The capacity of oxy fuel cutting to cut through different metal thicknesses makes it an essential tool. However, this potent technique is filled with danger. Neglect of oxy fuel cutting safety protocols can lead to disastrous accidents.
In fact, OSHA quotes that there are 500,000 welding-related injuries annually, a fact which emphasizes the critical need for extensive knowledge of safety in operations like oxy-fuel cutting. Continue reading to discover how to professionally practice safe oxy-fuel cutting!
Related article: What Is Oxy Fuel Welding?
What is Oxy-Fuel Cutting?
Oxy-fuel cutting is a thermal cutting process that uses the high temperature resulting from the combustion of a fuel gas (acetylene, but also propane, propylene, or natural gas) with oxygen to heat the metal to its kindling point.
Once the metal has been brought to this temperature, a high-pressure stream of pure oxygen is used on the hot metal. The oxygen rapidly oxidizes the metal, forming molten slag that is expelled, producing a clean and precise cut.
Oxy fuel cutting is useful in a wide variety of industries, including:
- Construction: Cutting structural steel, pipes, and reinforcing bars.
- Shipbuilding: Shaping and preparing steel plates for hull construction and repairs.
- Fabrication: Making specialty metal parts for equipment, automobiles, and other industries.
- Demolition: Removal of steel structures.
- Repair and Maintenance: Removal of wrecked metal components for replacement.
A typical oxy-fuel cutting arrangement includes several essential parts, each having an important role in the cutting operation:
- Torches: Where the oxygen and fuel gas combine and get burned to produce the cutting flame. The design of the torch differs according to the types of cutting tasks and metal thicknesses.
- Regulators: Fitted onto the gas cylinders so that the high stored pressure of the gas is reduced to safe and appropriate work pressure for application with the torch. There has to be proper regulation of the pressure so that there could be constant and regulated flame.
- Hoses: Flexible hoses transport the fuel gas and oxygen from the regulators to the torch. The hoses are typically color-coded (red for fuel gas, green for oxygen in the US) for easy identification and to prevent accidental mixing.
- Cylinders: High-pressure cylinders hold the fuel gas and oxygen. These cylinders must be handled and stored with extreme care due to the highly pressurized and often flammable contents.
- Flashback Arrestors: Installed between regulators and hoses (sometimes between hoses and the torch). They are designed to prevent a flashback – the dangerous backflow of gases into the cylinders.
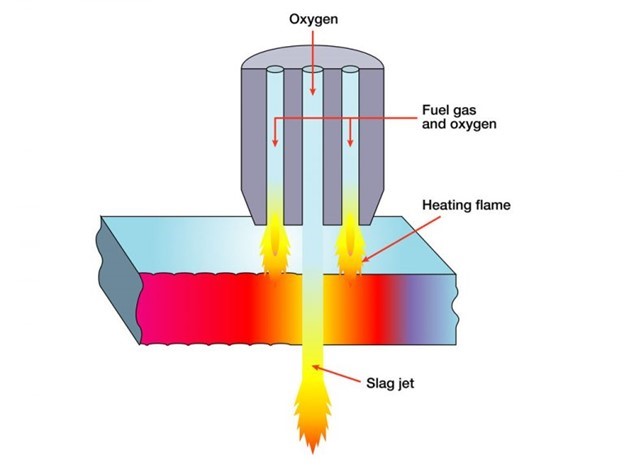
Key Oxy-Fuel Cutting Hazards
Fire and Explosion Risks
Fire and explosions can be due to a variety of factors:
- Gas Leaks: Regulators, hoses, or torch connections can leak combustible gases onto the working space, creating a hazard for explosion if a spark or open flame ignites it.
- Improper Flame Adjustment: Backfires (hissing or popping at the torch tip) or flashbacks (the moving flame backward through the torch and potentially the hoses and cylinders) can be caused by incorrect adjustment of the flame.
- Flashback: As said before, a flashback is a serious risk that can lead to an explosion within the machine.
- Combustible Materials: Allowing combustible materials like wood, paper, or solvents to be stored in the cutting zone adds a lot to the fire risk.
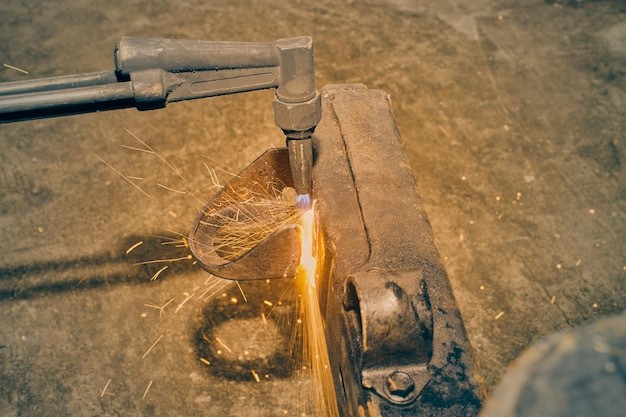
Health Risks
- Inhalation of Toxic Fumes: The combustion process and the oxidation of the cut metal release various fumes and gases, some of which are toxic when inhaled. Some of these include metal oxides, carbon monoxide, and nitrogen oxides, which may lead to respiratory diseases as well as long-term conditions.
- Burns: Exposure to the open heat of the flame or molten metal slag can cause severe burns to the skin. Sparks and molten metal can travel a long distance, with a possible burn hazard to exposed skin.
- UV Light Eye Damage: The oxy-fuel flame produces strong ultraviolet (UV) radiation, which can lead to “welder’s flash” or arc eye – a burning sensation like sunburn of the cornea. Prolonged exposure can result in more severe eye damage.
Environmental Risks
- Fuel Gas Emissions: Combustion of fuel gases releases greenhouse gases and other pollutants into the atmosphere. Even though acetylene gas itself is not a significant source of greenhouse gases, so are propylene and propane.
- Spent Cylinders Disposal: Spent or leaked gas cylinders have to be disposed of properly to prevent potential harm and contamination of the environment.
- Waste Generation: The oxy-fuel cutting process produces metal slag and potentially contaminated material, which has to be disposed of in a responsible manner.
Oxy Fuel Cutting Safety Checklist
Pre-Operation Checks
- Test Equipment: Check hoses, regulators, and torches for cracks, wear, or leaks. Perform a soap bubble test for gas leaks.
- Secure Cylinders: Store cylinders chained, upright, and well away from heat or flame.
- Install Flashback Arrestors: Place arrestors at the torch and regulator to prevent flame backflow.
- Check Workspace: Clear the area of combustible materials and ensure proper ventilation.
During Operation
- Adjust Flames Correctly: Set a neutral flame (sharp blue cone) for cutting.
- Wear Proper PPE: Use flame-resistant clothing, welding gloves, tinted goggles (shade #10), and a welding helmet.
- Monitor Surroundings: Keep a fire extinguisher nearby and avoid cutting near flammable substances.
Post-Operation Procedures
- Proper Shutdown: Close the oxygen valve first, then the fuel gas valve, to prevent gas buildup.
- Store Equipment: Coil hoses neatly, store torches securely, and check cylinders for residual gas.
- Double Check: Look for signs of damage or wear before storing equipment.
Personal Protective Equipment (PPE) for Oxy-Fuel Cutting
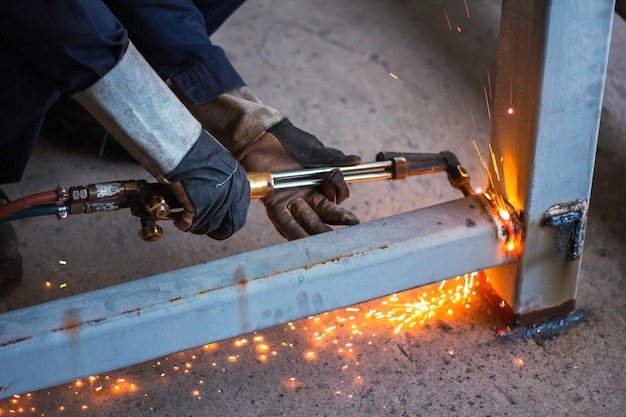
Wearing the correct PPE is non-negotiable when performing oxy-fuel cutting. It acts as the last line of defense against potential injuries.
Required PPE
- Flame-Resistant Jackets and Trousers
- Leather Gloves
- Leather Apron
- Welding Helmet with Appropriate Shade
- Steel-Toed Boots
- Respiratory Protection (A mask or respirator)
Choosing Quality PPE
When selecting PPE, prioritize quality and ensure it meets relevant safety standards. Look for certifications such as ANSI Z87.1 for eye protection.
PPE that fits well and is comfortable to wear is more likely to be used consistently. Inspect your PPE regularly for any signs of wear or damage and replace it when necessary.
Troubleshooting Common Oxy-Fuel Cutting Issues
Even with proper technique, operators may encounter common issues during oxy-fuel cutting. Knowing how to troubleshoot these problems safely is essential.
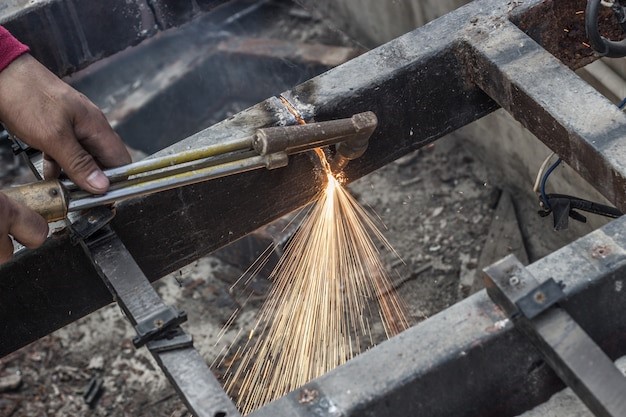
Handling Flashbacks and Backfires
- Causes: These can be caused by obstructions in the torch tip, overheating the tip, using incorrect gas pressures, or allowing the tip to come into contact with the workpiece.
- Immediate Actions: If a flashback occurs, immediately shut off the oxygen cylinder valve first, followed by the fuel gas cylinder valve. Allow the equipment to cool down before inspecting for damage. Check and clean or replace flashback arrestors if necessary.
- Prevention Tips: Ensure regular maintenance of equipment, use correct gas pressures, avoid overheating the torch tip, and always use properly functioning flashback arrestors.
Detecting and Fixing Gas Leaks
- Detection: The easiest way to detect gas leaks is by applying a soap bubble solution to all connections (hoses, regulators, torch). Bubbles will form at the site of a leak. Never use an open flame to check for leaks.
- Emergency Response: If a leak is detected, immediately shut off the gas supply at the cylinders. Ventilate the area to allow the gas to dissipate. Do not attempt to repair a leak while the system is pressurized. Have the damaged component repaired or replaced by a qualified technician.
Poor Cut Quality
Several factors can contribute to a poor quality cut:
- Causes: Incorrect flame type or adjustment, improper gas pressure settings, incorrect cutting speed, or a dirty or damaged cutting tip.
- Solutions: Ensure the correct flame type (typically neutral for steel) is used and adjusted according to the material thickness. Verify that the gas pressures are set to the manufacturer’s recommendations. Maintain a consistent cutting speed. Clean or replace the cutting tip if it is clogged or damaged.
Sustainable Oxy-Fuel Cutting Practices
In today’s environmentally conscious world, adopting sustainable practices in oxy-fuel cutting is increasingly important.
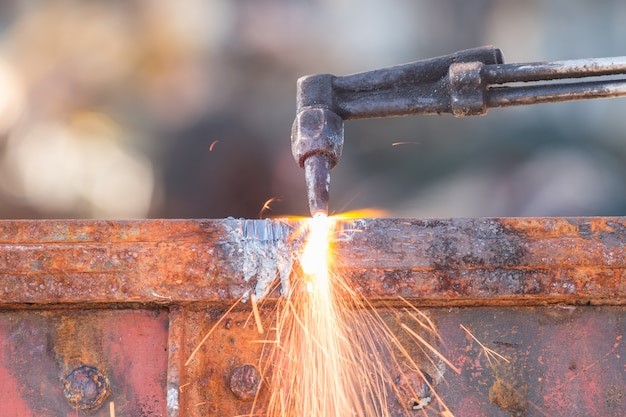
Reducing Emissions
- Use of Low-Emission Fuel Gases: Consider using alternative fuel gases like propylene or propane, which may have lower emission profiles compared to acetylene in certain applications.
- Proper Ventilation Systems: Ensure effective ventilation systems are in place to capture and filter fumes and gases generated during the cutting process, minimizing their release into the atmosphere.
Waste Management
- Recycling Spent Cylinders and Scrap Metal: Properly recycle empty or damaged gas cylinders through authorized facilities. Salvage and recycle metal scrap generated during the cutting process whenever possible.
- Safe Disposal of Hazardous Residues: Dispose of any hazardous residues, such as contaminated wipes or filters, according to local environmental regulations.
Training and Certification for Oxy-Fuel Safety
Proper training is fundamental to ensuring safe and efficient oxy-fuel cutting operations. Several options are available for oxy-fuel cutting training:
- AWS Courses
- Community College Programs
- Manufacturer Workshops
- Online vs. In-Person Options
Obtaining types of welding certifications (also cutting certifications) can offer benefits like:
- Improved Job Prospects
- Compliance with OSHA
- Enhanced Safety Knowledge
Final Thoughts
Oxy-fuel cutting is a valuable and useful technique, but in order to be used safely, it needs precision and a sharp awareness of risk and precaution. Following the safety checklist, using the appropriate PPE, being proficient at fault diagnosis, and meeting legislation will all go some way to reduce the risk of accident and harm significantly.
Remember, safety is not a task that is done once but an ongoing process. Regular education and unyielding adherence to safety protocols are the pillars of safe and successful oxy-fuel cutting.
Looking for reliable welding equipment, come to YesWelder wholesale and get efficient welding machines!
FAQs on Oxy-Fuel Cutting Safety
What should I do if a flashback occurs?
Immediately shut off the oxygen cylinder valve first, followed by the fuel gas cylinder valve. Allow the equipment to cool and inspect for damage, especially the flashback arrestors.
How often should I inspect oxy-fuel equipment?
Inspect hoses, regulators, and torches before each use for any sign of wear, damage, or leaks. Regular maintenance according to manufacturer instructions is also essential.
What PPE is required for oxy-fuel cutting?
Essential PPE includes flame-resistant clothing, leather gloves, a leather apron, a welding helmet and the correct shade lens or safety glasses, and steel-toed boots. Respiratory protection may be necessary in certain situations.
Additional Resources
Please refer to the following sites to get further information and resources on oxy-fuel cutting safety.