In modern industrial environments, welding fumes pose significant health risks, stemming from inhaling toxic metallic particulates and gases during welding operations. Effective strategies to reduce fume exposure are paramount to address this concern.
Solutions involve implementing advanced fume extraction systems and adopting safer welding practices aligned with regulatory guidelines. These measures safeguard worker health and enhance operational efficiency by adhering to industry standards, ensuring a healthier and more compliant workplace.
Welding Fumes Basics
Welding fumes are complex mixtures of metallic oxides, silicates, and fluorides. They are produced when metal is heated above its boiling point, and vapors condense into fine particles. Depending on the metals being welded and the processes used, common components include iron, manganese, chromium, nickel, and lead.
Sources of Welding Fumes
Sources of welding fumes include various welding techniques such as MIG, TIG, and stick welding, differing in intensity and type of fumes generated. Understanding the composition and sources of these fumes is crucial for developing targeted strategies to minimize exposure and protect worker health in industrial settings.
Welding Fume Impact
Health Risks
Exposure to welding fumes can lead to serious health issues. The fine particulates inhaled by welders can cause lung damage and respiratory diseases, such as bronchitis and pneumonia. Chronic exposure increases the risks of more severe conditions, including lung cancer and metal fume fever. Neurological effects are also a concern, with manganese in welding fumes being linked to neurological disorders similar to Parkinson’s disease.
Economic Impacts
The health risks associated with welding fumes lead to significant economic implications. Businesses face increased healthcare costs and compensation claims from affected workers. Additionally, regulatory fines for non-compliance with safety standards can be substantial. These financial burdens underscore the need for effective fume management systems to reduce potential liabilities and healthcare expenses.
Operational Impacts
Beyond health and economic issues, welding fume exposure can affect workplace efficiency. High levels of fumes can lead to worker fatigue and reduced productivity. Frequent health-related absences disrupt operations and can delay project timelines, impacting overall business performance. Implementing robust fume control measures is essential to maintain operational continuity and workforce effectiveness.
Environmental Concerns
Welding fumes also pose environmental challenges. Releasing toxic substances into the atmosphere contributes to air pollution, affecting the workplace and the surrounding community. Companies are increasingly accountable for their environmental impact, making the management of welding emissions critical to sustainable operational practices.
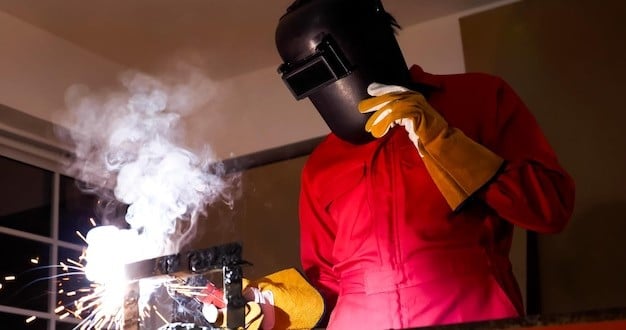
Industry Regulations for Welding Fume Control
- OSHA Standards: The Occupational Safety and Health Administration (OSHA) mandates specific measures to control welding fumes, setting permissible exposure limits (PELs) for various hazardous substances found in welding environments.
- Ventilation Requirements: OSHA requires adequate ventilation systems to capture and remove welding fumes at the source, preventing them from dispersing into the workplace atmosphere.
- Personal Protective Equipment (PPE): Regulations stipulate appropriate PPE, including respirators, welding gloves, and protective clothing, to shield workers from fume exposure.
- Training and Education: Employers are responsible for providing comprehensive training on the hazards of welding fumes, proper equipment use, and safety practices to minimize exposure.
- Monitoring and Compliance: Regular air quality monitoring in welding areas is required to ensure compliance with safety standards. Employers must also keep records of exposure data and health assessments to manage risks effectively.
- Global Standards: Beyond OSHA, other international bodies like the Health and Safety Executive (HSE) in the UK and WorkSafe in Australia enforce similar regulations, emphasizing global concern and action towards welding fume safety.
Reducing Welding Fumes in Operations
Fume Extraction Systems
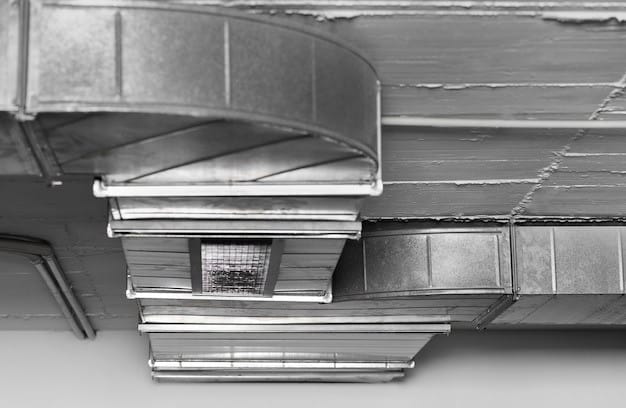
Implementing fume extraction systems is crucial for minimizing the inhalation of hazardous welding fumes. Depending on the setup, these systems capture fumes at their source before dispersing into the air, using local exhaust ventilation (LEV) devices that are either portable or fixed. Ensuring these systems are well-maintained and correctly positioned maximizes their efficiency and effectiveness in reducing airborne contaminants.
Welding Booths and Enclosures
Welding booths and enclosures are a physical barrier between the welding process and the workplace, containing and isolating fumes. These structures are equipped with ventilation systems to extract fumes directly from the enclosed area, significantly reducing the spread of fumes. This setup protects the welder and other nearby workers from exposure to harmful fumes.
Safe Work Practices
Adopting safe work practices is essential for minimizing fume exposure. This includes using welding processes that generate less fume, adjusting the welding technique to avoid excessive fume generation, and maintaining a clean work environment free from dust and debris that can exacerbate fume hazards. Regular training and adherence to safety protocols are vital to ensure all workers understand and implement these practices effectively.
Personal Protective Equipment (PPE)
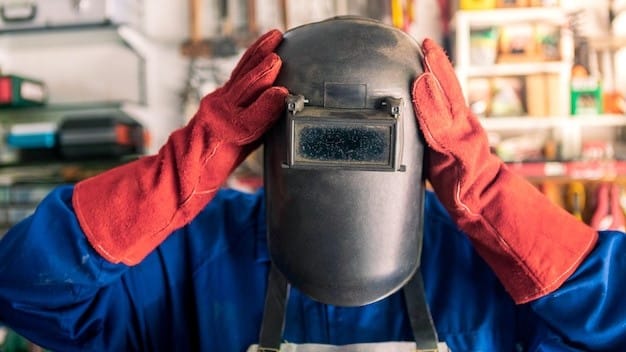
Personal Protective Equipment (PPE) is the last defense against welding fumes. Respirators, particularly those that provide air-purifying elements, are critical when engineering and administrative controls cannot reduce exposure to acceptable levels. Along with respirators, protective clothing, gloves, and goggles shield the welder from direct contact with harmful particles and gases produced during welding, ensuring a safer working environment.
Welding Techniques and Fume Emissions
Welding Technique | Typical Fume Types | Volume of Fumes Produced | Fume Control Necessity |
MIG | Iron, aluminum, stainless steel | High | High |
TIG | Aluminum, magnesium | Low | Low |
Stick | Iron, chromium, manganese | Moderate | Moderate |
Flux-cored Arc | Iron, manganese, nickel | High | High |
Selecting Low-Fume Welding Consumables
Low-fume welding consumables are specifically designed to reduce the amount of hazardous fumes produced during welding processes. Some common types of low-fume consumables include:
- Low-manganese tungsten welding electrodes reduce manganese exposure, which is critical given its neurological impacts.
- Among types of MIG welding wires, flux-cored wires are engineered to produce fewer fumes and are ideal for environments where ventilation is a concern.
- Gas-Shielded Arc Welding Consumables use specific gases that minimize the generation of harmful airborne particles.
Benefits of Using Low-Fume Consumables
Using low-fume welding consumables offers significant health and environmental benefits. Firstly, they greatly reduce welders’ inhalation risks by minimizing the release of toxic metals and gases. This improves immediate working conditions and contributes to long-term health benefits by decreasing the risk of respiratory diseases and cancer.
These consumables contribute to cleaner and safer workshop air quality, aligning with more stringent environmental regulations and workplace safety standards. Additionally, using these consumables can lower ventilation costs and reduce the need for expensive fume extraction systems.
Fume Control Measures and Their Effectiveness
Fume Control Measure | Effectiveness | Considerations |
Local Exhaust Ventilation (LEV) | High | Requires regular maintenance and correct positioning |
Respirators | Moderate | Type of respirator must match the specific hazards |
Substitution | Variable | Depends on the availability of less-toxic materials |
Welding Booths/Enclosures | High | Requires adequate space and setup |
Advanced Technology to Reduce Fumes
Remote Control
Remote control technology in welding operations allows operators to perform tasks from a distance, significantly reducing their exposure to harmful fumes. This technology enhances safety and improves precision in welding tasks, as operators can work from a vantage point that provides better visibility and control.
Automation
Automation in welding includes using robotic systems that handle the welding process without direct human intervention. By automating welding tasks, workers’ exposure to toxic fumes is minimized. Additionally, automated systems can be configured to optimize welding parameters that reduce fume production, such as adjusting voltage and speed.
Computer Vision
Computer vision technology supports automated systems by enabling precise monitoring and adjustments during welding. It helps detect and control the amount of fumes generated by automatically adjusting the welding parameters. This ensures optimal operation conditions that maintain quality and uphold stringent safety standards by minimizing hazardous emissions.
Final Thoughts
Managing welding fumes effectively is crucial for maintaining a safe and healthy work environment. Integrating advanced technologies such as automation, remote control, and computer vision with traditional methods like low-fume consumables and proper ventilation systems offers comprehensive solutions. Also pay attention to the welder’s quality, which requires a reliable welding equipment supplier.
These practices protect workers’ health, enhance operational efficiency, and ensure compliance with strict regulatory standards. Emphasizing continuous improvement and adopting these measures is key to advancing workplace safety in the welding industry.
FAQs
What are the health risks associated with welding fumes?
Welding fumes contain a variety of metals and gases that can cause respiratory issues, metal fume fever, and long-term health conditions like lung cancer and neurological damage.
How can welding fumes be controlled in the workplace?
Controlling welding fumes involves using local exhaust ventilation (LEV), ensuring proper use of personal protective equipment (PPE), and implementing safe work practices.
What personal protective equipment (PPE) should be used to protect against welding fumes?
PPE such as respirators, welding helmets with appropriate filtration, and protective clothing are essential to minimize inhalation and skin exposure to hazardous fumes.
Are there legal requirements for managing welding fumes?
Yes, regulations such as OSHA in the USA and HSE in the UK set exposure limits and safety requirements for controlling welding fumes in the workplace.
What are the effects of long-term exposure to welding fumes?
Long-term exposure can lead to serious health issues, including chronic respiratory conditions, cardiovascular diseases, and cancer. Employers are required to monitor and limit exposure to protect workers’ health.