Pulsed MIG welding, or Pulse Gas Metal Arc Welding (GMAW-P), is a modern welding process that combines the efficiency of traditional MIG welding with improved control of the welding process.
The new process has transformed the welding process by offering precise heat control, low distortion, and improved weld quality, particularly for thin metal. In this article, we’ll outline what is pulsed MIG welding, explain its advantages, explore its applications, and provide tips on how to get the best results.
How Does Pulsed MIG Welding Work?
At the heart of pulsed MIG welding is a significant difference from normal MIG welding: pulsing current. In contrast to normal MIG, pulsed MIG welding cycles between high peak currents and low background currents. This creates a pulsed arc that promotes control over heat input and weld quality.
The Process Included:
- High Current Pulse: This phase provides enough energy to melt the electrode wire and deposit metal on the weld joint. It finishes the fusion and penetration.
- Low Background Current: After the high pulse, current decreases, allowing the weld pool to cool slightly. This stabilizes the arc and minimizes heat input.
- Repeated Pulses: The process is cycled at rapid speed, allowing control of the weld bead with accuracy, preventing overheating and distortion, especially on thin material.
The key advantage of pulsed MIG is the ability to weld in a number of positions while controlling the heat input. This control is required when welding thin material since overheating will result in burn-through and faults.
Advantages of Pulsed MIG Welding
Pulsed MIG welding possesses several significant benefits that make it a more effective choice for many applications in welding:
Reduced Heat Input and Distortion
One of the critical strengths of pulsed MIG welding lies in its ability to maintain the lowest level of heat input compared to traditional MIG welding. With pulsing of the current, the welder is able to exercise complete control over the amount of heat delivered to the workpiece with utmost precision.
Thin Material Advantage: Heat from welding thin materials can result in burn-through. Pulsed MIG reduces this and also eliminates base metal distortion, creating a high-quality, clean weld.
Enhanced Weld Quality and Precision
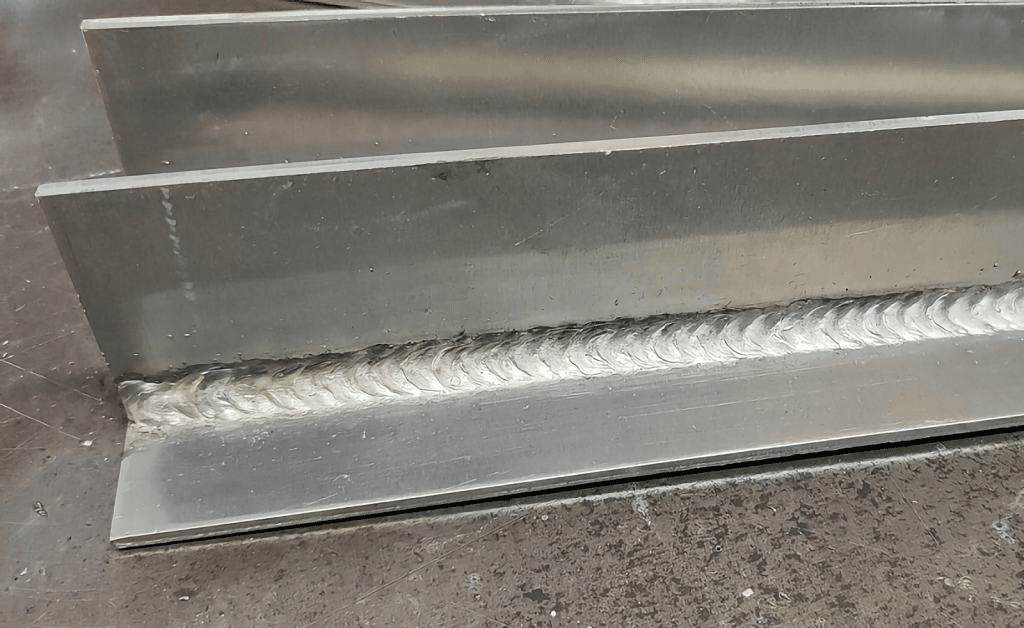
Pulsed MIG welding offers improved control of the weld pool. Welders can adjust pulse parameters such as peak current, background current, pulse frequency, and pulse width to create an optimum weld bead shape, depth, and quality.
Consistent Bead Appearance: Pulse parameter control creates a smooth, good-appearing weld bead with consistent penetration depth.
Less Spatter and Cleanup
Compared to conventional MIG welding, pulsed MIG produces significantly less spatter. Spatter is small metal droplets blown off the weld pool, providing the potential to increase post-weld cleanup time.
Less Spatter: Minimizing spatter not only improves the appearance of the weld, but it reduces cleanup time and expense as well.
Versatility Across Materials
Pulsed MIG is appropriate for welding diverse materials such as carbon steel, stainless steel, aluminum, and alloys. As it can be utilized with a variety of materials, it is mostly applied in the automotive sector, aerospace sector, shipbuilding, and general fabrication.
Ideal for Thin and Heavy Materials: Welding heavy and thin materials with minimal distortion makes pulsed MIG a best-fit candidate in numerous welding applications.
Enhanced Productivity
Pulsed MIG welding improves productivity in terms of increased arc stability, lower heat input, and reduced spatter. Such conditions yield higher travel speeds and enhanced weld quality, which lead to faster cycle times and greater throughput.
Improved Welding Speeds: Welders are able to create higher travel speeds without the reduction in weld quality, thereby enhancing overall productivity.
Applications of Pulsed MIG Welding
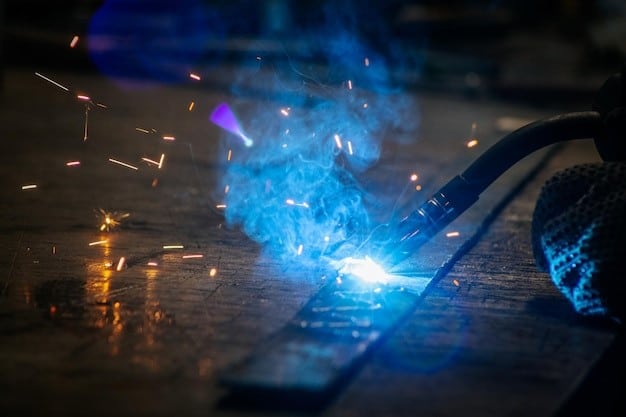
Automotive Industry
Pulsed MIG welding is often used in the welding of automotive body panels, chassis components, and exhaust systems. It is also apt for the level of accuracy required in automotive manufacturing because it has the ability to join thin materials with minimal distortion.
Aerospace
In the aerospace industry, pulsed MIG welding is required in welding aircraft structure, engine components, and fuel tanks. The ability of the process to provide precise control over heat input ensures high-quality welds that are crucial to aircraft reliability and performance.
General Fabrication
Pulsed MIG welding is applied in general fabrication for producing machinery, equipment, and structural components. Its efficiency and versatility make it the method of choice for most industrial welding uses.
Shipbuilding
Pulsed MIG welding, in shipbuilding, is used to weld the heavy and thin plates of the ship’s hull, decks, and seaborne structures. Good quality weld under marine conditions demanding heavily to be strong is all that counts when making the component last long in ships.
Considerations When Using Pulsed MIG Welding
Although the method of pulsed MIG welding has a lot going for it, there are some points that one needs to consider:
Equipment Requirements
Pulsed MIG welding requires pulsed waveform ability equipment, that is, suitable welding power supply and a wire feeder. While the equipment is more expensive than a usual MIG welder when initially purchased, productivity and weld quality benefits counteract the cost of investment in the longer run.
Equipment | Function |
Welding Power Source | Provides pulsed current for arc control |
Wire Feeder | Delivers consistent wire feed to the weld pool |
Shielding Gas | Protects the weld pool from contamination |
Click for more affordable while powerful MIG welder wholesale (also include pulsed MIG)! Here is one of the versatile MIG welder.
Training and Skill Development
Although pulsed MIG welding simplifies the process for welders of every experience level, correct training is still essential for becoming proficient in the technique. Welders must learn how to adjust pulse parameters based on the type of material, thickness, and joint configuration.
Material Thickness and Application Specifics
Different materials and thicknesses have to be compared with certain pulse settings to achieve adequate penetration and fusion. Awareness of the requirement of each application for welding is required to enhance weld performance and dependability.
Cost Factors
While pulsed MIG welding realizes long-term savings in cost through improved productivity and reduced material wastage, business firms must plan for the return on investment (ROI) based on their volume of production and welding needs.
How to Enhance Pulsed MIG Welding for Better Outcomes
Enhancing pulsed MIG welding for optimal results requires a few best practices:
Choosing the Right Shielding Gas
Different materials require different gas mixtures. For example:
- Carbon Steels: Typically use a 90% argon and 10% CO2 mixture.
- Aluminum: Requires 100% argon or argon/helium mixtures.
- Stainless Steel: Uses 98% argon and 2% CO2, with CO2 level limited to avoid sensitization.
Adjusting Welding Techniques
For optimum results, keep a stickout of 5/8 to 3/4 inch and employ a 45-degree work angle with a 10- to 15-degree travel angle. It is important to employ a push technique with pulsed MIG welding to achieve a smooth, fluid bead.
Arc Length Monitoring
Varying arc length can be used to control the weld puddle. A longer arc will produce less shorting, while a tighter arc provides more puddle control for precision welding.
Proper Connections
Ensure that all connections, i.e., grounding and wire feeder connections, are tight and secure. Loose connections could result in arc instability and poor weld quality.
Conclusion
Pulsed MIG welding is a cutting-edge process that provides numerous benefits to industries requiring precise, high-quality welds. With reduced heat input, improved weld pool control, reduced spatter, and increased productivity, pulsed MIG is transforming welding operations across various industries.
By understanding the process, advantages, and optimization methods, manufacturers and welders can realize the full potential of pulsed MIG welding to improve efficiency, reduce costs, and deliver improved welds.
FAQ
What is the difference between MIG and pulse MIG welding?
Technically, pulsed MIG is a highly-controlled spray-transfer MIG process. MIG welding uses a continuous current, while pulsed MIG alternates between high and low current for more control, less spatter, and reduced heat input.
Read this article to learn more about MIG welding: What is MIG Welding.
What is the purpose of pulse welding?
Pulse welding reduces heat input, improves weld pool control, minimizes spatter, and enhances productivity. It’s ideal for thin materials and precise welds.
Why is arc length important in pulsed MIG welding?
Arc length influences the size and control of the weld puddle. A longer arc can reduce shorting and minimize spatter, while a tighter arc provides better control for precision welding, especially on thin materials.
How can I ensure the best weld quality in pulsed MIG welding?
Make sure all connections, such as the ground and wire feeder connections, are secure. Loose connections can lead to arc instability, resulting in poor weld quality. Regularly inspect and maintain your equipment to ensure optimal performance.