In welding aluminum, choosing the right welding wire is as crucial as the welding process and welding equipment. Aluminum welding wire plays a crucial role in creating quality, long-lasting welds that are worth the wait.
But with so many on the market, how do you choose the ideal aluminum welding wire for your project? Keep reading and we’ll explore the different types of aluminum welding wires, their additives, common issues, and how to choose the best one for your specific needs.
What Are Aluminum Welding Wires?
Aluminum welding wires are specialty wires in welding to connect aluminum materials. Wires are forced through a welding tool to create an electrical arc that fuses the base metal and the filler metal to create a quality joint.
Aluminum wires are of various grades and types developed for different welding processes and applications. The most common aluminum welding processes are TIG (Tungsten Inert Gas) and MIG (Metal Inert Gas). The wire you select will be influenced by the base material, the welding process, the weld strength, etc.
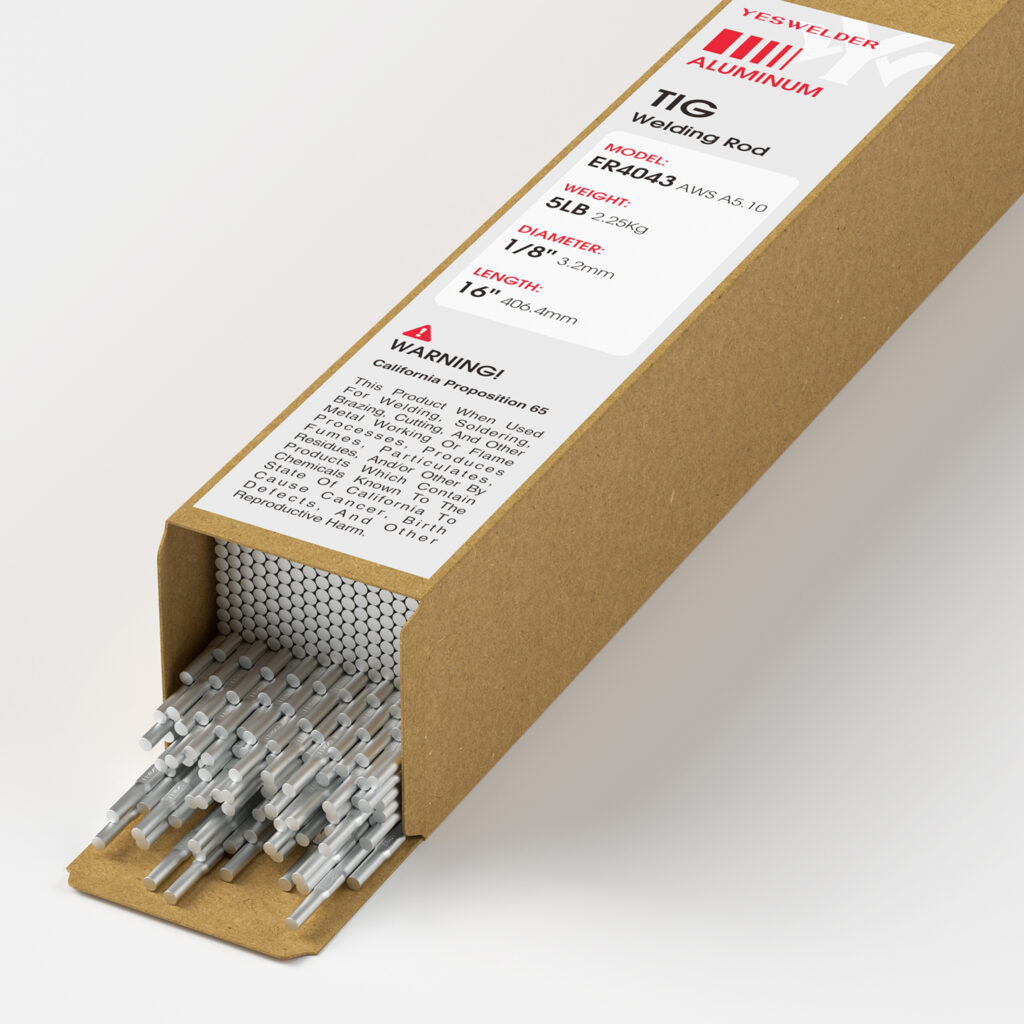
Additives in Aluminum Welding Wires
Aluminum welding wires typically have additives to improve performance. The additives enhance the wire properties, making it simpler to handle and providing solid, long-lasting, and wear-resistant welds.
Magnesium
Magnesium is a common aluminum welding wire additive. It makes the weld stronger and generally gives the wire higher corrosion resistance.
Magnesium appears in ER5356 welding wire, commonly employed to weld aluminum alloys like 5052 and 5083. The additive makes the wire suitable for high-strength applications in the auto and marine industries.
Silicon
Silicon is one of the prevalent additives and to the weld more fluid. It lowers the wire melting temperature, flowing more easily and forming a smooth weld pool.
Incorporated into the ER4043 welding wire handy, it is common in welding aluminum alloys like 3003, 6061, and 6063. Silicon also increases the appearance of the weld so that it will be smoother and more aesthetic-looking.
Do High Quality Aluminum Welding Wires Matter?
Yes, high-quality aluminum welding wires are necessary to produce the best results in your welding work. Some of the benefits of using high-quality aluminum welding wires include:
- Stronger Welds: High-quality wires produce stronger, more resistant welds. This is critical in aerospace, automotive, and construction, where weld strength is paramount.
- Improved Aesthetic Quality: They produce smoother, better-looking welds with fewer flaws.
- Less Spatter and Cleanup: They produce less spatter, reducing cleanup time on the weld when the process is complete.
- Better Feedability: Quality wires have better feedability (i.e., they become entangled less and do not lead to feed issues in the welding machine).
- Consistency: These welding wires provide more consistent results, something that matters if you’re doing professional-level projects.
ER4043 Aluminum Welding Wire
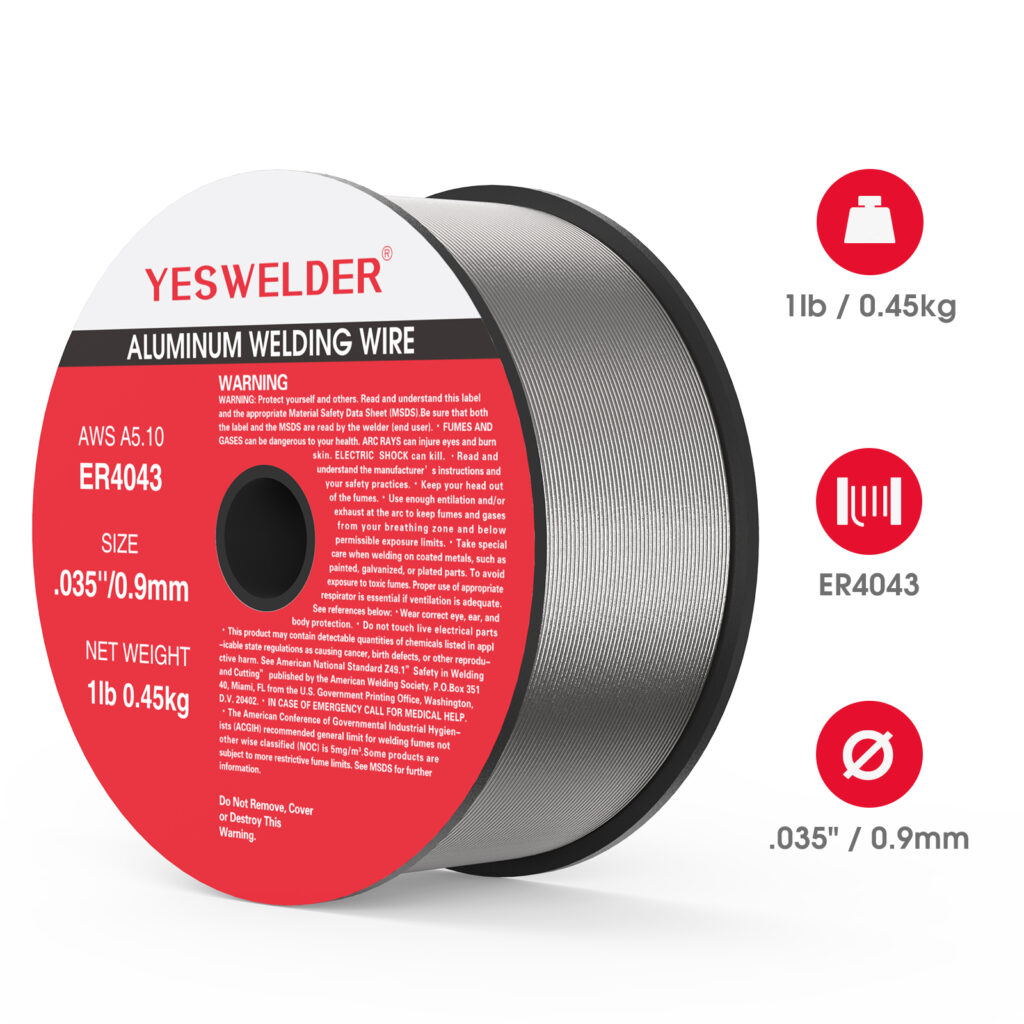
ER4043 is a common aluminum welding wire. It is an all-position general-purpose welding wire for a wide variety of uses, from automobiles to household appliances.
The ER4043 contains 5% silicon, which increases the weld pool’s fluidity, so welds are more fluid and are less apt to crack. It is especially ideal for welding aluminum alloys 5052 and 6061, and is usual in industries that include appearance welds as a consideration, such as bicycle frames and metal fabrication.
ER4043 Key Properties:
- Tensile Strength: 21,000-33,000 psi
- Melting Range: 1065°F-1170°F (574°C-632°C)
- Color Match After Anodizing: Gray
- Suitable for Base Materials: 3003, 5052, 6061, and 6063 aluminum alloys
ER5356 Aluminum Welding Wire
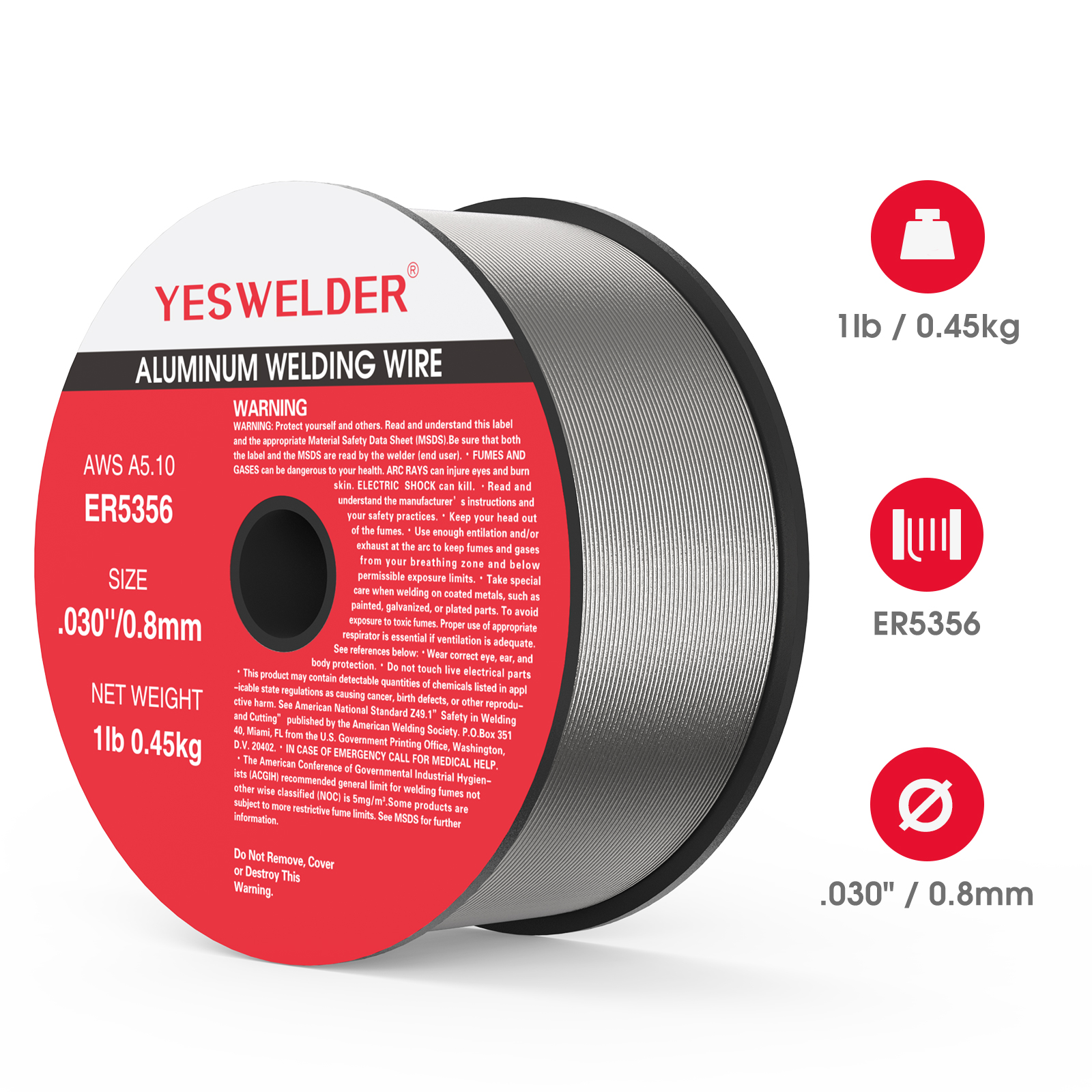
ER5356 is another widely used aluminum welding wire but with an addition of 5% magnesium, which makes it stronger and more corrosion-resistant. It is used extensively where additional strength is a requirement, but not necessary, (i.e., in marine, aerospace, and automotive applications.)
The ER5356 is ideally helpful for welding alloys such as 5083 and 5183, which are common in saltwater applications since magnesium is extremely resistant to corrosion in saltwater environments.
ER5356 Key Properties:
- Tensile Strength: 29,000-45,000 psi
- Melting Range: 1060°F-1175°F (571°C-635°C)
- Color Match After Anodizing: White
- Suitable for Base Materials: 5052, 5083, 6061 aluminum alloys
ER4043 vs. ER5356
Property | ER4043 | ER5356 |
Additives | 5% silicon | 5% magnesium |
Weld Puddle Fluidity | Higher fluidity | Good, but lower than 4043 |
Suitable for High-Temp Applications | Yes | No |
Color Match After Anodizing | Gray | White |
Typical Tensile Strength | 21,000-33,000 psi | 29,000-45,000 psi |
Weldability | Easier to weld, lower crack sensitivity | Stronger welds but harder to weld |
Choose the Right Aluminum Welding Wire for Your Application
Choosing the right aluminum welding wire depends on several factors, including the type of aluminum alloy being worked with, the welding procedure, and the wire diameter.
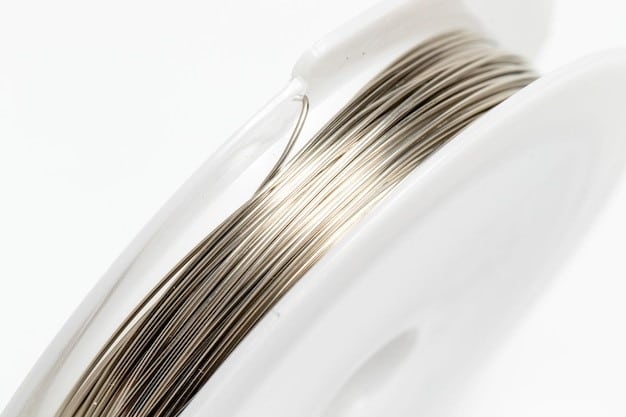
The Right Wire for Aluminum Alloys
Different aluminum alloys have distinct properties that require different welding wires.
As an example, ER4043 is best used with alloys like 3003 and 6063, while ER5356 is better used with alloys like 5052 and 5083. Be certain to match the wire with the alloy you’re working with to achieve good, consistent welds.
The Right Wire for Welding Processes
The welding process you’re doing also affects choosing the MIG welding wire. MIG welding is a common procedure for aluminum, and both ER4043 and ER5356 can be utilized with a MIG welding machine.
In case you’re using TIG welding, you can opt for a smaller wire and need to ensure that the wire is clean and impurity-free. Read more in TIG Welding Aluminum Complete Guide and Mastering MIG Welding Aluminum.
Wire Size and Feedability
The wire size is necessary to ensure proper feedability through the welding machine. Thicker wire may be necessary for heavy-duty applications and thinner wire for finer applications.
Aluminum wire is soft, and you may encounter some feeding issues, so it’s best to choose a wire size that your welding machine can feed.
Aluminum Welding Wire: Troubleshooting Common Problems
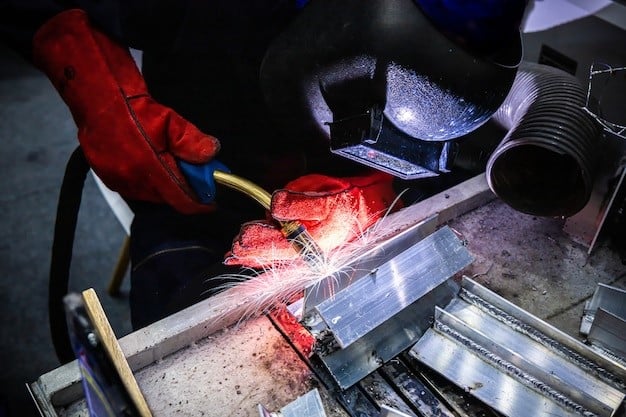
Poor Quality Welds
Inconsistent welds can be caused by the incorrect choice of wire, incorrect settings, or contamination. Ensure that you’re utilizing the correct wire for the alloy and that the welding machine is set correctly.
Wire Feed Problems
Wire feed issues are frequent while welding aluminum since aluminum wire is soft and can easily tangle. Using a spool gun or push-pull system could enhance the feedability.
Overcoming Oxide Layer
When aluminum comes into contact with air, it creates an oxide layer that may result in low-quality welds. To get over this, scrub the aluminum well prior to welding, and make sure that your welder is set on the proper parameters.
YesWelder: Partnering with a Professional Welding Machine Supplier
If you are looking for quality welding equipment and accessories, YesWelder wholesale is trusted by distributors and buyers.
With a track record of being reliable and affordable, YesWelder offers a comprehensive range of aluminum welding machines. Our products include MIG, Stick and TIG welders, spool guns, and multi-process machines. For a professional welder and a novice, YesWelder has the equipment necessary to achieve high-quality results for aluminum welding needs.
FAQ
What is the ideal wire for aluminum welding?
The ideal wire depends on which alloy you are welding. ER4043 is acceptable for alloys like 6061 and 3003, but ER5356 is better for higher-strength alloys like 5052 and 5083.
Can I use flux-cored wire for aluminum?
No, there isn’t any flux-cored aluminum welding wire for arc welding. Solid aluminum wire is used with MIG or TIG welding processes.
Why is aluminum welding wire softer than other metals?
Aluminum is a soft metal, and aluminum welding wire is designed to be flexible and easy to feed through welding machinery.
What is the purpose of magnesium in aluminum welding wire?
Magnesium adds strength and increases the corrosion resistance of the weld, making ER5356 a good choice for use in applications exposed to saltwater or other corrosive elements.
How do I prevent feedability problems with aluminum welding wire?
To prevent feedability issues, use a spool gun or push-pull system, which better feeds the wire through the machine.