In today’s fast-paced manufacturing industry, manual welding struggles to keep up with the rising demand for precision, speed, and safety. Human welders often face challenges in maintaining consistent quality across long shifts, leading to inefficiencies and potential hazards. The solution lies in welding automation, which leverages advanced technologies to handle repetitive tasks with greater accuracy and safety.
Automated systems not only ensure consistent weld quality but also enhance productivity, reduce human error, and improve overall workplace safety. As welding robots and collaborative systems become more advanced and affordable, they offer a practical way to overcome these challenges and meet the growing needs of industries like automotive, aerospace, and construction.
Types of Welding Automation
Fixed Welding Systems
Fixed welding systems, such as robotic welding cells, are designed for high-volume, repetitive tasks in controlled environments. These systems are stationary and typically consist of robots placed within a designated welding cell. The robots execute pre-programmed welding tasks, ensuring precise, consistent welds. This setup is ideal for industries like automotive manufacturing, where large production runs require repeatable accuracy. However, these systems are less adaptable to changes in task requirements due to their fixed nature.
Flexible Welding Systems
Flexible welding systems, including collaborative robots (cobots) and mobile welding units, offer more adaptability than fixed systems. Cobots work alongside human operators, enhancing productivity by taking over repetitive tasks while allowing humans to focus on complex jobs. Mobile welding units are designed to move around a workspace, making them suitable for applications where weld locations vary frequently, such as construction or shipbuilding. These systems provide flexibility and versatility, allowing for easier integration into different working environments.
Hybrid Welding Systems
Hybrid welding systems combine the strengths of both fixed and flexible welding systems. They utilize robotic components for repetitive tasks but allow for manual intervention when necessary. This combination offers a balance of automation and human control, making them suitable for industries where both precision and adaptability are required. Hybrid systems are often used in applications that require a mix of high-quality automated welds and complex, custom welds that benefit from human expertise.
Table Explaining the Types of Welding Automation
Type | Key Features | Advantages | Disadvantages | Example Applications |
Fixed Welding Systems | Stationary, designed for high-volume, repetitive tasks in controlled environments | High precision, consistent welds, ideal for mass production | Less flexible, high setup cost | Automotive manufacturing, appliance production |
Flexible Welding Systems | Includes cobots and mobile welding units, adaptable to various tasks and environments | Flexibility, can work alongside humans (cobots), suitable for variable tasks | Lower payload capacity, slower than fixed systems | Construction, shipbuilding, small-scale manufacturing |
Hybrid Welding Systems | Combines robotic automation with manual welding intervention for complex tasks | Balances automation and human control, suitable for custom welds | Requires both automation and skilled human labor | Aerospace, shipbuilding, custom fabrication tasks |
Technological Backbones in Welding Automation
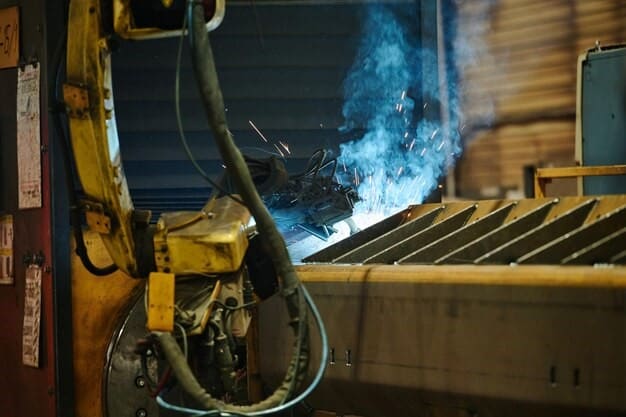
Robotic Welding
- Automated precision: Robotic welding systems use programmed machines to execute welding tasks with high precision and consistency. These systems reduce human errors and enhance production quality.
- Increased productivity: Robots can operate continuously without fatigue, making them ideal for high-volume production environments where repetitive tasks are common.
- Cost efficiency: Although initial investment is high, robotic welding reduces long-term operational costs by minimizing rework and improving overall efficiency.
- Wide applications: Robotic welding is used in various industries, such as automotive, aerospace, and shipbuilding, where consistency and speed are crucial.
Computer Numerical Control (CNC) Systems
- Precision control: CNC systems manage the movement of welding tools with extreme accuracy, ensuring that welds meet exact specifications. They are essential for complex welding tasks that require precise execution.
- Automation integration: CNC machines can be integrated into welding automation systems to enhance control over the welding process, reducing the need for manual intervention.
- Customizability: These systems allow for custom programming to handle various materials and welding techniques, making them versatile for different industrial needs.
- Reduced waste: CNC systems minimize material waste by controlling the exact amount of material used during the welding process, improving efficiency.
Advanced Sensors and Monitoring Systems
- Real-time feedback: Advanced sensors monitor weld quality in real-time, detecting defects like cracks or porosity early in the process, which helps avoid costly rework.
- Enhanced safety: Monitoring systems ensure the safety of the operator by constantly tracking environmental conditions such as temperature and gas levels.
- Predictive maintenance: These sensors help predict maintenance needs by monitoring the performance of welding equipment, reducing downtime, and extending the lifespan of the machinery.
- Improved accuracy: By continuously tracking weld parameters, sensors enable fine-tuning of the welding process, ensuring high-quality results.
Benefits of Welding Automation
Increased Productivity
Welding automation dramatically enhances productivity by reducing manual intervention. Automated systems can work continuously without breaks, leading to a significant increase in output. In industries with high-volume demands, such as automotive manufacturing, automated welding reduces cycle times, allowing businesses to meet production targets more efficiently. The elimination of human fatigue also ensures consistent performance throughout long shifts, resulting in faster project completion.
Consistent Quality
One of the key advantages of welding automation is the ability to maintain consistent quality across all welds. Manual welding can vary depending on the operator’s skill, fatigue levels, or welding machine types like a MIG welder or a TIG welder. Automated welding systems are programmed to follow precise instructions, producing uniform welds with minimal defects. This leads to fewer errors and less rework, ultimately improving the overall quality of the product.
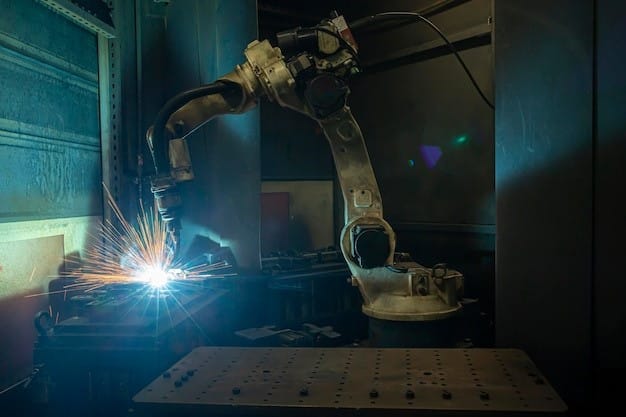
Improved Safety
Welding automation significantly reduces the risk of injuries associated with manual weldings, such as exposure to fumes, extreme heat, and radiation. Robots and automated systems can handle hazardous tasks while minimizing direct human involvement. By removing the operator from dangerous environments, companies can better comply with safety regulations and protect their workforce from accidents and health issues.
Long-Term Benefits
While the initial investment in welding automation may be high, the long-term benefits often outweigh the costs. Automated systems lead to lower operational expenses by increasing efficiency, reducing waste, and minimizing the need for rework. Over time, these systems also require less labor, lowering wage-related costs. The improved quality and faster production times help companies achieve better profit margins and a quicker return on investment.
Reduced Material Waste
Automated welding systems contribute to reducing material waste by controlling the welding process with greater precision. The machines are programmed to use the exact amount of material needed for each weld, preventing excess usage. This is particularly important in industries where material costs are high, such as aerospace and shipbuilding. Reducing waste not only cuts costs but also aligns with sustainability goals by minimizing resource consumption.
Scalability for Future Growth
As companies grow, manual welding processes may struggle to keep up with increasing production demands. Welding automation provides a scalable solution that can easily adapt to higher workloads. Additional robots or systems can be integrated into existing workflows without major disruptions. This flexibility allows businesses to expand operations efficiently, ensuring they can meet future demand without sacrificing quality or productivity.
Challenges of Welding Automation
Initial Investment
The upfront cost of implementing welding automation is a major barrier for many businesses. Purchasing the required machinery, robotic systems, and software can be expensive, especially for smaller companies. Additionally, installation, setup, and integration costs add to the overall investment. Despite long-term cost savings, the initial expenditure can be prohibitive, delaying the adoption of automation for some organizations.
Skill Gaps
Welding automation requires specialized knowledge for programming, operation, and maintenance. As technology evolves, the demand for skilled workers handling automated systems increases. However, many traditional welders may lack the technical skills needed for these roles, creating a skills gap. Companies need to invest in training and education to ensure their workforce can effectively use and maintain the new systems.
Workforce Transition
The transition to welding automation often raises concerns about job displacement. While automation can create new opportunities in programming and system maintenance, workers accustomed to manual welding may struggle with the shift. This transition requires businesses to carefully manage workforce changes, offering retraining and support to ensure employees can adapt to new roles within the automated environment.
Integration with Existing Processes
Integrating welding automation with existing workflows can be complex. Automated systems must be aligned with the company’s current production lines, equipment, and standards. This process often requires significant adjustments and testing to ensure that the new systems function smoothly without disrupting existing operations. Proper planning and coordination are essential to minimize downtime during the transition to automation.
Industry Applications of Welding Automation
Automotive Industry
Welding automation plays a critical role in the automotive industry, where high production volumes demand precision and efficiency. Robotic systems are used to weld components such as chassis frames and body panels. Automation ensures that each weld is consistent, contributing to improved vehicle safety and reducing production time. The automotive industry relies heavily on these systems to meet growing market demands.
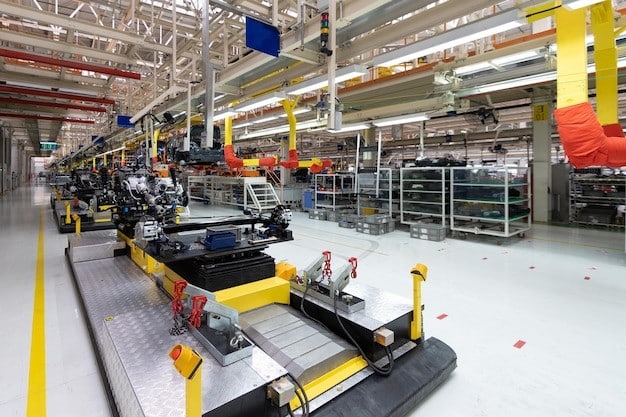
Aerospace Industry
In the aerospace industry, welding automation is essential for assembling complex components like aircraft wings and fuselages. The precision offered by robotic welding systems ensures high-quality welds that meet strict safety and performance standards. Aerospace applications also benefit from reduced material waste and improved repeatability, which are crucial in producing critical parts for planes and spacecraft.
Infrastructure Construction
Welding automation is used in infrastructure construction projects, especially for welding structural steel components like beams and columns. Automated systems help construction companies meet tight deadlines by speeding up the welding process. This technology also improves the quality and durability of welds, ensuring that structures such as bridges and high-rise buildings are safer and more reliable.
Shipbuilding and Marine
In shipbuilding, welding automation is essential for constructing large, complex structures like ship hulls and decks. Automated systems handle the repetitive and precise welds needed for such large-scale projects. By improving weld quality and reducing manual labor, automation in the marine industry helps streamline ship construction, making the process faster and more cost-effective.
Future Trends in Welding Automation
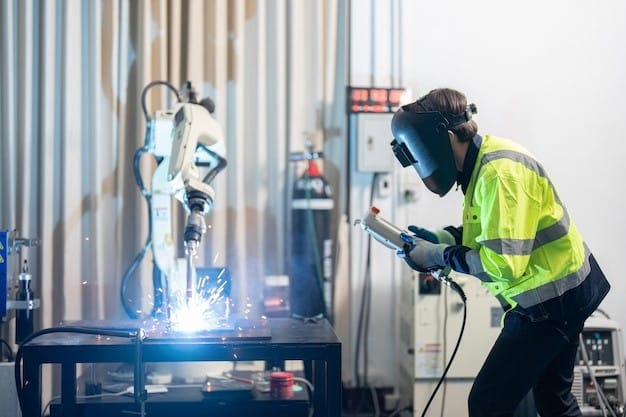
Advanced AI-Driven Systems
AI-driven welding systems are set to transform the industry by allowing machines to make real-time adjustments based on environmental and material factors. These systems will enhance precision, reduce errors, and improve overall efficiency. As AI continues to evolve, welding automation will become smarter and more adaptive.
Industry 4.0
Industry 4.0 integrates welding automation with smart manufacturing. By connecting welding systems with data analytics and the Internet of Things (IoT), manufacturers can monitor and optimize welding processes remotely. This leads to better quality control, predictive maintenance, and streamlined operations across industries.
Green Welding
Sustainability is driving innovation in welding automation through green welding technologies. These systems aim to reduce energy consumption and minimize emissions. Green welding also focuses on reducing material waste, making the process more environmentally friendly and cost-effective in the long run.
Final Thoughts
Welding automation is revolutionizing industries by increasing productivity, ensuring consistent quality, and improving safety. As technologies like AI and Industry 4.0 evolve, the future of welding automation looks promising, and welding machine suppliers will provide more and more exciting outcomes. With a focus on sustainability and adaptability, these advancements will continue shaping more efficient and environmentally friendly manufacturing processes.
FAQs
What are the main benefits of welding automation?
Welding automation improves productivity, ensures consistent weld quality, enhances safety, and lowers costs over time by reducing errors and material waste.
How does welding automation impact the workforce?
It shifts workforce needs, requiring fewer manual welders and more skilled operators and technicians to manage and maintain automated systems.
What industries benefit the most from welding automation?
Industries like automotive, aerospace, construction, and shipbuilding benefit most from welding automation due to high production demands and the need for precision.