Stick welding aluminum may seem like an impossible task to complete. But! It’s actually possible with the right techniques.
Let’s know more about stick welding aluminum. We can first start from the question: Does aluminum stick welding use AC or DC?
Aluminum Stick Welding AC or DC
Gaining an understanding of the power sources in aluminum stick welding.
The type of electrical current you use when welding aluminum with a stick welder is the determining factor in whether your weld is high quality and good or bad and of poor quality.
AC and DC both have their advantages and disadvantages when welding aluminum, and understanding these differences is where you need to begin in deciding on the best method for your use.
AC Welding:
Alternating current switches polarity constantly, which has a “cleaning” effect on the weld. This cleaning effect is particularly beneficial for aluminum because aluminum forms a hard oxide layer on its surface.
The rapid switching of polarity essentially “sandblasts” away the oxide, producing a cleaner weld pool. AC welding will occasionally produce less penetration and an unstable arc, however, compared to DC.
DC Welding:
Direct current flows in one constant direction, forming a more consistent arc and better penetration. This can be beneficial for welding thicker sections of aluminum because it allows the weld to flow smoothly into the base metal.
The downside? DC does not deposit the same oxide-cleaning advantage that AC does, so you might need to spend a little more time on surface cleaning.
Technical Differences and Impact on Weld Features
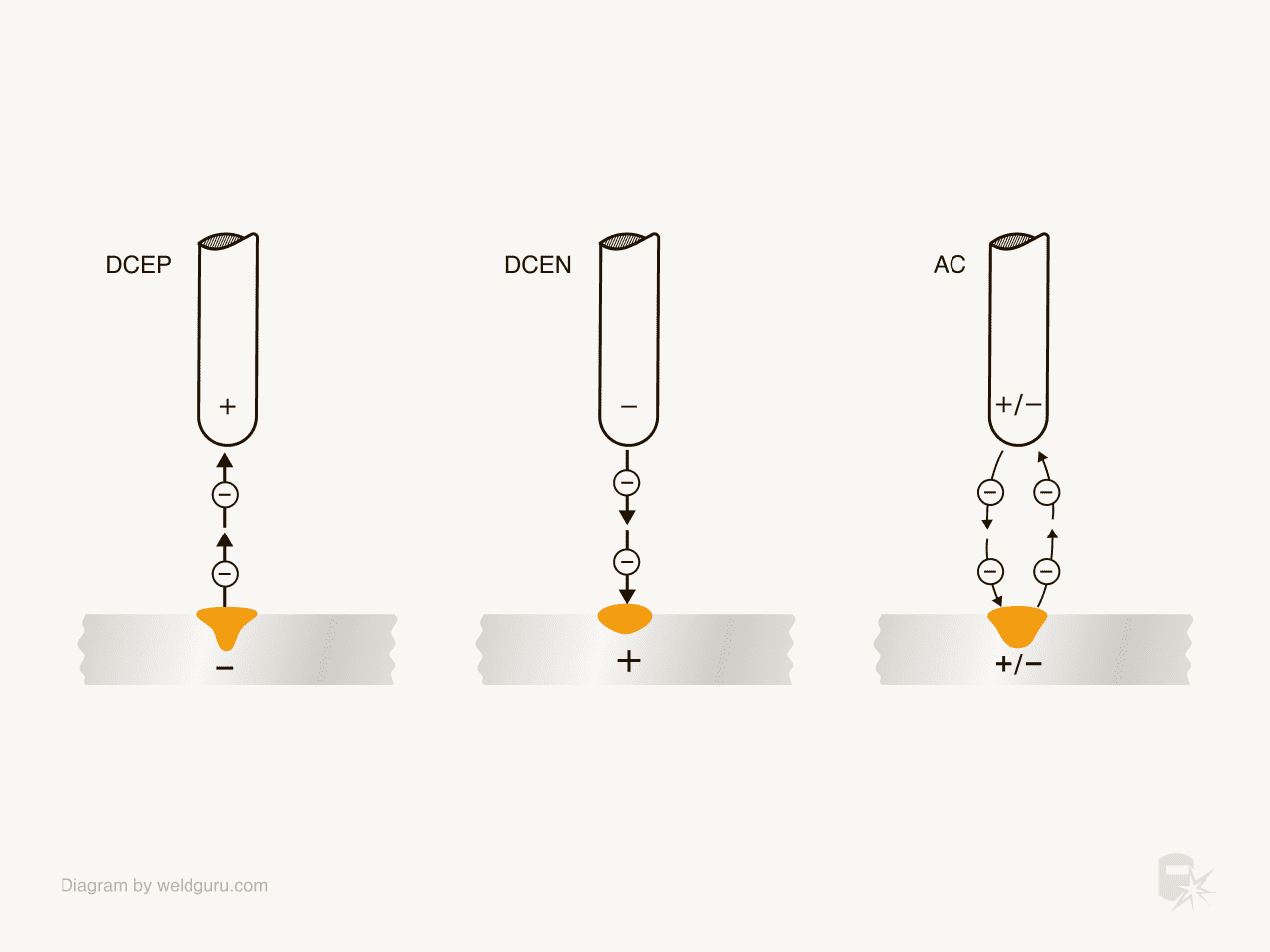
The choice between AC and DC isn’t arbitrary—it will impact your weld’s appearance and structural quality immediately:
AC Benefits:
- Oxide Removal: The back-and-forth polarity reversal provides a natural cleaning action, essential for removing aluminum’s stubborn oxide layer.
- Arc Stability on Aluminum: On certain aluminum alloys and sheet stock, AC can provide a more forgiving arc that will assist in making it simpler to produce a weld pool.
DC Benefits:
- Higher Penetration: DC provides increased penetration in the base metal from a uniform supply of current, ideal for heavier aluminum.
- Heat Input Control: Stable arc in DC welding provides easy control over the heat input, reducing the danger of burn-through.
Choosing AC or DC for Aluminum Stick Welding
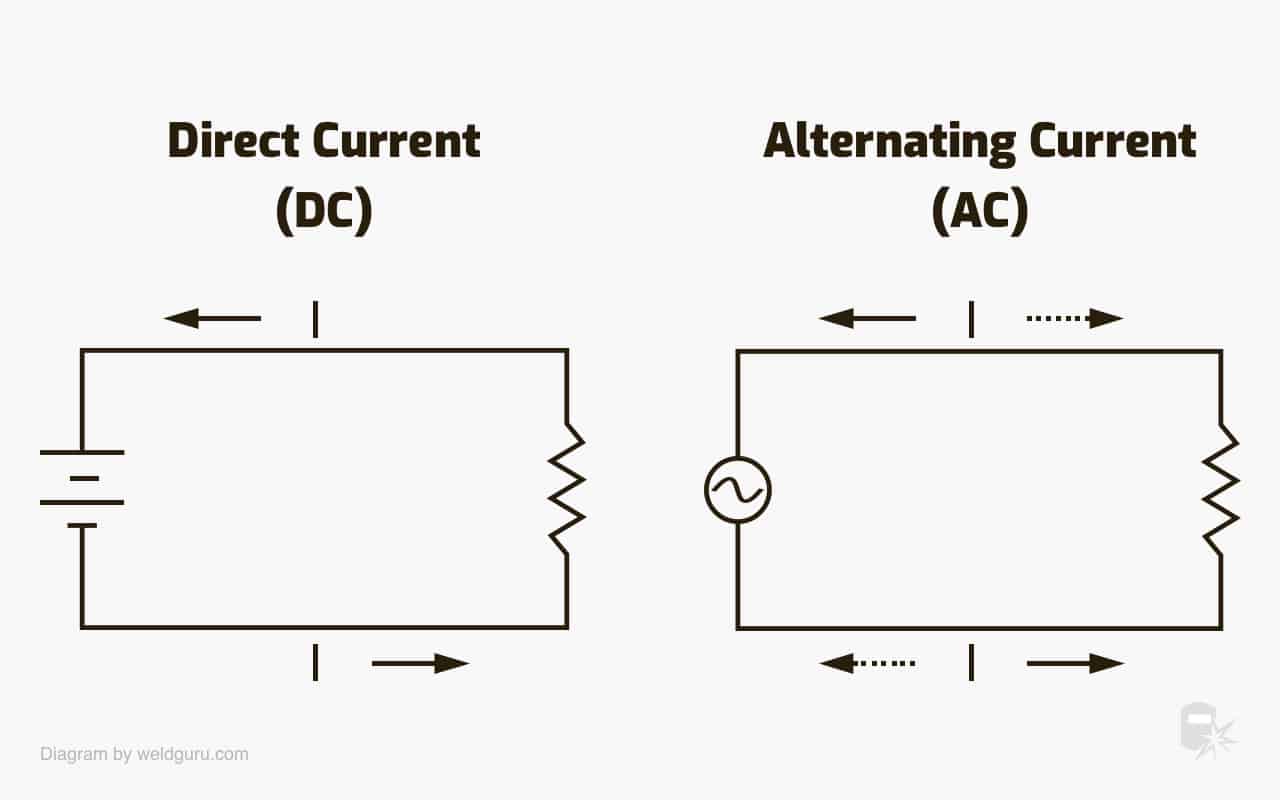
When deciding on the use of AC or DC for stick welding aluminum, bear the following facts in mind:
- Material Thickness: In the case of light-gauge aluminum, the cleaning benefit of AC could be greater than that of DC penetration. In heavier sections, however, the deeper penetration of DC could be desirable.
- Electrode Type: Such electrodes employed on special aluminum alloys, such as 4043 compositions, are often employed with AC welding.
- Welding Environment: Outdoors repairs that can have shielding gases needed for MIG or TIG scattered by wind might favor stick welding with AC or DC according to circumstances.
Lastly, make your choice between AC and DC according to the specific requirements of your project by balancing the need for oxide cleaning with the need for penetration.
Key Challenges in Stick Welding Aluminum
Welding aluminum with a stick welder is inherently challenging due to the unique physical properties of the metal. Below are some of the most significant issues you’ll need to overcome:
High Thermal Conductivity and Low Melting Point
The high thermal conductivity of aluminum makes the heat move quickly away from the weld. While this is good in most applications, it makes welding more difficult because you need to add more heat to keep the weld pool melted long enough to form a solid joint.
At the same time, aluminum’s low melting point increases burn-through danger if too much heat is applied.
Maintaining a Short Arc
Because the weld pool freezes rapidly, you must maintain a short arc length and travel quickly along the joint.
A short arc is necessary to prevent the electrode from “freezing” in the weld pool—a common problem with aluminum. This quick travel, however, requires some practice and control and can be challenging for new users.
Common Welding Defects
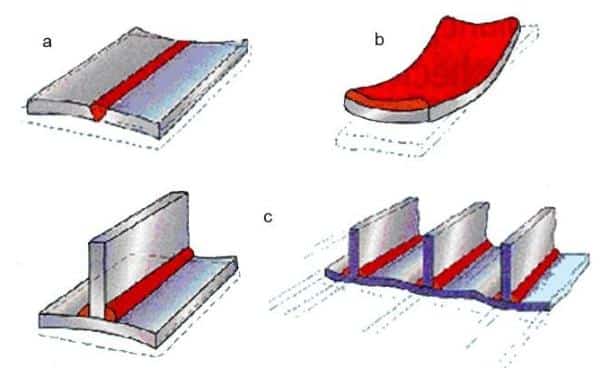
When stick welding aluminum, you might encounter several defects:
- Warping: Excessive heat input can cause the thin metal to warp.
- Burn-Through: Excessive heat, or movement too slow, can melt the metal completely in certain spots.
- Cracking: Temperature differences in the cooling rate of the weld and base metal can cause hot or cold cracking.
- Spatter and Rough Appearance: The characteristics of aluminum and the flux of the electrode can cause increased spatter and a less smooth weld bead.
Stick Welding Aluminum: Pros & Cons
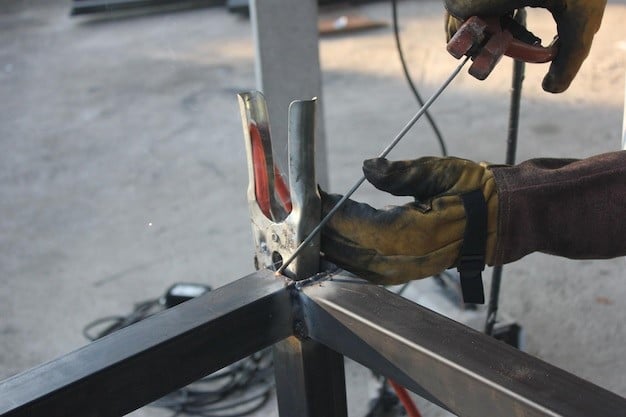
Advantages
1. Portability and Setup:
Stick welders are easier and more portable in the field compared to MIG or TIG equipment. Stick welders lack external shielding gas, which means they are ideal for open-air repairs.
2. Cost-Efficiency:
Stick welders are less costly compared to using MIG or TIG processes.
The overall equipment costs are lower for stick welding, and the process can be more economical in emergency repairs or where there is no strong focus on high-quality finishes.
3. Simplicity in Equipment:
Stick welding requires fewer consumables. As there is no need for gas tanks, welding in distant places or windy locations becomes easier.
Disadvantages
1. Aesthetic Limitations:
Welds made by the stick welding process have a rougher look with higher slag and spatter and are not suitable for use where the weld appearance is important.
2. Greater Sensitivity to Electrode Storage:
Aluminum stick electrodes are moisture-sensitive. They must be stored in dry conditions; otherwise, their performance is decreased very quickly.
3. Less Heat Control:
Stick welding has less heat control than MIG and TIG processes, so warping, burn-through, and inconsistent welds are more probable—especially on thinner stock.
Aluminum Stick Welding Practical Guidelines
If you do end up proceeding and trying stick welding aluminum, it is worth taking the proper procedures, as they can actually make a big difference in your result.
Equipment and Settings
1. Variable Amperage Output:
Choose a stick welder with a variable amperage. Aluminum being a highly conductive metal and therefore requiring more heat, having the provision to adjust the amperage is essential.
2. Electrode Selection:
Use specialty aluminum electrodes, such as the 4043 type, designed specifically for stick welding aluminum. The diameter of the electrode and the recommended amperage should be appropriate for the thickness of the aluminum you are working with.
For example, a 3/32-inch electrode can use 50–80 amps, whereas a thicker 5/32-inch electrode can use 100–160 amps.
Pre-Weld Preparation
- Surface Cleaning:
Aluminum creates an oxide coating that must be removed before it can be welded. Peel off the oxide with a specialized stainless steel wire brush, mild sanding, or chemical cleaning to drive out the oxide without making it sink deeper into the metal. Always use tools designed to be used on aluminum to avoid contamination.
- Proper Electrode Storage:
Store aluminum electrodes in a dry, controlled environment. Humidity can ruin the flux coating immediately, making the electrodes useless and affecting weld quality.
Technique and Execution
- Keep a Short Arc:
Due to the fast solidification of aluminum’s weld pool, it’s important to have a short arc and rapidly move the electrode along the joint. This prevents burn-through from occurring and results in a more stable weld pool.
- Proper Electrode Angle and Movement:
The electrode should be held at a slight angle—usually 10 to 20 degrees—in the direction of travel. This helps in proper arc control and transfer of the molten metal into the weld pool.
- Start and End the Weld Carefully:
When beginning and ending your weld, avoid making craters or excessive reinforcement. A couple of seconds of “backing up” on the end of a weld will sometimes fill in any craters that develop, reducing the likelihood of cracks later.
Tips and Troubleshooting for Maximizing Weld Quality
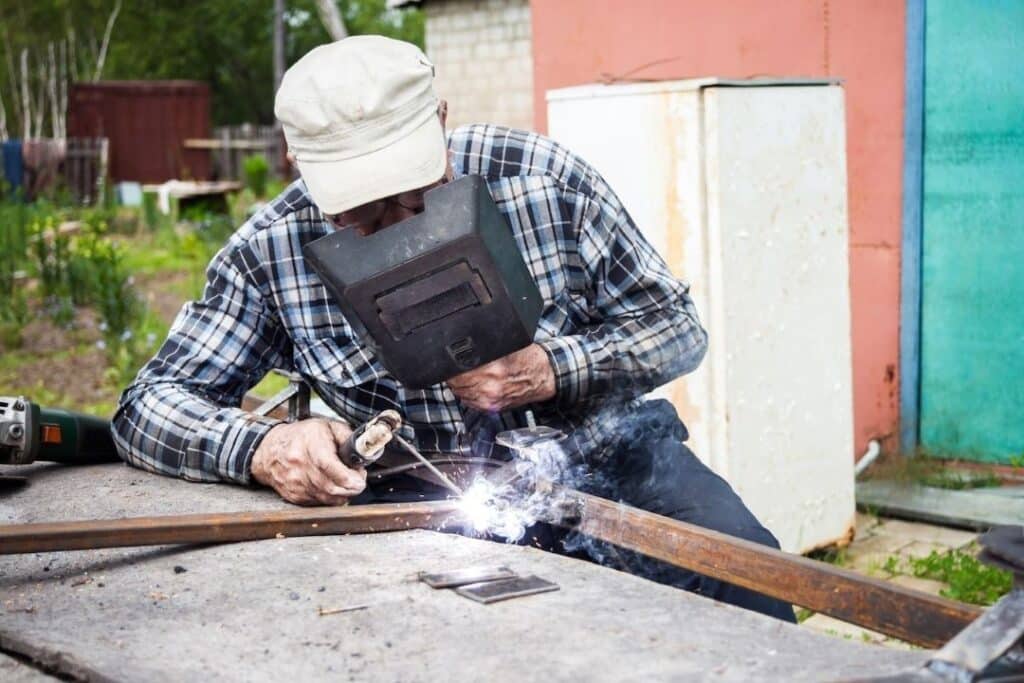
Even with the best preparation and techniques, stick welding aluminum can be problematic. Here are some additional tips and troubleshooting ideas:
Minimizing Spatter and Improving Appearance
Smooth Arc Movement:
Avoid lingering too long at any one point along the joint. A steady travel rate minimizes spatter and creates a cleaner weld bead.
Proper Amperage Settings:
Start with the suggested amperage for your electrode size and adjust as needed. Too high a setting will create too much spatter, and too low will create poor penetration.
Heat Input Control
Quick Tack Welding:
When starting your weld, use quick tack welds to secure the pieces. This prevents warping by minimizing continuous heat exposure to large surfaces.
Watching Weld Pool Size:
Keep an eye on your weld pool. If it’s too large or too sloppy, control your travel speed or amperage to achieve controlled penetration and prevent burn-through.
Post-Weld Cleanup
Removing Slag:
The flux coating slag may be hard. Remove it cautiously with chipping and brushing without hurting the weld.
Grinding and Finishing:
For looks, grind and blend the weld bead lightly after cleaning up. This process has to be done carefully not to over-grind and weaken the joint.
Adjusting for Different Aluminum Thicknesses
Test Welds:
For thinner aluminum, it’s generally a good idea to make test welds on scrap. This process enables you to adjust your settings and hone your technique prior to working on the actual piece.
Fine-Tuning Settings:
Thicker aluminum may need to have more amperage and lower travel speeds so that there is adequate penetration. You might need to fine-tune your settings based on the material and thickness being worked on.
Comparison with MIG and TIG Welding for Aluminum
While stick welding aluminum is a process that can be effective in certain circumstances, it is useful to compare it with other methods such as MIG and TIG welding.
MIG Welding Aluminum
Advantages:
A MIG welding machine creates cleaner, smoother welds with better visual appeal. It also enjoys better heat control, which is critical with thinner gauge materials.
However, it requires a spool gun along with external shielding gas, which can make field repairs more complicated.
Disadvantages:
MIG welding machines are larger, less portable, and more vulnerable to windy outdoor conditions because of the need for shielding gas.
TIG Welding Aluminum
Advantages:
TIG welding is also famous for its high-quality, good-looking welds with excellent control over heat input. It’s ideal for thin aluminum and precision work.
Disadvantages:
TIG welding is slower and more skill-dependent, so it’s less appropriate for quick repairs or fieldwork. The equipment is also typically more expensive and less forgiving for beginners.
When Stick Welding is More Practical?
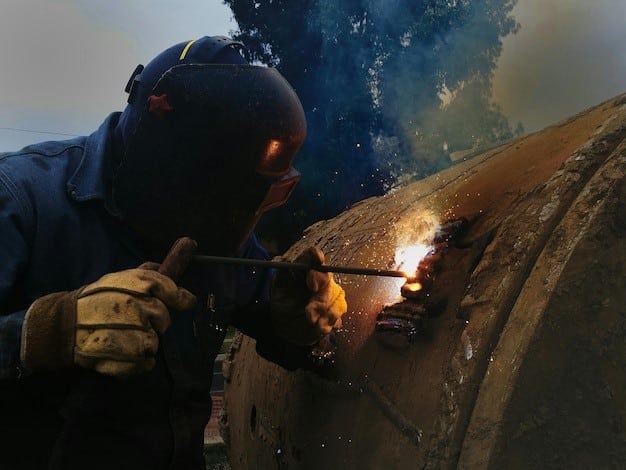
Stick welding aluminum, despite all its challenges, does hold some advantages in certain situations:
Outdoor Repairs:
In field situations where it is inconvenient to transport a gas tank or where wind might disrupt shielding gases, stick welding is a portable, simple alternative.
Cost-Effective Repairs:
For the purpose of making quick repairs where appearance is secondary to function, stick welding can be a less expensive alternative.
Want more aluminum welding tips?
Read these articles to get inspiration:
Aluminum Welding: A Comprehensive Guide,
TIG Welding Aluminum Complete Guide,
Mastering MIG Welding Aluminum,
Choosing the Right Aluminum Welding Wire
FAQ
What type of electrode is recommended for stick welding aluminum?
Stick welding aluminum is typically performed with aluminum electrodes such as the 4043 type. These electrodes work best with direct current electrode positive (DCEP) polarity and require specific amperage settings based on their diameter. Always consult the electrode manufacturer’s recommendations for optimal settings.
What are the most common challenges in stick welding aluminum?
Some of the common challenges are:
- Maintaining a short arc to preclude freezing of the electrode in the weld pool.
- Regulating heat input to avoid burn-through or warping.
- Dealing with more spatter and an ugly, textured weld bead.
- Dealing with the storage of moisture-sensitive aluminum electrodes.
How do I prepare aluminum for stick welding?
Proper surface preparation is important. Remove the aluminum oxide coating with a stainless steel wire brush that is meant for this purpose, light sanding, or chemical cleaning.
Use your tools only for aluminum to avoid contamination. Store the electrodes in a dry environment too.
How does stick welding aluminum differ from MIG and TIG welding?
TIG and MIG welding are more likely to produce neater, better-looking welds with more controlled heat input, and are ideally used for high-precision work as well as thin materials.
Stick welding, however, enjoys the luxury of portability, setup, and affordability, and thus is a handy choice in the case of field repair and outdoor use where MIG or TIG welding may be less convenient.
What safety precautions should I use when stick welding aluminum?
As with all welding, safety first. Wear appropriate personal protective equipment (PPE) at all times, including a welding helmet with a proper filter shade, gloves, and protective clothing.
Use good ventilation since aluminum welding will produce poisonous fumes and ozone. Properly store electrodes and maintain equipment on a regular basis.