Welding is a crucial process in manufacturing, but it often comes with significant costs that can strain budgets and reduce profitability. High materials, labor, and equipment maintenance expenses can quickly add up, impacting operations’ overall efficiency. However, companies can effectively manage and lower these expenses by implementing cost-saving strategies, such as optimizing material usage, improving process efficiency, and reducing labor costs.
These strategies not only help cut costs but also enhance productivity and ensure high-quality welds, contributing to the long-term success and sustainability of the business. By addressing the problem of high welding costs, businesses can achieve a more streamlined and cost-effective welding operation.
Typical Welding Costs
Welding costs can be broadly categorized into four main areas: labor, materials, equipment, and overhead.
Labor Costs
Labor is one of the most significant expenses in welding. This includes the wages of skilled welders, their training, and any additional support staff needed for the operation. Overtime and special skill premiums can further increase these costs, making labor a crucial area to manage effectively.
Material Costs
The cost of materials, such as TIG welding rods, MIG welding wire, and shielding gases, also contributes significantly to the overall expenses. These materials vary in price depending on quality and type, and managing waste and overuse is essential to keep costs under control.
Equipment Costs
Welding equipment, including machines, torches, and protective gear, requires substantial investment. Beyond the initial purchase, regular maintenance, repairs, and eventual replacements add to the ongoing costs. Investing in high-quality, durable equipment can help minimize these expenses over time.
Overhead Costs
Overhead costs encompass everything from utilities and facility maintenance to administrative expenses. While not directly tied to welding activities, these indirect costs still impact the budget. Effective management of overhead costs, such as optimizing energy use and minimizing downtime, can reduce the total welding expenses.
Optimizing Material Usage
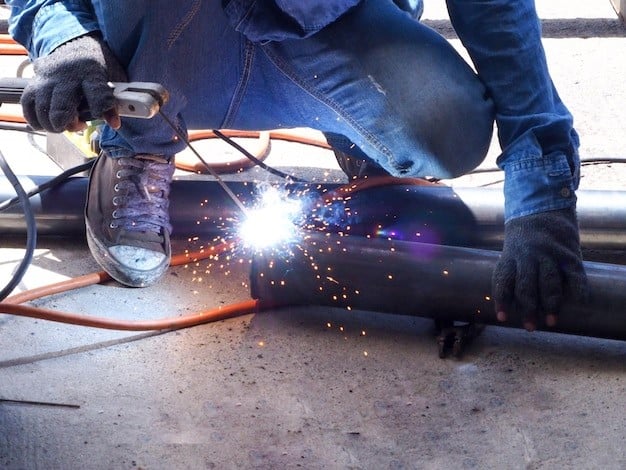
Optimizing material usage is essential for reducing welding costs and ensuring efficient operations. By carefully selecting the right materials and minimizing waste, companies can significantly lower their expenses while maintaining quality.
- Selecting the Right Materials: Choosing the appropriate materials for the specific welding task is crucial. This involves considering factors such as material compatibility, durability, and cost-effectiveness. Selecting the right materials can lead to fewer reworks and a more efficient welding process.
- Minimizing Waste: Reducing material waste is another key strategy for cost savings. This can be achieved by precise measurement, careful handling, and utilizing leftover materials whenever possible. Implementing strict waste management practices cuts costs and contributes to more sustainable and environmentally friendly operations.
Improving Process Efficiency
Improving process efficiency in welding operations is critical for reducing costs and boosting productivity. By automating welding processes and streamlining workflows, businesses can achieve more consistent results with less effort.
- Automating Welding Processes: Automation in welding can significantly enhance efficiency. Automated systems perform repetitive tasks with greater precision and speed, reducing the risk of errors and the need for manual intervention. This leads to faster production times and lower labor costs.
- Streamlining Workflow: Simplifying and optimizing the workflow is another effective way to improve efficiency. This involves organizing tasks logically, minimizing unnecessary steps, and ensuring that materials and equipment are readily accessible. A streamlined workflow reduces downtime and keeps the welding process running smoothly, contributing to overall cost savings and productivity gains.
Reducing Labor Costs
Reducing labor costs is essential for managing welding expenses effectively. One approach is to invest in training and upskilling workers, enabling them to complete tasks more efficiently and with fewer errors. Additionally, employing automation where possible can decrease the reliance on manual labor, leading to lower wage costs. Optimizing staff schedules to avoid unnecessary overtime and ensuring that each worker is fully utilized can help cut labor expenses. By focusing on these strategies, businesses can maintain a skilled workforce while controlling labor costs.
Enhancing Equipment Utilization
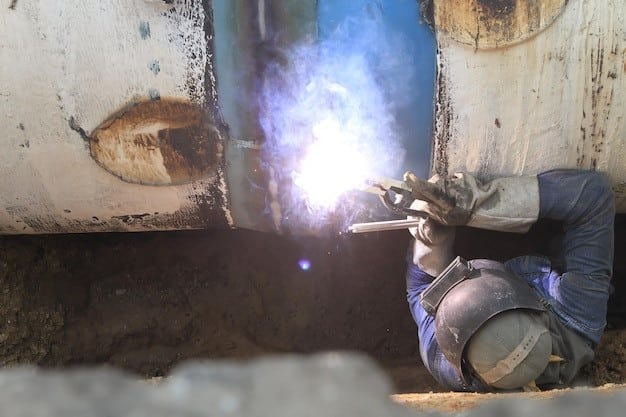
Enhancing equipment utilization is key to reducing welding costs and improving overall productivity. Companies can ensure their tools function efficiently and effectively by regularly maintaining and upgrading equipment.
- Regular Maintenance: Regular maintenance of welding equipment is essential for preventing breakdowns and costly repairs. By routinely inspecting and servicing machines, companies can extend the lifespan of their equipment and avoid unexpected downtime, which can disrupt workflow and increase costs.
- Upgrading Equipment: Investing in modern, more efficient welding equipment can save significant costs. Newer machines often have advanced features that improve precision, reduce energy consumption, and enhance overall performance. Upgrading equipment boosts productivity and helps maintain a competitive edge in the market.
Improving Quality Control
Improving quality control in welding processes is crucial for minimizing costs and ensuring high standards. A key aspect of this is reducing the need for rework, which can be time-consuming and expensive.
- Reducing Rework: Rework occurs when welding tasks need to be redone due to defects or errors. By implementing strict quality control measures, such as regular inspections and adherence to welding procedures, companies can significantly reduce the occurrence of rework. This saves time and resources and ensures that the final product meets the required quality standards, leading to greater customer satisfaction and cost efficiency.
Energy Efficiency and Cost Savings
Energy efficiency is critical to reducing welding costs and promoting sustainability. Companies can save significant costs by optimizing energy use while minimizing environmental impact.
- Optimizing Energy Use: Efficient energy management in welding processes involves using equipment that consumes less power and implementing practices that reduce energy waste. This can include selecting energy-efficient welding machines, maintaining equipment to ensure optimal performance, and scheduling welding tasks during off-peak hours to take advantage of lower energy rates. By optimizing energy use, businesses cut operational costs and contribute to a greener, more sustainable manufacturing process.
Strategic Sourcing
Strategic sourcing is essential for effectively managing welding costs. Businesses can secure better deals and reduce overall expenses by carefully selecting the right Stick, TIG, and MIG welding suppliers and considering bulk purchasing options.
- Choose the Right Supplier: Partnering with reliable, cost-effective suppliers ensures consistent quality and pricing. It is important to evaluate suppliers based on their track record, product quality, and pricing flexibility. Building strong relationships with suppliers can lead to better terms and timely deliveries, contributing to overall cost efficiency.
- Bulk Purchasing: Buying materials in bulk can offer significant cost savings. By purchasing larger quantities, companies can often negotiate discounts, reducing the per-unit cost of materials. Bulk purchasing also ensures a steady supply of essential materials, minimizing the risk of production delays due to shortages. This approach helps maintain smooth operations and control costs.
Innovations and Technology
Innovations and technology are vital in enhancing welding efficiency and reducing costs. Embracing digital tools and advanced welding technologies can significantly improve the quality and speed of welding operations.
- Digital Tools: Integrating digital tools into welding processes allows for better monitoring, control, and optimization. Software solutions can track performance, manage inventory, and ensure compliance with welding standards. Using digital tools, companies can gain real-time insights, make informed decisions, and streamline operations.
- Advanced Welding Technologies: Adopting the latest welding technologies can lead to more precise and efficient processes. Techniques such as laser welding, robotic welding, and advanced arc welding methods offer greater accuracy, reduced material waste, and faster production times. Investing in these technologies improves productivity and helps maintain a competitive edge in the industry.
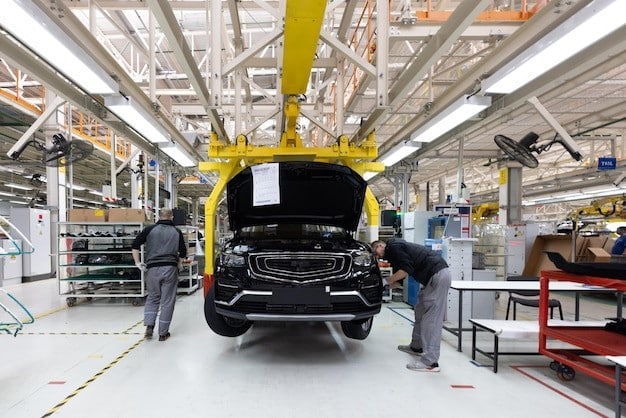
Important Welding Tips, Benefits, and Implementation Steps
Tips | Benefits | Implementation Steps | Impact Level |
Selecting the Right Materials | Reduces waste and ensures material compatibility. | Evaluate material needs and suitability. | High |
Minimizing Waste | Lowers costs by utilizing materials efficiently. | Implement waste reduction practices. | Medium |
Automating Welding Processes | Increases productivity and reduces labor costs. | Invest in automation technologies. | High |
Streamlining Workflow | Improves efficiency and minimizes downtime. | Optimize task sequencing and flow. | Medium |
Regular Maintenance | Prevents breakdowns and extends equipment life. | Schedule routine inspections and servicing. | High |
Upgrading Equipment | Enhances performance and reduces energy costs. | Purchase and install new equipment. | High |
Reducing Rework | Saves time and resources by ensuring quality. | Implement quality control checks. | High |
Optimizing Energy Use | Lowers energy expenses and promotes sustainability. | Use energy-efficient equipment. | Medium |
Choosing the Right Supplier | Ensures consistent quality and cost-effective pricing. | Research and select reliable suppliers. | Medium |
Bulk Purchasing | Reduces material costs and ensures steady supply. | Negotiate bulk purchase agreements. | Medium |
Using Digital Tools | Enhances monitoring and process optimization. | Implement relevant software tools. | High |
Adopting Advanced Technologies | Increases accuracy and production speed. | Invest in cutting-edge welding technology. | High |
Final Thoughts
Effectively managing welding costs is crucial for maintaining a profitable and efficient operation. Businesses can achieve significant savings without compromising quality by implementing the strategies discussed. For those seeking reliable and cost-effective welding solutions, YesWelder stands out as an ideal choice. They offer a wide range of high-quality and professional welders at approachable prices, making it easier for companies to equip their operations with the best tools without exceeding their budget. YesWelder’s commitment to quality and affordability ensures you get the best value for your investment, supporting your cost-saving efforts and operational needs.
FAQs
What are the most effective ways to reduce welding costs?
Optimize welding parameters and techniques, use automation and advanced technology, and minimize material waste through precise planning and inventory management.
How does using automation help lower welding costs?
Automation increases efficiency and consistency, reduces labor costs, and minimizes errors, lowering overall production costs.
Can changing welding consumables impact cost?
Yes, choosing high-quality consumables that match the specific welding process can reduce the frequency of replacements and improve weld quality, ultimately lowering costs.
How important is maintenance in reducing welding costs?
Regular maintenance of welding equipment ensures optimal performance, prevents breakdowns, and reduces repair costs, contributing to overall cost savings.
What role does employee training play in welding cost reduction?
Proper training enhances welders’ skills, reduces mistakes, and improves efficiency, leading to better quality welds and reduced rework costs.