Welding is an important industrial operation and an art. The diverse welding processes have varying degrees of complexity, material suitable for welding, and atmospheres.
Some welding processes are relatively simple and are suitable for do-it-yourselfers or hobbyists, whilst others are rather complicate and suitable for commercial or high-precision applications. Understanding the several welding processes and selecting the ideal one for your specific application will help ensure your success in the task.
MIG Welding (Gas Metal Arc Welding – GMAW)
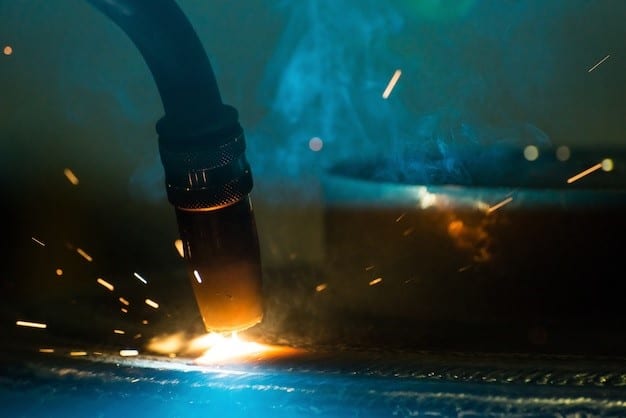
MIG welding (or Metal Inert Gas welding) is one of the most popular and simplest welding processes to learn. It is a continuous process of feeding a MIG welding wire through a welding gun. It creates an electric arc between the wire and the base metal.
The arc melts the wire and base metal, which creates a weld pool that solidifies to create a joint. It also uses shielding gas to protect the molten metal from air impurities for a clean weld. Know more about what is MIG welding.
MIG Welding Pros
- Ease of Use: A MIG welding machine is perfect for beginners as it has a simple setup and is simple to operate.
- Versatility: Can be utilized to weld a wide variety of metals such as steel, aluminum, and stainless steel.
- Clean Finish: Produces smooth, clean welds with minimal or no post-weld cleaning.
- Speed: It’s a fast welding process and is suitable for large-scale production.
MIG Welding Applications
This welding process is useful throughout automobile repair, construction, manufacturing, robotics, and shipbuilding industries and is an essential tool for industries that need good-looking and powerful welds.
Stick Welding (Shielded Metal Arc Welding – SMAW)
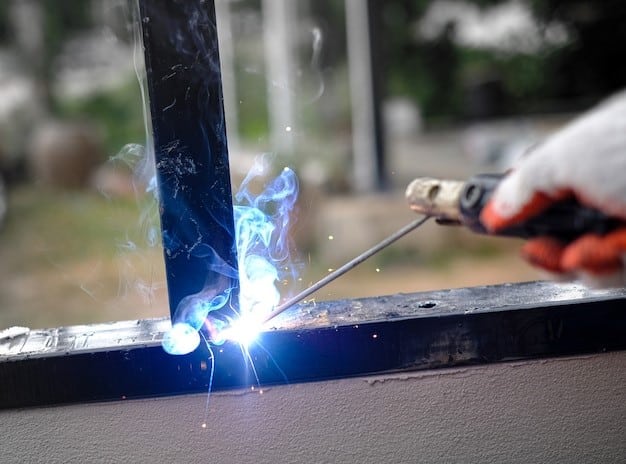
Stick welding, or Shielded Metal Arc Welding (SMAW), is one of the oldest and most common forms of welding.
It is a method where an electrode melts when it comes into contact with the base metal and forms a weld pool. The electrode consists of a flux coating that shields the weld area from airborne impurities.
Stick Welding Pros
- Affordable and Available: A Stick welder is low cost and requires minimal equipment, so it’s a great option for small shops and do-it-yourselfers.
- Outdoor Uses: It’s one of the few welding processes that can run outdoors in the rain or wind.
- Versatility: Stick welding can still work well on dirty, rusty, and painted metal, making it an excellent option for repair work.
Stick Welding Applications
Shielded metal arc welding is a common welding process in construction, pipe welding, and repair work, particularly for outdoor exposure or unfavorable environments.
TIG Welding (Gas Tungsten Arc Welding – GTAW)
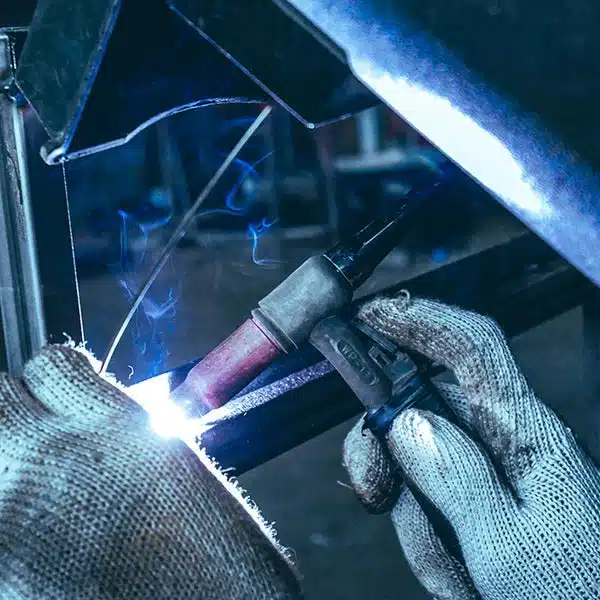
TIG welding, or Gas Tungsten Arc Welding (GTAW), is a process that uses non-consumable tungsten welding electrodes to create an arc between the electrode and work metal.
It can operate with or without filler metal and is an extremely versatile process. A constant flow of shielding gas (usually argon) must be there to protect the welded area.
TIG Welding Pros
- Accuracy: A wholesale TIG welder creates high-quality, precise welds, widely used in applications where aesthetics is valuable.
- No Cleanup: TIG welds are clean, reducing or removing the need for post-weld cleaning.
- Versatility: It can weld a very wide variety of metals, such as nonferrous metals like magnesium and aluminum.
TIG Welding Applications
The TIG welding is common in those industries that require precision, such as aerospace, automotive, bicycle frame building, and high-quality repairs.
Flux-Cored Arc Welding (FCAW)
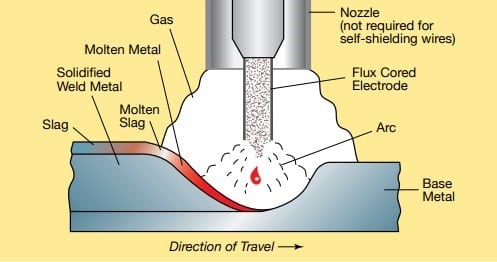
Flux-Cored Arc Welding (FCAW) resembles MIG welding but uses a filler wire having a flux core, which dispenses with the need for a shield gas source outside. The flux creates a gas shield about the weld and prevents contaminants entering the weld pool. Read more about Flux-Core Arc Welding.
Flux-Cored Arc Welding Pros
- Outdoor Friendly: Like stick welding, FCAW does not require an outside gas supply and is thus convenient for outdoor work.
- High Deposition Rate: FCAW is efficient and can deposit heavy materials with ease.
- Cost-Effective: The process does not require expensive shielding gases, thus the process is cheaper as a whole.
Flux-Cored Arc Welding Applications
FCAW helps a lot in heavy equipment manufacturing, ship construction, and construction, particularly for heavy metals and high-temperature applications.
Submerged Arc Welding (SAW)
Submerged Arc Welding (SAW) is an automatic welding process that uses a consumable electrode, and the arc is shielded by a covering of granular flux. The flux not only shields the weld area but also helps to make the process more efficient.
Submerged Arc Welding Pros
- High-Speed Production: SAW is ideal for mass production since it can weld quickly and efficiently.
- Safety: The flux layer protects the welder from harmful radiation and fumes.
- Deep Penetration Welds: It produces deep penetration welds with minimal distortion.
Submerged Arc Welding Applications
SAW is widely used in sectors that require thick metal welding, such as shipbuilding, steel fabrication, and heavy construction.
Gas Welding (Oxyacetylene Welding)
Gas welding (also oxyacetylene welding) utilizes a mixture of fuel gases (acetylene) and oxygen to produce a flame that can reach very high temperatures. The process allows for the melting of the base metals, which are then joined together.
Gas Welding Pros
- Portable: Gas welding is portable and can move to the site or utilized where mobility is important.
- Versatile: It will weld an enormous range of materials and functions well with thin metals.
- Simple Equipment: Gas welding requires a torch and fuel cylinders and is affordable for a hobbyist.
Gas Welding Applications
This welding technique is a typical method in pipe welding, metal repair, and cutting applications.
Thermit Welding
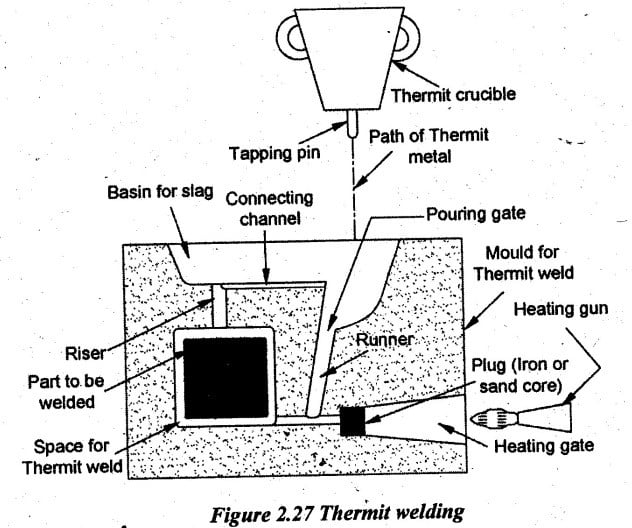
Thermit welding applies an exothermic reaction between iron oxide and aluminum powder to produce molten metal poured into the joint to form a strong connection. The process produces intense heat, which renders an external power source unnecessary.
Thermit Welding Pros
- No Power Source Needed: Thermit welding is not dependent on an external power source, a factor that enhances its use for field applications.
- Strong Welds: It achieves high-strength welds, a factor that makes it a perfect choice for joining similar metals and dissimilar metals.
Thermit Welding Applications
The thermit welding has a extensive use for railway track welding and heavy machinery repair.
Forge Welding
Forge welding is an old method of welding, in which the metal pieces are heated to a soft state and then pounded together to form a strong joint. It is also useful today in various applications.
Forge Welding Pros
- No Filler Material: Forge welding makes no use of any filler material like that of most other welding techniques.
- Traditional: It holds cultural and historical significance, particularly in blacksmithing and bespoke metalwork.
Forge Welding Applications
This welding process still work in aerospace applications and by blacksmiths for manufacturing bespoke tools and artwork.
Electron Beam Welding
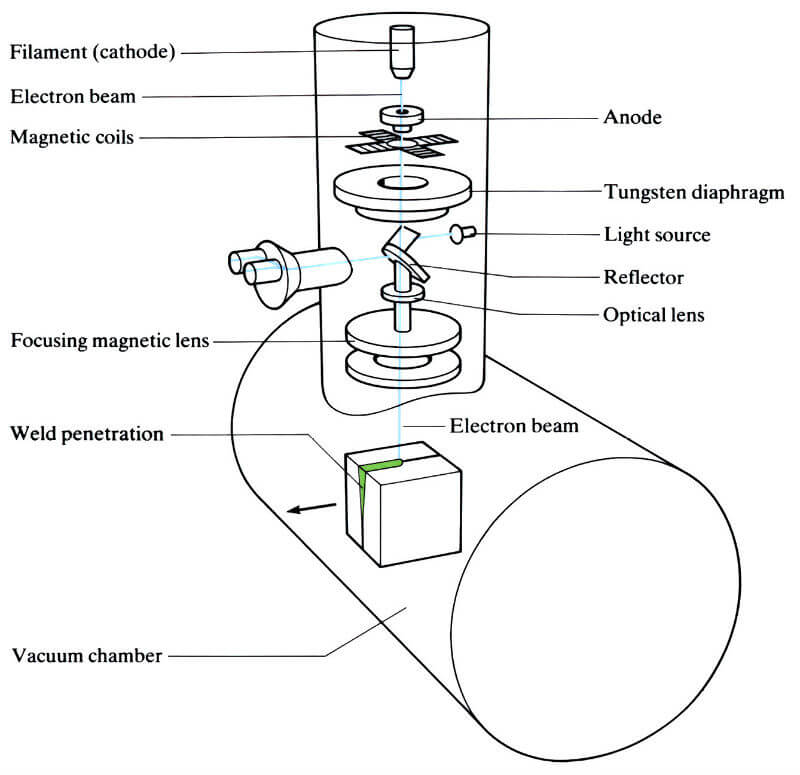
Electron Beam Welding (EBW) utilizes a focused beam of high-speed electrons to melt and join materials. EBW is an extremely precise welding process that produces neat and strong welds.
Electron Beam Welding Pros
- Precision: EBW provides high-quality, precise welds.
- Low Distortion: The method generates very low heat-affected zones (HAZ), a factor that is critical in maintaining the integrity of the materials.
Electron Beam Welding Applications
EBW is often used in aerospace, medical device manufacturing, as well as automobile application where precision is crucial.
Atomic Hydrogen Welding
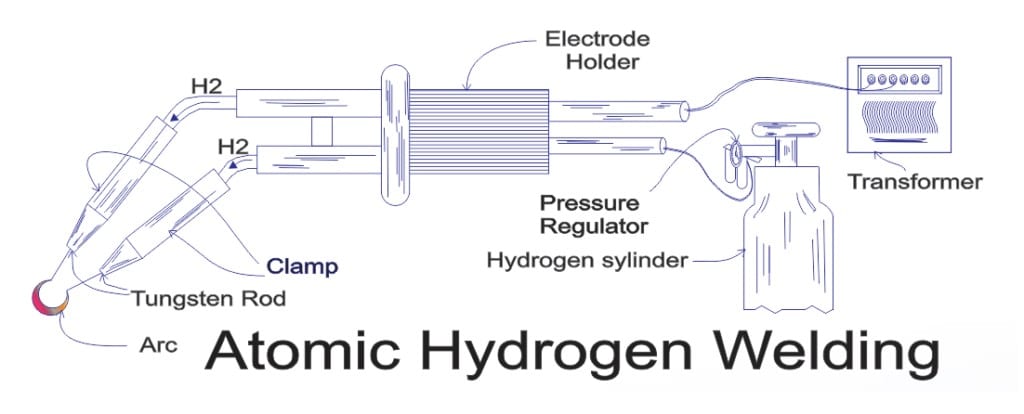
Atomic Hydrogen Welding (AHW) uses a hydrogen flame at high temperature to join metals, particularly tungsten. Though largely replaced by more efficient processes like MIG welding, it is still used in specialized applications.
Atomic Hydrogen Welding Pros
- High Temperature: Has the ability to generate extreme temperatures (up to 3000°C), which makes it most suitable for welding heat-resistant metals.
- Ideal for Tungsten: It is particularly suited for welding tungsten and other such metals.
Atomic Hydrogen Welding Applications
AHW is mainly used in high-temperature welding processes, e.g., aerospace applications.
Plasma Arc Welding
Plasma Arc Welding (PAW) is essentially the same as TIG welding except with more accuracy and precision. A thin, concentrated arc is generated with a plasma nozzle, resulting in higher penetration and better-controlled heat.
Plasma Arc Welding Pros
- Precision: Has narrower, clean welds with deeper penetration.
- Speed: Faster than TIG welding and thus perfectly adapted to mass production.
Plasma Arc Welding Applications
PAW finds application in industries with high-quality and deep weld requirements such as aerospace, automobile, and medical device production.
Resistance Welding
Resistance Welding relies on applying electric resistance to create heat for bonding materials. This is a fast, effective process and used under automated conditions.
Resistance Welding Pros
- Rapid and Effective: Ideal for high-volume production with quick welding times.
- Energy Economical: Minimal electricity required compared to other options.
- Automated: Often used in automated production environments.
Resistance Welding Applications
Automobile manufacturing, electronics, and metal fabrication most commonly apply resistance welding.
Welding Types Comparison Table
Welding Type | Process | Pros | Common Applications |
MIG Welding (GMAW) | Uses a continuous wire and shielding gas to create an arc between the wire and base metal. | Easy to use, versatile, fast, clean finish. | Automotive repair, construction, robotics, manufacturing. |
Stick Welding (SMAW) | Uses a consumable electrode coated with flux to create an arc, producing a molten pool to fuse metals. | Cost-effective, works outdoors, can weld rusty or dirty metals. | Construction, pipeline welding, repair work. |
TIG Welding (GTAW) | Uses a non-consumable tungsten electrode and shielding gas to create a precise weld. | High precision, clean welds, suitable for thin materials. | Aerospace, automotive, high-end repairs, bike frame welding. |
Flux-Cored Arc Welding (FCAW) | Uses a flux-cored wire that creates its shielding gas as it melts (similar to MIG welding). | Good for outdoor use, high deposition rate, cost-effective. | Heavy equipment, shipbuilding, thick metal applications. |
Submerged Arc Welding (SAW) | Uses a consumable electrode and a granular flux to create a submerged arc. | High-speed production, deep penetration, minimal spatter. | Shipbuilding, steel fabrication, heavy construction. |
Gas Welding (Oxyacetylene) | Uses an oxy-acetylene flame to melt and fuse materials. | Portable, simple equipment, versatile. | Pipe welding, metal repairs, cutting applications. |
Thermit Welding | Uses an exothermic reaction between aluminum powder and iron oxide to generate molten metal for joining. | No external power source needed, strong welds, can join dissimilar metals. | Railway track welding, large machinery repair. |
Forge Welding | Metal pieces are heated to a malleable state and hammered together to form a solid joint. | No filler material needed, traditional method still valued in custom work. | Aerospace, custom tools, blacksmithing. |
Electron Beam Welding | Uses a high-velocity electron beam to create a highly focused, precise weld. | Extremely precise, minimal distortion, deep penetration. | Aerospace, medical devices, automotive, precision welding. |
Atomic Hydrogen Welding | Uses an atomic hydrogen flame to create a high-temperature weld. | Very high temperatures for heat-resistant metals, ideal for tungsten welding. | Aerospace, high-temperature applications. |
Plasma Arc Welding (PAW) | Uses a focused plasma arc to provide precision and control for welding. | High precision, clean narrow welds, deeper penetration. | Aerospace, automotive, medical device manufacturing. |
Resistance Welding | Uses electric resistance to generate heat and fuse metals together. | Quick, energy-efficient, automated. | Automotive manufacturing, electronics, metal fabrication. |
Closing Words
Welding is a process that cannot be avoided as it helps industries weld metals together to make them stronger and more enduring products. The various types of welding processes and their advantages are important factors to know in order to choose the appropriate method for your project. Both professionals and hobbyists need to pick the best welding method to ensure their work is efficient and long-lasting.
By considering metal type, conditions, and required weld strength, you can decide which process will best suit you. Each process has advantages and is suitable for a certain application, from accurate aerospace work to heavy-duty construction repairs.
FAQ
What is the easiest type of welding for beginners?
Generally, MIG welding is easy for beginners since it’s simple to use. It has a clean finish, and requires little skill to achieve wonderful results. It’s widely used in DIY projects and light industry.
What’s the difference between MIG and TIG welding?
MIG welding uses a constant wire filler and shielding gas to join metals, and it is faster and more appropriate for thicker materials. TIG welding uses a non-consumable tungsten electrode and is more precise, making cleaner, smaller welds, and therefore best for thin work or high-precision use.
Read this related article:
What is the best welding method in outdoor uses?
Stick welding (SMAW) and flux-cored arc welding (FCAW) are excellent choices for outside use. These welding processes do not require a shielding gas, which could be dispersed by strong winds during inclement weather.
What type of welding is used in the aerospace industry?
TIG welding and electron beam welding are both very common in the aerospace industry because they create very precise and clean, strong welds. The processes are paramount to maintaining components’ integrity and strength used on aircraft and space vehicles.
Can I weld rusty metal with Stick welding?
Yes, Stick welding is one of the processes that can handle rust, grime, and paint on the metal’s surface. The flux coating on electrodes shields the weld from contaminants in the air and allows it to be used for repair of grimy or weathered metals.