up Welding Environment
A good welding environment improves safety and quality of welds. Keep the work area clean and tidy, with good lighting to see and minimize accidents. Good ventilation is necessary, and for that, exhaust fans or fume extractors are used to keep the welding fumes away and air quality good.
Allow the workplace temperature to be constant to prevent the formation of moisture on the parts in aluminum, which causes weld defects. A well-organized and well-ventilated workplace is just the very foundation for any successful and effective work with aluminum welding.
TIG Welding Aluminum
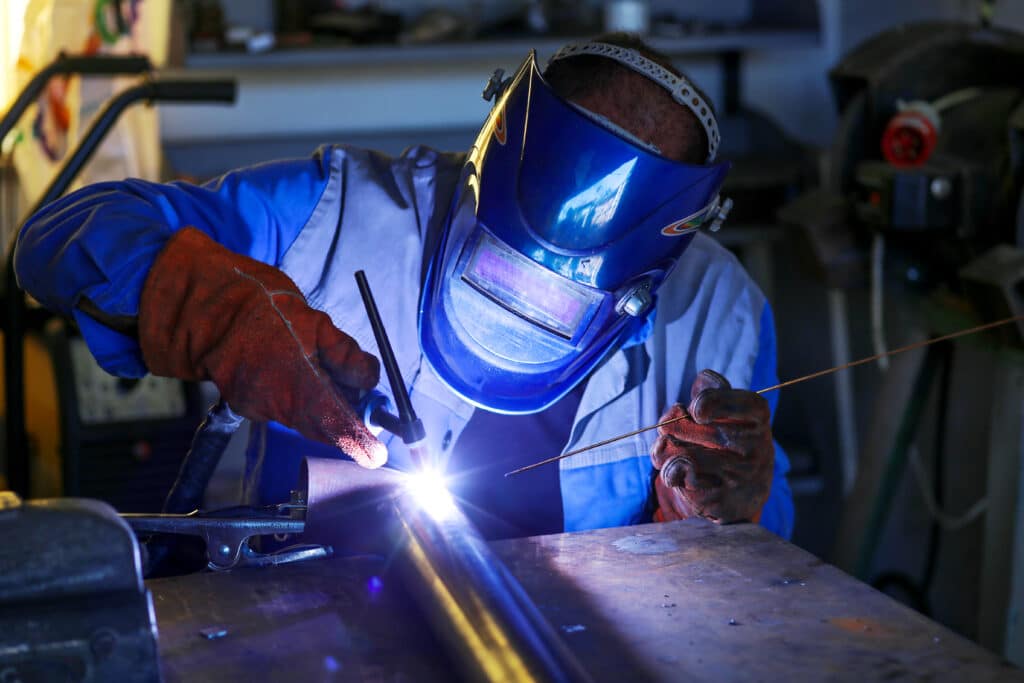
TIG aluminum welding has a lot of advantages, such as great precision and control that enable it to make clean, high-quality welds. This process generates little spatter, which greatly reduces the time spent cleaning up and preserves the integrity of the weld.
Also, TIG is quite versatile, as it can be effectively used on a wide variety of aluminum alloys, making it suitable for a great number of applications across different industries.
Equipment for TIG Welding Aluminum
- TIG Welder: TIG welders should be at least capable of AC and from trusted TIG welder suppliers, which is a requirement for welding aluminum.
- Tungsten Electrodes: The preferred tungsten welding electrodes are pure tungsten or ceriated tungsten.
- Filler Materials: Select the proper aluminum filler rod; two of the most common are 4043 and 5356, depending on the alloy.
- Shielding Gas: Argon is generally used, but argon-helium mixtures can be preferable with thicker materials.
TIG Welding Process
1. Setup
- Connect the TIG welder to an AC power source.
- Insert the tungsten electrode into the torch and set the appropriate gas flow rate.
2. Aluminum Preparation
- Clean the surface of the aluminum thoroughly, removing any oxide layer.
- Assemble the joint, with tight fit-up to avoid gaps in the joint.
3. Welding Technique
- Strike the arc by lightly touching the tungsten electrode against the workpiece.
- Maintain consistent arc length and move the torch along the joint in smooth, steady motions.
- Feed the filler rod into the weld pool as needed to achieve proper fusion.
Common Mistakes and How to Avoid Them
- Overheating the Material: Too much heat applied causes burn-through or warping.
- Not Cleaning: Not removing the oxide layer leads to a poor weld with porosity.
Stick Welding Aluminum
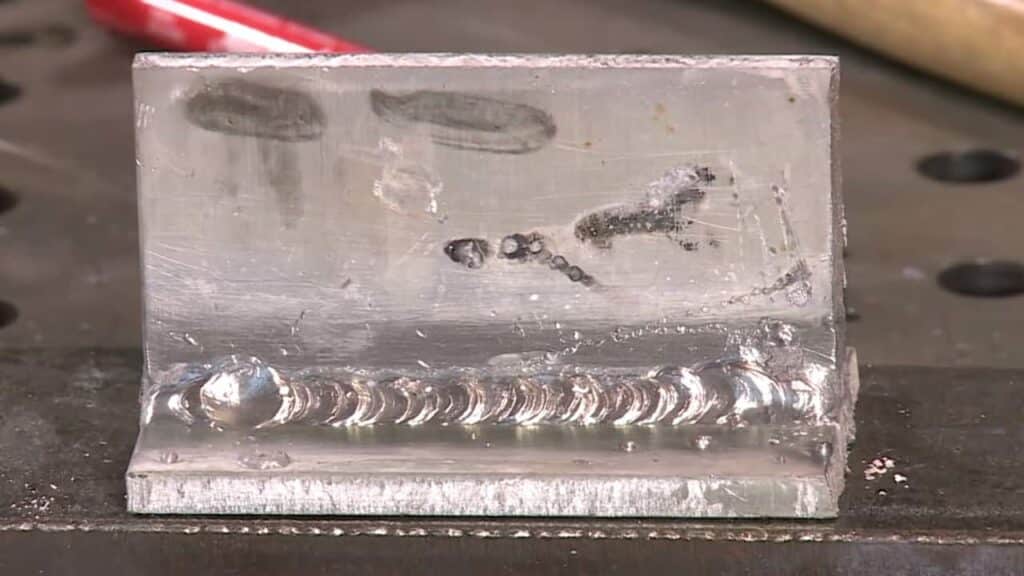
(Source: https://weldguru.com/aluminum-welding/)
Can You Stick Weld Aluminum?
Yes, it is possible to stick weld aluminum, though less frequently and more difficult compared to other methods like TIG or MIG welding. The stick welding of aluminum can get very messy and not as neat and strong as other methods.
Stick Welding Aluminum: Pros and Cons
Pros:
- No shielding gas is required to be used with stick welding, which can be a plus side in outdoor or remote locations.
- It can be used for repairing rusted and painted aluminum parts.
Cons:
- Stick welding process is generally messier, creating more slag and spatter, which will result in a less clean finish.
- Quality welds in aluminum by a stick welder require a great deal of skill and experience.
- Contamination can result in increased porosity and weak welds.
MIG Welding Aluminum
MIG, or GMAW, is a semi-automatic welding process wherein the continuous feeding of wire is used as an electrode and with the use of an inert shielding gas that protects the weld area from any kind of contamination. In welding aluminum, a MIG welder from MIG welding suppliers is also acceptable because it is efficient and reliable to produce strong, clean welds.
Advantages of MIG welding aluminum include higher travel speeds compared to TIG welding, hence best suited for high-production environments.
Besides, MIG welding realizes higher deposition rates by laying down more filler material in a shorter time, increasing the overall efficiency. Its ease of use also makes MIG welding popular among beginners since the process is generally simpler to learn and operate. These advantages make MIG welding a good option for industrial applications and also for hobbyist projects in aluminum.
Laser Welding Aluminum
Laser welding is a modern method of welding where high-intensity laser beams are used to melt and join materials. Characterized by accuracy, speed, and small heat-affected zones, it is suitable for welding aluminum and other sensitive materials.
Benefits of Laser Welding Aluminum
Precision and Low Heat-Affected Zone: Laser welding has focused heat for precise welds with minimal distortion.
High-Speed Welding: The process is very fast, increasing productivity and efficiency.
Automation Capabilities: Laser welding can easily be integrated into automated systems to ensure consistent and repeatable results.
Suitable Laser Types for Aluminum Welding
- CO2 Lasers: Good for high-speed welding but may require careful setup to manage reflectivity issues with aluminum.
- Nd:YAG (Neodymium: Yttrium-Aluminum-Garnet) Lasers: Offer a good beam quality and are suitable for aluminum welding with high precision.
- Fiber Lasers (Ytterbium Doped): Have good beam quality and high efficiency, hence ideal for a lot of applications in welding.
- Disk Lasers (Yb:YAG Ytterbium): Combine the merits of fiber and solid-state lasers. It has high power and excellent beam quality.
Aluminum Welding Technique Comparison
Technique | Advantages | Disadvantages | Best Applications |
TIG Welding | High precision, clean welds, minimal spatter | Slower process, requires skill | Automotive, aerospace, thin materials |
MIG Welding | Faster welding, higher deposition rates, easier to learn | Less precise, higher spatter compared to TIG | High-production environments, thicker materials |
Stick Welding | No need for shielding gas, versatile in outdoor settings | Messy, higher risk of porosity, requires skill | Repairs, heavy-duty applications |
Laser Welding | High precision, minimal heat-affected zone, fast | Expensive equipment, requires expertise | High-precision industries, automated systems |
Common Aluminum Welding Problems and Solutions
Oxidation and Porosity
Causes:
- Poor cleaning, leaving residual oxide layers.
- Moisture and hydrocarbons in the weld area.
Solutions:
- Clean the aluminum surface properly before welding.
- Shield properly with shielding gas to protect the weld from atmospheric contamination.
- Control the welding environment to minimize moisture exposure.
Burn-Through and Warping
Causes:
- Too much heat input makes the aluminum melt too deep.
- Distortion due to improper heat distribution.
Solutions:
- Control welding parameters for proper heat input.
- Use heat sinks to absorb excess heat to avoid warping.
- Regulate welding speed for consistent heat input.
Impurities and Contamination
Causes:
- Dirt, oil, and other contaminants on the surface of the aluminum.
- Poor shielding gas coverage allows impurities to enter the weld pool.
Solutions:
- Employ strict cleaning before welding.
- Adequate shielding gas flow and coverage.
- Use good-quality welding equipment to avoid chances of contamination.
Different Material Thicknesses
Causes: Incorrect heat input results in a weak weld or burn-through.
Solutions:
- Welding parameters vary with the thickness of the material.
- Selection of filler materials shall be according to the base metal.
- Practice welding techniques that are accurate for accommodating thickness variations.
Tools and Equipment for Aluminum Welding
Welding Machines
Equipment | Uses |
TIG Welders | High-precision aluminum welding, offering great control and clean welds. |
MIG Welders | Faster welding in thicker materials, especially in a production environment. |
Stick Welders | For repair work and heavy-duty applications (less common for aluminum). |
Laser Welders | Advanced equipment for high-precision and automated welding. |
Safety Gear
Tools | Uses |
Welding Helmets | Protect eyes from UV rays, enabling visibility when welding. |
Gloves | Protection from burns and spatter with heat-resistant gloves. |
Protective Clothing | Flame-resistant jackets and pants prevent burns from sparks and heat. |
Respirators | Proper ventilation to protect against welding fumes and gases. |
Cleaning Tools
Tools | Uses |
Stainless-Steel Wire Brushes | Taking off the oxide layer without contaminating the aluminum. |
Grinders | Surface preparation and shaping aluminum components. |
Solvents | Cleaners (acetone and alcohol-based) are good for the removal of oils and contaminants. |
Welding Accessories
Accessories | Uses |
Heat Sinks | Absorb excess heat to prevent warping and burn-through. |
Clamps | Hold aluminum pieces in place during welding to ensure consistent weld quality. |
Protective Covers | Protect joints from contamination when not welding immediately. |
Aluminum Welding: Safety Tips
Aluminum Welding Safety | |
Personal Protective Equipment (PPE) | Welding Helmets |
Gloves | |
Protective Clothing | |
Respirators | |
Ventilation and Fume Management | Local Exhaust Ventilation |
General Ventilation | |
Fume Filters | |
Safe Handling Materials and Equipment | Proper Lifting Techniques |
Equipment Maintenance | |
Organized Workspace | |
Emergency Procedures | First Aid Training |
Fire Safety | |
Incident Response |
Closing Words
Welding aluminum is both exciting and daunting. Your ability to manage TIG, MIG, Stick, and Laser will not leave the slightest hope of getting high-quality, durable welds from all real-to-life applications with a great strength output.
More importantly, with appropriate welding machines from reliable welding machine suppliers, you can get higher efficiency as well as precision of aluminum welding tasks.
If you’re considering quality welding machines, YesWelder is a good choice for you. We provide a wide range of welder series for your welding projects. Explore further about our welding equipment!
FAQs
Can you TIG weld aluminum with DC?
Yes, you can TIG weld aluminum with Direct Current (DC), but it is not normally done. You would usually be welding aluminum in Alternating Current (AC) because that cleans up the oxide layer nicely on an aluminum surface as you are welding it.
Some higher-level TIG welders will give you AC/DC functions that you can switch between in. Because the process is DC, TIG welding with a lot of control is needed, and tends to clean the oxide layer not so well as AC. Thus, while it can be done, this inefficiency with inherent oxidation issues in aluminum makes DC not recommended for most applications for welding aluminum.
Can you weld aluminum with a stick welder?
Yes, it’s possible to weld aluminum with a stick welder, but it is less common and more challenging than other methods like TIG or MIG welding. Stick welding aluminum can result in messy welds with higher porosity and weaker bonds. It requires specialized aluminum electrodes and significant skill to manage the process effectively.
What is the best welding process for aluminum?
The best welding process for aluminum depends on the application and requirement. TIG welding is best for precision and high-quality welds, especially on thinner materials. MIG welding is suitable for faster production and thicker materials. Laser welding offers high precision and speed for automated systems. Generally, TIG welding is preferred for most aluminum applications due to its versatility and control.
How do you prevent oxidation in aluminum welding?
Preventing oxidation in aluminum welding involves thorough cleaning and proper shielding:
- Cleaning: Remove the oxide layer using stainless-steel wire brushes, grinders, or chemical cleaners before welding.
- Shielding Gas: Use pure argon or argon-helium mixtures to protect the weld area from atmospheric exposure.
- Proper Storage: Store cleaned aluminum in a dry environment and cover it to prevent re-oxidation before welding.
- Immediate Welding: Weld the aluminum immediately after cleaning to minimize oxidation reformation.
What safety equipment is necessary for aluminum welding?
- Welding Helmet: To protect eyes and face from UV rays and sparks.
- Heat-Resistant Gloves: To protect hands from burns and spatter.
- Protective Clothing: Flame-resistant jackets and pants for protection against heat and sparks.
- Respirators or Ventilation Systems: To prevent the inhalation of fumes.
- Safety Glasses: To protect eyes when the helmet is not in use.
Additional Resources
Tutorials
Organizations and Communities