Welding stainless steel presents unique challenges. The high thermal conductivity and expansion rate can cause warping and heat distortion. These factors demand precision in gas selection to ensure strong, clean welds without compromising the material. MIG welding, popular for its versatility and speed, is an ideal solution, but the right gas mixture is crucial for success.
Choosing the best gas for MIG welding stainless steel ensures a smooth, defect-free weld, maintaining the integrity and appearance of the material. Understanding these options makes all the difference in quality and efficiency.
MIG Welding Stainless Steel
Stainless steel has properties that make it both valuable and challenging to weld. Its high resistance to corrosion and durability makes it ideal for many industries, but its low thermal conductivity causes it to retain heat. This can lead to warping, making precise temperature control crucial during welding. Stainless steel also expands more than other metals when heated, increasing the chance of distortion.
The chromium content in stainless steel forms an oxide layer that protects it from rust, but welding can disrupt this layer. If not handled carefully, the welded area may become vulnerable to corrosion. Another challenge is the material’s tendency to crack under stress, especially when exposed to prolonged heat. Controlling heat input and using the right gas mix helps prevent these issues.
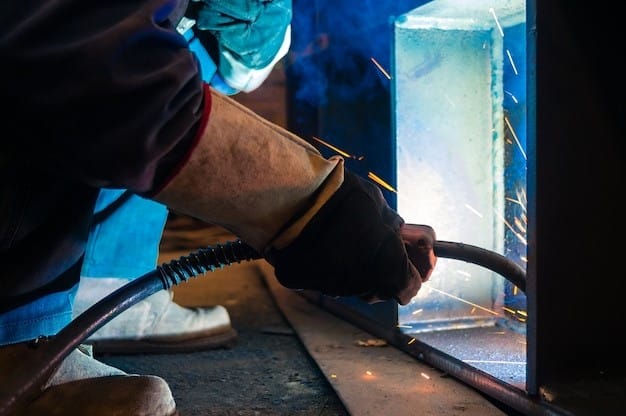
Gases Used in MIG Welding Stainless Steel
Pure Argon
Pure Argon is often for TIG welding machine but also plays a role in MIG welding stainless steel. However, Argon alone isn’t ideal for a MIG welding machine as it cannot stabilize the arc properly. While it produces a smooth arc and neat welds, it doesn’t penetrate deeply into the material. This can cause issues with thicker stainless steel sheets, limiting its use to thin applications.
Argon/Carbon Dioxide Mixtures (98% Argon / 2% CO2)
One of the most popular gas combinations for MIG welding stainless steel is a mix of 98% Argon and 2% Carbon Dioxide. This mixture provides better arc stability than pure Argon while offering a small penetration due to the Carbon Dioxide content. It helps create a cleaner weld with less spatter than other gas mixtures. This balance is often chosen for general stainless steel welding applications because it ensures a neat appearance and avoids oxidation at the weld site.
Tri-Mix Gas of Argon, Helium, and Carbon Dioxide
The Tri-Mix gas, which includes Argon, Helium, and Carbon Dioxide, is used when welding thicker stainless steel or in specific industrial applications. The presence of Helium increases the heat input, allowing for deeper penetration and faster welds, especially on thicker materials. The Argon maintains arc stability, while the small amount of Carbon Dioxide improves weld fluidity. This mixture is ideal for projects requiring precision and high strength. However, it can be more expensive, so it’s generally reserved for critical applications where weld quality is paramount.
Table Explaining the Gas Mixtures for MIG Welding Stainless Steel
Gas Mixture | Best Application | Advantages | Disadvantages |
Pure Argon | Thin stainless steel | Stable arc, clean welds | Limited penetration |
98% Argon / 2% Carbon Dioxide | General stainless steel welding | Good arc stability, minimal spatter | Limited penetration for thicker material |
Tri-Mix (Argon, Helium, Carbon Dioxide) | Thick stainless steel | Deep penetration, faster welding | Higher cost, less availability |
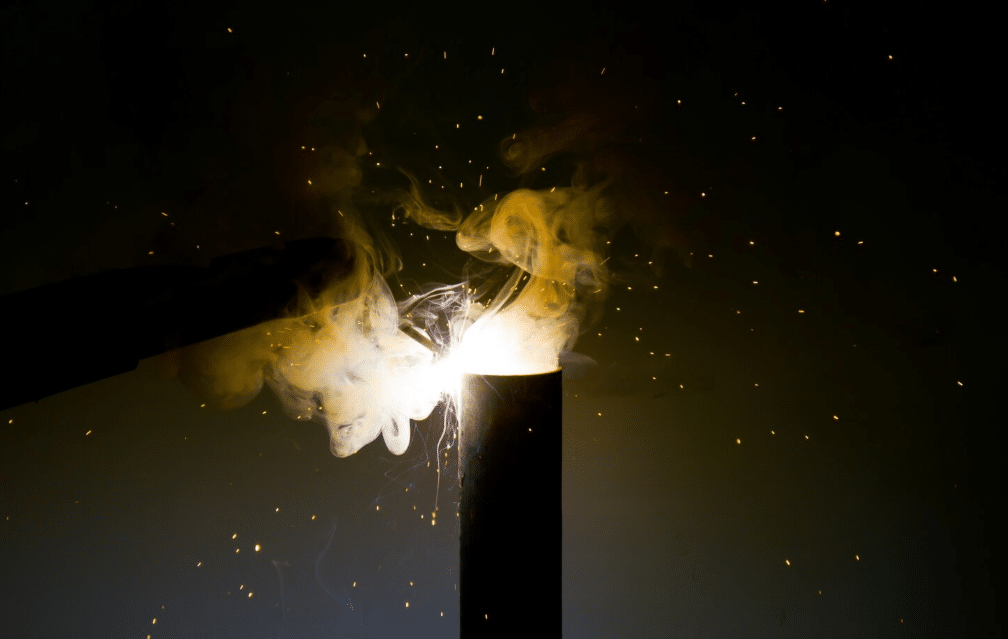
Why Welding Stainless Steel Without Shielding Gas Is Not Recommended
While it is technically possible to MIG weld stainless steel without shielding gas by using self-shielded flux-cored arc welding (FCAW) wire, this approach is generally not advisable. Stainless steel is more sensitive to oxidation and contamination than many other metals, and without proper shielding, the weld area remains exposed to oxygen, nitrogen, and moisture in the atmosphere. This can lead to multiple problems:
- Loss of Corrosion Resistance – High heat during welding can damage the chromium oxide layer that protects stainless steel from rust. Without shielding gas, this layer cannot reform properly, leaving the welded joint vulnerable to corrosion.
- Porosity and Weak Welds – Atmospheric gases can become trapped inside the molten weld, creating pores that weaken the joint and reduce its overall durability.
- Excessive Spatter and Poor Appearance – Lack of shielding gas can cause arc instability, producing more spatter and irregular bead profiles, which is especially undesirable for applications requiring a clean, aesthetic finish.
Although self-shielded flux-cored wires generate their own protective gas as the flux burns, this shield is often insufficient for stainless steel due to the material’s high heat retention and chemical reactivity. For strong, visually appealing, and long-lasting welds, it is highly recommended to use an appropriate shielding gas mixture—such as 98% argon with 2% carbon dioxide for general applications, or a tri-mix of argon, helium, and carbon dioxide for thicker materials—when MIG welding stainless steel.
Understanding why shielding gas is essential and which mixtures are recommended naturally leads to the next question: how do you choose the best gas for your specific stainless steel MIG welding application?
What Is the Best Gas for MIG Welding Stainless Steel
Choosing the best gas for MIG welding stainless steel depends on several factors, each affecting the weld’s quality and efficiency. Factors such as material thickness, welding position, weld quality, cost, and gas availability play crucial roles in this decision-making process. Selecting the correct gas can prevent defects like excessive spatter, oxidation, and poor penetration, ensuring strong, reliable welds.
Material Thickness
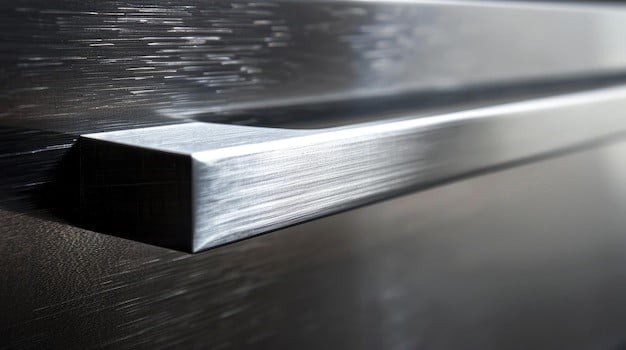
The thickness of the stainless steel significantly influences the gas choice. Thicker materials require more heat to ensure proper penetration, while thinner materials can warp if exposed to too much heat. A tri-mix gas containing Argon, Helium, and Carbon Dioxide is often recommended for thick materials. Helium increases heat input, allowing the welder to achieve deeper penetration. However, a 98% Argon and 2% Carbon Dioxide mixture is preferred for thinner sheets because it provides sufficient penetration without causing warping or distortion.
- Thick stainless steel: Tri-mix gas (Argon, Helium, and Carbon Dioxide) for deeper penetration.
- Thin stainless steel: 98% Argon and 2% Carbon Dioxide for less heat and minimal warping.
Welding Position
Different welding positions affect the gas selection. Positions like vertical or overhead require greater arc stability to avoid running or sagging of the weld. In these cases, a gas mix that promotes a more stable arc, such as Argon with a small amount of Carbon Dioxide, is ideal. Flat welding positions are more forgiving and may allow for a wider range of gas options, including pure Argon or Argon mixtures.
- Flat position: Pure Argon or Argon mixes work well due to ease of control.
- Vertical/Overhead positions: 98% Argon and 2% Carbon Dioxide or a tri-mix for better arc stability.
Desired Weld Quality
Selecting the right gas mixture is essential for high-quality welds where aesthetics are crucial. Stainless steel, often used in industries where appearance and corrosion resistance are vital, requires clean, spatter-free welds. A tri-mix gas can achieve excellent results, offering deeper penetration and smoother weld surfaces. However, a 98% Argon and 2% Carbon Dioxide mix provides sufficient weld quality for general applications where aesthetics aren’t as critical.
- Aesthetic welds: Tri-mix gas for smooth and visually appealing welds.
- General applications: 98% Argon and 2% Carbon Dioxide for satisfactory quality.
Costs
Cost is an essential factor when choosing welding gases. Pure Argon is typically less expensive than more complex mixtures, but it may not always offer the desired results for stainless steel welding. Tri-mix gases, while providing superior weld quality, are generally more costly due to the inclusion of Helium. Balancing cost and weld quality is crucial, particularly in large-scale projects with high gas consumption. The Argon and Carbon Dioxide mix offers an affordable yet effective solution for small-scale projects or budget-conscious operations.
- High budget/High quality: Tri-mix gases for top-tier results.
- Lower budget: Argon and Carbon Dioxide mix for a cost-effective alternative.
Gas Availability
Finally, the availability of the gas mixture must be considered. Not all welding gas suppliers may stock specialized mixtures like tri-mix gases. Argon and Carbon Dioxide mixtures are more readily available in some regions, making them the more practical option for MIG welding stainless steel. Availability can influence project timelines and costs, so selecting a gas that is both effective and easy to source is essential.
- Readily available gases: Argon and Carbon Dioxide mixtures are commonly found.
- Specialty gases: Tri-mix may require special ordering or sourcing from specific suppliers.
Key Factors for Gas Selection in MIG Welding Stainless Steel
Factor | Considerations | Recommended Gas Mixture |
Material Thickness | Thin or thick stainless steel | Argon/CO2 mix for thin, Tri-mix for thick |
Welding Position | Flat, vertical, or overhead | Argon/CO2 mix for vertical, Tri-mix for overhead |
Weld Quality | Aesthetic finish or general strength | Tri-mix for aesthetic, Argon/CO2 mix for general |
Cost | Budget limitations and gas price | Argon/CO2 mix for cost-effective, Tri-mix for premium |
Availability | Local supply of gases | Argon/CO2 more common, Tri-mix specialized |
Key Points for MIG Welding Stainless Steel
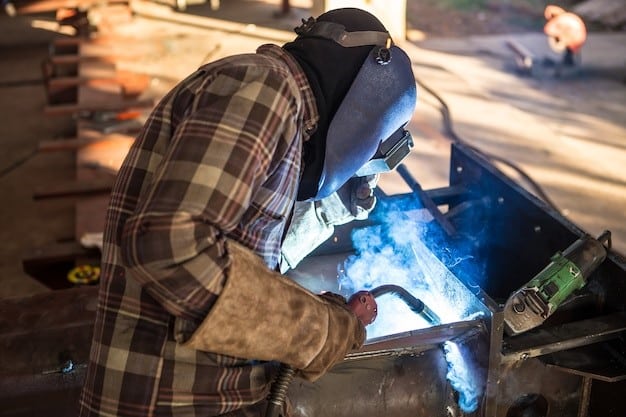
Gas Flow Rate
Maintaining the correct gas flow rate ensures the shield around the weld. Too much gas flow can lead to turbulence, introducing air into the weld, while too little can result in poor shielding, causing oxidation. A 20-30 cubic feet per hour flow rate is generally recommended for stainless steel.
Welding Techniques
Proper technique is crucial in MIG welding stainless steel. The welder should use a steady hand and ensure a consistent arc length. Short circuit transfer and spray transfer are popular methods, depending on the thickness of the material.
Safety Precautions
Welding stainless steel produces hazardous fumes, so proper ventilation and protective gear are vital. Welders must wear suitable protective clothing, including welding gloves and a welding helmet, to prevent burns and eye injuries.
Final Thoughts
MIG welding stainless steel requires careful planning and execution, especially when selecting the right gas mixture. Each aspect, from material thickness to weld position and gas availability, is vital in achieving the best results. Understanding the properties of stainless steel, using the right equipment from reliable welding machine suppliers and the correct techniques can improve weld quality and efficiency. While choosing the right gas may involve balancing cost and availability, investing in the proper gas mixture ensures stronger, more reliable welds, making it a critical factor in successful stainless steel welding.
Related Products
FAQs About Shielding Gas for MIG Welding Stainless Steel
What is the best gas for MIG welding stainless steel?
The best shielding gas for MIG welding stainless steel often depends on the material’s thickness and the desired weld quality. A common choice is a 98% Argon and 2% Carbon Dioxide mix, while a tri-mix with Argon, Helium, and Carbon Dioxide is preferred for thicker stainless steel sections.
Can I use pure Argon for MIG welding stainless steel?
Pure Argon is not ideal for MIG welding stainless steel. While it provides arc stability, it does not deliver the penetration or weld pool fluidity required for high-quality stainless steel welds.
What gas mixture is suitable for thick stainless steel?
A tri-mix shielding gas of Argon, Helium, and Carbon Dioxide is typically used for MIG welding thick stainless steel because it increases heat input, penetration, and weld speed.
What shielding gas is best for MIG welding thin stainless steel?
For thin stainless steel sheets, a 98% Argon and 2% Carbon Dioxide shielding gas mix is ideal. It offers stable arc control, minimal spatter, and reduces the risk of heat distortion during MIG welding.
How does the gas flow rate affect MIG welding stainless steel?
The shielding gas flow rate should be carefully controlled, with 20–30 cubic feet per hour being the standard for MIG welding stainless steel. Too much or too little shielding gas can result in poor arc stability, oxidation, and weld defects.
Does the stainless steel grade affect shielding gas selection for MIG welding?
Yes. Austenitic stainless steels usually work well with argon-rich shielding gas mixtures, while ferritic and martensitic stainless steels may require adjustments in gas composition to optimize penetration and bead quality in MIG welding applications.