Welding is a critical process in manufacturing and construction, but it often faces challenges due to varying material properties. One significant issue is the influence of material melting points on welding quality and efficiency. Different materials have different melting points, affecting the choice of welding techniques and equipment. To address this problem, understanding the melting points of metals and their impact on welding is essential. This knowledge helps select appropriate welding methods, ensure strong and reliable joints, and avoid common issues like burn-through or cracking.
Understanding Melting Point
The melting point is the temperature at which a solid material transitions to a liquid state. This temperature is crucial in welding, as it determines how a material behaves under heat. Several factors influence the melting point of materials, including atomic structure, bonding type, and impurities. For instance, metals with strong atomic bonds, like tungsten, have high melting points, while those with weaker bonds, like aluminum, melt at lower temperatures.
Understanding these temperatures helps select the right welding technique, ensuring the material is heated appropriately without causing damage or weakening the weld.
Melting Points of Common Metals Used in Welding
Material | Melting Point (°C) |
Aluminum | 660 |
Steel | 1370 |
Copper | 1085 |
Gold | 1064 |
Iron | 1538 |
Lead | 327 |
Tungsten | 3422 |
Melting Point in Welding
The melting point of a material is a critical factor in determining the appropriate welding technique. In welding, the goal is to join materials by melting and fusing them. Different materials have different melting points, influencing the choice of welding method to ensure a strong and durable bond.
For materials with high melting points, such as steel or tungsten, TIG (Tungsten Inert Gas) welding is often preferred. TIG welding machine provides precise control over the heat input, making it suitable for materials that require high temperatures to melt. This technique is also used when welding thin materials, allowing for better control and reducing the risk of burn-through.
On the other hand, MIG (Metal Inert Gas) welding is commonly used for materials with lower melting points, such as aluminum or copper. MIG welding machine is faster and more efficient for these materials, as it provides a continuous feed of filler material that helps maintain the weld pool and prevents overheating.
Stick welding, or Shielded Metal Arc Welding (SMAW), is versatile and can be used for various materials with varying melting points. It is often employed when precise control is less critical, such as in construction or repair work.
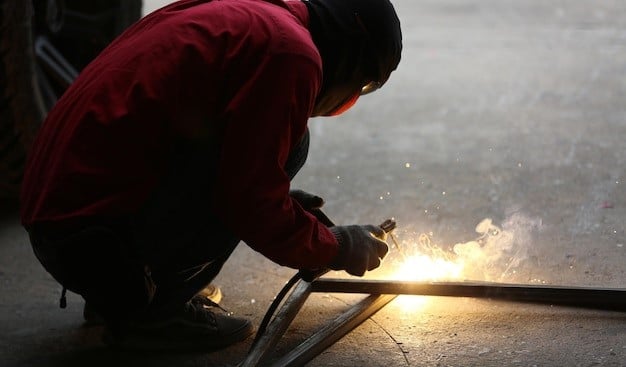
High Melting Point Materials
High melting point materials, such as tungsten and titanium, are commonly used in industries requiring extreme durability and resistance to heat. Tungsten, with a melting point of 3422°C, is often utilized in aerospace and military applications. Titanium, melting at 1668°C, is favored in medical devices and chemical processing due to its strength and corrosion resistance. While these materials offer significant benefits, they pose unique welding challenges.
Increased Energy Requirements
Welding high melting point materials demands significantly higher energy input than materials with lower melting points. The welding equipment must generate sufficient heat to melt these tough metals, which requires specialized machinery and a reliable welding equipment supplier. This necessity for higher energy can lead to longer weld times and greater operational costs.
Potential for Cracking
Another challenge when welding high melting point materials is the potential for cracking. These materials often have low thermal conductivity, meaning they don’t dissipate heat evenly. This can cause localized overheating, leading to thermal stresses and cracking during the cooling process. To mitigate this risk, welders must carefully control the heat input and cooling rate, often employing preheating or post-weld heat treatments.
Oxidation Risks
High melting point materials like titanium are prone to oxidation at elevated temperatures. When exposed to air during welding, these materials can form oxide layers that weaken the weld and reduce corrosion resistance. To prevent oxidation, inert gas shielding (such as argon or helium) is often used to protect the weld pool from exposure to air.
Low Melting Point Materials
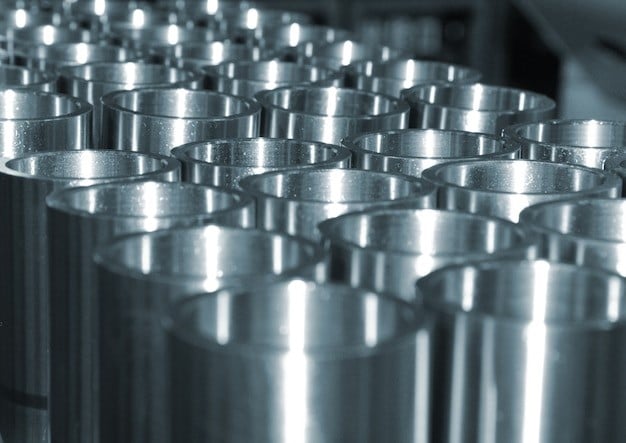
Low melting point materials, such as aluminum and lead, are widely used in various industries due to their ease of workability and lightweight. Aluminum, with a melting point of around 660°C, is common in automotive and aerospace applications. Lead, melting at 327°C, is often used in battery manufacturing and radiation shielding. Despite their advantages, these materials present unique challenges during welding.
Excessive Melting
One of the primary challenges in welding low melting point materials is excessive melting. Due to their low melting temperatures, these materials can easily overheat, leading to excessive melting of the base material. This can cause weak joints or destroy the material if not carefully controlled. Proper heat management and selecting appropriate welding techniques are crucial to avoid this issue.
Burn-Through
Burn-through is another significant concern when welding low melting point materials. Because these materials require less heat to melt, they are more prone to burning through during the welding process, especially when using high-energy welding methods. To prevent burn-through, welders must reduce the heat input and use techniques for greater control over the weld pool.
Distortion and Warping
Low melting point materials are also susceptible to distortion and warping due to the heat applied during welding. The rapid heating and cooling of the material can cause uneven expansion and contraction, leading to warping or misaligning of the welded parts. To minimize distortion, it is essential to use controlled heating techniques and consider preheating the material.
How to Avoid Temperature-Related Problems in Welding
Temperature plays a critical role in determining the quality of a weld. Excessive and insufficient heat can lead to welding defects, such as cracking, warping, and weakened joints. When the temperature is too high, it can cause the material to melt excessively, leading to burn-through or distortion. On the other hand, insufficient heat might result in poor fusion between the materials, creating weak joints prone to failure. Managing the temperature during welding is crucial to ensure the integrity and strength of the welded structure.
To avoid temperature-related problems in welding, several methods can be employed:
Preheating the Material
Preheating the material before welding can help reduce the risk of cracking, especially in materials with high melting points or thermal stress. Preheating ensures that the material’s temperature is more uniform, reducing the thermal gradient and minimizing the chances of distortion or cracking during the welding process.
Controlling Heat Input
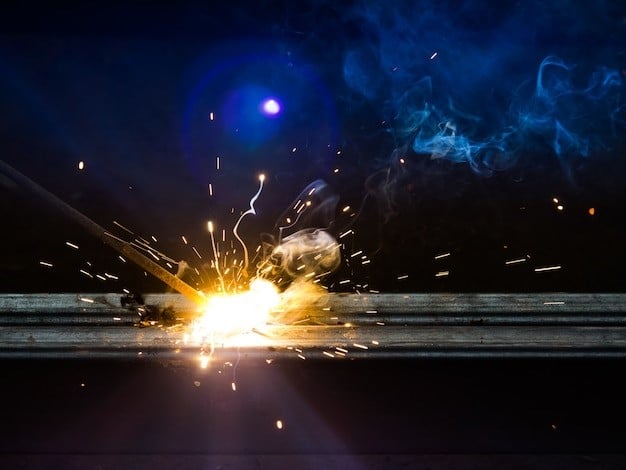
Proper heat input control is essential to avoid excessive melting or burn-through. This can be achieved by adjusting the welding parameters, such as voltage, current, and travel speed, to ensure that the heat applied is sufficient to melt the material without causing damage. Lower heat inputs for thin materials and higher for thicker sections help maintain the weld quality.
Using Appropriate Welding Techniques
Selecting the material’s welding technique and melting point is critical in managing temperature-related issues. For example, TIG welding provides precise heat control, making it suitable for materials with both high and low melting points. With its continuous feed, MIG welding can help maintain a consistent temperature in the weld pool, reducing the risk of overheating.
Post-Weld Heat Treatment
Post-weld heat treatment (PWHT) can relieve residual stresses and improve the weld’s mechanical properties after welding. This process involves heating the welded material to a specific temperature and then cooling it at a controlled rate. PWHT is particularly useful for high melting point materials prone to cracking or applications with critical weld strength and toughness.
Inert Gas Shielding
Using inert gas shielding, such as argon or helium, can prevent oxidation and contamination of the weld pool, especially in materials like titanium that are sensitive to temperature-related oxidation. The shielding gas creates a protective environment around the weld, ensuring a cleaner and stronger weld.
Monitoring and Adjusting Welding Parameters
Continuous monitoring of welding parameters during the process is essential to avoid temperature fluctuations that could affect the weld quality. Welders should be trained to recognize overheating or insufficient heat and adjust the parameters accordingly to maintain a consistent temperature throughout the weld.
Material and Potential Welding Challenges
Material | Melting Point (°C) | Suitable Welding Techniques | Potential Challenges |
Steel (Carbon) | 1425 – 1540 | Arc Welding (MIG, TIG), Resistance Welding | High heat can cause warping; oxidation without shielding gas |
Aluminum | 660 | TIG Welding, MIG Welding | High thermal conductivity; oxide layer requires cleaning |
Stainless Steel | 1375 – 1400 | TIG Welding, MIG Welding | Susceptible to distortion; requires proper heat control |
Copper | 1085 | TIG Welding, Gas Welding | High thermal conductivity; requires preheating |
Titanium | 1668 | TIG Welding, Laser Welding | Reacts with oxygen/nitrogen; needs inert gas shielding |
Nickel Alloys | 1350 – 1400 | TIG Welding, MIG Welding | Prone to cracking; requires controlled heat input |
Cast Iron | 1150 – 1200 | Arc Welding, Gas Welding | High brittleness; needs preheating and slow cooling |
Magnesium | 650 | TIG Welding, MIG Welding | Highly flammable; requires careful heat management |
Brass | 900 – 940 | TIG Welding, MIG Welding | Zinc fumes can be toxic; they require proper ventilation |
Tungsten Carbide | 2870 | Brazing, TIG Welding | Very high melting point; requires specialized equipment |
Final Thoughts
The melting points of materials are essential for successful welding. They influence the choice of welding techniques, heat management, and the overall quality of the weld. Professionals can avoid common issues like cracking, burn-through, and distortion by carefully selecting the appropriate methods and controlling the temperature during welding. Mastering these aspects not only ensures stronger, more reliable welds but also enhances the efficiency and safety of welding operations. Adapting to the specific needs of different materials will lead to better outcomes in any welding project.
FAQs
How does the melting point of a material affect welding techniques?
The melting point dictates the required heat and the suitable welding method, impacting the overall quality and integrity of the weld.
What are the challenges of welding high melting point materials like tungsten and titanium?
These materials need more energy, are prone to cracking, and may oxidize, requiring specialized techniques and careful heat control.
How can I prevent burn-through when welding low melting point materials?
Reduce heat input, use appropriate techniques like MIG welding, and maintain precise control over the weld pool.
What role does preheating play in welding?
Preheating minimizes the risk of cracking and distortion by ensuring uniform material temperature.
Why is post-weld heat treatment important for high melting point materials?
It relieves residual stresses and improves weld strength, reducing the risk of cracking.