Maintaining the integrity of welds under varying conditions is a significant challenge in the construction and manufacturing industries. Traditional welders like a stick welder often fall short, especially in windy environments where contamination can occur. Flux-Core Arc Welding (FCAW) offers a robust solution to this problem by using a flux-cored wire that generates its shielding gas, protecting the weld from contaminants.
This method is particularly effective in demanding applications like shipbuilding and structural steel fabrication, where reliability and strength are critical. FCAW enhances weld quality and increases efficiency, making it an essential process for industries that require durable and high-performance welds.
Types of Flux-Core Arc Welding
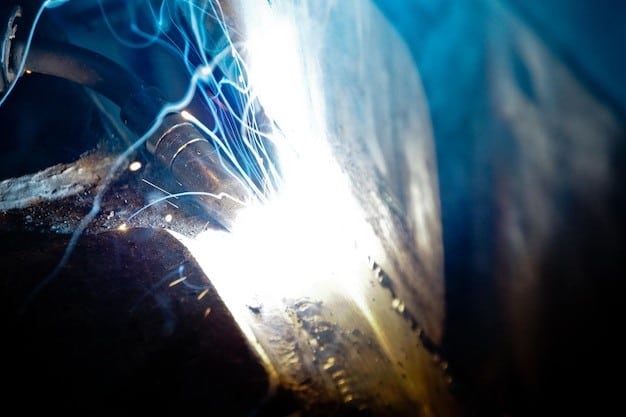
Flux-core arc Welding (FCAW) is divided into two main types: self-shielded flux-cored arc welding (FCAW-S) and Gas-shielded flux-cored arc welding (FCAW-G). Depending on the welding conditions and requirements, each type has specific applications and advantages.
Self-Shielded Flux-Cored Arc Welding (FCAW-S)
Self-shielded flux-cored arc welding (FCAW-S) does not require an external shielding gas. Instead, the flux within the wire produces the necessary gas to protect the weld from atmospheric contamination. This makes FCAW-S highly suitable for outdoor environments or where wind might disrupt the shielding gas if it were externally supplied.
FCAW-S is often used in construction, heavy equipment repair, and other fieldwork where portability and versatility are crucial. It is also effective on thicker materials and in difficult-to-access positions, offering good penetration and strength.
Gas-Shielded Flux-Cored Arc Welding (FCAW-G)
Gas-shielded flux-cored arc welding (FCAW-G) requires an external gas supply, typically carbon dioxide or a mixture of gases, to shield the weld area. This method is usually preferred in controlled environments like manufacturing plants where precise weld quality is necessary. FCAW-G produces cleaner welds with less spatter, which reduces the need for post-weld cleanup.
It is used in applications requiring high deposition rates, such as shipbuilding and structural steel fabrication. The external gas shielding also allows for better control over the welding process, leading to stronger and more consistent welds.
Feature | FCAW-S (Self-shielded) | FCAW-G (Gas-shielded) |
Shielding Method | No external gas is required | Requires external gas (e.g., CO2) |
Environmental Suitability | Ideal for outdoor/windy conditions | Best suited for controlled environments |
Weld Cleanliness | More slag, more cleanup needed | Cleaner welds with less spatter |
Material Suitability | Effective on thicker materials | Suitable for a variety of thicknesses |
Portability | More portable, no gas tank needed | Less portable due to gas tank |
Weld Quality | Strong welds but more slag | High-quality, consistent welds |
Application Areas | Construction, heavy equipment | Shipbuilding, structural fabrication |
Key Applications of Flux-Core Arc Welding
Flux-Core Arc Welding (FCAW) is widely used in various industries due to its versatility and efficiency. It plays a critical role in the construction industry, where strong, reliable welds are essential. In construction, FCAW is commonly used for joining structural steel components, reinforcing bars, and heavy machinery.
Construction Industry
Flux-Core Arc Welding (FCAW) is widely used in construction because it produces strong and durable welds. It is especially beneficial in large-scale projects where the welding needs to be done outdoors, often in challenging weather conditions. FCAW’s ability to perform well even in windy or contaminated environments makes it ideal for constructing bridges, buildings, and other infrastructure. The method allows for high deposition rates, enabling welders to complete tasks efficiently without compromising the quality of the welds.
Shipbuilding and Marine Applications
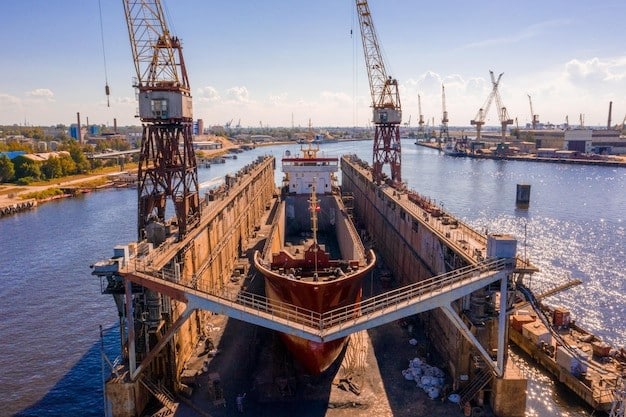
FCAW is indispensable in shipbuilding and marine applications. The harsh and variable conditions encountered in marine environments demand welding methods that can withstand moisture, salt, and other corrosive elements. FCAW, particularly the gas-shielded variant, provides the protection and strength required for ship hulls, decks, and other structural components. The process is also effective in welding thicker materials commonly used in shipbuilding.
Automotive and Transportation
The automotive and transportation sectors benefit from FCAW’s ability to deliver strong, reliable welds that endure the stresses of constant use and movement. FCAW is often used in manufacturing heavy vehicles, trailers, and railcars, where the strength of the welds directly impacts safety and performance. The method’s versatility allows it to be used on various metals and positions, making it suitable for the automotive industry’s complex and diverse welding requirements.
Industrial Fabrication
FCAW is frequently used in industrial fabrication due to its adaptability and efficiency. The process is well-suited for fabricating large and heavy components that require robust and durable welds. Industries such as heavy machinery, mining equipment, and pressure vessels rely on FCAW to weld thick materials and achieve deep penetration. The method’s consistency and reliability make it an essential part of industrial fabrication, where the quality and strength of welds are paramount to the safety and functionality of the final products.
Advantages of FCAW
High Deposition Rates
Flux-Core Arc Welding (FCAW) is known for its high deposition rates, meaning it can quickly deposit a large amount of weld material. This efficiency makes it a preferred method in industries where speed is crucial, such as construction and manufacturing. The ability to quickly lay down welds without sacrificing quality enhances productivity and reduces overall project timelines.
Versatile Welding Positions
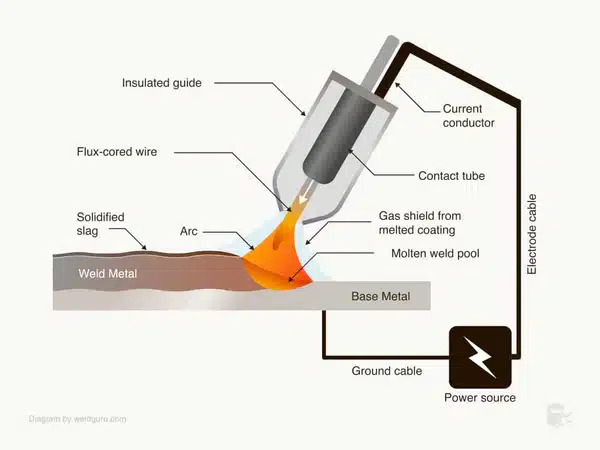
FCAW is highly versatile when it comes to welding positions. It can be used effectively in flat, horizontal, vertical, and overhead positions. This adaptability is particularly beneficial in industries like shipbuilding and structural steel fabrication, where welders often need to work in difficult-to-reach areas. The versatility of FCAW allows for consistent, high-quality welds in various orientations, making it a reliable choice for complex projects.
Various Conditions
One of FCAW’s key advantages is its ability to perform well in a wide range of environmental conditions. Unlike other welding methods, FCAW can be used outdoors in windy or contaminated environments without significant risk of weld defects. The self-shielded variant of FCAW, in particular, is designed to protect the weld from atmospheric contamination, making it ideal for fieldwork and outdoor projects.
Good Penetration and Strength
FCAW provides excellent penetration and produces strong, durable welds. This makes it suitable for welding thicker materials, often required in heavy industries like shipbuilding, construction, and industrial fabrication. The deep penetration achieved with FCAW ensures that the welds are robust and can withstand high stress, contributing to the structural integrity of the final product.
Less Preheat
Another advantage of FCAW is the reduced need to preheat the materials before welding. This is especially beneficial when working with thick or hard-to-weld materials. The reduced preheat requirement saves time and minimizes the risk of thermal damage to the welded materials, making FCAW an efficient and cost-effective welding method.
Less Hydrogen Cracking
Hydrogen cracking is a common concern in welding, especially when working with high-strength steel. FCAW helps to minimize the risk of hydrogen-induced cracking due to its ability to produce welds with low hydrogen content. The flux in the wire plays a crucial role in controlling hydrogen levels, reducing the chances of cracking, and ensuring the longevity and reliability of the welds. This makes FCAW a safer and more reliable choice for critical welding applications.
Challenges of FCAW
Slag Removal
One of the primary challenges of Flux-Core Arc Welding (FCAW) is the need for slag removal. The flux in the welding wire produces slag that covers the weld, protecting it during the welding process. However, this slag must be removed after welding, which can be time-consuming and requires additional effort. In some cases, improper slag removal can lead to defects in subsequent weld layers or negatively impact the appearance of the final weld.
Welding Thin Materials
FCAW can be challenging when welding thin materials. The process is known for its deep penetration, which can lead to burn-through or warping of thin metals. Controlling the heat input is crucial when using FCAW on thinner materials, but achieving a clean weld without defects can be difficult, even with careful control. This limitation makes FCAW less suitable for projects involving thin-gauge materials, where other welding methods might be preferred.
Spatter
Spatter is another challenge associated with FCAW. The process tends to produce more spatter than other welding methods, creating a mess around the weld area and requiring additional cleanup. Spatter can also adhere to the workpiece, leading to defects or the need for rework. While some spatter can be controlled by adjusting welding parameters, it remains a common issue that can affect the overall efficiency and quality of the welding process. Managing spatter is essential for achieving a clean and aesthetically pleasing weld.
Advantages of FCAW | Challenges of FCAW |
High deposition rates | Slag removal |
Versatile welding positions | Welding thin materials |
Effective in various environmental conditions | Spatter production |
Good penetration and strength | |
Less preheat required | |
Less hydrogen cracking | |
Suitable for outdoor and windy conditions | |
Strong welds in thick materials | |
Efficient for large-scale projects | |
Reliable in high-stress applications |
Final Thoughts
Flux-Core Arc Welding (FCAW) is a versatile and efficient welding method, particularly in industries that demand strong and reliable welds. While it offers significant advantages, such as high deposition rates and adaptability to various positions, it also presents challenges like slag removal and spatter. The decision to use FCAW should be based on the project’s specific requirements, considering its benefits and limitations in choosing reliable welding machine suppliers. By understanding the strengths and weaknesses of FCAW, industries can effectively leverage this welding method to achieve durable and high-quality results in demanding applications.
FAQs
What is Flux-Core Arc Welding (FCAW) used for?
Flux-Core Arc Welding is commonly used in heavy-duty applications such as shipbuilding, construction, and industrial fabrication due to its high deposition rates and ability to withstand various environmental conditions.
What is the difference between FCAW-S and FCAW-G?
FCAW-S (Self-shielded) does not require external shielding gas, making it ideal for outdoor work. FCAW-G (Gas-shielded) uses an external gas supply for shielding, which is more suited for indoor environments and provides cleaner welds.
What materials can be welded using FCAW?
FCAW is effective on various materials, including carbon steel, stainless steel, and alloy steel. However, it is particularly well-suited for thicker materials.
What are the main advantages of using FCAW?
FCAW’s main advantages include high deposition rates, versatility in welding positions, good penetration and strength, and reduced need for preheating, making it efficient for heavy-duty applications.
What are the common challenges faced when using FCAW?
Common challenges include slag removal, difficulty welding thin materials due to deep penetration, and spatter production, which can require additional cleanup and affect the quality of the weld.