Welding tasks in construction, shipbuilding, and repair jobs often face challenges such as outdoor conditions and contaminated surfaces. A stick welding machine addresses these issues by offering a versatile and effective solution. It is particularly beneficial for its adaptability in various environments and ability to work on various metals.
When compared to other welding methods, stick welding doesn’t require external shielding gas, making it ideal for fieldwork. This method is known for its portability, ease of use in adverse conditions, and minimal pre-welding preparation, making it a preferred choice for many industries.
Advantages & Disadvantages of Stick Welding
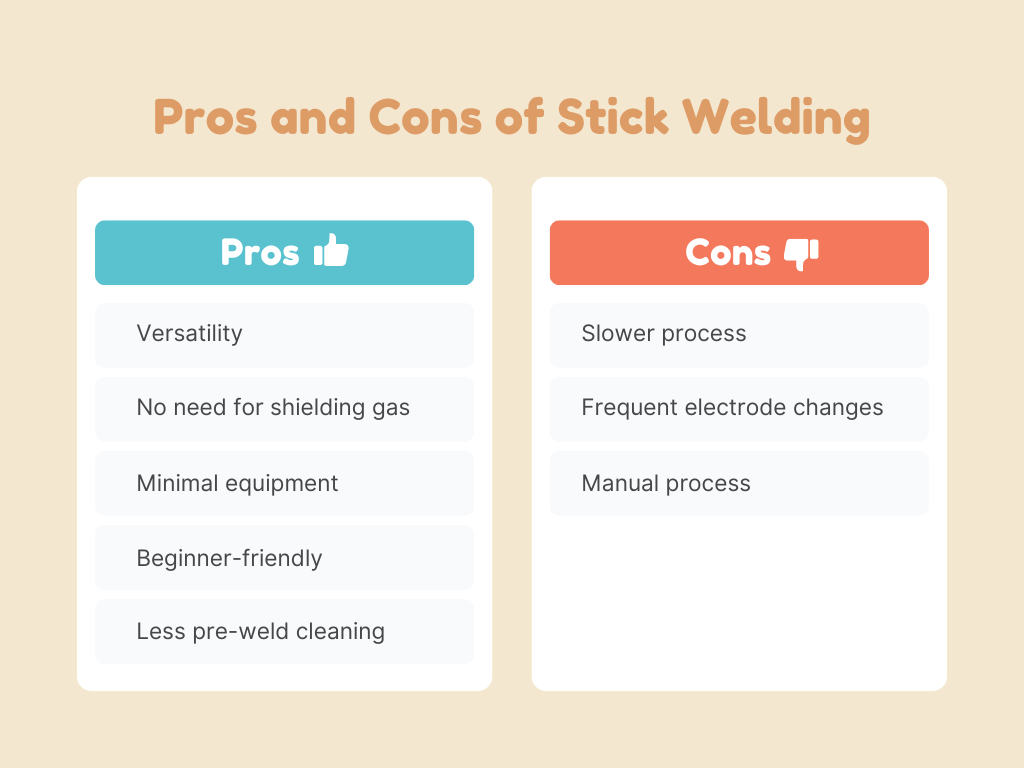
Advantages of Stick Welding
Stick welding offers several advantages, making it a preferred choice for many welding applications. Here are some key benefits:
Versatility
Stick welding can be used on various metals, including steel, stainless steel, and iron. This versatility makes it suitable for different projects and industries.
No Need for Shielding Gas
Unlike MIG and TIG welding, stick welding does not require external shielding gas. The electrode’s flux coating provides the necessary protection, allowing welding to be done in windy or outdoor conditions without compromising the weld quality.
Minimal Equipment
Stick welding equipment is relatively simple and portable. A basic setup includes a power source, electrode holder, ground clamp, and electrodes, making it easy to transport and set up on-site. This simplicity also reduces initial costs.
Beginner-Friendly
While all welding requires practice, stick welding is more accessible for beginners. The process is straightforward, and the equipment is easy to use, making it a good starting point for those new to welding.
Effective in Adverse Conditions
Stick welding performs well in various weather conditions, including wind and rain. This capability is due to the electrode’s flux coating, which protects the weld area from atmospheric contamination. As a result, stick welding is often used in outdoor and field applications.
Less Pre-Weld Cleaning
Stick welding is less sensitive to surface contaminants like rust, paint, and dirt. This tolerance reduces the need for extensive pre-weld cleaning, saving time and effort during welding.
Strong and Durable Welds
Stick welding produces strong and durable welds suitable for structural applications. The process is beneficial for welding thick materials and creating robust joints that can withstand significant stress and load.
Disadvantages of Stick Welding
Despite its many advantages, stick welding also has several drawbacks that can limit its use in specific applications. Here are some key disadvantages:
Production of Smoke and Fumes
Although stick welding doesn’t need shielding gas, this welding method generates a significant amount of smoke and fumes, which can be hazardous to the welder’s health. Proper ventilation and protective equipment are necessary to mitigate these risks.
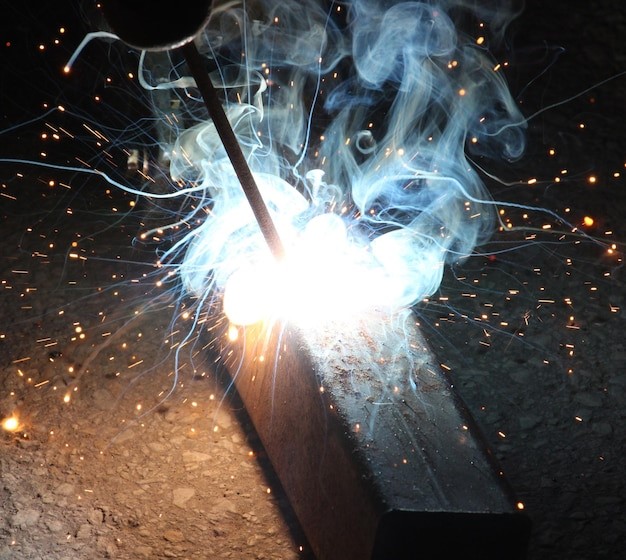
Manual Process
Stick welding is a manual process that requires constant attention and skill from the welder. This can lead to fatigue and inconsistencies in the welds, especially during long welding sessions. Automated welding processes, like robotic MIG welding, can reduce these issues but are not applicable to stick welding.
Slower Process
Compared to other welding methods like MIG and TIG welding, stick welding is relatively slow. The need to frequently change electrodes and the manual nature of the process contribute to longer welding times, which can be a disadvantage in high-production environments.
Frequent Electrode Changes
Stick welding requires frequent electrode changes, which can interrupt the welding process and reduce overall efficiency. This is particularly disadvantageous when welding large structures or long seams.
5 Important Steps for Best Results from Stick Welding
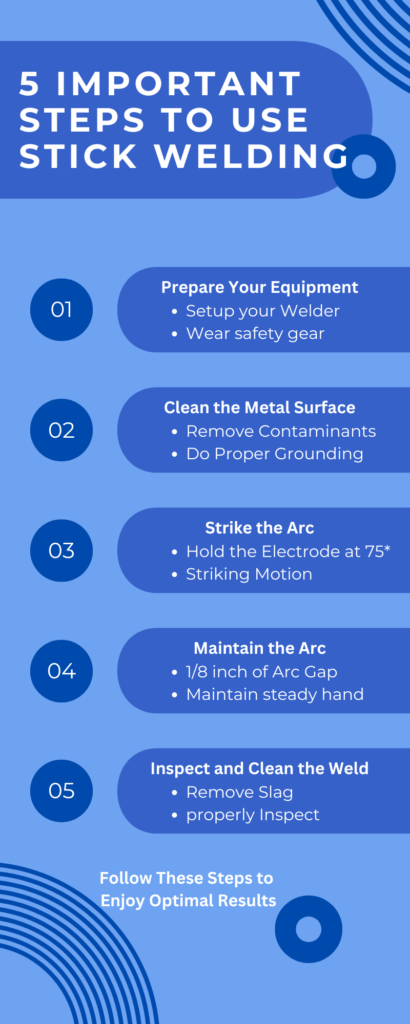
Comparison of Different Welding Methods
Feature | Stick Welding | MIG Welding | TIG Welding |
Versatility | High (various metals and environments) | Moderate (primarily steel and aluminum) | High (precise and various metals) |
Shielding Gas | Not required | Required | Required |
Equipment | Minimal | Moderate | Extensive |
Ease of Use | Beginner-friendly | Beginner-friendly | Advanced skill required |
Outdoor Use | Excellent (wind and rain) | Limited (requires shielding gas) | Limited (requires shielding gas) |
Thin Metals | Not suitable | Suitable | Excellent |
Thick Metals | Excellent | Good | Good |
Speed | Slow | Fast | Slow |
Production of Fumes | High | Moderate | Low |
Clean-Up | Required (slag removal) | Minimal | Minimal |
Structural Welding | Excellent | Good | Good |
Automotive | Good | Excellent | Excellent |
Pipe Welding | Excellent | Good | Excellent |
Manufacturing | Good | Excellent | Moderate |
Precision Welding | Moderate | Good | Excellent |
Cost | Low | Moderate | High |
Choosing the Right Welding Method
Project Requirements
- Steel and Iron: All three methods (Stick, MIG, TIG) work well, but stick welding is often preferred for its robustness and simplicity.
- Aluminum and Non-Ferrous Metals: MIG and TIG are better suited. A TIG welder is
particularly good for thinner materials due to its precision. - Stainless Steel: TIG is ideal for its clean, precise welds, while MIG welder is also effective for thicker sections.
- Thick Materials: Stick welding is excellent for thicker sections, as it provides deep penetration and strong welds.
- Thin Materials: TIG welding is the best choice for thin materials due to its precise control and minimal heat input, reducing the risk of warping.
Joint Design
- Complex Joints: TIG welding offers the best control for complex joints and detailed work.
- Simple Joints: MIG and stick welding can handle simple joints effectively and are faster for straightforward tasks.
Environment and Working Conditions
- Stick Welding: This performs well in outdoor and windy conditions, as it doesn’t require shielding gas.
- MIG Welding: Less suitable for outdoor work unless proper wind protection is used to shield the gas.
- TIG Welding: Generally not recommended for outdoor work due to the sensitivity of the shielding gas to wind and contaminants.
- All methods are suitable for indoor working environments, but the choice depends on other factors like material and precision needed.
Precision and Finish
- TIG Welding: Provides the highest precision and the cleanest welds, ideal for projects requiring detailed and visually appealing welds, such as art, automotive, and aerospace applications.
- MIG Welding: Offers good precision and a relatively clean weld, suitable for production work that needs to look good but doesn’t require TIG’s level of precision.
- Stick Welding: Adequate for general-purpose welding where precision is less critical.
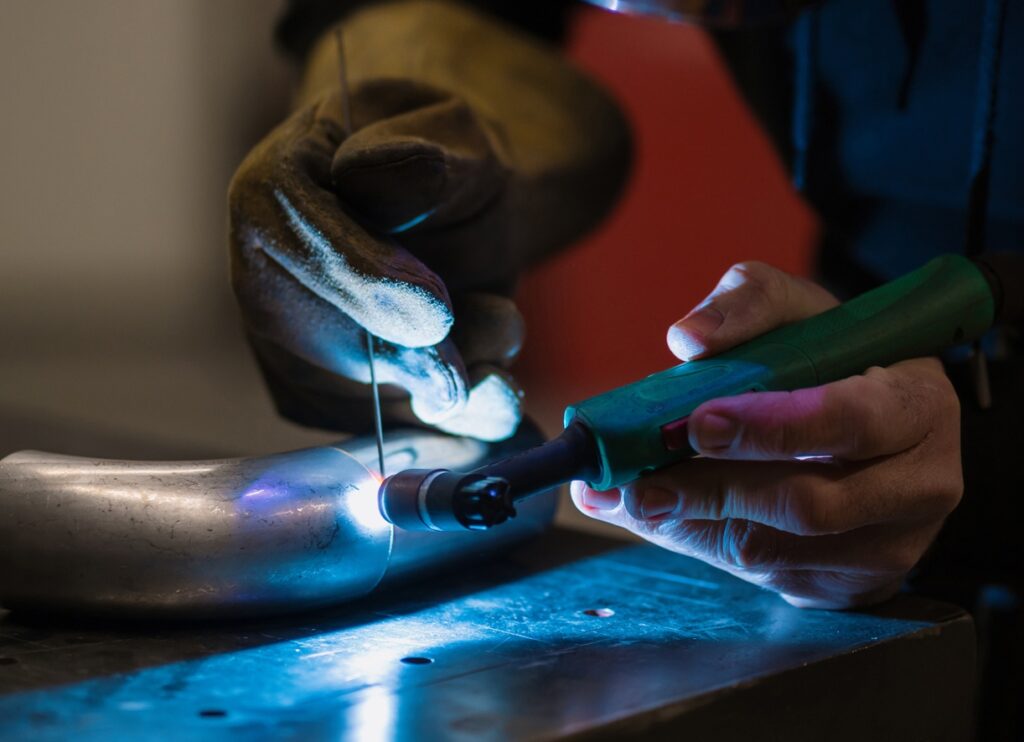
Speed and Efficiency
- MIG Welding: The fastest method, making it ideal for high-volume production and when speed is a priority.
- Stick Welding: Moderate speed, suitable for repair work and situations where setup time is minimal.
- TIG Welding: The slowest method, best suited for detailed and intricate work.
Cost and Equipment
- Stick Welding: Generally the most cost-effective in terms of equipment and operational costs. Ideal for beginners and small projects.
- MIG Welding: Equipment is more expensive than stick welding but offers ease of use and efficiency for larger projects.
- TIG Welding: The most expensive in terms of equipment and requires a high skill level, but it provides superior weld quality.
Skill Level
- MIG Welding: Easiest to learn, with automatic feeding of the filler wire and straightforward operation.
- Stick Welding: Requires some skill to master, especially striking and maintaining the arc, but still accessible for beginners.
- TIG Welding: Most challenging to learn due to the need for precise control over the torch, filler rod, and foot pedal.
Summary
Stick Welding | MIG Welding | TIG Welding |
Versatile for general purpose and repair | Best for high-volume production and speed | Excels in high precision and finishes |
For General Purpose and Repair Work: Stick welding is versatile, cost-effective, and suitable for a variety of environments, especially outdoors.
For High-Volume Production and Speed: MIG welding is the best choice for fast, efficient welding on a range of materials, primarily in indoor or controlled environments.
For High Precision and Clean Welds: TIG welding excels in applications requiring fine detail and high-quality finishes, making it ideal for professional and specialized work.
Final Thoughts
Stick welding remains a vital technique in various industries due to its versatility and reliability. It has its limitations, such as the production of fumes and the need for skill, when compared to other welding methods like TIG or MIG welding. its benefits, including minimal equipment requirements and effectiveness in adverse conditions, make it invaluable. Understanding the advantages and disadvantages of stick welding helps select the right method for different welding tasks, ensuring quality and efficiency in welding projects.
FAQs
What is stick welding best used for?
Stick welding is best used for heavy-duty tasks like construction, shipbuilding, and pipeline welding because it creates strong, durable welds.
Can stick welding be used outdoors?
Yes, stick welding is ideal for outdoor use as it does not require shielding gas and performs well in windy and rainy conditions.
What materials can be welded with stick welding?
Stick welding can weld various materials, including steel, stainless steel, cast iron, and aluminum.
Is stick welding suitable for beginners?
Yes, stick welding is beginner-friendly due to its straightforward process and minimal equipment requirements.
What are the common disadvantages of stick welding?
Common disadvantages include the production of smoke and fumes, the need for frequent electrode changes, and slower welding speeds compared to other methods.