Welders often face the challenge of choosing between flux-core welding and stick welding, both of which have advantages and drawbacks. This decision becomes crucial depending on the specific requirements of a project, such as material type, work environment, and desired weld quality. Flux-core welding offers faster welding speeds and better performance in outdoor conditions, while stick welding is known for its versatility and better heat control.
Understanding the differences between these methods helps welders select the most suitable technique for their conditions, ensuring optimal results in various welding applications.
Differences Between Flux-Core Welding and Stick Welding
Several key factors differentiate these two methods when comparing flux-core and stick welding. Below is a table summarizing the main differences:
Factor | Flux-Core Welding | Stick Welding |
Welding Speed | Faster | Slower |
Portability | Less portable due to equipment needs | Highly portable |
Material Thickness | Better for thicker materials | Can be used on a variety of thicknesses |
Outdoor Performance | Excellent in windy conditions | Good, but wind can affect the arc |
Slag Production | Produces significant slag | Produces slag, but typically less |
Smoke Production | High amount of smoke | Moderate smoke |
Heat Control | Less control, higher risk of burn-through | Better heat control |
Cost of Materials | More expensive wire | Less expensive electrodes |
Ease of Use | Easier for beginners | Requires more skill |
Weld Quality | Dependent on skill, generally good | Consistently good with proper technique |
Welding Process and Equipment
Welding Processes
Flux-core welding (FCAW) and stick welding (SMAW) differ significantly in their processes. Flux-core welding uses a continuously fed wire that serves as both the electrode and the filler material. The wire contains flux, which creates a shielding gas when heated. This process is often semi-automatic and is well-suited for faster welding tasks. In contrast, stick welding uses a consumable electrode coated with flux. The electrode is manually fed, and as it melts, it creates a weld pool while the flux coating forms a protective gas shield.
Equipment
The equipment used in these welding processes also varies, but the first thing is to get a machine from a reliable welding equipment supplier. A wire feed system and a constant voltage power source are essential for flux-core welding. This setup can be more complex, requiring additional equipment like rollers and spool guns to handle the wire. On the other hand, stick welding equipment is more straightforward, consisting mainly of a power source and electrode holder. This simplicity makes a stick welder more portable and easier to set up, especially in remote or challenging environments.
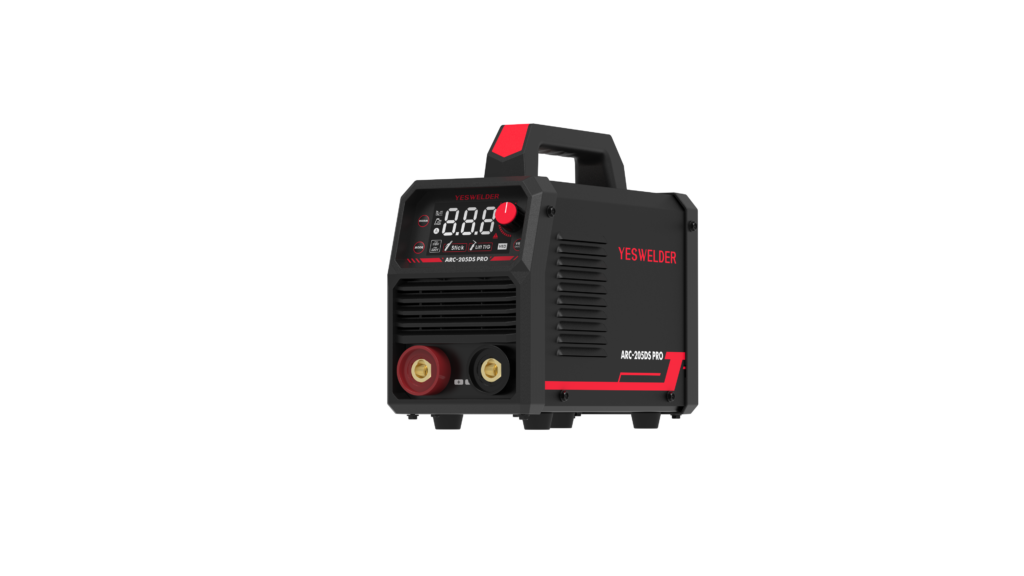
Shielding Mechanism
Flux-Core Welding Shielding Mechanism
Flux-core welding relies on a unique internal shielding mechanism. The wire used in this process is filled with flux material that, when heated, generates a shielding gas around the weld pool. This gas protects the molten metal from contaminants in the air, such as oxygen and nitrogen, which can lead to weld defects. The self-shielding nature of flux-core welding makes it ideal for outdoor work, where wind might otherwise disperse externally supplied shielding gases. This method ensures that the weld remains strong and free from impurities even in less controlled environments.
Stick Welding Shielding Mechanism
In stick welding, the shielding mechanism is also provided by flux, but in a different form. The electrode used in stick welding is coated with a flux material. As the electrode melts, the flux vaporizes, creating a protecting gas shield around the weld area. Additionally, the flux forms a slag layer over the weld, further protecting it as it cools. This dual protection is crucial for maintaining weld integrity, especially in environments where air quality cannot be controlled.
Application Suitability
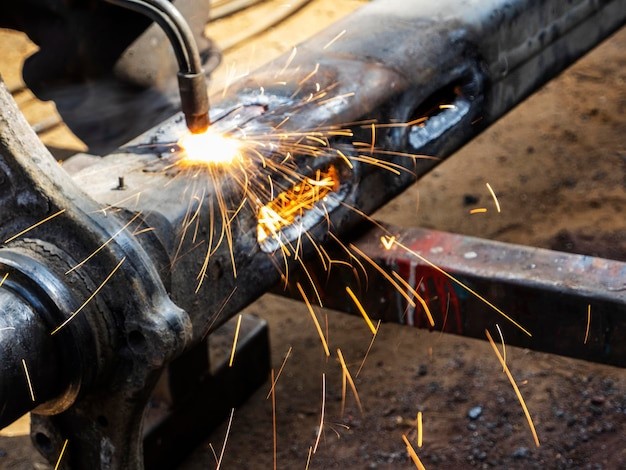
Flux-Core Welding Application Suitability
Flux-core welding is well-suited for applications that require high deposition rates and the ability to work in outdoor environments. It is commonly used in construction, heavy equipment repair, and shipbuilding, where the need for speed and strong welds on thick materials is critical. This method performs well in windy or less controlled environments because of its self-shielding capabilities, making it ideal for fieldwork. Flux-core welding is also effective for joining thicker materials, where deeper penetration is necessary for a strong bond.
Stick Welding Application Suitability
Stick welding is adaptable and can be used across various industries, including maintenance, repair, and fabrication. Its adaptability to different material types and thicknesses makes it a go-to method for many welders. Stick welding excels when portability and accessibility are essential, such as in remote locations or confined spaces. It is also suitable for working on metals that are not perfectly clean, as the flux helps to manage impurities. This method is often preferred for projects that require strong, durable welds, especially in structural work and pipeline construction.
Weld Quality
Flux-Core Welding Quality
Flux-core welding generally produces strong, durable welds with good penetration, making it ideal for heavy-duty applications. The weld quality depends heavily on the welder’s skill, as proper technique is required to manage the high heat and fast deposition rates. While flux-core welding can result in a solid weld, it often requires significant cleanup due to slag formation. Additionally, the high levels of smoke and spatter can obscure the welder’s view, making precision more challenging. Despite these challenges, flux-core welding delivers reliable results, especially when speed and strength are paramount.
Stick Welding Quality
Stick welding is known for producing consistently strong and high-quality welds, especially when performed by an experienced welder. This method allows for better control over heat, which helps to avoid burn-through, particularly on thinner materials. Stick welding also excels in creating welds resistant to stress and impact, making it suitable for structural work. The slag produced during the process provides an additional layer of protection, ensuring a cleaner weld as it cools. While it may be slower than flux-core welding, the precision and reliability of stick welding make it a favored choice for projects requiring high-quality results.
Welding Costs
Flux-Core Welding Costs
Flux-core welding tends to be more expensive due to the higher cost of the consumables involved. The wire used in flux-core welding is generally more costly than the electrodes used in stick welding. Additionally, the equipment for flux-core welding, including wire feeders and more sophisticated power sources, adds to the overall expense. While the process can be faster, leading to potential labor savings, the initial setup and consumable costs can be a significant factor in the total project cost. This method is often chosen for projects where the benefits, such as faster weld times and suitability for thicker materials, outweigh the higher costs.
Stick Welding Costs
Stick welding is generally more cost-effective, especially regarding initial equipment investment and consumable costs. The electrodes used in stick welding are less expensive than flux-core wire, making this method more economical for projects with tight budgets. The simplicity of the equipment also contributes to lower upfront costs, as fewer components are required. While stick welding may take longer than flux-core welding, which could increase labor costs, its overall affordability and versatility make it a preferred choice for many welders, particularly in small-scale or budget-conscious projects.
Pros and Cons of Flux-Core Welding (FCAW)

Pros
- Faster Welding Speed: Allows for quicker completion of projects, particularly when dealing with thicker materials.
- Excellent Outdoor Suitability: Self-shielding flux makes it ideal for welding in windy or less controlled environments.
- Effective on Thick Materials: Provides deep penetration, making it suitable for heavy-duty applications.
- Ease of Use: Generally, it is more manageable for beginners to learn and use effectively.
Cons
- Higher Costs: Both equipment and consumables, like flux-core wire, tend to be more expensive.
- Significant Slag Production: Generates considerable slag, requiring extra cleanup.
- High Smoke Production: Produces a lot of smoke, which can obscure visibility and create a less pleasant working environment.
Pros | Cons |
Faster Welding Speed | Higher Costs |
Excellent Outdoor Suitability | Significant Slag Production |
Effective on Thick Materials | High Smoke Production |
Ease of Use | |
High Deposition Rate | |
Less Need for External Shielding Gas |
Pros and Cons of Stick Welding (SMAW)
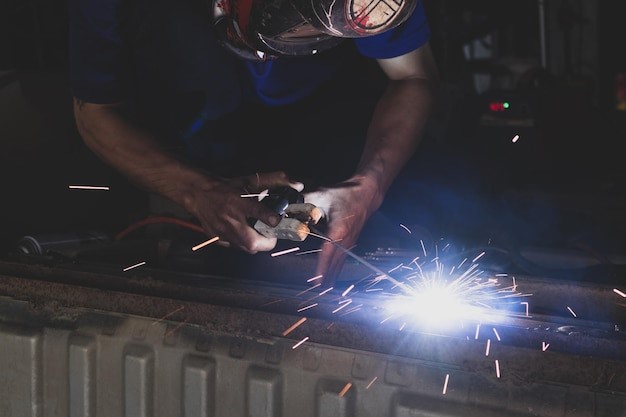
Pros
- Universal Application: Appropriate for various materials and thicknesses, making it a flexible choice for various projects.
- Lower Costs: Both the equipment and consumables are generally more affordable, making it cost-effective.
- Highly Portable: Minimal equipment is required, which makes it easy to transport and use in different locations.
- Reliable Weld Quality: Produces consistently strong welds, particularly in skilled hands.
Cons
- Slower Welding Speed: Completing welds takes more time than flux-core welding.
- Requires More Skill: Achieving high-quality welds, especially on thin materials, demands greater expertise.
- Affected by Wind: The arc and weld quality can be compromised in windy conditions unless proper precautions are taken.
Pros | Cons |
Versatile Application | Slower Welding Speed |
Lower Costs | Requires More Skill |
Highly Portable | Affected by Wind |
Reliable Weld Quality | |
Effective on Dirty or Rusty Metals | |
Minimal Equipment Required |
Choosing Between Flux-Core Welding and Stick Welding
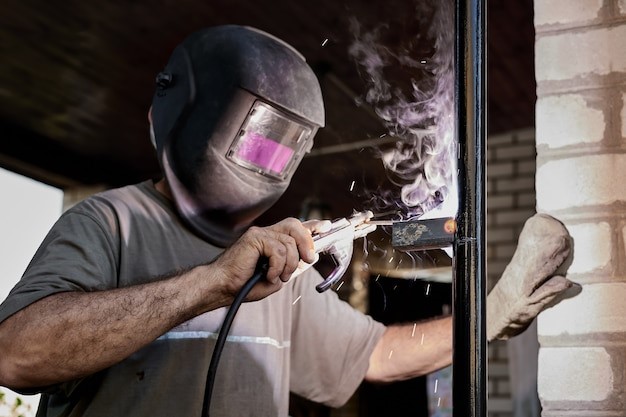
Project Requirements
When deciding between flux-core welding and stick welding, the specific requirements of your project play a crucial role. Flux-core welding is often the better choice for projects that demand high-speed welding and are performed outdoors or in less controlled environments. It excels in heavy-duty applications where thick materials need to be joined quickly. On the other hand, stick welding is ideal for smaller-scale projects requiring versatility in material types and thicknesses. Its simplicity and lower cost make it suitable for a broad range of welding assignments, especially where precision and control are more critical than speed.
Welding Skill
The skill level of the welder is another important factor. Flux-core welding is generally easier to learn and use, making it more accessible for beginners. The process is more forgiving and allows for quicker progress. Stick welding requires a higher skill level to produce quality welds, particularly on thinner materials. Experienced welders might prefer stick welding for its precision and the ability to work on various materials.
Welding Accessibility
Accessibility to welding equipment and materials can also influence your choice. Flux-core welding typically requires specialized equipment, which might not be readily available in all locations. Stick welding, with its simpler setup and more widely available consumables, offers greater accessibility, making it easier to perform in remote or resource-limited environments.
Environmental Considerations
The environment where the welding will take place is a critical consideration. Flux-core welding is well-suited for outdoor environments where wind and other elements might disrupt other welding processes. Its self-shielding nature provides a robust solution in such conditions. Stick welding, while also capable of outdoor work, is more sensitive to environmental factors like wind, which can influence the quality of the weld. Therefore, choosing the right method depends on the specific environmental conditions of the job site.
Final Thoughts
Choosing between flux-core and stick welding depends on your project’s specific needs, the welder’s skill level, and the working environment. Flux-core welding is advantageous for its speed and outdoor suitability, making it ideal for heavy-duty tasks. Stick welding, on the other hand, offers versatility and simplicity, making it a reliable choice for various materials and conditions.
Both methods have strengths and limitations, so understanding these factors will help you select the best approach for your welding needs. By carefully considering the project requirements, skill level, and environmental requirements, you can make a knowledgeable decision that ensures the best results.
FAQs
What is the primary difference between flux-core welding and stick welding?
Flux-core welding uses a continuously fed wire with internal flux for shielding, while stick welding uses a flux-coated electrode. Flux-core is faster and better for outdoor work, whereas stick welding is more versatile and cost-effective.
Which welding method is better for beginners?
Flux-core welding is easier for beginners due to its forgiving process and simpler equipment handling. Stick welding needs more skill and experience to achieve high-quality welds.
Can flux-core welding be used indoors?
Yes, but proper ventilation is needed due to the high amount of smoke and fumes produced. Stick welding also produces smoke but generally at a lower level.
Is flux-core welding more expensive than stick welding?
Yes, flux-core welding is usually more expensive because of higher wire costs and specialized equipment. Stick welding is more budget-friendly and has cheaper consumables.