Welding is a critical process in manufacturing, but common welding mistakes can lead to significant product failures, affecting quality and safety. These errors often stem from inadequate surface preparation, worn-out equipment, or improper welding techniques. Such issues can compromise the integrity of the weld, leading to weak joints, defects, and potential hazards for end-users.
Adhering to best practices in welding, including thorough inspection and testing, proper equipment maintenance, and sourcing welded products from reliable suppliers, is essential to preventing these problems. By addressing these key areas, businesses can ensure the production of high-quality welded products, minimize risks, and maintain customer trust.
Common Welding Mistakes
Common welding mistakes often arise from inadequate surface preparation, leading to weak welds. Using worn or inappropriate equipment can result in defects that compromise product quality.
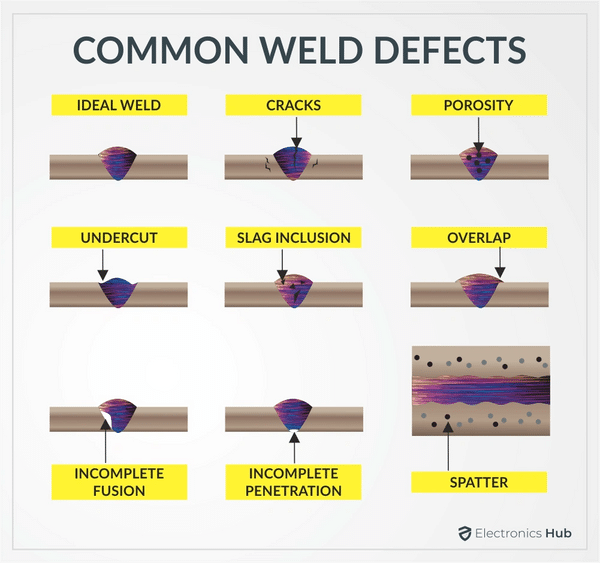
Inadequate Surface Preparation
Inadequate surface preparation is a common issue that can significantly weaken welds. When surfaces are not properly cleaned or prepared, contaminants like rust, oil, and dirt can remain on the metal. These contaminants interfere with the welding process, preventing proper fusion between the materials. As a result, the weld may not fully penetrate or bond with the base metal, leading to weak joints. This can cause the weld to crack or fail under stress, compromising the structural integrity of the final product.
Proper surface preparation, including thorough cleaning and removal of all contaminants, is essential to ensure a strong, durable weld. By taking these steps, manufacturers can avoid defects and produce high-quality welded products that meet safety and performance standards.
Poor Welding Outcomes
Poor welding outcomes are often the result of improper techniques or incorrect settings during the welding process. When the welding parameters, such as voltage, current, or travel speed, are not correctly adjusted, defects like porosity, incomplete penetration, or excessive spatter can lead to defects.
These defects compromise the strength and appearance of the weld, making it prone to failure under load or stress. Poor welding practices, such as inadequate joint alignment or inconsistent welding speed, can create weak points in the weld. These weaknesses can result in cracks, fractures, or other structural issues that may not be immediately visible but can cause significant problems over time.
Cracks
Cracks are among the most severe weld defects. They occur when there is excessive stress on the weld, either during or after welding. Factors such as rapid cooling, improper welding techniques, or using the wrong filler material can cause cracks. These defects weaken the weld and can lead to failure under load. Cracks may appear on the surface or within the weld metal and are difficult to detect without proper inspection.
Porosity
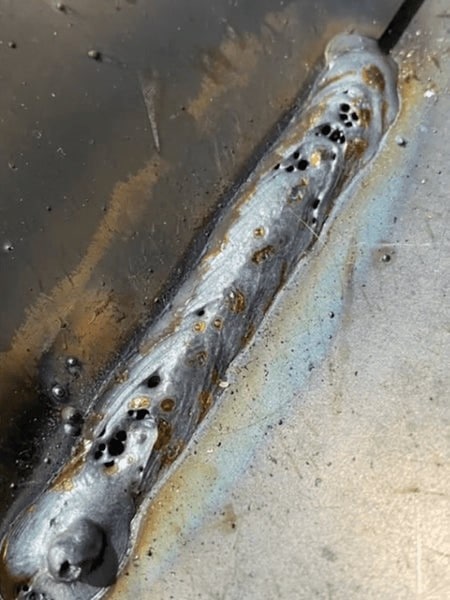
Porosity refers to tiny holes or cavities within the weld metal. The entrapment of gases causes these during solidification. Common sources of porosity include contamination on the welding surface, improper shielding gas, or moisture in the tungsten welding electrodes. Porosity reduces the strength of the weld by creating voids that can lead to cracks or fractures. Ensuring clean surfaces and proper gas coverage is important to minimize porosity.
Undercut
Undercut is a groove that forms at the weld toe, where the base metal is melted away, leaving a weak point in the weld. This defect occurs when the welding speed is too high, or the welding angle is incorrect. Undercutting can compromise the structural integrity of the weld, as it reduces the thickness of the base metal at the weld joint. Careful control of welding parameters can help prevent undercut.
Slag Inclusion
Slag inclusion happens when non-metallic materials, such as flux residues, become trapped in the weld metal. This defect is common in shielded metal arc welding (SMAW) and flux-cored arc welding (FCAW). Slag inclusions weaken the weld by creating areas of non-metallic material that can cause cracking or failure. Proper slag removal between weld passes and the correct welding technique can reduce the risk of slag inclusion.
Overlap
Overlap occurs when the weld metal rolls over the base metal without properly fusing it. This defect is typically caused by low heat input or an incorrect welding angle. Overlap can create weak points in the weld, as the lack of fusion prevents the weld from fully penetrating the base metal. Adjusting the heat input and angle can help ensure proper fusion and prevent overlap.
Incomplete Fusion
Incomplete fusion occurs when the weld metal does not fully bond with the base metal or previous weld passes. This defect can be caused by insufficient heat input, improper welding technique, or incorrect joint preparation. Incomplete fusion results in weak joints that are prone to failure under stress.
Incomplete Penetration
Incomplete penetration happens when the weld does not fully penetrate the thickness of the base metal. This defect is often due to insufficient heat input or improper joint design. Incomplete penetration creates weak points in the weld, which can compromise the overall strength of the welded structure.
Spatter
Spatter refers to small droplets of molten metal expelled from the weld and landing on the surrounding metal surfaces. While the spatter does not typically weaken the weld, it can create an uneven surface and require additional cleaning or grinding. Incorrect welding parameters, such as excessive current or voltage, often cause a spatter.
Use of Inadequate Equipment
The use of inadequate or worn equipment can significantly impact the quality of welds, leading to defects in the final product. When welding equipment is outdated or poorly maintained, it may not deliver consistent heat, proper arc stability, or precise control, which are critical for producing strong welds.
Issues like irregular current flow, faulty wire feeding, or inconsistent shielding gas coverage can result in weak welds, porosity, or other defects compromising the product’s structural integrity. Regular maintenance, timely replacement of worn components, and reliable, up-to-date equipment are essential to produce high-quality welded products.
Common Welding Mistakes and their Solutions
Welding Defects | Causes | Potential Solutions |
Cracks | Excessive stress, rapid cooling, wrong filler material | Proper cooling, correct filler material, careful stress management |
Porosity | Contaminants, improper shielding gas, moisture in electrode | Clean surfaces, proper gas coverage, dry electrode |
Undercut | High welding speed, incorrect welding angle | Control welding speed and angle |
Slag Inclusion | Non-metallic materials trapped in weld metal, improper slag removal | Remove slag between weld passes, use correct technique |
Overlap | Low heat input, incorrect welding angle | Adjust heat input and welding angle |
Incomplete Fusion | Insufficient heat, improper technique, poor joint preparation | Ensure proper heat input and joint preparation |
Incomplete Penetration | Insufficient heat, improper joint design | Adjust welding parameters and joint design |
Spatter | Incorrect welding parameters, excessive current or voltage | Properly adjust current and voltage settings |
Welding Mistakes on Product Quality
Welding mistakes can severely impact the overall quality of the final product, leading to significant risks for both end-users and welder distributors.
Potential Risks to End-Users
When welding defects such as cracks, porosity, or incomplete fusion occur, they compromise the product’s structural integrity. This can result in product failures, accidents, or even safety hazards for end-users, especially in critical applications like construction, automotive, or industrial machinery. Such failures can lead to injury, financial loss, and a loss of trust in the product’s reliability.
Consequences for Distributors
For distributors, welding mistakes can lead to returns, warranty claims, and damage to their reputation. Defective products increase the cost of handling and replacement, reducing overall profitability. Additionally, consistent quality issues can result in lost business opportunities, as customers may seek more reliable suppliers. Ensuring high-quality welds is crucial for maintaining customer satisfaction and protecting the distributor’s market position.
Ensuring High-Quality Welded Products
Implementing stringent inspection and testing processes and collaborating with reliable welder suppliers are essential to guaranteeing the quality and durability of welded products.
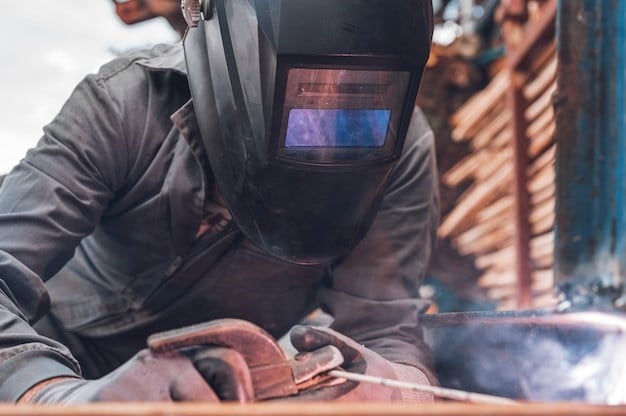
Inspection and Testing
Inspection and testing are crucial to ensuring that welds meet the required standards. Techniques like visual inspection, ultrasonic testing, and X-ray examination can identify defects like cracks, porosity, or incomplete fusion. By thoroughly inspecting welds, manufacturers can detect and address potential issues before the product reaches the end-user, thereby reducing the risk of failure and enhancing product reliability.
Working with Reliable Welder Suppliers
Partnering with reliable welder suppliers is another key factor in ensuring high-quality welds. Reputable suppliers provide well-maintained, up-to-date equipment and offer support and training to ensure proper use. By working with trusted suppliers, manufacturers can minimize the risk of defects caused by inadequate equipment or poor welding practices, ultimately delivering superior products to the market.
Spark Success Together with YesWelder
YesWelder stands out as a reliable supplier of high-quality welding equipment. It is known for its strong brand foundation and massive fan base. The company offers a wide range of welding products that cater to professionals and hobbyists, ensuring that its equipment meets the highest quality and performance standards.
YesWelder provides top-notch products and extends comprehensive support to its distributors. From marketing assistance to technical training, they are committed to helping their partners succeed in the competitive welding industry.
By working with YesWelder, distributors can leverage their strong reputation and customer loyalty, boost their business, and ensure a steady supply of reliable welding equipment. YesWelder’s commitment to excellence makes it a valuable partner in achieving success.
Final Thoughts
Ensuring high-quality welding requires attention to detail, proper equipment, and adherence to best practices. Common welding mistakes can lead to significant defects that compromise the strength and reliability of the final product. Manufacturers can prevent defects and deliver superior products by understanding these potential issues and implementing robust inspection and testing processes. Partnering with reliable suppliers like YesWelder further enhances the quality of welded products, offering distributors the tools and support needed to succeed in the market.
FAQs
What are the most common welding defects, and how can they be prevented?
Common defects include cracks, porosity, and undercutting. Prevention involves proper surface preparation, appropriate equipment, and correct welding techniques.
How do welding defects affect the quality of a product?
Welding defects weaken joints and can lead to product failures, compromising safety and reliability.
What steps can be taken to ensure high-quality welds?
Ensure thorough inspection, maintain equipment, and partner with reliable suppliers for quality assurance.
How important is equipment maintenance in preventing welding defects?
Regular equipment maintenance is vital to prevent inconsistent welds and defects, ensuring reliable product quality.