Selecting between inverter and transformer welders requires a weighing of project needs, operational efficiency, and long-term value. Both technologies, at the heart of arc welding, are applied for distinct purposes—lightweight, portable work or heavy-duty, fixed use.
The following content makes an in-depth study of their mechanism, performance characteristics, and usability in residential, commercial, and industrial settings, where experts and hobbyists can make informed choices.
Inverter and Transformer Welders: Working Principles
To properly assess these welding systems, it is critical to understand the technology behind them.
Inverter Technology
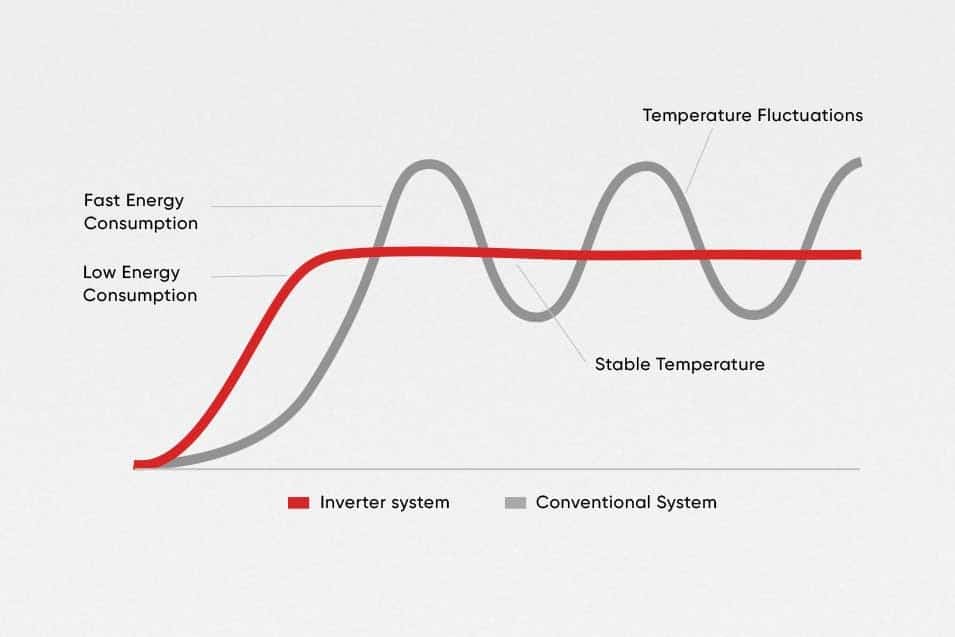
Advanced electronics are used by inverter welders to invert power. They receive alternating current (AC) at 50Hz or 60Hz (typically 110V–240V) through a rectifier and transform it into direct current (DC).
High-frequency switching components such as Insulated Gate Bipolar Transistors (IGBTs) subsequently switch this DC to frequencies from 20,000Hz up to 100,000Hz.
This high-frequency output enables a small transformer, normally lighter than 5 kg—to be obtained, as opposed to the usual weighty designs above 25 kg. The result is better arc stability and accuracy, suitable for various welding applications.
Note: Inverter technology was initially seen in the late 1980s with the evolution of semiconductor engineering, where welder portability and efficiency were enabled.
Transformer Mechanics
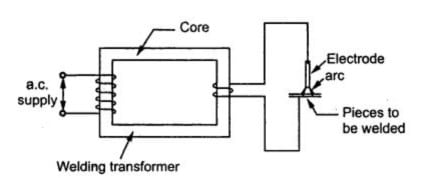
Transformer welders use electromagnetic induction, a phenomenon developed in the early 20th century with the discovery of industrial arc welding. They take 220V–240V AC as input, directing it through heavy copper or aluminum coils—15–30 kg in size—to step down the voltage to 20V–30V at 50Hz–60Hz.
This simple design does not incorporate electronic devices, favoring ruggedness over sophistication. The compromise is more space and less flexibility to power variations.
Power and Efficiency Analysis
Inverter Efficiency
Inverter welders are 90%–95% efficient because of their high-frequency conversion. For 140A output, power consumption is 280W to 320W, with an average of 300W.
With 10 hours of weekly use and an electricity rate of $0.12/kWh, costs of operation are approximately $1.80 per month. Their ability to run on unstable inputs—such as 110V circuits with 15A breakers or 6,000W generators—adds versatility for small-scale and remote applications.
Data Point: Stick welding machine has experienced a 20% reduction in energy consumption compared to transformer models owing to the lowered resistive losses.
Transformer Power
Transformer welders are 55%–65% efficient, and they consume 500W–550W for a 140A output. Even with the same usage rate, monthly costs add up to $3.00. The lowered efficiency is due to dissipation as heat in large coils with losses of up to 200W.
However, with higher currents, they are better—providing 225A continuously for heavy material (like 12 mm steel)—where inverters will lag behind on breaker limits or burn out.
Table: Power Metrics Comparison
Type | Efficiency | Wattage (140A) |
Inverter | 93% | 300W |
Transformer | 60% | 500W |
Inverter vs Transformer Welders: Size, Weight, and Portability Specs
Inverter Portability
Inverter welders generally weigh 9–14 kg and is on average 43 cm x 28 cm x 30 cm. Due to its compactness, it can be easily moved, suitable for application in portable cases such as field repair or roof usage.
They support double-voltage inputs (110V–240V) with the use of merely a standard outlet or 12-gauge, 30A extension cord necessary for them to operate, supporting diverse environments.
Transformer Dimensions
Transformer welders are 32–45 kg, about 61 cm x 43 cm x 30 cm. As a result, they demand a dedicated work space and a 220V, 50A circuit that usually necessitates professional electrical installation, $150–$300.
They are ideally suited for permanent installations, e.g., structural steel or farm equipment repair in workshops, though portability necessitates the use of additional equipment like a 225 kg-capacity dolly.
Arc Quality and Welding Performance
Inverter Accuracy
Inverter welders yield consistent arcs with voltage response times of 0.1 seconds, thanks to digital control systems. They better thin stock—say, 3 mm aluminum, 1.5 mm steel, or 6 mm stainless steel—using a smooth, low-spatter finish.
Typical duty cycles are in the range of 60% at 140A (6 on, 4 off, 10-minute cycle), well-suited for extended periods of use in production processes like the manufacture of automobiles or aircraft.
Transformer Power
Transformer welders have a stable, high-power arc, which is well suited to thick materials—25 mm steel plate or 10 mm rebar—up to 225A. Their duty cycle is reduced, usually 20% at 225A (2 min on, 8 off), but adequate for heavy-duty welds with deep penetration, e.g., structural and agricultural uses. They underperform on thin stock, and a danger of burn-through exists below 6 mm.
Cost, Durability, and Maintenance
Cost Analysis
- Inverters: They cost $300–$800 for 140A–210A outputs and have a 10–15 year working life in favorable conditions. Electronic breakdown repair takes between $100–$200.
- Transformers: They cost $200–$500 for 140A–160A and have over 50 year working lives in steady conditions. Repairs, often for coils or wiring, are $50–$100.
- Statistic: Inverter failure levels at adverse conditions are estimated at 5% annually, compared to 15% for inverters due to their electronic vulnerability.
Maintenance Requirements
- Inverters: Should have their vents cleaned monthly to prevent overheating, which is achievable within 5 minutes using compressed air. Storage should maintain temperatures at between 5°C and 32°C to protect circuitry.
- Transformers: Coil checks every year, with a multimeter test for resistance (>1 ohm), ensure operation. Mechanical components can be tightened or degreased to offset wear or environmental exposure.
Application Suitability of Inverter & Transformer Welders
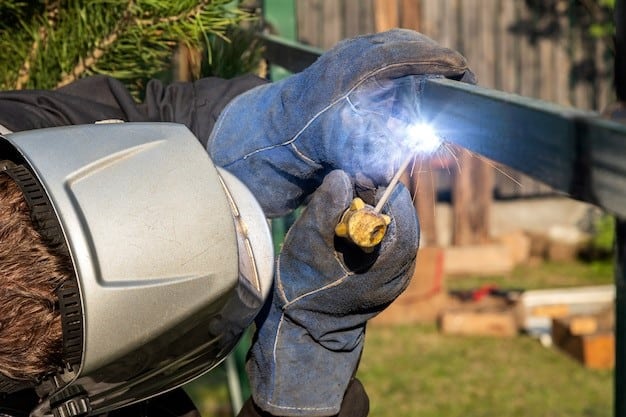
Inverter Advantages
- Small-Scale Projects: Suitable for welding 6 mm steel frames, with portability and 110V compatibility requirements.
- Mobile Operations: Suitable for on-site operations (e.g., fencing), using dual-voltage capability and 20% energy efficiency.
- Precision: Suitable for thin material (e.g., 1 mm titanium), reducing defects by as much as 30% in environment-controlled conditions.
Transformer Advantages
- Heavy Industry: For use in 25 mm steel welds, offering reliable long-term performance spanning decades.
- Farm Equipment Repairs: Durable on 10 mm steel components due to resistance to rural power fluctuations.
- Cost-Sensitive Operations: Provides a 40% lower initial investment, payback in high-volume applications within 2–3 years.
Assessment Guide: Evaluate needs based on budget (<$400 favors transformers), mobility (inverters), and material thickness (>12 mm suits transformers).
Conclusion: Selecting the Right Welder
Inverter welders are more efficient, portable, and precise and are suitable for mobile and small welding. Transformer welders provide unmatched power and durability for stationary, heavy-duty applications at a lower initial cost.
The choice depends upon the type of operations, material specifications, and budget constraints. This review is a comprehensive guide for professionals and technicians.
Come to YesWelder wholesale for more types of welding equipment!
FAQs on Inverter & Transformer Welders
What is the difference between inverter and transformer welders?
Inverter welders incorporate advanced semiconductor technology to convert standard AC power to high-frequency DC, which is both power efficient and small. Transformer welders use large copper or aluminum coils to step down the high voltage AC to a lower voltage, which provides raw, constant power.
Which is more energy efficient, inverter or transformer welders?
Inverter welders are 90%–95% efficient, needing less power for the same output compared to transformer welders, which are about 55%–65% efficient. Inverters can therefore offer long-term savings on electricity.
Do their power supply requirements vary?
Yes. Inverter welders are versatile and can be operated on a range of input voltages (110V–240V), which makes them ideal for home and job site use. Transformer welders will generally require a 220V dedicated supply, which will more than likely need to be installed professionally to get maximum performance.
Which welder type is best for DIY or light industrial uses?
Inverter welders are highly recommended for DIYers and small contractors because they are portable, efficient, and multiprocess for MIG, TIG, or stick welding on thinner metals.