In the versatile world of welding, enthusiasts often encounter the challenge of needing different machines for TIG and stick welding, which can be costly and space-consuming. However, a practical solution exists: converting a TIG welder for stick welding. This approach saves on resources and enhances a welder’s adaptability.
By using conversion kits and following specific modifications, welders can efficiently use a single machine for multiple welding processes. This adaptability enables novice and experienced welders to expand their capabilities without significant investment, thus optimizing their setup for various welding tasks.
Can You Stick Weld with a TIG Welder?
Many welders wonder if they can utilize a TIG welder for stick welding to avoid the cost of multiple machines. The answer is yes, with the right setup. A TIG welder can be adapted for stick welding by integrating specific components to handle stick-welding electrodes. This modification connects a compatible stick electrode holder to the TIG welder’s output. It’s essential to ensure that the TIG welder can handle the electrical output requirements for stick welding, which typically involves simpler equipment and less precision than TIG processes.
Why TIG Welders Can Stick Weld
TIG welders are inherently versatile due to their design, which supports multiple forms of welding with minor modifications. The key lies in their power supply, which can produce a stable DC, essential for stick welding. This adaptability allows the welder to switch from the high precision required for TIG welding to the robust and forgiving nature of stick welding.
TIG machines can effectively serve dual purposes by attaching a stick electrode holder and adjusting the settings to accommodate the thicker electrodes used in stick welding. This functionality makes TIG welders a cost-effective option and expands their utility in various welding scenarios, making them invaluable in both professional and home workshops.
TIG Welding vs. Stick Welding
Feature | TIG Welding | Stick Welding |
Equipment Needed | TIG torch, non-consumable tungsten electrode, shielding gas (typically argon) | Stick welder, consumable electrode coated in flux |
Material Compatibility | Mild steel, stainless steel, aluminum, and more | Mild steel, stainless steel, cast iron, and hard surfacing |
Typical Applications | Precision welding, thin materials, aesthetic welds | Construction, heavy repair, outdoor conditions |
Pros | High-quality, clean welds with precise control | Simple setup, versatile, cost-effective |
Cons | Slower process, requires more skill, higher equipment cost | Messier with slag, less precision, not suitable for thin materials |
When to Use TIG Welders for Stick Welding
Stick Welding for Thick Materials
A stick welder is often preferred when welding thick materials due to its robust nature and deep penetration. TIG welders, adapted for stick welding, can be particularly effective in these scenarios. The ability to handle higher currents makes it possible to weld thick, heavy materials that require more intense heat, which TIG machines can provide. This makes TIG welders suitable for constructing heavy steel frames, repairing heavy equipment, and other tasks involving thick materials.
Field Welding
Field welding often demands equipment that is versatile and capable of performing under various environmental conditions. TIG welders converted for stick welding are ideal for field use because they are portable and easily set up with minimal adjustments. Whether repairing pipelines in remote areas or working on construction sites where power supply might be inconsistent, these welders offer the reliability and flexibility needed for effective field operations.
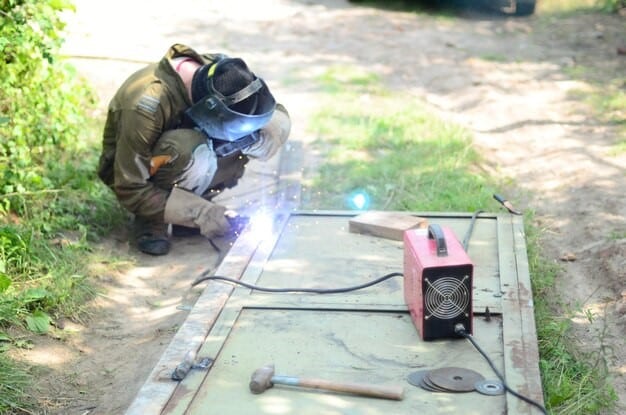
Versatility in Workshop Settings
In workshop settings, where space and budget constraints limit the number of machines a welder can have, TIG welders adapted for stick processes provide a practical solution. They enable a workshop to handle a broader range of welding tasks without requiring additional space for more machines. This versatility is crucial for small businesses or hobbyists who need to maximize their resources while still being able to tackle different types of welding projects, from intricate TIG applications to more general stick welding tasks.
Setup Table: Using a TIG Welder for Stick Welding
Requirement | Details |
Electrode Holder | Attach a compatible stick electrode holder to the TIG welder. |
Power Settings | Adjust power settings to match the electrode’s requirements; typically higher amperage. |
Electrodes | Use electrodes suitable for the material and thickness, such as 6013, 7018. |
Additional Equipment | May need additional cables or connectors, depending on the TIG welder model. |
Safety Considerations for Stick Welding with a TIG Welder
When adapting TIG welders for stick welding, safety is paramount. This setup, while versatile, introduces specific safety challenges that must be addressed to ensure a safe working environment. Here are key safety considerations:
Electrical Safety
- Ensure all electrical connections are secure and insulated. Faulty connections can lead to short circuits or shocks.
- Always use a welder with a functioning ground fault circuit interrupter (GFCI) to protect against electrical shocks, especially in damp environments.
Fire Hazards
- Maintain a clean workspace free from flammable materials. Stick welding can produce sparks that might ignite combustible materials.
- Have appropriate fire extinguishing equipment, such as a fire extinguisher suitable for electrical fires.
Ventilation
- Provide adequate ventilation in the welding area to prevent the accumulation of toxic fumes produced during welding.
- Consider using extraction fans or respiratory protective equipment if welding in confined spaces.
Personal Protective Equipment (PPE)
- Wear appropriate PPE, including a welding helmet with a suitable filter shade to protect your eyes from arc flash.
- Use flame-resistant welding gloves and clothing to protect against sparks and hot metal.
- Ensure that all protective clothing is free of oils or flammable liquids.
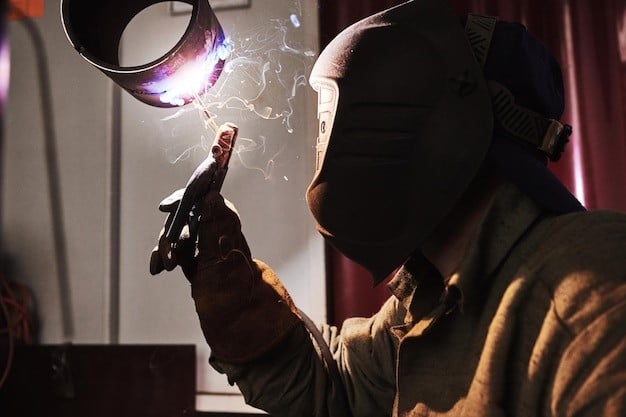
Equipment Checks
- Regularly inspect the TIG welder and any adapted components for wear and damage. Replace any defective parts immediately.
- Verify that all settings on the welder are correctly adjusted for stick welding to prevent overheating and potential equipment failure.
Training and Procedures
- Ensure that all operators are properly trained in TIG and stick welding techniques and that the adapted equipment is set up specifically.
- Develop and follow strict procedural guidelines for setting up and breaking down the equipment to minimize risk.
Common Challenges in Stick Welding with a TIG Welder
Arc Instability
Ar instability is one of the most frequent issues when using a TIG welder for stick welding. This problem often arises due to improper setting adjustments or using incompatible electrodes. Arc instability can lead to uneven welds and difficulty maintaining the arc, which is critical for a consistent weld pool. To mitigate this, it’s crucial to:
- Ensure the power settings are suitable for the type of electrode used.
- Check that cables and connections are secure and in good condition.
Slag Inclusions
Slag inclusions occur when slag, the byproduct of the welding process, becomes trapped inside the weld metal. Stick welding with a TIG welder can be more prevalent if the flux does not properly protect the molten weld pool. To prevent slag inclusions:
- Use the correct angle and speed during welding to allow the slag to rise to the surface of the melt.
- Select appropriate electrodes with compatible flux properties for the base metal.
Spatter
Spatter, the spray of molten metal particles during welding, is a common challenge in stick welding. When using a TIG welder adapted for stick welding, the spatter can increase due to the high temperatures. To reduce spatter:
- Adjust the amperage and polarity settings based on the electrode and material.
- Maintain a steady hand and proper arc length to minimize disturbances in the arc.
Electrode Sticking
Another challenge is electrode sticking, where the electrode fuses into the workpiece, disrupting the welding process. This sticking often results from low current settings or a slow arc strike. Strategies to prevent electrode sticking include:
- Ensuring the current setting is high enough to maintain the arc without overheating the electrode.
- A ‘scratch start’ technique with a swift and smooth motion establishes the arc.
The Importance of Multi-Process Welders
Multi-process welders are invaluable in modern fabrication and repair work because they can handle various welding techniques with a single machine. These versatile units can switch between processes like TIG, MIG, Stick welding, or even plasma cutting without needing multiple, space-consuming setups. This adaptability saves space, reduces costs, and increases workflow efficiency, as operators can seamlessly transition between tasks without significant downtime.
One standout model in this category is YesWelder’s FIRSTESS CT2050. It’s a 7-in-1 multi-function welder and cutter that epitomizes the benefits of multi-process machines. Capable of performing AC/DC TIG, AC/DC Pulse TIG, Stick Welding, and Plasma Cutting, the FIRSTESS CT2050 is designed for novice and experienced welders who require a wide range of capabilities. It supports a variety of materials and applications, making it a practical choice for both shop and field work. With features like a built-in air compressor and advanced IGBT inverter technology, the CT2050 combines performance with portability, representing a smart investment for those looking to maximize their welding capabilities with a single piece of equipment.
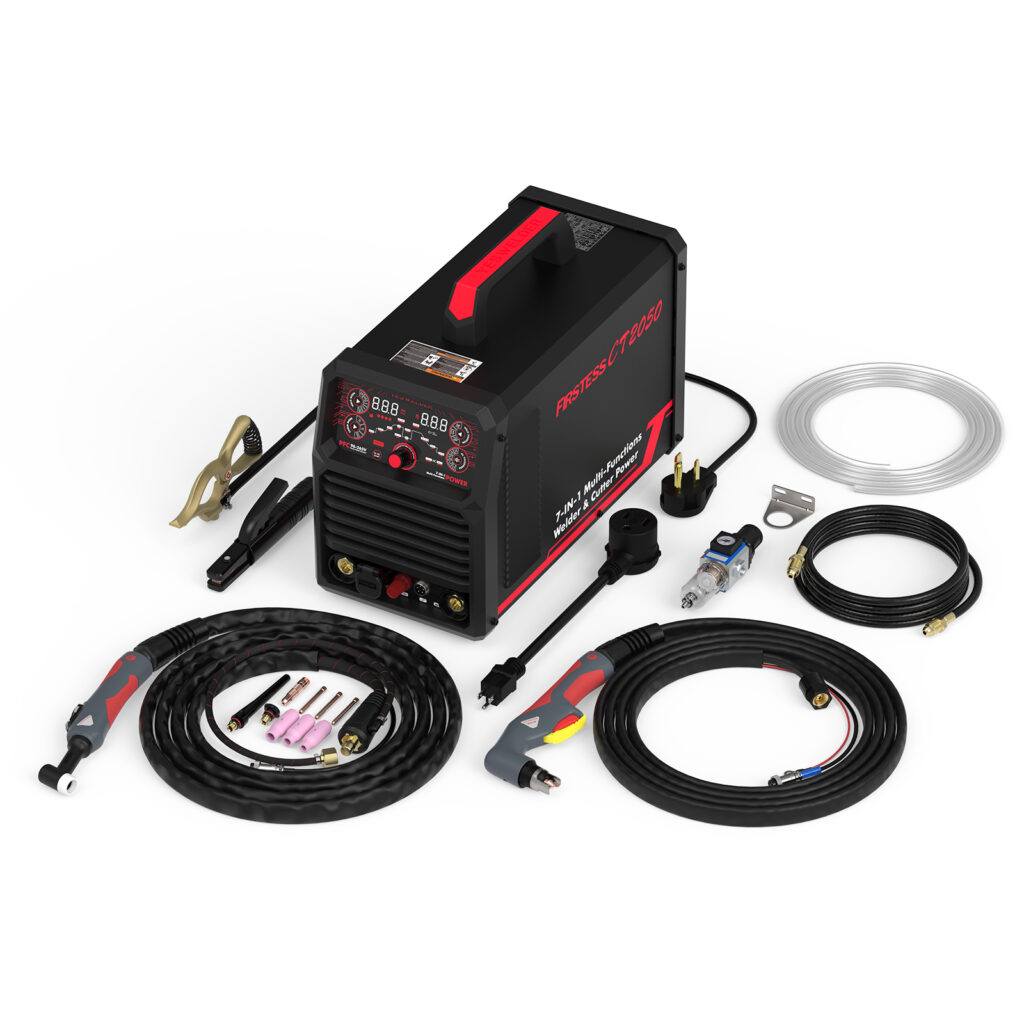
Final Thoughts
Adapting a TIG welder for stick welding offers a practical solution for welders looking to expand their capabilities without incurring the high costs of additional equipment. The flexibility to switch between TIG and stick welding processes using a single machine enhances both productivity and versatility, making it a valuable skill set for any welder.
For those requiring an even broader range of functionalities, multi-process welders from professional suppliers like YesWelder provide an all-in-one solution that covers various welding and cutting needs. This adaptability is crucial in today’s diverse fabrication environments, where efficiency and cost-effectiveness are paramount.
FAQs
Can you use a TIG welder for stick welding?
Many TIG welders can be adapted for stick welding by modifying the setup to use stick electrodes and adjusting the settings to suit the stick welding process.
What are the main advantages of using a TIG welder for stick welding?
The primary advantage is versatility. A TIG welder configured for stick welding can save space and cost by reducing the need for multiple machines.
Are any specific considerations or modifications needed to use a TIG welder for stick welding?
Yes, modifications include attaching a compatible stick electrode holder and adjusting the power settings to match the requirements of stick electrodes, ensuring effective welding.
What challenges might you face when using a TIG welder for stick welding?
Potential challenges include managing different electrode handling and feed rates and ensuring the power and settings are correctly adjusted for effective stick welding.