Aluminum is a universal material widely used in various industries due to its weightless and corrosion-resistant properties. However, cutting aluminum efficiently and precisely can be challenging. Traditional methods often need more speed and accuracy. This is where a plasma cutter comes into play, providing a powerful solution to the problem.
Plasma cutters utilize ionized gas to slice through aluminum with precision and speed. This article explores whether plasma cutters can effectively cut aluminum, delving into the factors influencing the process, benefits, challenges, and solutions to ensure high-quality cuts.
Factors to Consider When Cutting Aluminum
Thickness of Aluminum
The thickness of the material is a primary consideration when cutting aluminum with a plasma cutter. Different thicknesses require specific settings and techniques to achieve optimal results.
- Thin Aluminum (up to 1/4 inch): Thin aluminum sheets are easier to cut and require lower power settings. This reduces the risk of warping and ensures clean, precise cuts. Using a fine-cut consumable for thin materials helps achieve a narrow kerf and minimal dross.
- Medium Thickness (1/4 inch to 1/2 inch): Power settings and cutting speed adjustments are necessary for medium-thickness aluminum. Maintaining the right balance is crucial to avoid excessive heat, leading to warping and a rougher edge finish.
- Thick Aluminum (over 1/2 inch): Cutting thick aluminum requires a powerful plasma cutter with a higher amperage. Slow-cutting speeds are recommended to ensure full penetration and to produce a clean-cut edge. Preheating the aluminum can help achieve better results with very thick materials.
Plasma Cutter Type and Power Settings
The type of plasma cutter and its power settings are crucial factors that influence the quality and efficiency of the cutting process.
- Inverter-based Plasma Cutters: These are more efficient and provide a stable arc, making them ideal for cutting aluminum. They are also more portable and consume less power than transformer-based cutters.
- Transformer-based Plasma Cutters: These are typically more robust and durable, suitable for heavy-duty industrial applications. However, they are bulkier and consume more power than inverter-based cutters.
- CNC Plasma Cutters: These are integrated with computer numerical control (CNC) systems, allowing for automated, precise, and repeatable cuts. They are ideal for complex shapes and high-volume production.
- Power Settings: The power settings should be adjusted based on the thickness of aluminum. Lower amperage settings are sufficient for thinner materials, while higher amperage settings are necessary for thicker materials to ensure complete penetration and a clean cut.
Cutting Speed and Quality
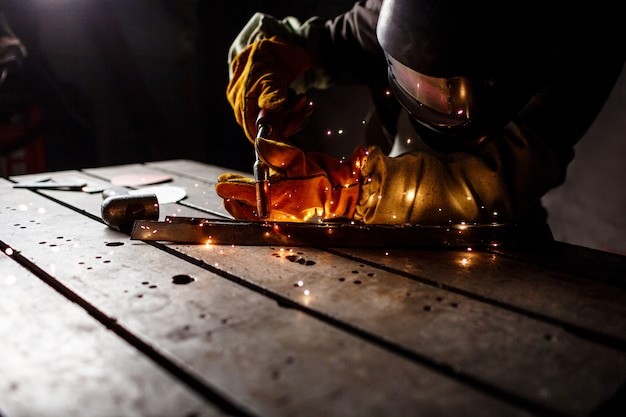
Cutting speed significantly affects the cut’s quality and the process’s overall efficiency.
- Optimal Speed: Determining the optimal cutting speed is crucial. Cutting too slowly can lead to excessive heat buildup, causing warping and a rough edge finish, while cutting too quickly can result in incomplete cuts and a jagged edge.
- Quality of Cut: High-quality cuts require speed, power, and technique. Ensuring the torch is held at the correct angle, and consistent speed will help produce a clean, smooth cut with minimal dross.
- Trial and Adjustment: It is often necessary to perform test cuts and make adjustments to find the perfect balance of speed and power settings for a specific thickness and type of aluminum.
Other Necessary Considerations
- Consumables: Regularly monitoring and replacing consumables such as nozzles and electrodes is essential for maintaining cutting quality and efficiency. Worn-out consumables can lead to poor cuts and increased operational costs.
- Cooling and Ventilation: Proper cooling and ventilation systems are crucial to manage the heat generated during cutting. This helps in preventing warping and prolongs the lifespan of the plasma cutter.
- Safety Measures: Always prioritize safety by wearing appropriate protective gear, ensuring proper grounding of the plasma cutter, and working in a well-ventilated area to avoid inhaling fumes.
Table explaining the plasma cutter types and their Efficiencies
Plasma Cutter Type | Aluminum Thickness Range | Power Source/Settings |
Inverter-based Plasma Cutters | Up to 1/2 inch | Efficient, stable arc, lower power consumption |
Transformer-based Plasma Cutters | Over 1/2 inch | Higher power consumption, robust |
CNC Plasma Cutters | Up to 1/2 inch | Automated settings, precise control |
Multi-process Plasma Cutters | Varies (based on function) | Adjustable settings for various functions |
Benefits of Plasma Cutting Aluminum
1. Efficiency
One of the primary benefits of using a plasma cutter for aluminum is its efficiency. Plasma cutting is faster than traditional cutting methods, such as sawing or mechanical cutting, making it a preferred choice in various industrial applications.
- Speed: Plasma cutters can slice through aluminum at high speeds, significantly reducing the time required for cutting tasks. This speed is particularly beneficial in production environments where time efficiency is crucial.
- Minimal Setup Time: Plasma cutters require minimal setup time compared to other cutting tools. Once the machine is set up, it can be used continuously with minimal adjustments, enhancing overall productivity.
- Reduced Downtime: With fewer moving parts and a simplified cutting process, plasma cutters experience less downtime due to maintenance or part replacements. This reliability ensures that projects stay on schedule.
2. Precision and Quality
Plasma cutters are known for their precision and high-quality cuts, which makes them ideal for projects that require accuracy and smooth edges.
- Clean Cuts: Plasma cutting produces clean and smooth edges on aluminum, reducing the need for secondary finishing processes. The precise control over the cutting arc allows for detailed and intricate designs.
- Minimal Distortion: Unlike other cutting methods that may cause warping or distortion, plasma cutting minimizes thermal distortion due to its focused heat application. This results in more accurate cuts and better-fitting parts.
- Narrow Kerf: The narrow kerf produced by plasma cutters means less material is wasted. This is especially important when working with costly materials such as aluminum, where conserving materials is a priority.
3. Cost-Effectiveness
Another significant advantage of plasma-cutting aluminum is its cost-effectiveness. This method offers businesses both short-term and long-term savings.
- Lower Material Costs: Since plasma cutting produces narrow kerf and clean cuts, less material is wasted. This efficiency in material usage translates to cost savings, especially when working with costly materials like aluminum.
- Reduced Labor Costs: Plasma cutting’s speed and efficiency reduce the labor required for cutting tasks. This can significantly save labor costs, especially in high-volume production settings.
- Lower Maintenance Costs: Plasma cutters generally have lower maintenance costs than other cutting tools. The durability and reliability of plasma cutting systems mean fewer replacements and repairs, leading to cost savings over time.
4. Versatility
Plasma cutters are versatile tools that can handle various thicknesses of aluminum and other materials, making them suitable for various applications.
- Thickness Range: Plasma cutters can efficiently cut aluminum across varying thicknesses, from thin sheets to thick plates. This versatility allows them to be used in different industries and for diverse projects.
- Multi-material Cutting: In addition to aluminum, plasma cutters can cut other metals such as steel, stainless steel, and copper. This multi-material capability makes plasma cutters valuable in workshops and manufacturing facilities.
5. Safety
Safety is crucial in any cutting process, and plasma cutters offer several advantages.
- Reduced Risk of Injury: Plasma cutting is a non-contact process, meaning the operator does not need to handle the material directly during cutting. This helps lower the chances of injuries related to manual cutting tools.
- Cleaner Work Environment: Plasma cutting produces fewer sparks and less debris than other methods. This results in a cleaner and safer work environment, lowering the risk of fire hazards and improving overall safety.
Challenges Faced During Plasma Cutting and Solutions
Heat and Warping Problem
One of the primary challenges when using plasma cutters on aluminum is managing heat input to prevent warping. Aluminum is a heat-sensitive material, and excessive heat can cause it to warp or distort, affecting the quality and precision of the cut.
Solution
It is crucial to manage the heat input carefully to prevent warping. Lower amperage settings and higher cutting speeds help minimize the heat generated during the cutting procedure. Additionally, intermittent cutting or pausing periodically can allow the material to cool down, reducing the risk of distortion.
Effective cooling methods, such as air or water cooling systems, can help manage the heat. These methods dissipate the heat away from the cutting area, keeping the aluminum at a stable temperature and preventing warping.
Dross Building Problem
Dross buildup is another common issue encountered when plasma cutting aluminum. Dross is the material left on the cut edge, which can impact the final product’s quality and formation.
Solution
To minimize dross formation, it is essential to optimize the cutting parameters. Adjusting the cutting speed, amperage, and torch height can significantly reduce dross accumulation. Using high-quality consumables designed specifically for aluminum can also improve cut quality and reduce dross.
Despite preventive measures, some dross may still form. Post-cut cleaning is necessary to remove any remaining dross and achieve a smooth edge finish. Tools such as scrapers, wire brushes, or grinding wheels can be used. Ensuring a clean-cut edge enhances the overall quality and appearance of the aluminum piece.
Consumables Replacement Problems
Consumables, such as nozzles and electrodes, are crucial in the plasma-cutting process. Monitoring and replacing consumables regularly is essential to maintain cutting efficiency and quality.
Solution
Keeping a close watch on the condition of consumables is vital. Worn-out or damaged consumables can lead to poor cut quality, increased dross, and higher operational costs. Regular inspection of nozzles, electrodes, and other consumable parts can help identify when replacements are needed.
Timely replacement of consumables ensures consistent cutting performance. Using high-quality consumables compatible with the plasma cutter and the cut material can extend the consumables’ lifespan and improve the cutting process’s overall efficiency.
Final Thoughts
Plasma cutters offer a reliable solution for cutting aluminum efficiently and precisely across various thicknesses. Operators can achieve clean cuts with minimal distortion and dross buildup by adjusting power settings and cutting speeds. Speed, cost-effectiveness, and safety benefits make plasma cutting a preferred method in industries requiring accurate metal fabrication. Despite challenges like heat management and consumable maintenance, proper techniques and equipment ensure high-quality results, supporting productivity and minimizing material waste in aluminum cutting processes.
FAQs
What Thickness of aluminum can plasma cutters handle?
Plasma cutters can handle a range of aluminum thicknesses. They are suitable for thin sheets up to thick plates, with adjustments in power settings and cutting speeds required for different thicknesses.
How do you prevent warping when cutting aluminum with a plasma cutter?
To prevent warping, it’s crucial to manage heat input. This can be done using lower amperage settings, higher cutting speeds, and cooling methods like air or water cooling systems.
What are the benefits of using plasma cutters for cutting aluminum?
Plasma cutters offer high cutting speeds, minimal setup time, and clean cuts with smooth edges, and cost-effectiveness due to reduced material and labor costs.
What are the main challenges when plasma cutting aluminum?
Challenges include managing heat to prevent distortion, minimizing dross buildup on cut edges, monitoring and replacing consumables like nozzles and electrodes, and ensuring proper safety measures are in place during operations.