What process welds at 3000°C without applying a power source? Meet thermit welding—fascinating, century-long technology that’s still revolutionizing industries today. Hailed for its smooth, durable joints, thermit welding (or exothermic welding) uses an internal heat source to melt and bond metals together.
What Is Thermit Welding?
Thermit welding is an exothermic fusion welding process that uses a reaction between a metal oxide (typically iron oxide) and aluminum powder to generate molten metal for joining.
It does not require or use external energy in the form of an arc or gas—it takes only a spark to ignite the mixture, or thermite. What is generated is a pool of highly superheated liquid metal that fills a mold, fusing parts when it cools.
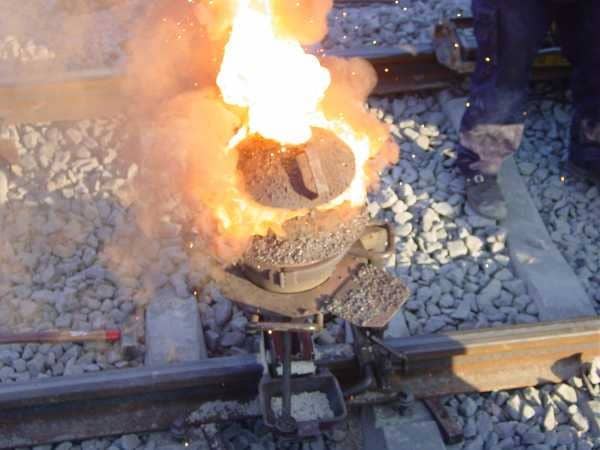
Public Domain, https://commons.wikimedia.org/w/index.php?curid=1719556
The process originated in 1895, when German chemist Hans Goldschmidt developed the aluminothermic process – the basis for the thermit welding process.
By 1904, railway maintenance was transformed using this method, allowing workers to weld rail ends in the field without the need for cumbersome machinery.
Picture 20th-century crews casting fire-embers on Europe’s expanding railroad network. Its heyday was during the 1920s–30s with millions of welds documented worldwide. Nowadays, it is not utilized as much anymore—60% less since 2000, as revealed by a 2022 report by the rail industry—but still utilized for distant repair and specialized applications.
The Science Behind Thermit Welding
Thermit welding hinges on a controlled chemical reaction:
8Al + 3Fe3O4 → 9Fe + 4Al2O3 + heat
Here’s how it works: 8 units of aluminum combine with 3 units of magnetite (Fe₃O₄) to produce 9 units of molten iron and 4 units of aluminum oxide slag, along with a burst of heat—at up to 4500°F (2500°C) at the reaction center.
The resulting molten iron, about 3000°C, is poured into a mold to bond metal pieces. The typical thermite combination is 1 part aluminum powder to 3 parts iron oxide by weight, ground into a light, gray powder.
To specialized welds, alloying elements like manganese (for toughness) or nickel (for corrosion resistance) may be added, changing the iron’s properties.
This self-sustaining exothermic reaction emits about 850 kJ/mol of energy when ignited—far more than necessary to melt steel edges without a torch or generator. Fun fact: Thermite heat was even utilized in WWII to melt tank armor. It is now precision-recalled to weld.
The Thermit Welding Process: Step-by-Step
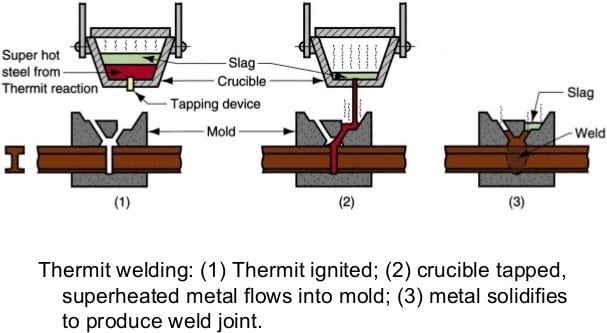
Preparation
Clean the metal surfaces (e.g., rail ends) with a wire brush to remove rust and dirt. Align them with a 1–2 inch gap, depending on joint size.
Build a mold around the gap using refractory sand or ceramic, shaped to match the weld profile (e.g., rail head).
Preheat the area around with a propane torch 10–15 minutes to 300–500°C, making moisture burn off and allow fusing. The foe is moisture—steam explosion is danger if trapped. (For rail welds, preheating to 500°C ensures the molten iron bonds deeply, reducing cracks.)
Equipment Setup
Place a crucible (normally graphite-lined steel) over the mold, connected by a tapping hole. A typical crucible holds 5–10 kg of thermite for a rail weld.
Charge the mixture of thermite, topped with ignition powder (barium peroxide or magnesium ribbon).
Clamp the setup in place—any tilt risks spillage of 3000°C metal.
Reaction
Ignite the powder with a flint gun or sparkler. The reaction is 20–30 seconds long, giving a brilliant flash and a hiss as the thermite ignites.
When done, tap the crucible to fill the mold with molten iron, filling within seconds. Excess metal is caught by the mold, forming a collar at the joint.
Finishing
- Allow to cool naturally for 15–30 minutes (forced cooling reduces strength of weld).
- Smash mold away with a hammer, revealing the weld and slag layer (aluminum oxide).
- Cut off excess metal with an angle grinder for a smooth, flush finish.
Types of Thermit Welding
Thermit welding isn’t one-size-fits-all. Each type tweaks the reaction for specific metals, making thermit welding versatile beyond steel.
- Standard Thermit Welding: Uses iron oxide and aluminum to weld steel—perfect for railway tracks.
- Copper Thermit Welding: Swaps iron oxide for copper oxide to join copper parts, common in electrical grounding systems.
- Specialized Variants: Includes magnesium-based mixes or proprietary blends (e.g., Orgo-Thermit’s “SkV Weld”) for specific applications.
Applications of Thermit Welding
Thermit welding shines in practical, high-stakes scenarios:
Railway Welding: Binds rail ends together to create uninterrupted track, appreciated for unbroken strength.
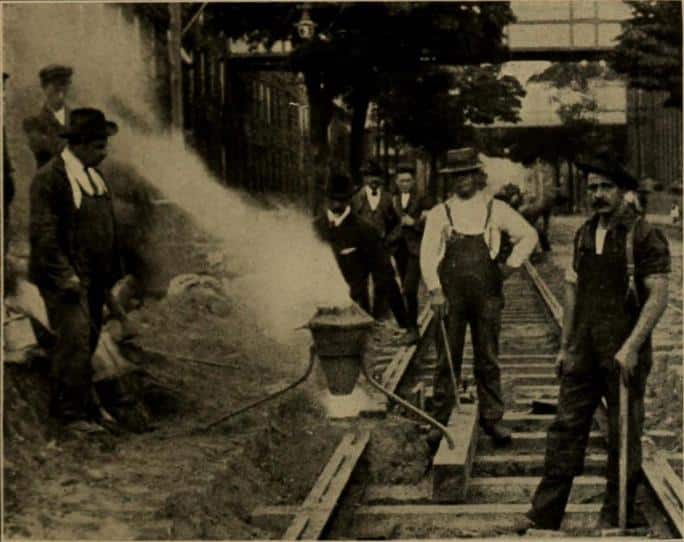
Source: Ernest Stütz: The Thermit Process in American Practice
Electrical Joints: Copper thermite joins busbars, transmission lines, and grounding systems. One weld carries 1000+ amps, with no seams to corrode.
Heavy Machinery: Fixes massive steel components—think 10-ton ship propeller shafts or steel mill rolls. In a 2019 project, a thermit weld fixed a broken press frame in less than 2 hours, avoiding weeks of downtime.
Other Uses: Historically, thermite incendiary bombs disabled artillery in WWI and WWII. Today, it’s an emergency fix for out-of-the-way pipeline repair or developing world structural steel.
Advantages and Disadvantages of Thermit Welding
Thermit welding has unique pros and cons. It’s a trade-off between rugged simplicity and modern efficiency.
Advantages | Disadvantages |
No electricity needed | Highly expensive materials and skilled labor |
Strong, smooth welds with great durability and corrosion resistance | Limited precision and reusability—one shot per weld |
Simple setup | Molten metal and fume safety hazards |
Safety Protocols for Thermit Welding
Thermit welding’s heat and materials demand caution. Here’s how to stay safe:
1. Risks: Burns from metal at 3000°C, eye injury from intense light, inhaling fumes.
2. Protocols:
- Wear PPE like heat-resistant welding gloves, welding helmet, and apron.
- Provide ventilation—avoid enclosed spaces to dissipate fumes.
- Use dry molds and tools—water can trigger explosions.
- Train thoroughly—ignition and pouring require precision.
Wrap Up
Thermit welding is a chemistry and engineering wonder—converting powder to molten metal to form unbreakable bonds. From its roots in railroads to modern-day niche uses, it marries simplicity with power, despite encroachment from newer methods.
Want more about welding applications? Read our blogs on: “Welding Applications and Their Advantages”. Or you can learn more about different types of welding on “Different Types of Welding: A Comprehensive Guide”.
FAQ
Is thermit welding the same as exothermic welding?
Yes, they’re two names for the same reaction-based process.
Can thermit welding be used on aluminum?
No—the reaction requires compatible metals like steel or copper, not aluminum itself.
How long does the thermit welding process take?
From setup to finish, about 30–60 minutes, and the size depending.
How much time does thermit welding take?
The method begins with mixing and igniting the thermite mixture. When ignited, the reaction produces intensely high temperatures (typically to approximately 2500°C–4500°F).
The metal is then poured into an existing mold or gap between the workpieces, and when it hardens, it forms a firm, permanent bond.
Is thermit welding suitable for all types of metals?
It is predominantly used for ferrous metals (for example, steel) like rail welding. There are also variations of the thermite process in non-ferrous metals (for example, copper), where the metal oxide within the thermite mixture is adjusted accordingly based on the proposed application.