Some may be wondering which is better for their needs – arc or gas welding? The short version is that both techniques have their advantages. But, there is more to the story than that.
In this guide for beginners, you can read about the details of both arc and gas welding, including how they function, their relevance in today’s industries, and choosing the right option based on your requirements.
What Is Welding and Why Is It Important in 2025?
Welding is the method of joining materials (commonly metals) together by using heat and/or pressure. While this process was hundreds of years ago, welding in recent years is far more efficient than it used to be thanks to new technologies like computers and smart algorithms.
Our modern world heavily relies on welding – from repairs to building skyscrapers to fabricating vehicles, aeroplanes, and even art sculptures.
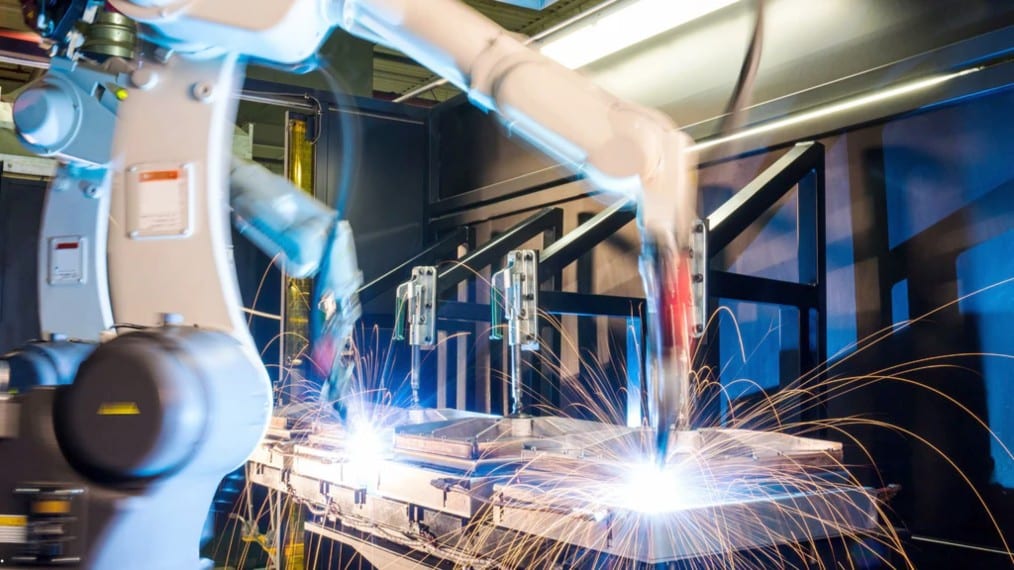
What Is Arc Welding?
To join two metals with arc welding electricity is used to produce an intense heat arc that melts both the base metal and electrode (or filler) into a joint. It is primarily used in cases where speed and precision are critically important alongside considerable strength.
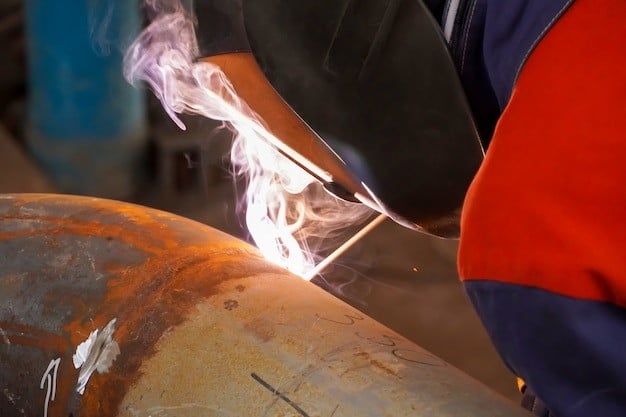
How It Works?
A molten weld pool is formed when the metals at the joint are neutralized by an electric arc which is generated as the electrode tip touches the metal and then moves back slightly. The molten mixture cools down to solidify later on.
Types of Arc Welding in 2025
Different forms can be applied depending on job requirements:
1. Stick Welding (SMAW – Shielded Metal Arc Welding): Stick welding machines utilizes a flux-covered consumable electrode as a shield with gas as well as slag provided once the arc melts, and flux ensures protection for the weld pool during cooling.
- Heavy-duty outdoor jobs find this very useful around construction sites or other such industrial locations, almost exclusively.
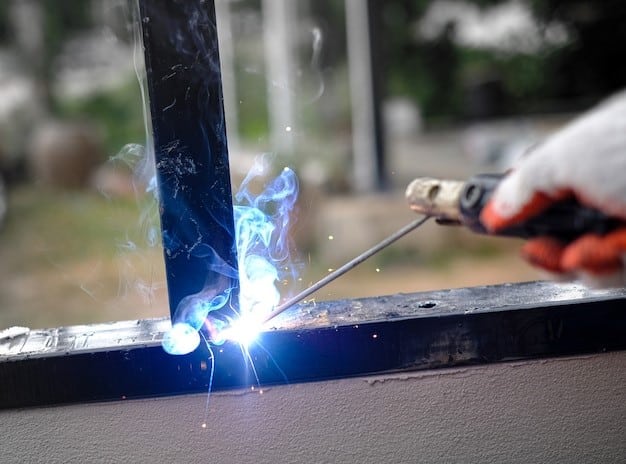
2. MIG Welding machines (GMAW – Gas Metal Arc Welding): Utilises continuously fed wire through a gun along with shielding gas like argon or CO₂ for prevention of external contamination.
- Works best for light construction activities and with inexperienced personnel due to it being much quicker and cleaner to use sand, which is easier to learn.
3. TIG (GTAW – Gas Tungsten Arc Welding): In TIG welding, a tungsten electrode that does not melt is used with an inert gas, usually argon, for shielding. A filler rod can be added but is optional.
- Works with high precision and is used in the aerospace and automotive industries as well as for intricate artistic welds.
4. Flux-Cored Arc Welding (FCAW): Similar to MIG welding, flux-cored has a unique tubular wire with special fillers. Additional shielding gas may or may not be required.
- Best suited for thick outdoor materials.
Ideal Applications
Preferred areas for arc welding are:
- Shipbuilding
- Pipeline welding
- Heavy Construction
- Fabrication shops
- Bodywork on vehicles, especially with MIG
What Is Gas Welding?
Gas welding goes by the names ‘mes’ and ‘oxy-fuel welding’. It uses flames fuelled by burning gases such as oxygen paired with fuel (commonly acetylene). This process is older and simpler but still effective where advanced technology is not available because it is cheap and portable.
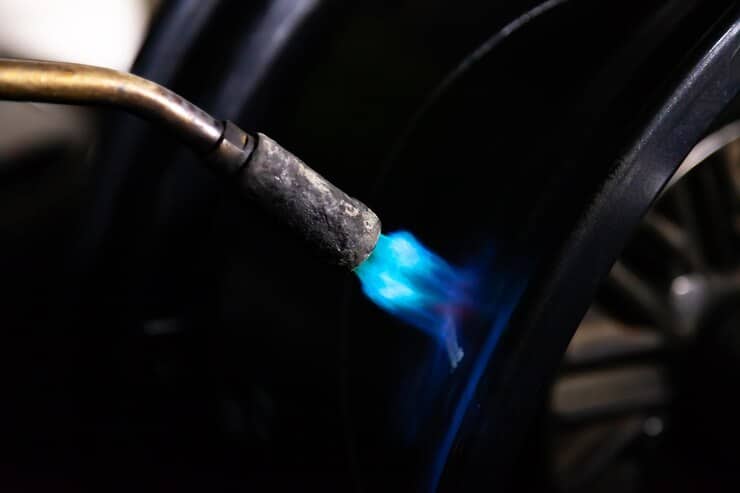
How It Works?
The torch combines both oxygen and acetylene and then ignites them to yield focused flames. You manually work the flame to adjust parts of metal until they become liquid and blend either without a filler or together with a filler rod.
Common Gas Welding Types
1. Oxy-Acetylene: Uses hydrogen instead of acetylene. It is cleaner and cooler than what is often used in applications needing sterility.
- The standard and hottest flame. Suitable for cutting and welding.
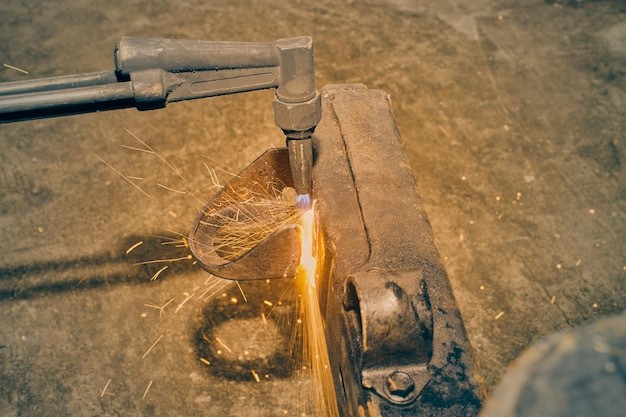
2. Oxy-Hydrogen Welding: Replaces acetylene with hydrogen, not using it entirely. Along with being fuel, it is also less contaminating when compared to traditional rituals where the element gets burnt off.
- Cleaner but cooler flame. Use jewelry and lab work.
3. Air–Acetylene Welding: Utilises acetylene but does away with the required oxygen tank, using atmospheric air instead as the substitute, mixing both elements in an external tank rather than within a closed system like other weld processes would operate. Proper use has been made of this innovation since it’s ideally suited for soft metals.
- Combines acetylene with air; used for softer metals and plumbing.
Ideal Applications
Gas welding is ideal for the following:
- Sheet metal work
- Copper, brass, and bronze components
- Automotive exhaust repair
- HVAC services
- Sculptures and artistic works in metal
Arc Welding vs Gas Welding: A Side-by-Side Comparison
For clarity, here is a side-by-side comparison of both methods.
Feature | Arc Welding | Gas Welding |
Heat Source | Electric arc | Oxy-acetylene flame |
Max Temperature | Up to 6,500°F | Up to 5,700°F |
Power Required | Yes | No |
Precision Level | High (especially TIG) | Moderate |
Best For | Thick metals, structural jobs | Thin metals, mobility |
Learning Curve | Steeper | Easier |
Portability | Limited (needs power) | High (portable tanks) |
Setup Cost | Moderate to High | Low to Moderate |
Safety Risks | Electric shock, UV exposure | Gas leaks, explosion risk |
Arc Welding vs Gas Welding in Industries
Now we can look at how each method performs across industries looking ahead.
Construction Industry
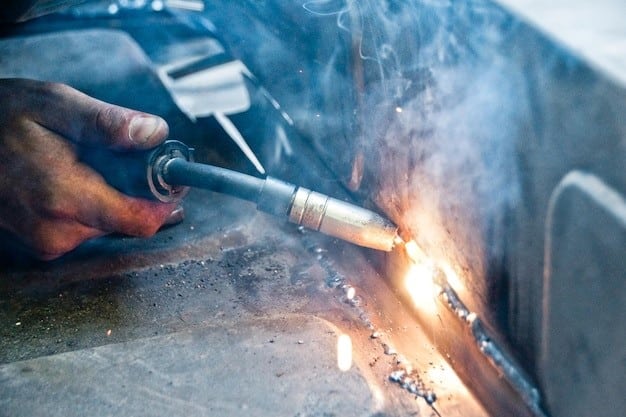
- Arc Welding: Dominates stick and MIG welding for their strength, plus welding steel beams, structural frames, pipelines, etc.
- Gas Welding: Almost entirely absent in new construction other than small repairs or confined areas where torch access is made.
Automotive Industry
- Arc Welding: MIG and TIG are used for frame construction along with body panels and exhaust systems.
- Gas Welding: Applicable to small tasks like restoring vintage cars where flame control is required.
Aerospace Industry
- Arc welding: TIG is very important for the industry because of its accuracy while joining thin sheets of aluminum or titanium.
- Gas Welding: Not often practiced because of a lack of accuracy and safety issues.
Art and Sculpture
- Arc Welding: It aids in creating larger metal structures which need to be durable.
- Gas Welding: Artists prefer gas welders because they can use the torch freely when shaping delicate pieces, and adding or joining intricate parts together.
Shipbuilding and Rail
- Arc Welding: FCAW and stick welding are the standards for arc welding, which makes it essential for thick steel plate intersections.
- Gas welding: It is rare due to the limitations of flames and being a slower method.
In short: Arc welding will power the future, while gas welding maintains niche value.
Advantages of Arc Welding
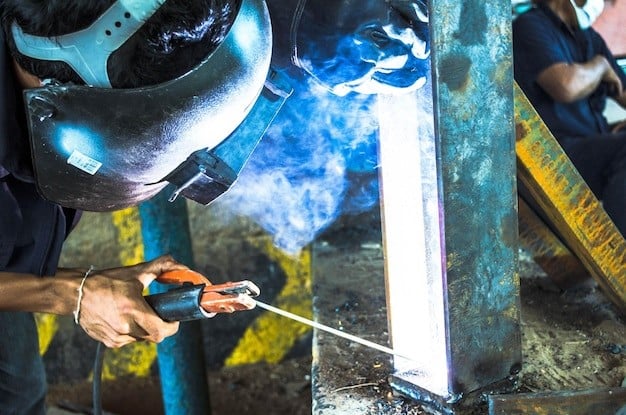
1. Strength for Heavy-Duty Jobs
Repairing civil structures like buildings, bridges, and ships requires high strength welds that arc welding provides.
2. Adaptable to Multiple Metals
From stainless steel to aluminum, arc welding works on a wide range of materials with ease.
3. Speed with Experience
With automated feeders set on specific metrics and power adjusted accordingly, sustained speed can be achieved.
4. Better for Vertical/Overhead Positioning
For overhead position work, using an electric arch remains advantageous since welded joints tend not to collapse easily.
5. Cleaner Finish with TIG and MIG
Gas-shielded techniques minimize spatter while producing neat beads.
Disadvantages of Arc Welding
- Requires more practice and training.
- Without proper gear, it can pose safety risks.
- Not ideal for delicate or thin items.
- Requires stable grid electricity or a generator.
Advantages of Gas Welding
1. Lower Cost of Entry
With a basic setup, you could start gas welding for under $500.
2. No Electricity Needed
Ideal for remote repairs or fieldwork.
3. More Than Welding
Cuts metal, heats bolts and brazes parts using the same torch.
4. Great for Thin Materials
Less likely to burn through sheet metal than other methods.
5. Simpler to Learn
Offer control over flame temperature; help beginners understand metal manipulation.
Disadvantages of Gas Welding
- Slower than ARC methods.
- Outdoor wind conditions can be problematic.
- Limited to lower-temperature applications.
- Cylinders can pose a fire/explosion risk.
When Should You Choose Arc Welding?
Select arc welding when:
- Strength and penetration are key factors.
- Structures or thick metals are being fabricated/handled.
- A reliable power supply exists in the workspace.
- Advanced skill-level welds and finishes are desired.
When Should You Choose Gas Welding?
Opt for gas welding if:
- You are working on intricate designs or artistic pieces.
- You work in locations without access to electrical power.
- Along with welding, you must also heat or cut the metal.
- You want to learn a new skill but are short on funds.
Which welding type is easier to learn?
Gas welding is the easiest type of welding to start with because it offers the most gentle introduction through flame control due to its visibility as well as a lack of fear-inducing electric sparks.
On the other hand, Arc welding provides greater employment prospects. If you hope to go professional, begin with basic gas welding before advancing to MIG or TIG.
Tools You’ll Need to Get Started
Arc Welding Starter Kit:
- Inverter or transformer welder
- Electrodes or spool gun
- Auto-darkening helmet
- Welding gloves and apron
- Angle grinder for cleanup.
Gas Welding Starter Kit:
- Oxygen and acetylene tanks
- Regulator valves
- Welding torch and tips
- Flameproof goggles
- Fire blanket or welding screen
Future Trends in Welding for 2025 and Beyond
Welding technology has advanced rapidly; here’s what emerging tech is changing:
AI-powered robotics: Robots now analyze and adjust real-time welds.
Augmented reality helmets: Enables novices to view simulated practice welding overlays.
Eco gas solutions: more manufacturers are adopting policies that reduce harmful gases used as shielding during arc welding.
Portable battery arc welders: field jobs would benefit from battery-operated machines.
Smart wearables: like safety gloves are capable of vibrating to warn users if they approach dangerous areas.
The goals of these advancements are enhanced intelligence, increased safety and reduced barriers to entry – all while expanding access to modern technologies in both industrial contexts and educational settings.
FAQs
Is arc welding suitable for aluminum applications?
Yes, but you will need either a TIG welder or a spool gun for MIG.
Does gas welding need electricity?
Neither requires electric power; it operates using gas and oxygen.
Which one is better for the environment?
Gas welding doesn’t draw on electrical power while arc welding uses eco gases now using at least some greener energy sources. TIG seems to be more efficient overall.
What is the safest method of Welding?
Both methods have their own unique risks. With more electrical hazards, arc welding poses a greater risk than gas welding which presents fire dangers.
Which one earns more professionally?
Professionally, an expert at using an arc welder—MIG and TIG specialists in particular—will make more because they are in greater industrial demand.
Conclusion: Which Is Right for You?
Everyone’s situation is different so there will be no best option. Considered factors include your objectives, region, and material class.
If entering the industry, consider pursuing a training program in arc welding, working with thick metals, or mastering advanced techniques.
Gas welding is more suitable for mobile applications or less complicated entry points.
Any specific direction you take, entering the world of welding is deeply satisfying, as it encompasses creativity and power in tremendous amounts.