Plasma cutting, a widely used technique for slicing through electrically conductive materials, presents several safety challenges. The intense heat and high voltage involved in this process pose significant risks, including severe burns, eye injuries from the arc light, and exposure to toxic fumes. These hazards underscore the importance of stringent safety measures to protect operators from potential accidents.
Implementing comprehensive safety protocols is crucial for mitigating these risks. Key measures include wearing appropriate personal protective equipment (PPE) such as gloves, face shields, and flame-resistant clothing. Ensuring proper ventilation to disperse harmful fumes and maintaining a clean work environment to prevent fire hazards are also vital.
Regular equipment checks and adherence to operational guidelines further enhance safety, reducing the likelihood of injuries and ensuring a safer working environment for all involved in plasma-cutting operations.
Understanding Plasma Cutting
Plasma cutting is a process that uses a high-velocity jet of ionized gas, known as plasma, to cut through electrically conductive materials. The process begins with creating an electric arc between an electrode and the workpiece. This arc ionizes the gas, turning it into plasma, which is then ejected through a constricted opening at high speed. The high temperature of the plasma melts the material, while the velocity of the gas blows the molten metal away, resulting in a clean cut.
A power supply, a plasma torch, and a compressed gas supply are required to operate a plasma cutter. The power supply generates the electrical energy needed to create the arc, the torch holds the electrode and directs the plasma, and the gas supply provides the necessary ionized gas. Common gases used in plasma cutting include compressed air, nitrogen, and oxygen.
Common Materials Cut by Plasma Cutting
- Aluminum: Lightweight and corrosion-resistant, aluminum is frequently used in automotive and aerospace industries. Plasma cutting effectively handles its reflective surface and varying thicknesses
- Stainless Steel: Known for its strength and rust resistance, stainless steel is ideal for manufacturing and construction. Plasma cutting ensures precise cuts, maintaining its structural integrity
- Alloy Steel: Used in heavy machinery and structural applications due to its enhanced strength. Plasma cutting provides clean cuts in this robust material
- Mild Steel: Commonly used in construction and fabrication due to its malleability and affordability. Plasma cutting is efficient for varying thicknesses of mild steel
- Copper: Valued for its electrical conductivity, plasma cutting offers a fast and effective method to cut copper while maintaining its conductive properties
- Cast Iron: Durable and heat-retentive, cast iron is used in heavy-duty applications like engine blocks. Plasma cutting allows accurate cuts even in thick sections
- Chrome: Used as a plating material for corrosion resistance and a shiny finish. Plasma cutting ensures clean edges without damaging the chrome plating
The Dangers of Plasma Cutting
High Voltage Risks
Plasma cutting involves using high voltage, typically 100 to 400 volts, to create the plasma arc necessary for cutting through metal. This high voltage can pose serious risks if not handled properly. Direct contact with the electrical components can result in severe electric shocks, leading to injuries or fatalities. To mitigate these risks, operators must ensure that all equipment is properly insulated, grounded, and maintained.
Intense Arc Light
The plasma arc emits intense ultraviolet (UV) and infrared (IR) light, which can cause severe eye injuries, including “arc eye” or photokeratitis and skin burns. Proper eye protection, such as a welding helmet with the appropriate shade, is necessary to protect against these harmful rays. Additionally, operators should wear long-sleeved clothing and gloves to shield their skin from UV exposure
High Temperatures
Plasma cutting generates extremely high temperatures, often reaching 45,000 degrees Fahrenheit. If operators come into direct contact with the plasma stream or the heated metal, these temperatures can cause severe burns. To protect against thermal burns, it is crucial to wear flame-resistant clothing and gloves.
Molten Metal
During the plasma cutting process, molten metal is produced, which can splatter and cause burns or ignite flammable materials nearby. Ensuring a clean work area is free of flammable objects and using protective barriers can help contain molten metal and prevent fires.
Toxic Fumes
Cutting through certain metals can release toxic fumes and gases, such as ozone and metal oxides, which can be harmful if inhaled. Proper ventilation systems and fume extraction units are essential to minimize exposure to these hazardous substances.
Essential Safety Measures for Plasma Cutting
Personal Protective Equipment (PPE)
Personal Protective Equipment (PPE) is critical in ensuring the safety of operators during plasma cutting. The high temperatures, intense arc light, and potential for molten metal splatters necessitate comprehensive protective gear. Key PPE items include:
- Welding Helmet: This helmet protects the eyes and faces from intense arc light and flying debris. Wearing a helmet with the appropriate shade level is essential to prevent eye damage.
- Safety Glasses: Worn under the helmet, safety glasses provide additional eye protection from UV and IR radiation.
- Flame-Resistant Clothing: Long-sleeved shirts and pants made of flame-resistant materials protect the skin from burns and molten metal splatters.
- Gloves: Heavy-duty, heat-resistant gloves protect the hands from burns and allow safe handling of hot materials.
- Respiratory Protection: Masks or respirators are necessary to protect against inhaling toxic fumes and gases generated during cutting.
- Hearing Protection: Earplugs or earmuffs protect against the high noise levels of plasma cutters.
- Steel-Toed Boots: Protect feet from heavy falling objects and provide a non-slip grip to prevent accidents.
Basic Safety Equipment
- Fire Extinguisher: Essential for quickly extinguishing any fires that may start due to sparks or molten metal.
- Ventilation System: Effective ventilation systems or fume extractors remove toxic gases and ensure clean air in the workspace.
- Grounding Clamps: Proper grounding of the plasma cutter prevents electrical hazards.
- First Aid Kit: A well-stocked kit should be readily available to treat minor injuries promptly.
Proper Setup and Equipment Use
Ensuring proper installation and setup of plasma cutting equipment is fundamental for safety and efficiency. Here are the essential steps:
- Follow the manufacturer’s guidelines for setting up the plasma cutter. This includes proper grounding, connecting the gas supply, and securing all electrical connections.
- Regularly inspect the plasma cutter and associated tools for any signs of wear or damage. Components such as the torch, electrode, and nozzle should be checked frequently and replaced.
- Ensure that the plasma cutter is calibrated correctly to operate at the required settings for the specific task. Incorrect settings can lead to poor cuts and an increased risk of accidents.
- Keep the work area clean and free of flammable materials. Ensure adequate ventilation to disperse toxic fumes and provide clear access to fire extinguishers.
Infographic Explain 5 necessary safety Steps for plasma cutting
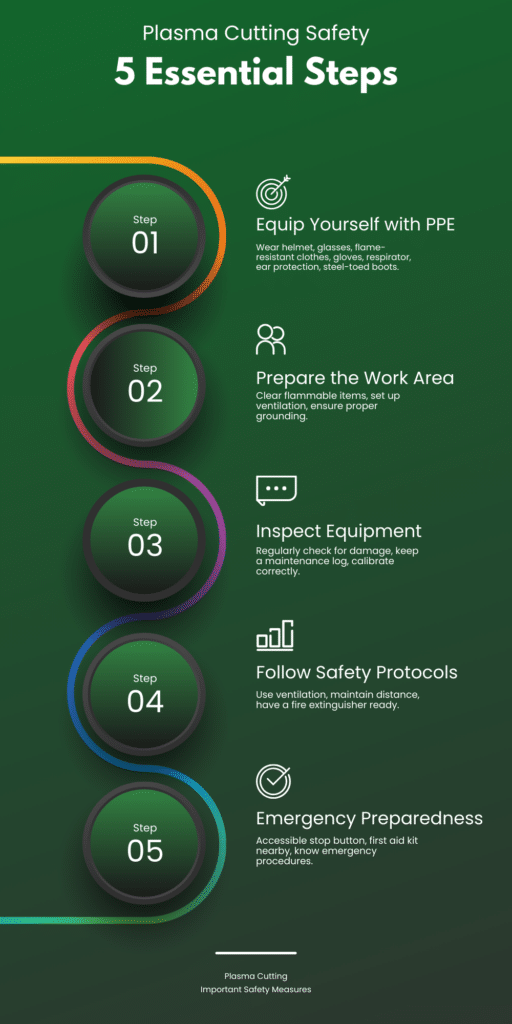
Key Safety Tips for Plasma Cutting
Fire Hazard Prevention
Due to the high temperatures and sparks generated during plasma cutting, fire hazards are a significant concern. To prevent fires, maintain a clean work area free of flammable materials like paper, cloth, and chemicals. Ensure all combustible items are at least 35 feet from the cutting zone. Additionally, having a fire extinguisher nearby and ready for immediate use is crucial. Regularly inspect and maintain the equipment to prevent malfunctions that could ignite fires.
Protection against Infrared Light
The plasma arc produces intense ultraviolet (UV) and infrared (IR) light, which can cause severe eye and skin injuries. To protect against these harmful rays, always wear a welding helmet with the appropriate shade level. Safety glasses should be worn under the helmet for additional eye protection. Long-sleeved, flame-resistant clothing, gloves, and a full-face shield can help shield your skin from burns caused by exposure to UV and IR radiation.
Avoiding Electrocution
Electrocution is a serious risk when working with plasma cutters due to the high voltage. To avoid electrocution:
- Ensure that all electrical connections are secure and properly insulated.
- Ground the plasma cutter correctly and avoid using it in wet conditions.
- Regularly inspect the power cords, plugs, and other electrical components for signs of damage and replace them as needed.
Following these precautions can significantly reduce the risk of electrical accidents.
Managing Toxic Fumes
Plasma cutting can release toxic fumes and gases, such as ozone and metal oxides, which pose health risks if inhaled. To manage these fumes, ensure that your workspace is well-ventilated. Use fume extraction systems or local exhaust ventilation to capture and remove harmful gases at the source. Additionally, wearing respiratory protection, such as masks or respirators, can help safeguard your lungs from inhaling toxic substances. Monitoring air quality regularly ensures that the environment remains safe for all workers.
Conclusion
Plasma cutting is a powerful metal fabrication technique that requires stringent safety measures. Adhering to safety protocols, using proper personal protective equipment (PPE), and ensuring correct equipment setup and maintenance are crucial. Following these guidelines, operators can significantly reduce risks and enhance workplace safety, making plasma cutting efficient and safe.
FAQs about Plasma Cutting Safety
What are the essential safety measures for plasma cutting?
Essential safety measures for plasma cutting include using appropriate personal protective equipment (PPE) such as welding helmets, safety glasses, flame-resistant clothing, gloves, and respiratory protection.
Why is PPE important in plasma cutting?
PPE is vital in plasma cutting because it protects operators from hazards such as intense arc light, molten metal splatters, toxic fumes, and high temperatures.
How can I prevent fire hazards during plasma cutting?
Keep the work area clean and free of flammable materials to prevent fire hazards. Maintain a minimum distance of 35 feet from combustible items and have a readily available fire extinguisher.
What should I do to manage toxic fumes during plasma cutting?
Managing toxic fumes involves ensuring good ventilation in the workspace. Use fume extraction systems or local exhaust ventilation to capture and remove harmful gases from the source.
How do I avoid electrocution when using a plasma cutter?
To avoid electrocution, ensure all electrical connections are secure and properly insulated. Correctly ground the plasma cutter and avoid using it in wet conditions. Inspect power cords, plugs, and other electrical components for damage and replace them as needed.