Pre and post weld heat treatment—preheating before welding and heat treatment after welding—ensure welds are strong, durable, and safe. The processes of pre and post weld heat treatment are helpful to project success.
Keep reading and get more!
What is Pre and Post Weld Heat Treatment?
Pre-weld heat treatment, or preheating, involves heating the base material before welding to reduce thermal gradients, prevent hydrogen-induced cracking, and improve weldability.
Post-weld heat treatment applies controlled heat after welding to relieve residual stresses, temper hardened zones, and enhance material properties. These processes ensure welds meet rigorous standards, reducing the risks of common welding mistakes.
Standards like ASME Section VIII, AWS D1.1, and API 510 govern pre and post weld heat treatment. These codes specify:
- Temperature Ranges: E.g., 600–700°C for PWHT on carbon steel.
- Soak Times: Typically 1 hour per 25 mm of thickness.
- Cooling Rates: Controlled to avoid thermal shock.
Non-compliance can lead to rejected welds, costly rework, or safety hazards. For instance, ASME Section VIII mandates PWHT for carbon steel vessels thicker than 38 mm to ensure structural integrity.
Key Applications
Pre and post weld heat treatment is critical in high-stakes industries. For example, PWHT is mandatory for thick-walled pressure vessels to prevent catastrophic failures under high pressure, while preheating ensures crack-free welds in cold climates.
Here are some key applications:
Industry | Application |
Oil and Gas | Welding in the oil and gas industry is common in building pipelines, pressure vessels, and offshore platforms. |
Aerospace | Turbine blades, landing gear, and fuselage components are essential for welding in aerospace industry. |
Power Generation | Boiler tubes, nuclear reactor vessels, and steam turbines. |
Shipbuilding | Hulls, propeller shafts, and high-strength joints. |
Construction | Bridges, skyscraper frameworks, and heavy machinery. |
Pre-Weld Heat Treatment (Preheating)
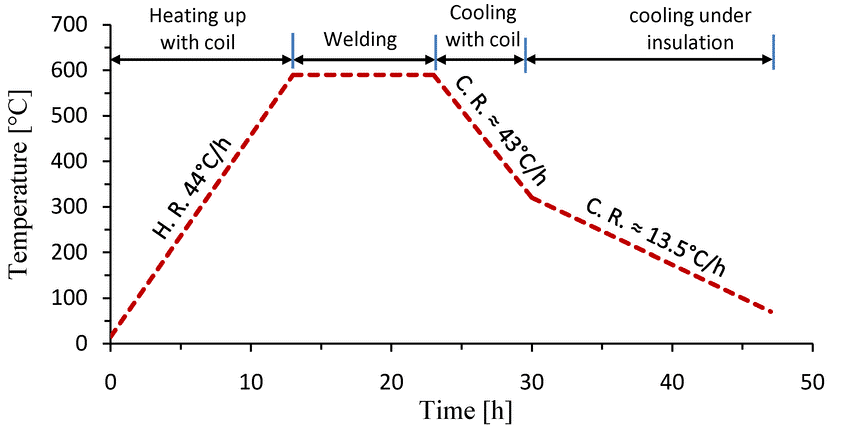
Why Preheating Is Essential?
- Reducing Thermal Gradients: Minimizes distortion and cracking by ensuring uniform heating across the weld zone.
- Preventing Hydrogen-Induced Cracking: Drives out moisture and hydrogen, critical for materials like low-alloy steels.
- Improving Weldability: Enhances fusion and reduces weld imperfections, especially for thick sections.
- Enhancing Worker Safety: Stabilizes the weld pool, reducing arc blow and spatter.
Process and Parameters
Materials requiring preheating include carbon steels, high-strength low-alloy (HSLA) steels, and chromium-molybdenum alloys. It involves heating the base material to a specific temperature before welding:
Temperature Ranges (per AWS D1.1):
- Carbon steel: 50–150°C.
- Low-alloy steel: 100–250°C.
- Chromium-molybdenum alloys: 200–350°C.
Methods:
- Resistance Heating: Electric pads provide precise, localized heating for small components.
- Induction Heating: Electromagnetic coils heat large structures quickly, ideal for pipelines.
- Flame Heating: Propane or oxy-acetylene torches are cost-effective but less precise, used in field applications.
Monitoring:
- Thermocouples: Attached to the material for real-time temperature data.
- Infrared Thermometers: Non-contact measurement for safety.
- Data Loggers: Record temperature profiles for quality assurance.
Common Mistakes and Risks
- Underheating: Fails to prevent hydrogen cracking, especially in thick or high-carbon materials.
- Overheating: Causes grain growth, reducing material strength and toughness.
- Uneven Heating: Creates thermal stresses, leading to distortion.
Post-Weld Heat Treatment (PWHT)

Benefits of Post Weld Heat Treatment
Post weld heat treatment delivers critical advantages:
- Stress Relaxation: Reduces residual stresses from welding, preventing distortion and cracking.
- Tempering: Softens hardened zones in the heat-affected zone (HAZ), improving ductility.
- Hydrogen Removal: Eliminates trapped hydrogen, reducing delayed cracking risks.
- Improved Toughness: Enhances resistance to brittle fracture, critical for low-temperature applications.
- Corrosion Resistance: Minimizes stress corrosion cracking in harsh environments like offshore platforms.
For example, PWHT on a carbon steel pressure vessel can increase its fatigue life by 25 years, saving millions in maintenance costs.
Process and Parameters
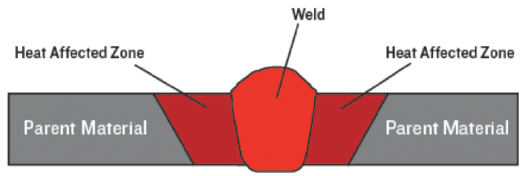
PWHT involves heating the welded component, holding it at a target temperature, and cooling it gradually.
1. Temperature Ranges (per ASME Section VIII):
- Carbon steel: 600–700°C.
- Low-alloy steel: 650–760°C.
- Chromium-molybdenum alloys: 700–900°C.
2. Methods:
- Furnace-Based: Entire components are heated in large ovens, ideal for pressure vessels.
- Localized Resistance: Heating pads or blankets treat specific weld zones, common for pipelines.
- Induction: Coils provide rapid, precise heating for on-site applications.
3. Soak Times: 1 hour per 25 mm of thickness, with a minimum of 30 minutes.
4. Cooling Rates: 100–150°C per hour to prevent thermal shock, often in a furnace or insulated environment.
5. Quality Control: Use data loggers to record temperature profiles and ensure compliance with ASME codes. Non-destructive testing (NDT) like ultrasonic inspection post-PWHT verifies weld integrity.
When to Use PWHT?
- Thick Materials: Carbon steel >38 mm, low-alloy steel >25 mm (ASME Section VIII).
- High-Strength Alloys: E.g., Cr-Mo steels prone to cracking.
- Critical Applications: Pressure vessels, pipelines, and nuclear components.
- Code Requirements: ASME, API, or AWS standards.
Comparing Pre and Post Weld Heat Treatment
Complementary Roles
Preheating and PWHT are complementary. Combining both processes is standard for critical welds, but preheating may suffice for thin materials, while PWHT is critical for thick sections.
- Preheating: Prepares the material by reducing thermal shock and hydrogen content, ensuring a stable weld pool.
- PWHT: Refines the weld by relieving stresses and improving mechanical properties, ensuring long-term performance.
Aspect | Pre-Weld Heat Treatment | Post-Weld Heat Treatment |
Timing | Before welding | After welding |
Temperature | 50–350°C | 600–900°C |
Goal | Prevent cracking, improve weldability | Relieve stresses, enhance properties |
Methods | Resistance, induction, flame | Furnace, localized resistance, induction |
Duration | Minutes to hours | Hours, based on thickness |
Monitoring | Thermocouples, infrared | Data loggers, thermocouples |
Tools for Pre and Post Weld Heat Treatment
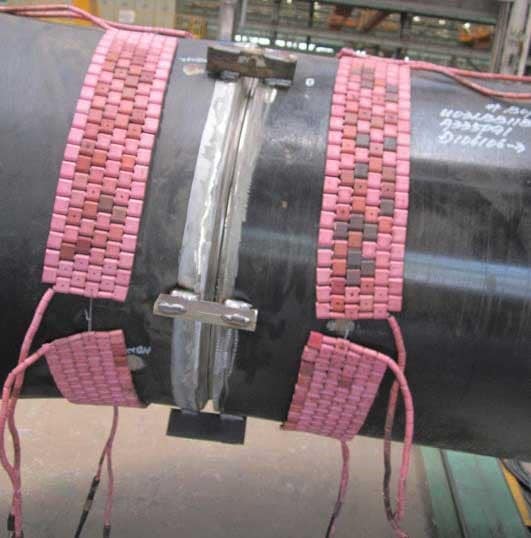
Effective heat treatment relies on specialized equipment. We’ve collected some of the essential tools to consider:
Heating Systems
- Resistance Heaters: Ceramic pads or blankets for localized heating.
- Induction Coils: Electromagnetic systems for rapid, uniform heating.
- Furnaces: Gas or electric ovens for large components.
- Ceramic Mat Heaters: Flexible, lightweight options for field welds.
Monitoring Tools
- Thermocouples: Measure surface temperatures with ±1°C accuracy.
- Infrared Cameras: Detect hot spots or uneven heating.
- Data Loggers: Store temperature profiles for code compliance.
Control Units: Programmable systems adjust power output to maintain target temperatures.
Emerging Technologies
- IoT Monitoring: Sensors transmit real-time temperature data to cloud platforms, enabling remote oversight.
- Automated Systems: Robotic arms apply heating pads with precision, minimizing human error.
- Hybrid Heating: Combines induction and resistance for faster, energy-efficient processes.
How to Choose the Right Tools
We provide some factors for you to consider. This may help you choose the right tools for pre and post weld heat treatment.
- Project Scale: Furnaces for factory-based vessels, portable induction for field welds.
- Material Type: Induction for high-alloy steels, resistance for carbon steel.
- Site Conditions: Battery-powered systems for remote sites, gas furnaces for industrial plants.
- Budget: Flame heating is cheapest but least precise; induction is costlier but faster.
Alternatives to Traditional Heat Treatment
Alternatives | Pros | Cons |
Composite Repairs | Fast, low-cost, no energy required. | Limited to non-critical applications, less durable than PWHT. |
Mechanical Stress Relieving | Energy-efficient, portable. | Less effective for thick materials. |
Final Thoughts
Pre and post weld heat treatment are non-negotiable for creating strong, safe, and compliant welds. Preheating prevents defects during welding, while heat treatment after welding ensures long-term durability and performance.
By adhering to ASME and AWS standards, leveraging modern heating equipment and other wholesale welding machines, and addressing other welding challenges, one can achieve flawless welds.
FAQs
What is the difference between pre and post weld heat treatment?
Preheating occurs before welding to prevent cracking, while PWHT happens after to relieve stresses and improve properties.
When is PWHT mandatory per ASME codes?
PWHT is required for carbon steel thicker than 38 mm or alloys prone to cracking, per ASME Section VIII.
What are the benefits of post weld heat treatment for carbon steel?
PWHT reduces stresses, improves ductility, and prevents cracking, extending component life.
How do I choose between resistance and induction heating?
Resistance is cost-effective for small projects; induction is faster for large or alloy components.
Can preheating be skipped for thin materials?
Yes, for materials under 25 mm, per AWS D1.1, but always check code requirements.
Is post weld heat treatment required for stainless steel welds?
Not always. Austenitic stainless steels usually don’t require PWHT due to their inherent corrosion resistance and ductility. However, some duplex and martensitic stainless steels may require it to restore toughness or reduce residual stress.
Can flame heating be used for post weld heat treatment?
Flame heating is not typically recommended for PWHT due to the difficulty of controlling temperature uniformly. Furnace, resistance, or induction methods provide much better control and repeatability.