Whether you’re assembling a circuit board or constructing a steel bridge, choosing between soldering and welding can define a project’s success. The difference between soldering and welding lies in their techniques, applications, and outcomes.
What Is Soldering?
Soldering is common in industries requiring meticulous connections, such as consumer electronics or artisanal crafts.
It joins metals using a low-melting-point filler material (solder) at temperatures below 840°F (450°C). This non-fusion process avoids melting the base metals, making it ideal for delicate components. The solder, typically a tin-lead or lead-free alloy, flows into the joint, creating a reliable but relatively weak bond. Key characteristics include:
- Precision: Perfect for small-scale, intricate work.
- Low Heat: Protects sensitive materials from thermal damage.
- Applications: Electronics (circuit boards), plumbing (copper pipes), jewelry (delicate designs).
What Is Welding?
Welding is the backbone of industries building infrastructure or heavy machinery. It fuses metals by melting them at high temperatures, often exceeding 6,500°F (3,600°C), to create a strong, permanent joint.
This fusion process melts both the base metals and, in some cases, a filler material, forming a robust bond. Useful MIG welding machines or TIG welding machines vary by application. Key characteristics include:
- Durability: Produces joints capable of withstanding heavy loads.
- High Heat: Requires robust materials and safety measures.
- Applications: Construction (skyscrapers), automotive (car frames), shipbuilding (hulls).
Soldering vs Welding: Key Differences
Understanding the soldering vs welding comparison requires examining their core differences. The following table summarizes key factors:
Factor | Soldering | Welding |
Temperature | Below 840°F (450°C) | Up to 10,000°F (5,500°C) |
Strength | Low, for non-structural joints | High, for structural integrity |
Applications | Electronics, plumbing, jewelry | Construction, automotive, shipbuilding |
Materials | Soft metals (copper, tin, brass) | Hard metals (steel, aluminum, titanium) |
Equipment | Soldering iron, flux, solder | Welder (MIG, TIG, arc), shielding gas |
Skill Level | Beginner-friendly | Advanced, requires training |
Setup Complexity | Simple, portable tools | Complex, requires power source and safety gear |
Temperature sets the foundation: soldering’s low heat preserves delicate components, while welding’s extreme heat fuses metals for unmatched strength.
Strength reflects this—soldered joints suffice for electrical conductivity or light mechanical loads, but welded joints endure the stress of bridges or vehicles.
Materials further differentiate them: soldering excels with soft, conductive metals like copper, while welding handles robust metals like steel or aluminum. The choice depends on your project’s demands, from precision to durability.
When to Use Soldering
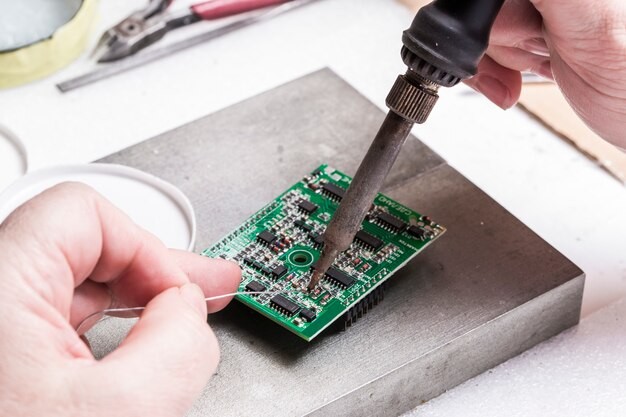
Soldering is the preferred method for projects requiring precision and minimal heat. Its applications span industries and hobbies:
- Electronics: Soldering connects components on circuit boards, ensuring reliable electrical pathways. It’s critical for devices like smartphones, computers, and IoT gadgets.
- Plumbing: Soldering creates leak-proof joints in copper piping, common in residential and commercial water systems.
- Jewelry: Artisans use soldering to join delicate metals, crafting intricate designs without compromising material integrity.
Pros: Minimal heat, portable tools, beginner-friendly.
Cons: Weak joints, limited to soft metals, not suitable for structural tasks.
When to Use Welding
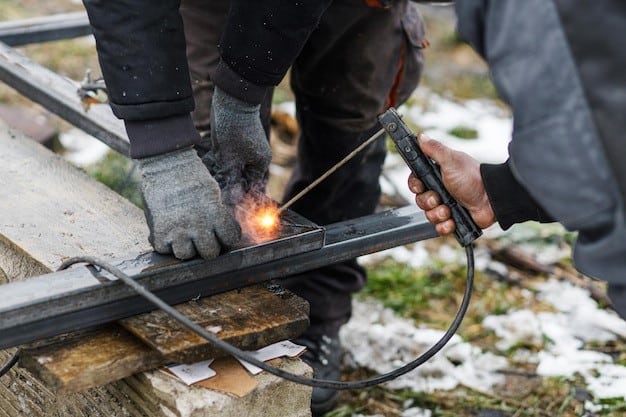
Welding is the go-to for projects demanding robust, permanent joints. It’s essential in heavy industries and large-scale repairs:
- Construction: Welding builds skyscrapers, bridges, and stadiums, ensuring structural stability under extreme loads.
- Automotive: Welders assemble car frames, repair chassis, and customize exhaust systems for performance vehicles.
- Shipbuilding: Welding creates watertight hulls and superstructures, critical for maritime safety.
Pros: Exceptional strength, versatile for hard metals, permanent joints.
Cons: High heat risks damage to sensitive materials, complex setup, steep learning curve.
Safety Considerations of Soldering and Welding
Both soldering and welding involve risks, but proper precautions ensure safe operation. Understanding these hazards is critical for beginners and professionals alike.
Soldering Safety
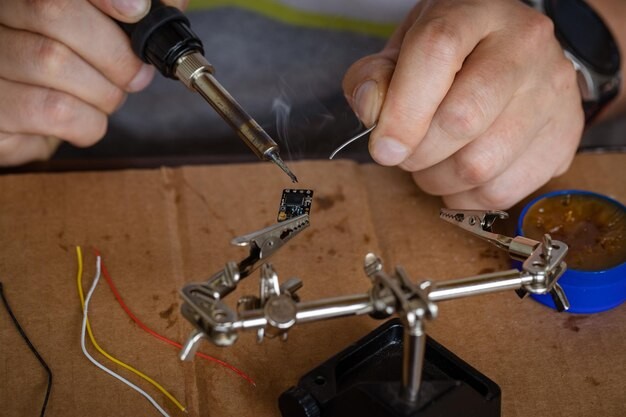
Soldering is safer than welding but still poses challenges:
- Burns: Soldering irons reach temperatures of 600–800°F, risking skin burns.
- Toxic Fumes: Solder, especially lead-based, releases harmful vapors during melting.
- Eye Strain: Prolonged focus on small components can cause discomfort.
Precautions:
- Work in a well-ventilated area or use a fume extractor to remove vapors.
- Choose lead-free solder to minimize health risks.
- Wear heat-resistant gloves, safety glasses, and use a soldering stand to secure the iron.
- Take breaks to reduce eye strain and maintain focus.
Welding Safety
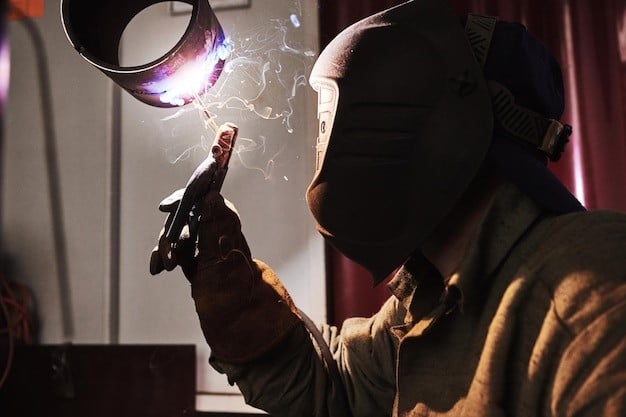
Welding’s high heat and intense light demand stringent safety measures:
- Burns and Sparks: Molten metal and sparks can cause severe burns or ignite flammable materials.
- UV Exposure: Welding arcs emit ultraviolet light, risking “arc eye” (painful eye inflammation).
- Toxic Fumes: Welding generates hazardous gases like ozone or metal vapors.
Precautions:
- Wear a welding helmet with an auto-darkening lens to protect eyes and face.
- Use fire-resistant clothing, welding gloves, and boots to shield against sparks.
- Ensure proper ventilation or wear a respirator in confined spaces.
- Keep a fire extinguisher nearby and clear the workspace of flammable materials.
Tip: Always inspect equipment before use—damaged soldering irons or welding cables can cause electrical hazards or inconsistent performance.
Skill Levels and Learning Curves
Soldering Skills
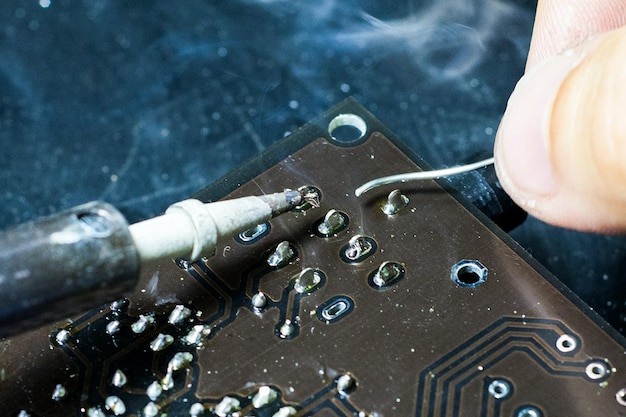
Soldering is accessible to beginners, with a learning curve of just a few hours to achieve basic proficiency. Key skills include controlling the soldering iron, applying solder evenly, and cleaning joints with flux for strong bonds. Common challenges include overheating components or creating “cold joints” (weak, unreliable connections).
Resources:
- Online tutorials (e.g., YouTube channels).
- DIY soldering kits with practice boards.
- Community workshops at makerspaces or tech schools.
Tip: Start with a low-wattage soldering iron to avoid damaging components, and practice on scrap electronics before working on critical projects.
Welding Skills
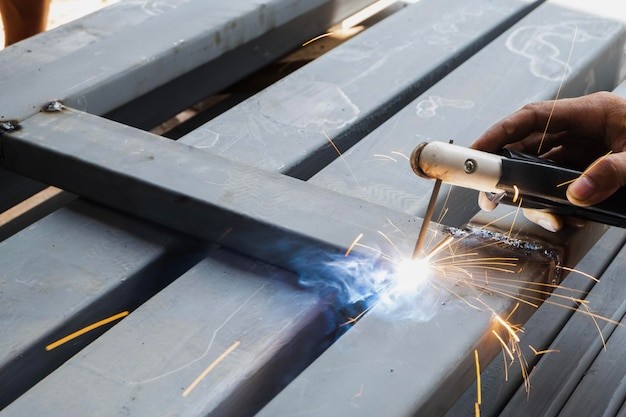
Welding demands significant training, often through certifications, apprenticeships, or vocational programs. Mastering techniques like MIG, TIG, or stick welding requires months of practice to control the arc, manage heat, and produce clean welds. Challenges include maintaining a steady hand and avoiding defects like porosity or cracking.
Resources:
- Vocational schools (e.g., leading U.S. welding programs).
- Online courses for welding theory and safety (e.g., American Welding Society resources).
- Apprenticeships with experienced welders in construction or manufacturing.
Tip: Practice on scrap metal to perfect your bead consistency, and prioritize safety training to handle high-risk equipment confidently.
Final Thoughts
Soldering and welding are powerful metal-joining techniques with distinct strengths: soldering offers precision for electronics and delicate crafts, while welding delivers unmatched durability for infrastructure and heavy machinery. Explore related guides on soldering techniques or welding fundamentals to deepen your skills.
FAQs
Which is stronger, soldering or welding?
Welding is stronger, fusing metals to create durable joints for structural projects like bridges. Soldering produces weaker joints, suited for delicate tasks like electronics.
Can you solder and weld the same metals?
Yes, metals like copper and steel can be soldered or welded, but the project dictates the method. Soldering is ideal for soft metals in precision tasks, while welding suits hard metals for heavy-duty applications.
What’s the difference between soldering and welding?
Soldering joins metals with a low-temperature filler (below 840°F), perfect for electronics and plumbing. Welding fuses metals at high temperatures (up to 10,000°F), ideal for construction and automotive projects.
Which is better for electronics, soldering or welding?
Soldering is better for electronics, as its low heat preserves delicate components like microchips. Welding’s high heat risks damaging circuit boards.
Are there safety risks with soldering or welding?
Soldering risks include burns and toxic fumes, mitigated by ventilation and lead-free solder. Welding risks include UV exposure and burns, requiring helmets and protective clothing.
Which is easier to learn, soldering or welding?
Soldering is easier, with a short learning curve for beginners using basic tools. Welding requires extensive training to master complex techniques and handle high-risk equipment.