TIG welding aluminum has turned out to be both rewarding and a challenging skill to master in aluminum welding. (Read Aluminum Welding: A Comprehensive Guide for more.) Unlike steel, the properties of aluminum are so different that special attention is required to avoid those imperfect welds due to incorrect settings or technique applied.
The following guide will walk you through how to TIG weld aluminum, offering practical tips and advice on how to enhance your welding performance, common pitfalls to avoid, and get solid and durable welds. Whether you’re a beginner or an experienced welder, this comprehensive guide will give you the knowledge you need to handle aluminum with confidence.
Why Aluminum Is Popular for Welding
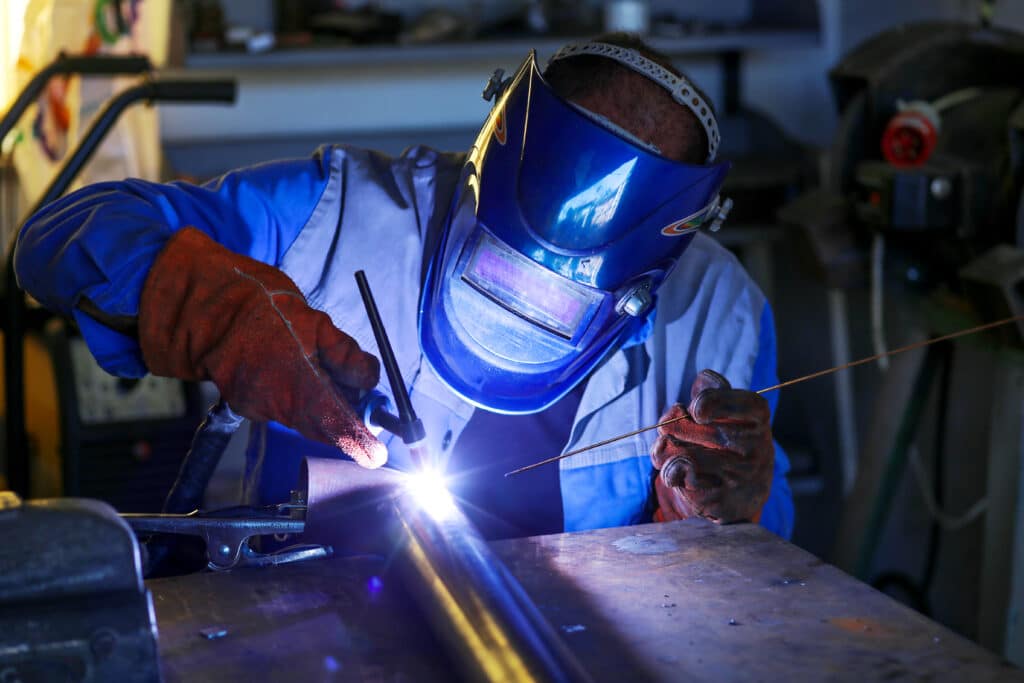
Aluminum is one of the most common metals welded in industry, especially due to several key advantages. Understanding these benefits can help you appreciate why aluminum is often chosen for welding applications:
- Lightweight: Aluminum is much lighter compared to most other metals, which makes it perfect for applications that are highly weight-sensitive, such as in the aerospace and automotive industries.
- Corrosion Resistance: Aluminum naturally forms an oxide layer that protects it from corrosion, making it ideal for use in outdoor and marine environments.
- Excellent Strength-to-Weight Ratio: Aluminum offers a good balance of strength and lightness, making it versatile for various structural applications.
- Thermal and Electrical Conductivity: Aluminum has a high degree of thermal and electrical conductivity, hence its multiple applications in electrical uses and those that involve heat transmission.
TIG Welding Aluminum: Challenges
Welding aluminum has its special challenges that demand particular techniques and settings. Among the important difficulties encountered are:
Low Melting Point
Aluminum is a metal with a relatively low melting point of approximately 1,220°F (660°C), which could easily make the material susceptible to burn-through if too much heat input is applied. Because of this, heat input is carefully controlled during the process of welding to avoid material damage.
High Heat Conductivity
Aluminum is an excellent conductor of heat, which is to say it loses heat very quickly. This can make it difficult to sustain a weld pool and will give the puddle some hard-to-handle characteristics, especially for the beginning welder.
Aluminum Oxide
The main challenge to welding aluminum is the natural, ongoing formation of an aluminum oxide layer on the surface. The melting point of this oxide layer is 3,700°F or 2,037°C, whereas for pure aluminum, it is much lower. For a clean, strong weld, it needs to be removed or treated accordingly.
Essential TIG Welding Settings for Aluminum
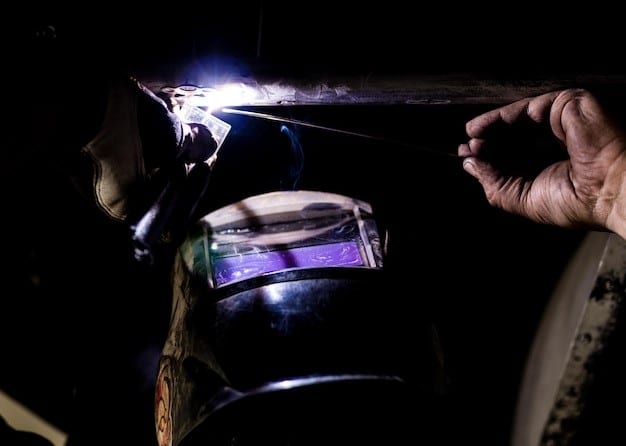
The right settings are vital when TIG welding aluminum. The most important of the following parameters will provide a strong and clean weld.
Polarity Settings
When TIG welding with aluminum, good arc stability and cleaning action could only be achieved using the right polarity. Unlike in welding steel, aluminum requires AC, polarity, which helps break the aluminum oxide layer and cleans the surface of the material.
- AC Polarity: Current in AC welding switches between positive and negative. This allows both a cleaning phase-when the polarity is positive-and a welding phase-when the polarity is negative.
- Why AC: The cleaning effect of the positive polarity serves to remove the oxide layer while the negative polarity allows deeper penetration into the base material.
Amperage Settings
The amperage setting is something that will make the heat input during the process, and welding aluminum is an important component.
- Amperage Calculation: The general rule when finding proper amperage to be used with TIG welding is the belief that with every 0.001-inch thickness, an amp will be used in material thickness. For example, working on a piece of aluminum about 1/8 inch in thickness, one would be thinking along the line of about 125 amps.
- Amperage Changing: Lighter-gauge metals will require amperage turned down, or it could easily burn through the aluminum. As the materials are thicker, that is when more amperage is needed to get enough penetration.
AC Output Frequency
Frequency setting controls stability and focus of the welding arc.
- Low Frequency (50-60Hz): Provides a wider, softer arc. It is good to use with bigger material. It does help in general cleaning.
- High Frequency (100Hz and above): Offers a tighter and more focused arc. In turn, this will make the process perfect for thinner materials and provide finer welds.
TIG Welding Aluminum Detailed Guide
The process of TIG welding aluminum requires great precision in technique and control. Here’s a step-by-step breakdown of the process:
Step 1: Preparation of Aluminum for Welding
Before doing the actual welding itself, it is important to prepare the aluminum correctly:
- Clean the Surface: Cleans off dirt and oil, grease, and very importantly an aluminum oxide layer. Use a stainless steel wire brush used on only aluminum and clean the metal or use any chemical cleaner on it.
- Check the Contamination: Check that the metal is clean of rusted spots or others that may potentially affect the metal’s weld’s integrity.
Step 2: Proper Torch and Hand Placement for Puddle Control
Good puddle control is the foundation for a sound, clean weld.
- Torch Placement: The torch should be kept at an angle of about 15° and held constant in a forward moving position.
- Hand Placement: Keep your hand as steady and in control as possible to guide the torch without imparting any unwanted motion to the puddle.
Step 3: Adding Filler Metal for a Strong and Clean Weld
Once you’ve established the puddle, it’s time to add the filler metal.
Dab and Move: Bring the filler rod to the leading edge of the puddle, keeping a steady cadence, adding filler metal as you move forward.
Common Aluminum Welding Problems
There are some common problems in welding aluminum that can give you less-than-perfect welds. Here’s how to prevent and correct them:
Preventing and Fixing Porosity
Gas becomes trapped in the weld and forms holes or bubbles. Most often, porosity is caused by contamination or improper flow of shielding gas.
How to avoid porosity:
- Clean the surface before welding.
- Adequate gas coverage and no leaks.
Avoiding Cracking and Burn-Through
Material gets too cold too quickly or material overheats causing it to break.
How to avoid this:
- Use a lower amperage setting for thinner aluminum.
- Avoid excessive heat input, and regulate weld speed for not overheating the material.
TIG Weld Aluminum Safety
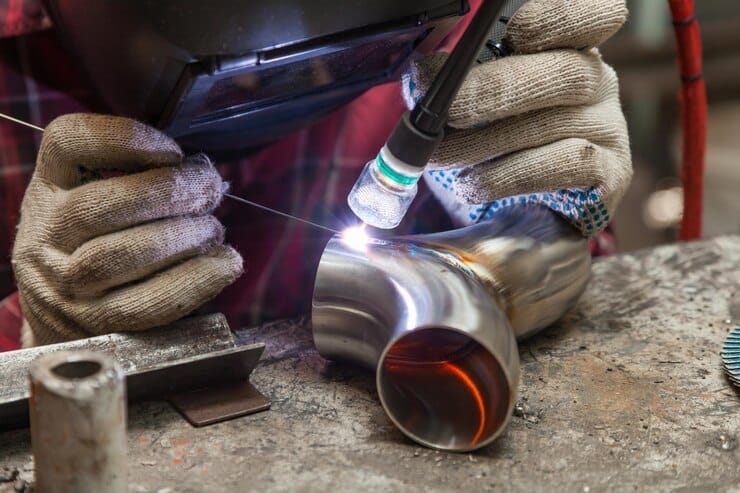
The most important concern of welding is its safety, and working with aluminum is no different. Following are some of the measures for your safety:
Protective Gear: One should always wear protective gear like gloves, a welding jacket, and safety glasses.
Ventilation: Proper ventilation is critical since aluminum welding produces very harmful fumes. Either use the welding fume extractor or go into a well-ventilated area.
Electrical Safety: The welding machine shall be operated by following electrical safety to avoid getting electric shock.
Closing Words
TIG welding in aluminum can become very rewarding once one has learned the proper technique and settings involved.
If one pays close attention to the particular properties of the aluminum and can set accordingly, high-quality welds that come out strong are achievable for applications. Be able to go through any sort of aluminum welding project with confident assurance, when you practice well and have suitable equipment from TIG welder suppliers.
YesWelder: Your Professional Welding Machine Partner
In regard to welding machines, YesWelder wholesale is a real and inexpensive wholesaler for both buyers and sellers alike. With the reputation of making quality long-lasting welding machines, YesWelder is a trusted partner when pros want to equip their operations with the best tools. Whether you are engaged in big industrial projects or small repair work, YesWelder has what you need to do the job right.
FAQ
What is the best filler metal for TIG welding aluminum?
4043 is a commonly used filler metal for welding aluminum with the TIG process. It’s versatile and can be used in general-purpose welding on most of the aluminum alloys.
How do I prevent burn-through when TIG welding aluminum?
To avoid burn-through, use the right amperage for the thickness of the aluminum, keep a steady pace, and don’t overheat.
Can I weld aluminum without filler rod?
Yes, you can weld without any filler rod when working with thin materials, but in most cases, adding filler metal is usually needed to strengthen the joint.
How to clean aluminum before welding?
Use a stainless steel brush, which is exclusively used for aluminum, followed by a chemical cleaner to remove oxide layers and contaminants.