In the dynamic field of welding, the versatility and strength of mild steel make it a preferred material for a range of applications, from simple home repairs to complex industrial constructions. However, the diversity of mild steel types and their specific welding requirements often pose challenges for welders, leading to potential inefficiencies or material mismatches.
To address these challenges, understanding the unique properties and appropriate welding techniques for different types of mild steel is crucial. This knowledge ensures the selection of the right materials and methods, enhancing the durability and quality of the welds while optimizing performance across various welding projects.
What is Mild Steel
Mild steel, a common carbon steel, is known for its low carbon content, typically between 0.05% and 0.20%. This composition makes it more ductile and malleable, allowing easier manipulation in various industrial applications. Adding carbon can enhance the strength of mild steel, although this reduces its weldability.
It is widely used due to its affordability and ability to be welded easily, making it suitable for building infrastructure, automotive bodies, and home appliances. The balance of strength and ductility in mild steel makes it an invaluable resource in manufacturing and construction, fulfilling demands for flexibility and durability in metal works.
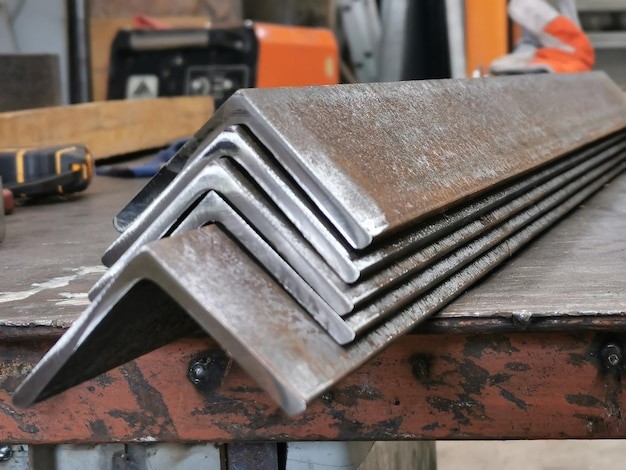
Mild Steel vs. Carbon Steel
Mild steel, often called low-carbon steel, contains a lower percentage of carbon than other types of carbon steel. This difference in carbon content significantly influences the material’s hardness and strength. Mild steel typically has a carbon content of 0.05% to 0.20%, making it more ductile and easy to form. In contrast, carbon steel can have a carbon content as high as 1.5%, providing higher hardness but less ductile than mild steel. This makes carbon steel better suited for tools and cutting implements where hardness is essential.
Mild Steel vs. Stainless Steel
When comparing mild steel to stainless steel, the key differentiator is the presence of chromium in stainless steel. Stainless steel contains a minimum of 10.5% chromium, which forms a protective layer of chromium oxide on the steel’s surface. This layer grants it a high resistance to corrosion and staining, making stainless steel ideal for environments that are aggressive chemically or climatically. Mild steel, lacking this chromium content, does not offer the same resistance to corrosion, which limits its utility in outdoor or corrosive environments. However, mild steel is more cost-effective and easier to weld than stainless steel, which requires specific welding techniques due to its varying chromium content and other alloying elements.
Common Types of Mild Steel in Welding
Low Carbon Mild Steel
Low-carbon mild steel, with less than 0.3% carbon content, is the most widely used welding type. This minimal carbon presence ensures better weldability and ductility than higher-carbon steels. It’s commonly used in manufacturing and structural applications requiring bending and forming. The ease of welding and forming makes low-carbon mild steel ideal for automotive body panels, construction frames, and piping systems.
Medium Carbon Mild Steel
Medium carbon mild steel typically contains about 0.3% to 0.6% carbon, making it stronger and harder than its low carbon counterpart. This increased strength and hardness enhance wear resistance but can reduce the material’s weldability. It often requires pre-heating and post-heating to avoid cracking during the welding process. Medium carbon mild steel is frequently used in manufacturing gears, rails, and structural components where higher strength and toughness are required.
High Strength Low Alloy (HSLA) Steel
High Strength Low Alloy (HSLA) steel is mild steel that includes small amounts of alloying elements such as vanadium, niobium, or titanium, which enhance its strength without significantly increasing its weight. HSLA steels maintain good formability and weldability while providing a higher strength-to-weight ratio than conventional mild steels. These properties make HSLA steel suitable for structural applications such as bridges, buildings, and vehicle frames, where strong, lightweight materials are crucial.
Welding Methods for Mild Steel
Welding mild steel involves various techniques that cater to its different forms, from low carbon to high strength low alloy (HSLA) steel. Each mild steel type has unique properties requiring specific welding methods to ensure optimal durability and structural integrity. Understanding these methods allows for better planning and execution of welding projects.
MIG Welding (Metal Inert Gas)
A MIG welder is a popular choice for welding mild steel, especially low-carbon varieties, due to its efficiency and the high quality of the welds it produces. This process uses a wire-feeding gun emitting gas to shield the weld area from contamination. It’s particularly useful for its speed in welding thin or thick sections and is favored for manufacturing and home repair due to its versatility and relative ease of learning.
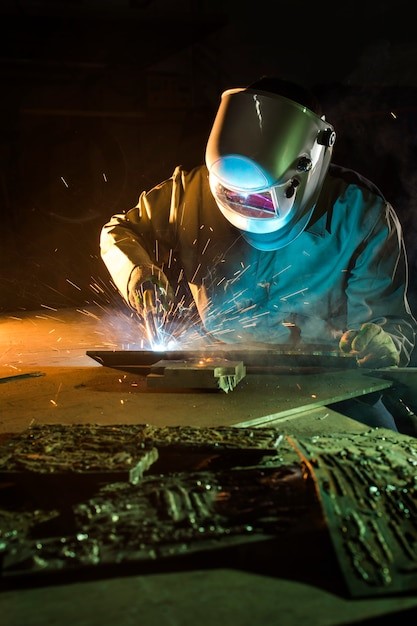
TIG Welding (Tungsten Inert Gas)
TIG welding is often preferred for medium carbon mild steel because it can precisely control the weld and create strong, clean welds. Using a TIG welder often needs non-consumable tungsten welding electrodes to produce the weld and is excellent for tasks requiring detailed workmanship on smaller or more intricate pieces. TIG welding is appreciated for its aesthetic finish and is commonly used in automotive and artistic applications.
Stick Welding (Shielded Metal Arc Welding)
Stick welding is effective across all types of mild steel and is known for its simplicity and the robustness of the welds it produces. A stick welder uses an electric current to form an arc between the stick and the metal, melting the stick and bonding the pieces. This method is particularly valuable for outdoor welding, as it does not require external shielding gas and can withstand various environmental factors.
Flux-Cored Arc Welding (FCAW)
This method is similar to MIG welding but uses a special tubular wire filled with flux. It can be used with or without shielding gas, making it flexible in all environments, including windy conditions. FCAW is well-suited for HSLA steel, providing deep penetration and a high deposition rate, which speeds up the welding process while maintaining strength and durability.
Type of Mild Steel | Recommended Welding Method |
Low Carbon Mild Steel | MIG, TIG |
Medium Carbon Mild Steel | TIG, Stick |
High Strength Low Alloy (HSLA) Steel | MIG, Flux-Cored Arc Welding |
Selecting the Right Mild Steel for Welding
Selecting the appropriate type of mild steel for welding projects is crucial to ensuring the final product’s structural integrity, durability, and performance. Factors such as thickness, application, strength requirements, and specific steel grades must be carefully considered to match the project’s demands with the steel’s properties.
Considering Thickness and Application
The thickness of the steel plays a significant role in determining the suitable welding method and the type of mild steel used. Thinner sheets of mild steel, typically low-carbon steel, are commonly used in automotive body panels and require precise welding techniques such as TIG or MIG welding to avoid warping. For thicker sections, such as structural beams, higher-carbon mild steel might be appropriate to ensure strength and durability, using stick welding or flux-cored arc welding.
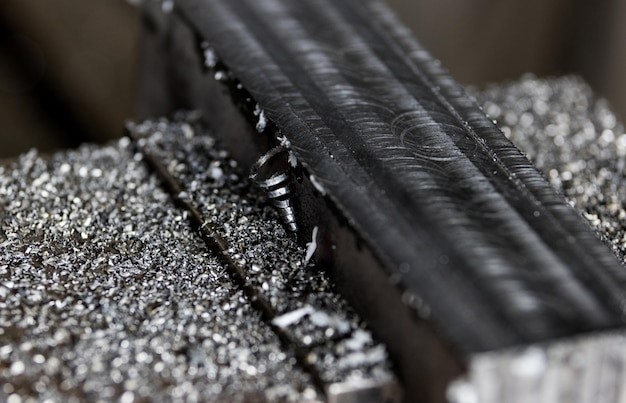
Strength Requirements
The required strength of the weld joint is a critical consideration. High Strength Low Alloy (HSLA) steels are often selected for projects needing higher tensile strength without compromising ductility. These steels are ideal for critical load-bearing structures due to their enhanced performance compared to regular mild steel. Understanding the specific stress conditions a project will encounter can guide the selection of an alloy that provides the necessary resistance to fatigue, wear, and failure.
Mild Steel Grades and Their Applications
Different grades of mild steel, such as ASTM A36, are standard for general structural purposes and offer good weldability, strength, and formability. For more demanding applications, higher grades like ASTM A572 Grade 50 come into play, which provides greater strength while remaining formable. The choice of grade should align with the mechanical demands of the project to ensure that the steel can perform under the expected loads and environmental conditions.
Common Challenges in Welding Mild Steel
- Porosity in Welds: One of the most frequent issues when welding mild steel is porosity, which is the presence of trapped gas in the weld metal. This can weaken the weld and is often caused by contamination on the metal’s surface or in the welding environment.
- Excessive Spatter: Welding mild steel, especially with certain methods like MIG welding, can produce excessive spatter. This not only affects the appearance of the weld but also results in a loss of material and requires additional cleanup time.
- Warping of the Steel: Due to its low melting point, mild steel is particularly susceptible to warping and distortion during welding. This is exacerbated when high heat is applied, which is necessary for proper fusion.
- Cracking: Cracks can occur in the weld or the heat-affected zone surrounding the weld. These are typically the result of rapid cooling, which can be managed by controlling the welding speed and pre-heating the metal.
- Difficulty in Achieving Strong Welds with Thick Materials: While mild steel is generally easy to weld, thicker pieces require more careful heat management to penetrate deeply without adversely affecting the metal’s integrity.
- Corrosion Susceptibility: Unlike stainless steel, mild steel does not inherently resist corrosion unless treated or painted. This makes applying proper finishes to welded structures exposed to corrosive environments is crucial.
Welding Challenge | Solution/Preventative Measure |
Porosity | Use clean and dry base metal, ensure gas flow is correct |
Spatter | Use clean and dry base metal, and ensure gas flow is correct |
Warping | Pre-heat the metal, control the heat input during welding |
Cracking | Pre-heat the metal, ensure proper electrode selection |
Corrosion Susceptibility | Apply protective finishes, use corrosion-resistant welding wire |
Final Thoughts
Despite its challenges, welding mild steel remains a cornerstone in fabrication and construction due to its versatility and cost-effectiveness. Understanding the different types of mild steel and the appropriate welding methods can significantly enhance the quality and strength of welds. Welders must consider the steel’s thickness, intended application, and environmental exposure to choose the correct type and grade of steel. Also, choosing the right welding machine from a reliable welding equipment supplier matters for the welding outcome.
Addressing common issues like porosity, spatter, and warping and employing preventive measures such as proper cleaning and controlled heat application can optimize the durability and appearance of mild steel welds. Ultimately, success in welding mild steel lies in meticulous preparation, selecting the right materials, and mastering the welding techniques tailored to each project’s needs.
FAQs
What are the main safety precautions when welding mild steel?
Wear appropriate personal protective equipment such as a welding helmet, welding gloves, and protective clothing. Ensure the workspace is well-ventilated to avoid inhaling harmful fumes.
What are the dangers associated with welding?
Welding can present risks such as fire or explosions, exposure to harmful fumes and gases, and possible electrical shock.
How do I improve my welding skills?
Practice welding on different types of metal and thicknesses, learn various welding techniques and attend workshops or classes to enhance knowledge and practical skills.
What are the differences between welding mild steel and stainless steel?
Mild steel is generally easier to weld than stainless steel, which requires specific techniques due to its higher nickel and chromium content. Stainless steel welding often demands specialized filler metals and more precise heat control to prevent warping or corrosion.