When TIG welders are not properly maintained, their performance deteriorates, leading to subpar welds, equipment failures, and potential safety hazards. The accumulation of debris, worn-out parts, and improper calibrations can severely affect the quality and longevity of the welds. Regular and systematic maintenance of TIG welders is essential to address these issues.
You can ensure the equipment remains in optimal condition by adhering to a structured maintenance schedule that includes daily checks, periodic servicing, and annual overhauls. This improves the quality of the welds and extends the welder’s life, ensuring safe and efficient operations over the long term.
Key Components of TIG Welders
The key components of a TIG welder are critical to its functionality and performance. Each part plays a unique role in ensuring that the welding process is efficient and produces high-quality results.
Torch
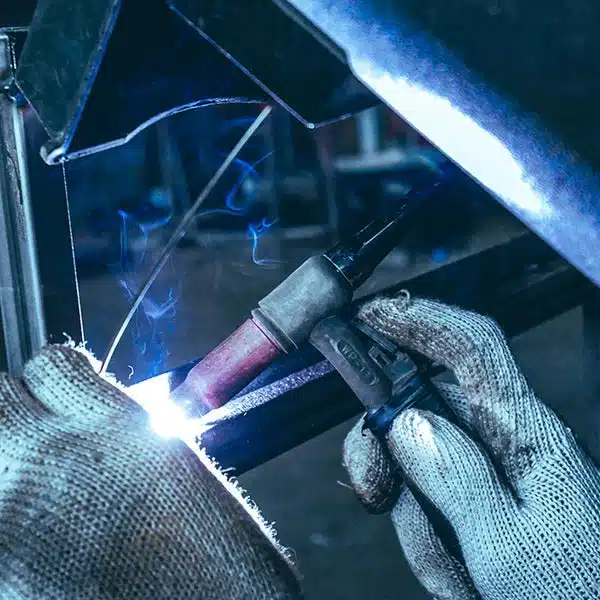
The torch is the primary tool in TIG welding. It directs the welding current to the workpiece, holds the electrode, and allows the welder to control the arc. The torch’s design and cooling system can withstand high temperatures during prolonged use. Regular inspection and maintenance of the torch are necessary to prevent issues like overheating and maintain a stable arc.
Foot Pedal
The foot pedal in a TIG welder controls the amperage, giving the welder precise control over the heat applied during the welding process. This control is essential for achieving smooth, consistent welds, especially on materials that require varying heat levels. Ensuring that the foot pedal functions properly is crucial for maintaining this control. Any malfunction can lead to inconsistent weld quality, so regular checks and maintenance are vital.
Power Source
The power source in a TIG welder provides the necessary electrical energy to create the welding arc. Depending on the welded material, it must be stable and capable of delivering AC and DC currents. Proper power source calibration and maintenance ensure consistent output, preventing arc instability and poor weld penetration. Regular servicing can also extend the life of the power supply, reducing the likelihood of unexpected failures.
Electrode
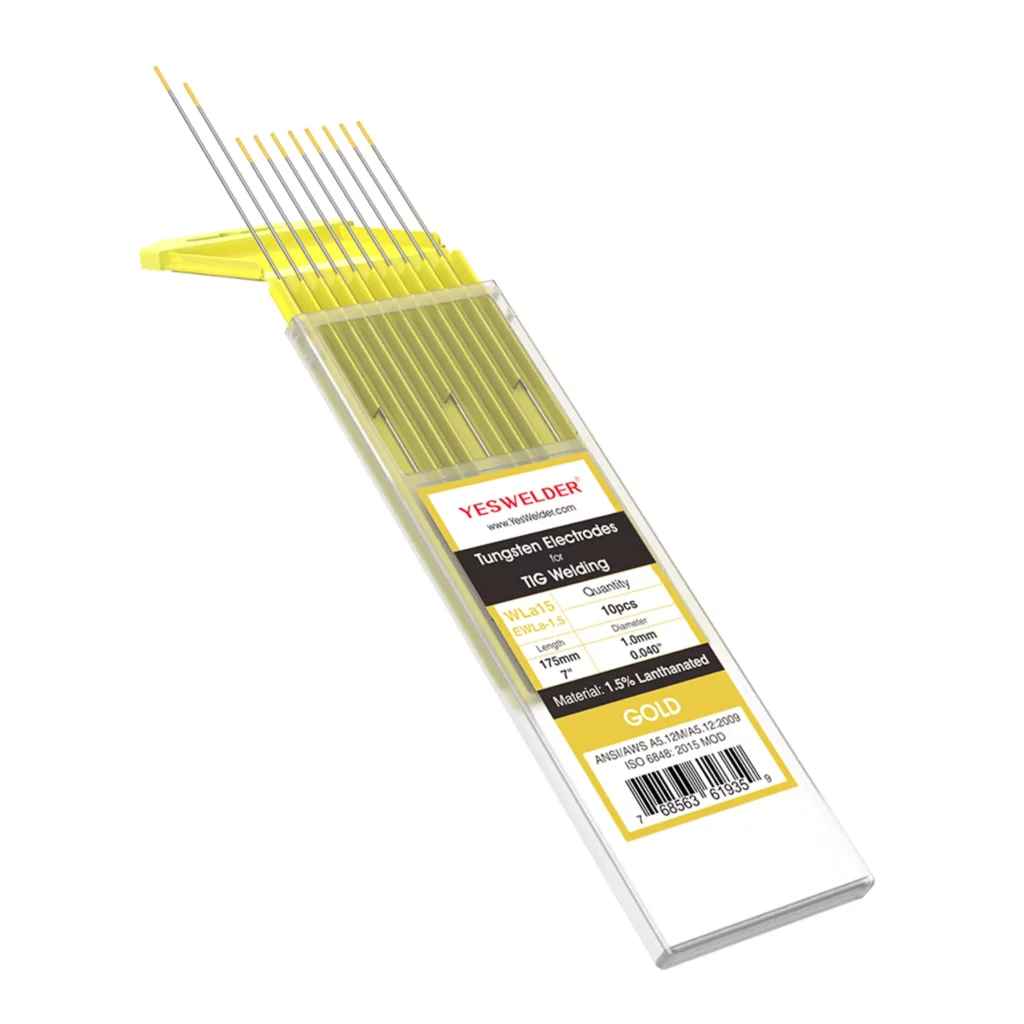
TIG welding tungsten electrodes are typically made of tungsten and are responsible for conducting the welding current to the workpiece. The choice of electrode type and its condition directly affects the quality of the weld. Over time, electrodes can become contaminated or worn, leading to arc instability and poor weld quality. Sharpening and replacing electrodes regularly are essential to maintaining optimal welding performance.
Gas Supply System
The gas supply system in TIG welding provides the shielding gas, typically argon, that protects the weld area from atmospheric contamination. This system includes gas cylinders, regulators, and hoses, all of which must be in good condition to ensure a steady gas flow. Any leaks or blockages in the gas supply system can lead to weld defects, so regular inspection and maintenance of this system is critical for producing clean, strong welds.
Maintenance Tasks
Daily Maintenance Tasks
- Inspect the Torch: Ensure the torch is free from debris and damage. Check the nozzle, collet, and back cap for wear. Clean or replace any worn components to maintain a stable arc.
- Check the Electrode: Verify that the electrode is sharp and clean. Replace or sharpen it if necessary to ensure a consistent arc and quality welds.
- Examine the Foot Pedal: Test the foot pedal’s responsiveness. Ensure it controls the amperage smoothly. Any stiffness or irregularities should be addressed immediately to maintain control over the welding process.
- Inspect the gas supply: Check the gas flow rate and ensure no leaks in the hoses or connections. A consistent gas flow is crucial for protecting the weld from contamination.
- Clean the Work Area: Remove any dust, dirt, or debris from the work area and the welder. This prevents contamination and ensures a safe and efficient working environment.
Weekly & Monthly Maintenance Tasks
- Check All Cables and Connections: Inspect all cables, connectors, and hoses for signs of wear, fraying, or damage. Replace any damaged components to prevent power loss or gas leaks during welding.
- Test the Power Source: Perform a routine check of the power source, including voltage output and amperage stability. If necessary, calibrate the settings to ensure the welder delivers consistent performance.
- Clean the Cooling System: If your torch is water-cooled, check the coolant level and clean the cooling system. Ensure no blockages or leaks could lead to overheating during extended welding sessions.
- Examine the Ground Clamp: Inspect the ground clamp for any signs of wear or corrosion. A strong, clean ground connection is essential for maintaining a stable arc and preventing electrical issues.
- Review the Gas Cylinder: Check the gas cylinder for proper pressure and ensure the regulator functions correctly. Replace the cylinder if it is nearly empty, and check the regulator for any signs of wear or leaks.
Annual Maintenance Tasks
- Full System Inspection: Conduct a thorough inspection of the entire TIG welding system, including the torch, power source, cables, and gas supply system. Look for any signs of wear, corrosion, or other damage that could affect performance.
- Calibrate the Power Source: Perform a detailed calibration to ensure it meets the manufacturer’s specifications. This includes checking the output for AC and DC currents and adjusting as needed.
- Replace Worn Components: Identify and replace worn or outdated components, such as the torch nozzle, collet, or gas lenses. This prevents unexpected failures during operation and ensures the system remains in top condition.
- Service the Cooling System: Drain and replace the coolant in water-cooled systems and clean the entire cooling circuit. Ensure that the pump and hoses are functioning correctly to avoid overheating.
- Consult the Manufacturer: Review the manufacturer’s recommendations for additional maintenance tasks or updates. Consider scheduling a professional service visit to perform more complex tasks or address recurring issues.
TIG Welder Maintenance Tasks
Maintenance Task | Frequency | Benefits |
Inspect Torch | Daily | Ensures proper cooling, prevents overheating and extends component life. |
Check Electrode | Daily | Maintains consistent arc, improves weld quality, and reduces contamination. |
Examine Foot Pedal | Daily | Ensures smooth amperage control, improving weld consistency. |
Inspect Gas Supply | Daily | Ensures stable arc, prevents overheating and maintains weld quality. |
Clean Work Area | Daily | Reduces contamination risks, ensures safety, and promotes efficient work. |
Check Cables and Connections | Weekly/Monthly | Prevents power loss, reduces the risk of gas leaks, and ensures stable performance. |
Test Power Source | Weekly/Monthly | Ensures consistent output, prevents arc instability, and improves weld penetration. |
Clean Cooling System | Weekly/Monthly | Prevents overheating, prolongs component life, and maintains welder efficiency. |
Inspect Ground Clamp | Weekly/Monthly | Ensures strong ground connection, preventing electrical issues. |
Full System Inspection | Annually | Identifies wear and tear, ensures all components are in optimal condition, and prevents unexpected failures. |
Calibrate Power Source | Annually | Ensures precise operation, improves weld quality, and maintains manufacturer standards. |
Replace Worn Components | Annually | Prevents unexpected failures, maintains optimal performance, and extends welder life. |
Service Cooling System | Annually | Ensures proper cooling, prevents overheating, and extends component life. |
Tips for Extending the Life of TIG Welders
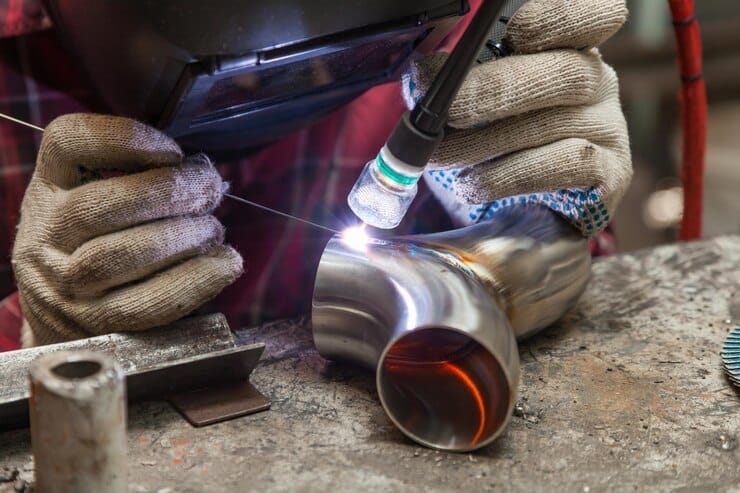
- Regular Inspection: Inspect all components, including the torch, cables, and gas supply system. Identifying and addressing minor issues early can prevent costly repairs and extend the welder’s lifespan.
- Proper Storage: Store the TIG welder in a clean, dry environment. Moisture and dust can lead to corrosion and other damage, so keeping the equipment in a controlled environment will help preserve its condition.
- Use Quality Consumables: Always use high-quality electrodes, gas lenses, and other consumables. Low-quality parts can wear out faster and cause damage to the welder, reducing its overall life.
- Monitor Cooling Systems: Ensure that the cooling systems, whether air—or water-cooled, function correctly. Overheating is a common damage cause, so keeping the cooling system in top condition is essential.
- Follow Manufacturer Guidelines: Adhere to the manufacturer’s maintenance and operation guidelines. These recommendations are tailored to the specific welder model and are crucial for long-term durability.
- Avoid Overloading: Do not exceed the welder’s capacity, whether in terms of amperage or duty cycle. Overloading the welder can cause overheating and long-term damage, leading to reduced performance.
- Clean After Use: After each use, clean the torch, cables, and any other parts that may have come into contact with welding debris. This simple task prevents buildup that can interfere with the welder’s operation and prolongs its life.
- Professional Servicing: Schedule professional servicing at regular intervals, especially for complex tasks like calibration. Professional maintenance ensures that all aspects of the welder are in optimal condition and can help catch issues that may not be visible during routine checks.
Final Thoughts
After getting the machine from reliable TIG welder suppliers, maintaining a TIG welder is essential to ensure its longevity and consistent performance. Regular inspections, proper usage, and adherence to a well-planned maintenance schedule can prevent common issues that lead to equipment failure. By following the tips and guidelines provided, operators can extend the life of their TIG welders and improve the quality of their welds. Investing time in daily, weekly, and annual maintenance tasks is a small effort that yields significant benefits regarding safety, efficiency, and cost savings. A well-maintained TIG welder is an asset that contributes to better welding results and a longer operational life.
FAQs
How often should I perform maintenance on my TIG welder?
Daily inspections and cleaning should be done after every use, while more thorough checks, like cable inspections and power source calibration, should be carried out weekly or monthly. Annual maintenance involves a complete system check to ensure all components function properly.
What are the key components that require regular maintenance in a TIG welder?
The primary components that need regular maintenance include the torch, foot pedal, power source, electrode, and gas supply system. Each plays a critical role in the welder’s performance and must be kept in good condition to ensure optimal operation.
Can any type of electrode be used for TIG welding?
No, TIG welding typically requires tungsten electrodes available in different types (e.g., pure tungsten, thoriated). The choice depends on the welded material and current (AC or DC). Using the correct electrode ensures a stable arc and high-quality welds.
How to manage an overheated TIG welder?
If your TIG welder overheats, immediately stop welding and allow the machine to cool down. Check the cooling system for any issues, and ensure that you are operating within the machine’s duty cycle limits to prevent future overheating.