Among the most used metals in almost every industry, for great resistance to corrosion, strength, and its good-looking appearance, stainless steel holds pride. Of the various grades available, 316 stainless steel is considered to offer outstanding corrosion resistance in the marine environment and at high temperatures.
Knowledge of the details on how to weld 316 stainless steel is important for welder distributors and bulk buyers of welding equipment in order to make the right kind of solutions available to the end users. This article covers various best practices for welding 316 stainless steel, from MIG and TIG to stick welding.
Preparations Before Welding 316 Stainless Steel
The right preparation is one of the essentials in producing quality welds in 316 stainless steel. It reduces contamination and oxidation while maximizes weld strength.
Clean the Surface: Stainless steel is a metal that can be highly contaminated by dust, dirt, oils, and other elements. Make sure the welded area is free from contaminants. Use a wire brush or special cleaners to clean off any impurities on the surface easily.
Clean up the Work Site: Clean the work site to an area that would be less accessible to contaminated carbon steel dust. Using tools not contaminated by other metals will prevent cross-contamination in your weld.
Gas Coverage: Gas coverage is quite important, as 316 stainless steel is prone to oxidation. Argon or argon and helium mixture will avoid oxidation and discoloration of the weld.
Choosing the Correct Filler Material: Some of the common filler materials normally recommended for 316 stainless steel are 316 or 316L. Matching will maintain the corrosion resistance and steel strength.
MIG Welding 316 Stainless Steel
MIG welding (Metal Inert Gas welding) is used much with stainless steel because it works fast and is easy to do. That’s why MIG welding suppliers recommend wide applications in production and fabrication works.
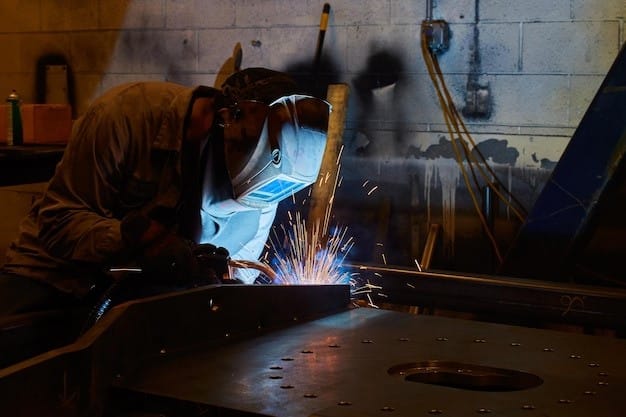
Pros and Cons of MIG Welding for 316 Stainless Steel
Pros
High Productivity: MIG welding machines can do fast welds, which apply to high-volume production.
Conveniences: MIG setup is less cumbersome than TIG. Less experienced welders will find it more easy to handle.
Economical: MIG welding uses electrodes as consumable parts and generates little waste.
Cons
Less Precise: The MIG process is less exacting than that of TIG. Consequently, this is a big turn-off for projects that would need high-quality aesthetics to come into place.
Splashing: MIG welding tends to splash, especially more than other processes. It requires more cleaning post-weld.
Less Control: Heat and weld pool may be difficult to handle which would result in low-quality weld.
Tips for Quality MIG Welding 316 Stainless Steel
Tri-mix Gas: Helium-based tri-mix gas, 90% helium, argon 7.5%, and 2.5% CO2 gives the best results. Helps in maintaining arc stability and less oxidation.
Adjust Wire Feed Speed: Stainless steel-type overheats and distorts at the same feed rate as mild steel. A slower wire feed is recommended.
Choose Correct Amperage: Too much amperage creates burn-through and distortion. It is advisable to start with low or lower and work up to where needed.
Torch Motion: Do focus on smooth steady motions of the torch, avoiding too much weaving, as stainless steel is apt to warp.
TIG Welding 316 Stainless Steel
Using TIG welders to weld 316 stainless steel is for precision and control. TIG welder suppliers usually regard it as a perfect fit for any stainless steel work when aesthetic and structural quality are of higher importance.
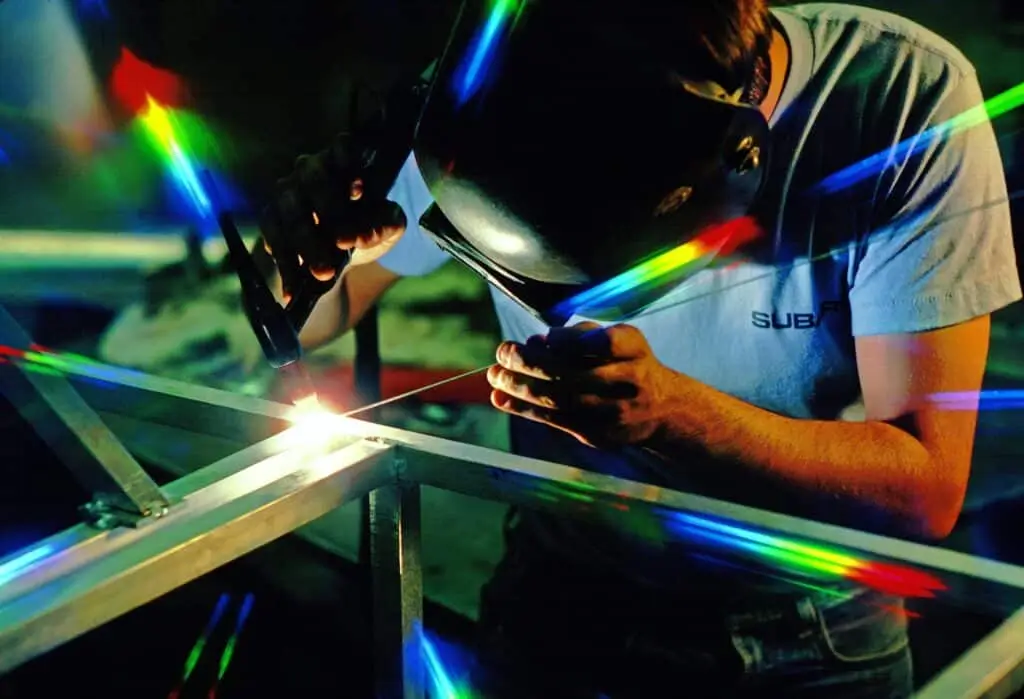
Pros and Cons of TIG Welding for 316 Stainless Steel
Pros
High Precision: TIG provides a small control over the weld pool and heat input, the welds are clean and accurate.
More Heat Control: Due to the thin sections in 316 stainless steel. TIG welding is a good way to solve warping.
Cons
Slower Process: Relatively, TIG welding is somewhat slower than MIG and could be a drawback under certain conditions of high production.
Higher Skill Requirement: Technically, TIG welding is more challenging, and better skills and more competent operators are demanded for better performance.
Equipment Cost: TIG machinery and accessories are costlier than others, which adds to the operation cost.
Tips for TIG Welding 316 Stainless Steel
Use Argon with Helium: 90% Argon with 10% Helium works well to give a stable arc and gives better heat control.
Use a 2% Thoriated Tungsten Electrode: The tungsten welding electrodes will give a stable arc and will last much longer when TIG welding stainless steel.
Adjust the Amperage: Too little amperage can help avoid burn-through and minimize warping.
Back Purge the Weld: By purging with inert gas on the backside, welds that show both sides will not oxidize.
Stick Welding 316 Stainless Steel
Honestly, stick welder suppliers may not highly recommend the technique for stainless steel. But it might be successfully applied for field repairs or where pays attention to portability.
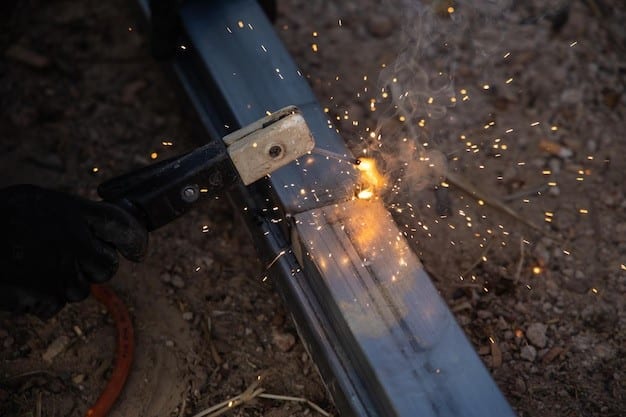
Pros and Cons of Stick Welding for 316 Stainless Steel
Pros
Portable and Versatile: Portable equipment used for the process makes it ideal for on-site or repair work.
Good for Thick Sections: Effective in welding thicker sections of the 316 stainless steel.
Cost-Effective Equipment: Stick welders are generally less expensive, reducing capital investment.
Cons
Lower Precision: It is less welcome when aesthetics plays an important role in a project
Much More Splatter: The application of stick welding results in much more splatter, creating a need for more cleanup.
Experienced Welders: Stainless steel stick welding requires experience to maintain the quality consistently.
Tips for Stick Welding 316 Stainless Steel
1. While welding 316 stainless steel, E316L-16 electrodes are recommended as they keep the metal’s durability intact without cracking.
2. A short arc should be maintained. This will help minimize spatter and promote good arc stability.
3. Preheating will help improve weld penetration and reduce stress when the sections are thicker.
4. Provide adequate ventilation as the fumes produced in welding stainless steel are hazardous.
How to Prevent Welding 316 Stainless Steel Defects
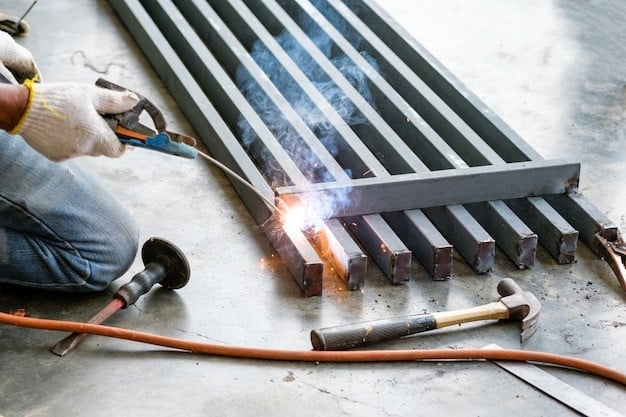
Preventing defects is essential to achieve quality and durability for a long period in corrosive services. Some of the common defects and how to avoid them are outlined below.
Porosity: This happens due to contamination, inadequate shielding gas, and poor gas coverage. Surfaces need to be clean at all times. Allow gas flow in a controlled manner.
Cracking: This occurs due to excessive heat input into the thicker sections because heat tends to have thermal stress. Low-input heat is applied using processes. Control the cooling rate. Apply preheating for heat treatment if required.
Distortion: The stainless steel will be distorted by the heat, so the minimum input of heat is desired, and alignment should be held by clamping or with fixtures.
Back Purging: Proper back purging and the use of the right shielding gas minimize oxidation and discoloration.
You will be able to understand these common problems better and take some necessary prevention to prevent high-cost repairs and continuous production of top-notch welds.
Post-Weld Treatment for 316 Stainless Steel
The post-weld treatment gives corrosion resistance to 316 stainless steel in a harsh environment.
1. Cleaning: Residues and oxides around the weld are cleaned with a stainless wire brush.
2. Polishing: Quite often, aesthetically or otherwise for functional purposes, the weld needs to be polished to its original smooth finish to enhance corrosion resistance.
3. Passivation: Further, passivation can be done with a nitric acid solution to remove free iron particles and improve corrosion resistance.
4. Inspection: Visual examination and non-destructive testing shall be done concerning the requirements mentioned for the weld.
A suitable treatment after welding will improve not only the visible appearance of the weld, but it will also prolong the weld lifetime in corrosive media.
Conclusion
Each welding technique has advantages and limitations. The distributors and bulk buyers shall have to keep in mind the client requirements and intended applications to recommend welding machines and consumables. Following the best practices, one will get quality, durable welds that can retain the unique properties of 316 stainless steel.
Partner with YesWelder
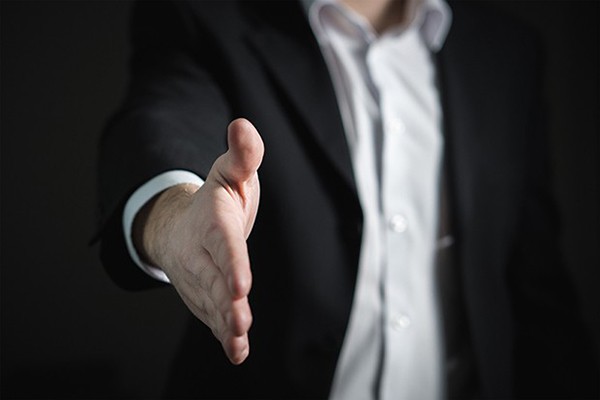
As a leading brand in welding equipment and supplies, YesWelder provides everything you need to support your customers in welding 316 stainless steel. From reliable MIG, TIG, and Stick machines to industrial ones, we help your business grow fast.
Interested in offering YesWelder products to your customers? Our wholesale and distributor programs back your business with high-quality, affordable welding solutions that deliver impressive performance.
FAQ
What kind of welding is most preferred for 316 stainless steel?
It is the TIG, as it is a process that can grant precision and control, best for aesthetic and structural integrity for most projects using stainless steel.
Can 316 stainless steel be MIG welded?
Yes, MIG welding can be done, especially in a high-production environment, but requires careful control in order to evade defects.
Why is back purging so important in welding stainless steel?
Inert gas back purging avoids oxidation, and the weld maintains corrosion resistance. It is a must for two-sided visible welds.
Why are stainless steel preparation tools preferred to be used?
Because it doesn’t contaminate and thus provides for a good quality weld with only stainless steel tools.