Industrial welding often requires versatility and efficiency, but traditional single-function welding machines can limit productivity and increase operational costs.
For businesses handling diverse welding tasks, managing multiple specialized machines can complicate workflows and inflate budgets. This challenge becomes even more critical for B2B buyers and distributors looking to optimize operations across varied industries.
Multi-process welding machines provide an effective solution to this problem. Combining multiple welding methods, such as MIG, TIG, and stick welding, in one device streamlines operations and reduces the need for separate equipment.
These welders from welding machine suppliers save space and improve cost-efficiency and adaptability, making them a preferred choice for distributors and manufacturers serving dynamic industrial needs.
What is a Multi-Process Welder and Who Benefits
A multi-process welder is a versatile machine that integrates multiple welding processes into a single unit. It is designed to handle various welding tasks, including MIG (Metal Inert Gas), TIG (Tungsten Inert Gas), and stick welding. This adaptability makes it a valuable tool for construction, manufacturing, and automotive repair businesses.
These machines are especially beneficial for B2B buyers and distributors catering to customers with diverse requirements. Distributors can meet demand more efficiently by offering a solution that addresses various welding needs while reducing inventory complexity. Small businesses and large-scale industrial operations benefit from the cost savings and operational flexibility multi-process welders provide.
How Does a Multi-Process Welder Work
Multi-process welders function by integrating multiple welding technologies into a single unit, allowing operators to switch seamlessly between different welding methods.
These machines use advanced inverters and software-controlled systems to manage power output and welding parameters. This flexibility enables the machine to handle various materials and welding techniques efficiently.
The core of the technology lies in its ability to modify the current type and voltage to suit specific welding processes. For example, it can provide a constant voltage as that from a MIG welder or a steady current as a stick welder. This adaptability ensures optimal performance across different tasks.
The machine’s control panel simplifies operation by offering pre-set configurations for common welding types. Users can easily adjust parameters such as amperage and wire feed speed, ensuring precision for diverse projects. This user-friendly approach reduces the learning curve and enhances productivity.
Multi-process welders have components like dual gas inputs and quick-change torch connections. These features allow users to switch processes quickly without extensive setup changes, saving time and improving workflow efficiency. This versatility makes them an essential tool for businesses needing reliable, all-in-one welding solutions.
Key Features Comparison of Multi-Process Welders
Feature | Description |
Welding Processes | Supports MIG, TIG, and Stick welding |
Control Systems | Advanced inverter and software-controlled systems |
Portability | Lightweight and compact models available for on-site welding |
Maintenance Requirements | Requires regular upkeep to maintain consistent performance |
Cost Efficiency | Reduces the need for multiple machines, saving initial and operational costs |
User Interface | Simplified control panels with pre-set configurations for various welding processes |
Are Multi-Process Welders Worth It
Multi-process welders are valuable for many users due to their versatility and cost-effectiveness. These machines eliminate the need for multiple devices for hobbyists, allowing them to experiment with various welding techniques without significant additional costs. This makes them ideal for personal projects and occasional repairs.
Small business owners benefit from the machine’s ability to handle diverse tasks with minimal downtime. By consolidating multiple functions into one unit, they can save on equipment expenses and optimize workspace efficiency. This streamlined approach is especially useful for workshops dealing with varied welding requirements.
Industrial welders gain the most from multi-process machines’ robust performance and reliability. These units are designed to handle high workloads, making them suitable for demanding applications across industries such as manufacturing and construction. The ability to switch quickly between processes enhances productivity and ensures high-quality results.
Due to their broad market appeal, multi-process welders represent a smart choice for distributors and buyers. Their adaptability ensures they meet the needs of diverse customer bases, from small-scale operations to large industrial projects. This wide applicability makes them a profitable addition to any product lineup.
Multi-Process Welders: Advantages
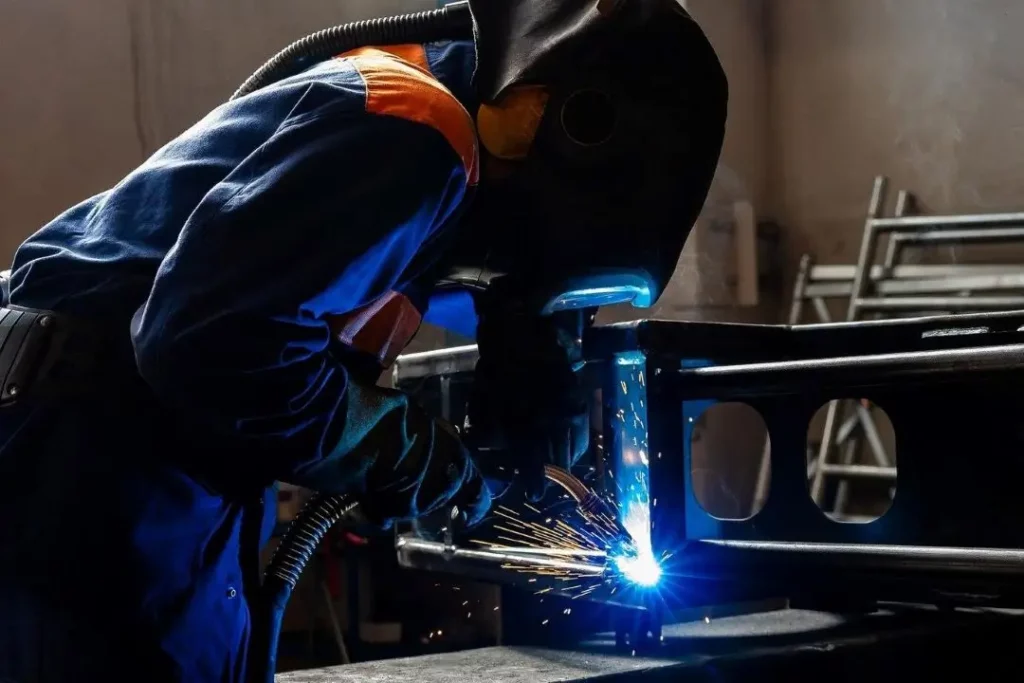
Cost Efficiency
Multi-process welders reduce the need for multiple machines, leading to significant cost savings. For businesses, this means a lower upfront investment while still having access to multiple welding methods. Additionally, the ability to perform various tasks with a single device minimizes maintenance and operational costs over time.
Versatility for Small Business
Small businesses often face the challenge of managing diverse welding projects with limited resources. A multi-process welder’s ability to handle different welding techniques makes it a practical choice. Whether it’s MIG, TIG, or stick welding, these machines provide the flexibility to meet client demands without requiring separate equipment.
Convenience and Efficiency
With their ability to switch seamlessly between welding processes, multi-process welders save time and simplify workflows. Operators can transition between tasks without the hassle of setting up multiple machines, improving overall efficiency. This convenience is especially beneficial for industries with tight production schedules.
Space-Saving
Multi-process welders offer a compact solution in workshops and factories with premium space. Combining multiple welding capabilities into one unit reduces clutter and frees up space for other essential tools and operations. This space optimization is valuable for small and large-scale operations alike.
Reduced Training Requirements
Using a multi-process welder simplifies operator training since workers only need to learn one machine’s functionality. This reduces the time and cost associated with training employees on multiple devices. For distributors and businesses, this advantage translates into quicker onboarding and improved workforce efficiency.
Enhanced Portability
Many multi-process welders are designed with portability in mind, featuring compact builds and lightweight designs. This makes them ideal for on-site welding jobs where mobility is crucial. Portable units ensure businesses deliver consistent performance across different locations, broadening their operational capabilities.
Multi-Process Welders: Disadvantages

Higher Initial Costs
Multi-process welders often come with a higher upfront cost compared to single-function machines. This can be a concern for businesses working with tight budgets. However, the long-term savings from reduced equipment purchases and maintenance can offset the initial investment.
Power Limitations
While multi-process welders offer versatility, they may lack the power output for heavy-duty industrial applications. For tasks requiring extremely high power, specialized machines may still be necessary. This limitation should be considered when planning for specific project needs.
Maintenance and Repair Costs
The complexity of multi-process welders can lead to higher maintenance and repair expenses. With more components integrated into a single unit, businesses might face increased downtime and costs when issues arise. Regular maintenance is essential to ensure consistent performance.
Weight
Although portable models exist, many multi-process welders are heavier than single-function machines. This added weight can make them less convenient to transport, especially for on-site jobs. Businesses should evaluate portability needs before selecting a model for their operations.
Advantages and Disadvantages of Multi-Process Welders
Advantages | Disadvantages |
Cost-effective | Higher initial cost |
Space-saving | May lack power for heavy-duty tasks |
Versatile for diverse projects | Increased maintenance complexity |
Reduces training requirements | Can be heavier than single-function machines |
Enhances efficiency | Potential repair costs due to integrated components |
Final Thoughts
YesWelder stands out as a reliable supplier of professional welding machines, offering high-quality multi-process welders tailored to the needs of wholesale buyers and distributors. Their machines are designed to meet the demands of various industries, providing versatility and efficiency in one package.
These machines combine robust performance with advanced features, ensuring compatibility with diverse welding applications. By incorporating cutting-edge technology, YesWelder delivers solutions that streamline operations and enhance productivity.
Distributors can trust YesWelder to provide machines that appeal to a broad customer base, from small-scale workshops to large industrial operations. Their commitment to quality and innovation makes them a preferred partner for businesses aiming to optimize their welding processes. Choosing YesWelder ensures access to reliable, versatile equipment that aligns with operational and budgetary needs.
FAQs
What are the main benefits of multi-process welders?
Multi-process welders combine multiple welding techniques into one unit, offering cost savings, versatility, and space efficiency. They streamline workflows and reduce equipment needs.
Are multi-process welders suitable for industrial applications?
Yes, multi-process welders are ideal for many industrial applications. They are versatile and efficient, but some models may have power limitations for heavy-duty tasks.
How do multi-process welders save space?
By integrating multiple welding methods into one machine, multi-process welders reduce the need for separate devices, freeing up the workspace and reducing workshop clutter.
What are the limitations of multi-process welders?
Common limitations include higher initial costs, potential power restrictions, and increased maintenance requirements due to the complexity of the machine.
Why choose YesWelder for multi-process welders?
YesWelder offers high-quality, reliable welding machines designed for versatility and efficiency. Their products cater to various industry needs, ensuring optimal performance for wholesale buyers and distributors.