The welding industry faces a significant challenge due to the growing labor shortage, primarily driven by an aging workforce and a skills gap that leaves many positions unfilled. This shortage threatens the industry’s ability to meet demand and maintain high quality and safety standards. However, solutions are emerging, such as adopting robotic welding and automation technologies.
These innovations address the shortage by reducing dependency on human labor and enhancing productivity and precision in welding processes. By integrating advanced machines from welding equipment suppliers and new training methods, the industry can bridge the gap and ensure a sustainable future for welding operations.
Factors Contributing to the Labor Shortage
The labor shortage in the welding industry is a multifaceted issue, with several key factors contributing to the problem.
Aging Workforce
One significant factor is the aging workforce. Many experienced welders are nearing retirement, and fewer younger workers are entering the field to replace them. This creates a gap that is difficult to fill, especially given the specialized skills required for welding.
Skills Gap
Another contributing factor is the skills gap. As technology advances, the skills needed in the welding industry have evolved, but training programs have not always kept pace. This results in a shortage of qualified workers with the technical expertise to operate modern welding equipment and techniques.
Industry Perceptions
Industry perceptions also contribute to the labor shortage. Welding is often seen as a physically demanding and less glamorous career choice, which deters young people from pursuing it as a profession. This perception, coupled with a lack of awareness about the industry’s opportunities and potential for growth, further exacerbates the shortage.
Economic and Market Trends
Economic and market trends add another layer to the issue. Economic downturns and fluctuations in demand for welded products can lead to periods of uncertainty in the industry. This instability can make welding less attractive as a career option, discouraging new entrants and contributing to the overall labor shortage.
Factors | Description |
Aging Workforce | Many experienced welders are retiring, creating a gap in skilled labor. |
Skills Gap | The skills required for modern welding have evolved, but training programs have not always kept pace. |
Industry Perceptions | Welding is often viewed as a less attractive career option, which deters new entrants. |
Economic and Market Trends | Economic downturns and market fluctuations affect job stability and the attractiveness of welding careers. |
Lack of Training Programs | Inadequate or outdated training programs fail to prepare new welders for current industry demands. |
Low Recruitment Efforts | Insufficient efforts to attract younger individuals to the welding profession contribute to the shortage. |
Robotic Welding and Automation
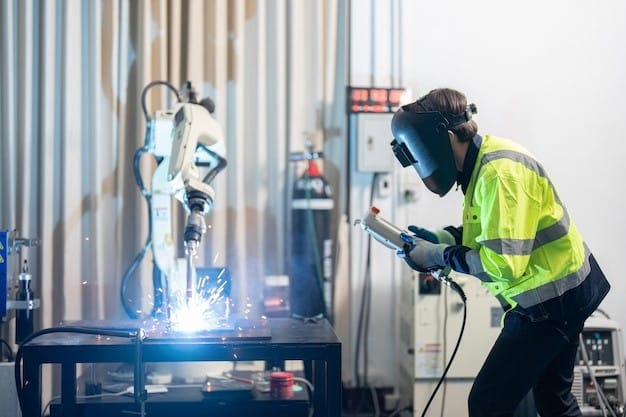
Robotic welding and automation have become increasingly important in addressing the labor shortage in the welding industry. These technologies offer a way to maintain production levels and quality standards without relying solely on human welders. Robotic welding involves using programmable machines to perform welding tasks with precision and consistency. As automation advances, more industries are adopting these technologies to enhance efficiency and reduce the burden on the shrinking workforce.
Pros of Robotic Welding
- Increased Productivity: Robots can work continuously without the need for breaks, leading to higher output and faster project completion.
- Improved Precision: Robotic systems can perform welds with a high level of accuracy, reducing the likelihood of errors and rework.
- Consistency: Robots can maintain the same level of performance across multiple welds, ensuring uniformity and quality in the final product.
- Cost Savings: Over time, robotic welding can reduce costs by minimizing waste, rework, and labor expenses.
- Safety: Robots can handle hazardous tasks, reducing the risk of injury to human workers and improving overall workplace safety.
Cons of Robotic Welding
- High Initial Investment: The cost of purchasing and setting up robotic welding systems can be substantial, which may be a barrier for smaller companies.
- Complex Maintenance: Maintaining and repairing robotic systems requires specialized knowledge and can be time-consuming and expensive.
- Job Displacement: The increased use of robots can lead to job losses among human welders, contributing to concerns about the future of employment in the industry.
Advanced Welding Equipment and Techniques
The welding industry is rapidly evolving with the introduction of advanced equipment and techniques designed to meet the demands of modern manufacturing and construction. Two key areas of innovation include smart welding machines and adaptive welding technologies. These advancements are helping to bridge the skills gap and improve overall efficiency in welding operations.
Smart Welding Machines
Smart welding machines represent a significant leap forward in welding technology. These machines have advanced sensors, data processing capabilities, and automated controls that enable them to perform complex welding tasks with minimal human intervention.
Real-time Monitoring and Adjustment
Smart welding machines can monitor welding parameters in real-time, such as voltage, current, and speed. If any deviation from the desired settings occurs, the machine can automatically adjust these parameters to ensure consistent weld quality. This capability reduces the risk of defects and rework, leading to higher efficiency and cost savings.
Enhanced Data Collection
Smart welding machines collect vast amounts of data during operation. This data can be analyzed to identify trends, optimize processes, and improve efficiency. By leveraging this data, companies can make informed decisions about equipment usage, maintenance schedules, and operator training, leading to continuous improvement in welding performance.
Adaptive Welding Technologies
Adaptive welding technologies are designed to automatically adjust to varying conditions in real-time, ensuring optimal performance even in challenging environments. These technologies are particularly useful in industries where precision and consistency are critical, such as aerospace, automotive, and shipbuilding.
Adaptive Welding Control Systems
Adaptive welding control systems use advanced algorithms to adjust welding parameters based on real-time sensor feedback. For example, if the system detects material thickness or temperature changes, it can modify the welding speed or power to maintain consistent weld quality. This adaptability is crucial for producing high-quality welds in complex or variable environments.
Laser Welding Technologies
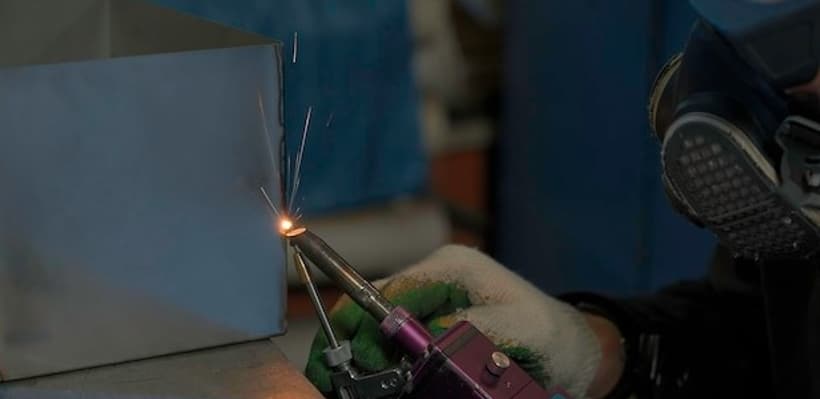
Laser welding is an advanced technique with several advantages over traditional welding methods. Adaptive laser welding systems can focus the laser beam with extreme precision, allowing for high-quality welds in materials that are difficult to weld using conventional methods. These systems can also adjust the laser’s power and focus in real-time, ensuring optimal performance in various conditions.
Robotic Welding with Adaptive Technology
Robotic welding systems with adaptive technology can adjust their welding paths and parameters based on real-time data. For instance, if the robot encounters a change in the joint geometry, it can automatically adjust its movements to compensate. This flexibility is particularly valuable in industries where welding tasks involve complex geometries or require high levels of precision.
Adaptive Gas Metal Arc Welding (GMAW)
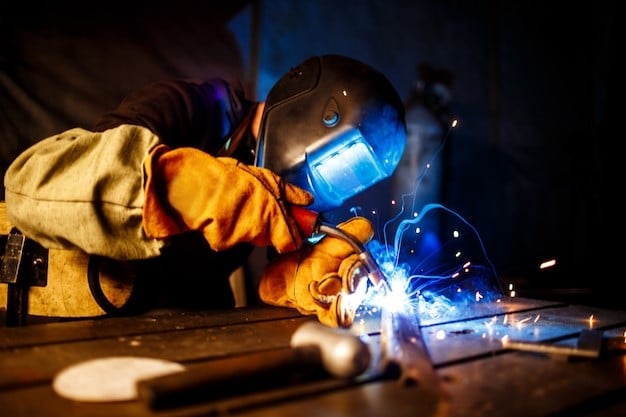
Adaptive GMAW systems are designed to adjust the welding parameters based on the specific characteristics of the weld joint. These systems can automatically modify factors such as MIG welding wire feed speed, voltage, and travel speed to achieve optimal results. This adaptability reduces the need for manual adjustments and ensures consistent weld quality across different applications.
Advanced Technologies and Benefits
Technology | Description | Benefits |
Smart Welding Machines | Machines equipped with sensors and data processing for real-time adjustments. | Improves weld quality, reduces errors, and enhances efficiency. |
Adaptive Welding Control Systems | Systems that adjust welding parameters based on real-time feedback. | Ensures consistent welds, minimizes defects, and optimizes performance. |
Laser Welding Technologies | Technologies that focus laser beams precisely for high-quality welds. | Provides high precision, reduces heat distortion, and improves weld strength. |
Robotic Welding with Adaptive Technology | Robots that adjust welding paths and parameters based on data. | Enhances productivity, ensures uniform welds, and reduces manual labor. |
Adaptive Gas Metal Arc Welding (GMAW) | Systems that modify parameters for consistent weld quality. | Improves weld consistency, adapts to different materials, and increases efficiency. |
Ultrasonic Welding | Uses high-frequency ultrasonic vibrations to join materials. | Enables welding of thin and delicate materials, reduces heat input, and produces strong joints. |
Friction Stir Welding (FSW) | A solid-state welding process that uses frictional heat to join materials. | Provides high-strength welds, minimal thermal distortion, and is ideal for aluminum and other non-ferrous materials. |
Plasma Arc Welding | Uses a plasma torch to produce high-precision welds. | Offers high-speed welding, precise control, and is suitable for thin materials. |
AR and VR in Welding Training
Augmented Reality (AR) and Virtual Reality (VR) revolutionize welding training by providing immersive and interactive learning environments. These technologies offer a safe and cost-effective way for trainees to practice welding techniques without the risks associated with real-world welding.
Benefits of AR and VR in Welding
AR and VR allow trainees to simulate various welding scenarios, enabling them to gain hands-on experience with different materials and techniques. These simulations can be tailored to specific skill levels, making them suitable for beginners and advanced welders. Additionally, AR and VR systems provide real-time feedback to help trainees identify and correct mistakes immediately, accelerating the learning process.
Internet of Things (IoT) in Welding
The Internet of Things (IoT) is significantly impacting the welding industry by connecting welding equipment to networks, allowing for real-time monitoring and control. This connectivity enhances operational efficiency and enables more informed decision-making.
IoT-enabled welding systems can monitor critical parameters like temperature, voltage, and current, ensuring consistent weld quality. Additionally, these systems can predict maintenance needs by analyzing performance data, reducing downtime, and extending equipment lifespan. IoT also facilitates remote management, allowing operators to oversee welding processes from anywhere, improving productivity and flexibility.
Collaborative Robotics (Cobots) in Welding
Collaborative robots, or cobots, are increasingly used in the welding industry to work alongside human operators. These robots are designed to assist in welding tasks, enhancing productivity while maintaining a safe working environment.
Cobots are equipped with sensors that allow them to safely interact with humans, making them ideal for tasks requiring precision and flexibility. They can take over repetitive or physically demanding tasks, allowing human welders to focus on more complex work. Additionally, cobots are easy to program and can quickly adapt to different welding tasks, making them versatile tools in various welding applications.
Future Trends
The welding industry is poised for significant advancements driven by emerging technologies. Adopting artificial intelligence (AI) and machine learning is expected to further automate welding processes, allowing for real-time adjustments and enhanced precision.
Sustainability and Green Welding
Sustainability will also play a crucial role in future welding trends. Companies will likely adopt greener welding practices, including eco-friendly materials and energy-efficient technologies, to reduce the environmental impact.
Human-Machine Collaboration
Human-machine collaboration will continue evolving, with more sophisticated collaborative robots (cobots) integrated into welding operations. These cobots will work more seamlessly with human workers, enhancing productivity and safety.
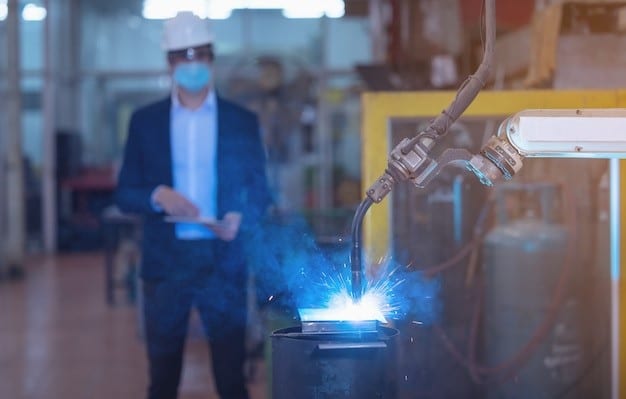
Final Thoughts
The welding industry is undergoing significant changes due to technological advancements and evolving workforce dynamics. Addressing the labor shortage requires a multifaceted approach, including adopting automation, advanced equipment, and new training methods. The industry can overcome current challenges and thrive as it embraces these changes. The future of welding lies in integrating innovative solutions that improve efficiency, safety, and sustainability. The welding industry will be well-equipped to meet future demands by staying adaptable and forward-thinking.
FAQs
What are the main causes of the labor shortage in the welding industry?
The primary causes include an aging workforce, a skills gap, negative industry perceptions, and economic fluctuations that affect job stability and attractiveness.
How is the welding industry addressing the labor shortage?
The industry is adopting robotic welding, automation, and advanced training methods and promoting welding as a viable and rewarding career to attract new talent.
What role does technology play in solving the welding labor shortage?
Technologies like robotic welding, smart machines, and adaptive welding techniques are helping to bridge the skills gap and improve efficiency, reducing the reliance on human labor.
Can robotic welding completely replace human welders?
While robotic welding enhances productivity and precision, it cannot fully replace human welders, especially in complex or custom tasks where human expertise is still essential.