TIG welding can produce precise and flawless welds. Its success not only depends on skill but also on science. Properly managed melting point of metal with controlled heat ensures clean welds. It directly impacts weld quality, required filler materials, and weld bead flows.
Understanding melting points and how they influence the metal joining process helps achieve the best out of TIG welding. In this guide, we’ll dive deep into the various aspects of TIG welding melting point.
What Is the Melting Point in Welding?
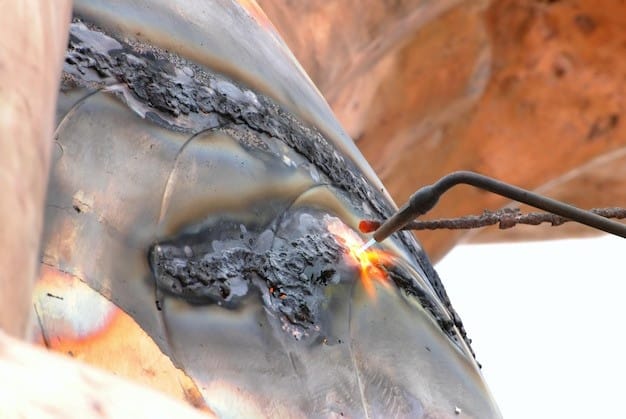
The melting point is the specific temperature level at which a metal transitions from a solid to a liquid state. It allows the metal to fuse with another metal. In general, the melting temperature range is between 660°C and 3422°C.
It’s significant to understand the melting temperature of metal in welding because it determines how the metal reacts under heat. Several factors impact the melting point and it can be changed slightly. Atomic structure, metal impurities, joining type, and the adjacent material can influence the liquefaction temperature of a metal.
Some metals like tungsten have stronger atomic bonds, and their melting point is higher than silver’s, which has weaker bonds. Knowing about these temperatures assists in selecting the right materials, welding type, and appropriate technique for a welding project.
Melting Points of Common Metals in TIG Welding
To work with different materials, in-depth understanding of the melting points is essential. This makes it easy to select suitable parameters such as arc temperature, heat input, and shielding gas in TIG welding.
There are generally three types of metals based on the melting temperatures:
- Low melting point metals
- Medium melting point metals
- High melting point metals
Low melting point metals start melting at lower temperatures, so working with them is easier at low heat settings.High heat input can cause excessive vaporization that is toxic. Careful amperage and heat control are necessary for low melting point materials.
Medium melting point metals such as copper, gold, brass require medium heat input to achieve the best fusion. These metals have melting temperatures between 930°C and 1204°C. Welding on Gold and other valuable metals can get benefits from TIG welding controlled arc.
Using high melting point metals in TIG welding require expertise and specialized techniques to ensure clean welds. These metals melt at higher temperature input. When welding these metals, proper heat control and oxidation prevention are significant for a safe weld.
The chart below shows the melting points of commonly used metals:
Metal | Melting Point (°C) |
Lead | 327°C |
Zinc | 420°C |
Aluminum | 660°C |
Silver | 961°C |
Copper | 1085°C |
Gold | 1064°C |
Brass | 930°C |
Cast Iron | 1204°C |
Carbon Steel | 1425°C |
Stainless Steel | 1375°C |
Nickel | 1453°C |
Titanium | 1670°C |
Chromium | 1860°C |
Platinum | 1770°C |
Tungsten | 3422°C |
Why Melting Points Matter in TIG Welding?
Melting points matter because they influence overall weld quality in TIG welding. Let’s learn why the melting point is highly considerable; here are a few points to discuss.
- Controlling Heat
- Compatibility of Metals
- Avoiding Defects
- Precision and Perfection
Controlling Heat: Each metal has a specific melting temperature. For example, aluminum melts at around 660°C, while stainless steel melts at approximately 1,400°C.
When you know these temperatures, you can set the right heat levels on the TIG welder from reliable TIG welder suppliers. Too much heat can cause excessive melting and weakening joints. On the other hand, too little heat may result in an incomplete weld.
Compatibility of Metals: Melting points are important, especially when you’re welding two different metals. If one metal melts faster than the other, it can naturally create uneven welds.
Using the wrong melting temperatures can even destroy your whole welding project. The operator needs to apply the appropriate temperature on the particular metal in the welding process.
Precision and Perfection: TIG welding is popular for producing clean and precise welds. The best welds can be achieved by applying actual melting heat on the materials. It ensures a smoother weld and reduces the chances of overheating.
Avoiding Defects: Improper control of heat for melting can cause defects like cracks and oxidation. TIG welding technique can use an inert gas shield, such as argon, to prevent oxidation.
However, if the melting point isn’t managed correctly, the weld pool may overheat. As a result, the metal joining can be harder to control and protect.
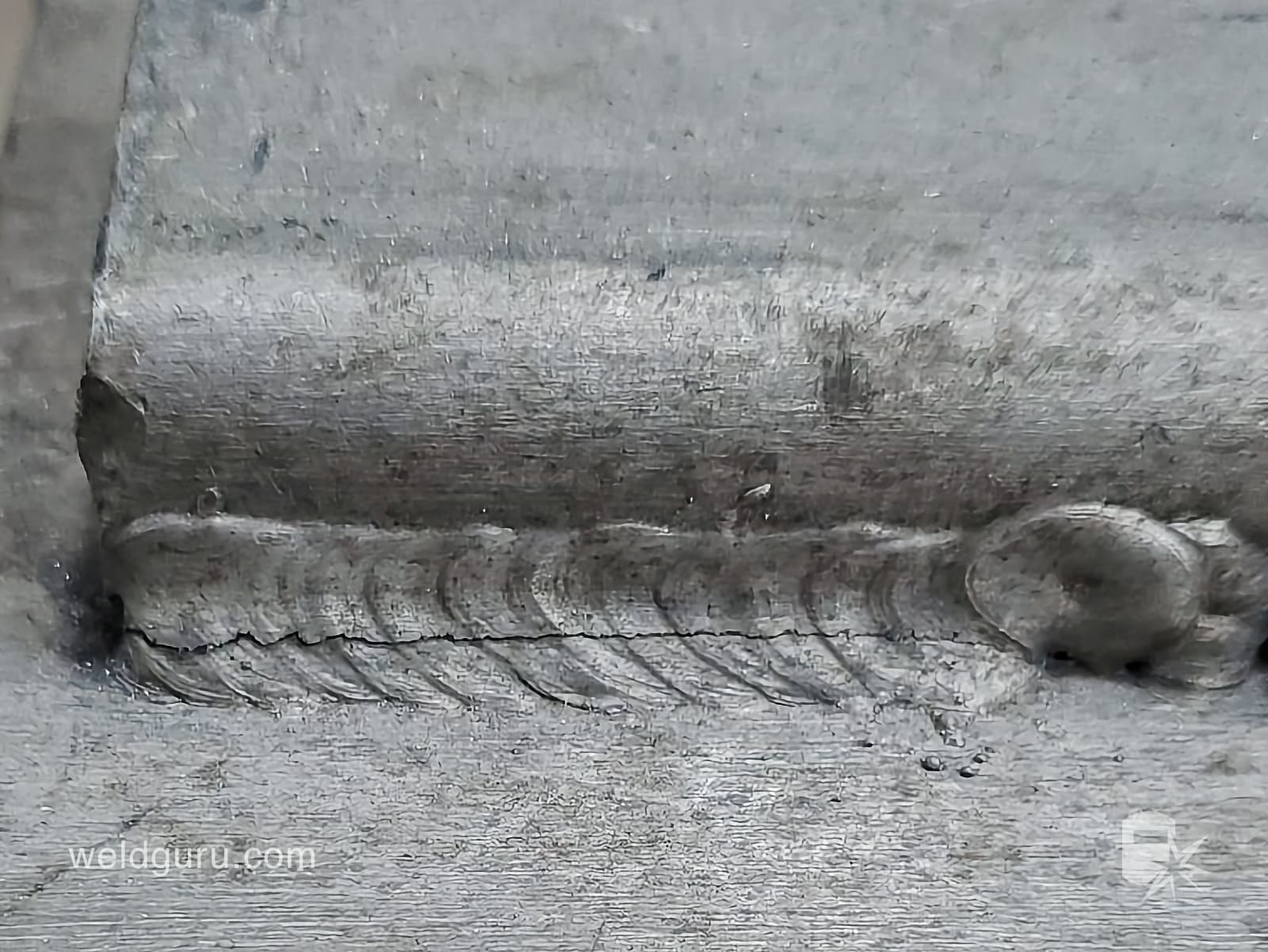
TIG Welding Rod Melting Point
The welding rod is the filler rod in tungsten inert gas (TIG) welding. Its melting point needs to complement the base material for a strong weld. The composition of TIG welding rods is the key element that determines the melting point.
When exposed to the heat of the TIG arc, the rod melts. It then joins with the base metal to create a defect-free joint. TIG rods are produced from alloys closely matching the composition of the base material. For example, stainless steel rods are for steel welding, and aluminum rods are for aluminum welding.
The melting point TIG welding rod and base material should be almost the same. The significant difference in the melting point can make the welding futile.
What Affects Melting Points in TIG Welding?
Several factors affect the TIG welding melting point of various materials. Let’s check how each of the factors plays an important role.

1. Heat Input
Heat input delivers the necessary energy to the weld area. Higher heat input means the increased temperature to melt the metal faster. However, excessive heat may cause material distortion. So, controlled heat input is required for a complete joint without overheating.
2. Arc Temperature
The arc temperature is influenced by current settings and electrodes. A hot arc delivers more energy to the base material to reach its melting point quickly. Controlling this parameter works for melting without compromising weld quality.
3. Shielding Gas Selection
There are several types of shielding gases that affect the melting points of the metals. Argon provides excellent arc stability and suits well low melting points metals. Helium provides higher heat input and helps metals with higher melting points.
4. Preheating and Cooling Rates
Preheating adds temperature to the weld area. When starting the welding process, the metal reaches its melting point easily. It minimizes the required heat input. It’s important for metals with high melting points.
Controlled cooling rates ensure weld integrity and remove defects. These work efficiently for aluminum and stainless steel.
Challenges Related to TIG Welding Melting Points
TIG welding often faces challenges when it comes to metals’ melting points. The frequent difficulties are:
Overheating: TIG welding applies high heat to melt materials. If the heat is too much or not controlled, the metal can overheat. This can weaken the new joint. Consequently, it leads to cracks on the surface.
Base Metals Warping: When heat is applied for too long or too extreme, the base metals can warp. It can change the shape of the metals and make them harder to use in welding.
Welding in Different Melting Points: It is tricky to join two metals with different melting points. The one with the lower melting point can melt too fast and another with higher melting point can melt too slowly. This makes the welding a difficult task.
Burning with High Heat: If the welder uses too much heat, the material may burn through. This creates holes in the material and makes welding tough.
Contamination: Impurities in the metal can affect the melting process. This can turn the welding project into a difficult task.
Oxidation: TIG welding requires shielding gas to protect the weld from the air. If the gas coverage is poor, air can mix with the weld. This causes oxidation and makes the weld weaker.
Optimal Welding on Melting Points: Advanced Tips
Mastering the art of welding requires in-depth knowledge of weld types, metal properties, various techniques, and metal melting knowledge. Here we’ll focus on advanced tips for high-quality welding on melting points.
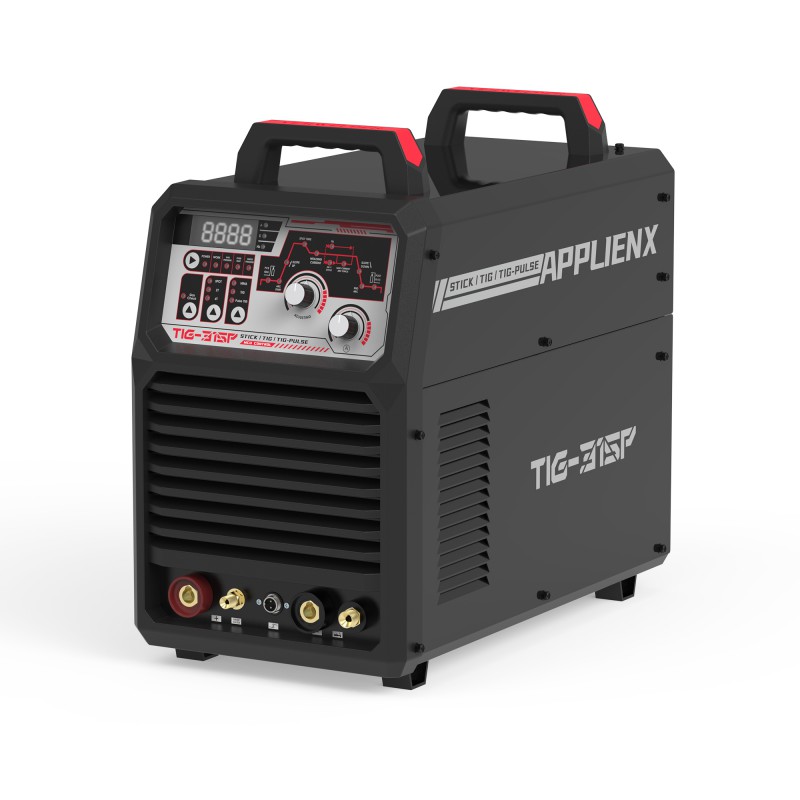
Using Pulse TIG Welding: Some metals are very sensitive to heat, and TIG welding works better for them. Pulse TIG welding controls heat precisely, which results in precise welding on aluminum and stainless steel.
This technique prevents warping and ensures the integrity of the surface. It creates consistent welds without overheating on the metal. Additionally, it’s an efficient way for clean and uniform welds without any spatter.
Managing Weld Pool Dynamics: The molten surface during welding is known as a weld pool. Managing its consistency offers clear welds. Keep your welding speed in control. Moving too fast or slow can lead to poor welds and overheating.
Use the filler metal that matches the base metal’s melting point. Adjust gas flow properly to prevent contamination. Point the welding on the surface at a 10-15° angle.
Preheating Metals: Preheating can lessen the risk of uneven welds and cracking for metals with high thermal conductivity. Preheating offers a uniform temperature all over the surface of the materials. Thus, it maintains the required weld pool and welds great on aluminum and copper.
Selecting the Electrode: Tungsten welding electrodes influence arc stability and accuracy. There are commonly two types of electrodes:
- Thoriated Tungsten
- Lanthanated Tungsten
Thoriated tungsten is commonly used for thick materials and Lanthanated tungsten is used for thin materials like aluminum.
YesWelder: Your Professional Welding Machine Partner
Learning about welding techniques, required heat input, and suitable filler materials helps achieve high-quality welds. What technique and how much heat are required for a weld is determined by melting point. So, getting an idea about the melting point should be considered very carefully.
And above all these, you should have the right equipment for a successful welding job. Here comes YesWelder, a professional-grade supplier that offers TIG welding machines designed for the best performance. With a commitment to customer satisfaction, YesWelder is the trusted companion for all your welding needs.
FAQs
Why is the melting point vital when welding dissimilar metals?
Appropriate heat distribution is important in TIG welding. Understanding the melting points for different metals ensures the required heat for the project. It helps avoid premature melting of one metal and prevent insecure joining.
How does the melting temperature of filler metal influence welding?
The melting heat of a filler metal should be lower than the base metal. It ensures proper joints between two metals and reduces weld defects.
Does shielding gas affect the melting point in TIG welding?
Argon and helium are commonly used as shielding gas in TIG welding. These gases don’t change the melting temperature but prevent oxidation. As a result, the weld gets perfection without making any uneven marks on the surface.
Can You Use TIG welding for metals with high melting points?
A skilled welder can use TIG welding for metals with high melting temperatures like tungsten. This metal has a melting point about 3,400°C. To work with this type of metal, specialized equipment and methods should be applied.
Does welding speed affect the melting temperature?
Faster or slower welding speeds don’t offer good results while welding. Faster speeds reduce heat input which results in weak melting and improper fusion of the metals.