Cutting metal efficiently and accurately is a common challenge in various industries. Traditional methods often result in uneven edges, slower cutting speeds, and greater heat-affected zones, leading to material distortion. Plasma cutting addresses these issues by offering high-speed, precise cuts with minimal heat impact, making it ideal for thin and thick materials.
Plasma cutters create clean, consistent cuts using a superheated, electrically ionized gas. This method enhances productivity and reduces material waste, ensuring optimal application performance. Understanding the right techniques and maintenance practices can significantly improve plasma-cutting results.
How to Choose the Right Plasma Cutter
Choosing the right plasma cutter is essential for achieving optimal cutting performance. Several factors should be considered to ensure the plasma cutter meets your needs.
Material and Thickness
The type and thickness of the material you plan to cut are primary considerations. Plasma cutters vary in their capacity to cut different metals and thicknesses. For instance, cutting thin-gauge aluminum requires less power than thick steel plates. The cutter’s amperage rating directly influences its ability to handle various material thicknesses. Machines with higher amperage can cut through thicker materials more efficiently, while lower-amperage machines are suitable for thinner materials .
For example, a machine rated at 40 amps might efficiently cut through 1/2-inch steel but need help with thicker materials. Conversely, a 60-amp plasma cutter can handle thicker steel and other tough metals, providing more versatility for different projects. Always refer to the manufacturer’s specifications to match the machine’s capabilities with your cutting requirements.
Cutting Speed and Quality
Cutting speed is another critical factor. It is typically measured in inches per minute (IPM) and determines how fast the machine can cut through a given material thickness. Faster cutting speeds are beneficial for increasing productivity, especially in industrial applications where time efficiency is crucial. However, cutting speed should maintain the quality of the cut. High-quality plasma cutters balance speed with precision, ensuring smooth, clean edges with minimal dross (residual waste material). Quality cuts are characterized by smooth edges requiring minimal post-cut processing.
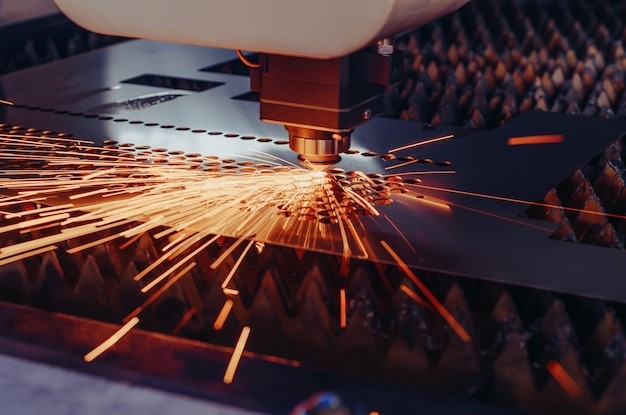
Duty Cycle
This refers to the time the machine can operate continuously before needing to cool down. A higher duty cycle benefits long-cutting tasks and prevents the machine from overheating.
Portability
For jobs requiring movement between different locations, the weight and size of the plasma cutter are important. Compact and lightweight models are easier to transport and use in various settings.
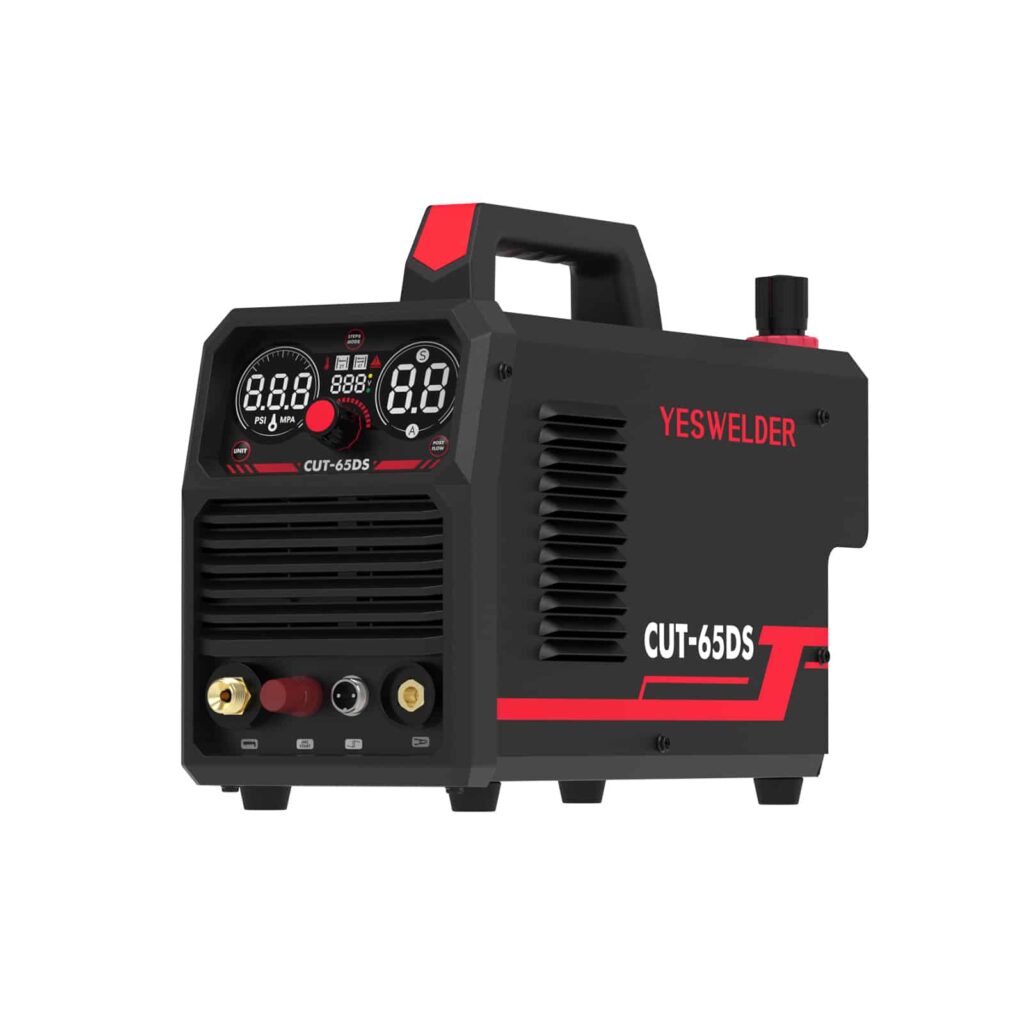
Power Supply
Consider whether the plasma cutter requires a single-phase or three-phase power supply. Some models can switch between 120V and 240V, offering greater flexibility for different work environments.
Air Supply
Plasma cutters typically use compressed air or nitrogen. Ensure that the air supply is clean and dry to prevent damage to the machine and ensure consistent performance.
Consider these Factors for Maximum Benefits
Plasma Cutter Factors | Description | Benefits |
Material and Thickness | Types and thickness of metals the cutter can handle. | Provides clean cuts for various materials. |
Cutting Speed | Rate of cutting through material, measured in IPM. | Increases productivity with faster cuts. |
Duty Cycle | Percentage of operational time before overheating. | Allows extended use without interruption. |
Portability | Weight and size affecting transport and use. | Facilitates use in various locations. |
Power Supply | Type and range of power required. | Ensures compatibility with power sources. |
Air Supply | Quality and type of air or gas used. | Optimizes cutting conditions and prevents contamination. |
Consumables Quality | Durability and effectiveness of consumable parts. | Reduces replacement frequency and maintains quality. |
Ease of Use | User-friendly features and ease of setup. | Enhances user experience and minimizes setup time. |
Maintenance Requirements | Level of maintenance needed. | Prolongs lifespan and ensures consistent performance. |
Safety Features | Protects users and equipment, reducing risks. | Protects user and equipment, reducing risks. |
Plasma Cutting Tips for Best Performance
Optimizing the performance of a plasma cutter involves several best practices, from setup and calibration to maintaining a consistent cutting speed and ensuring safety. These tips can help you achieve cleaner cuts and prolong the lifespan of your equipment.
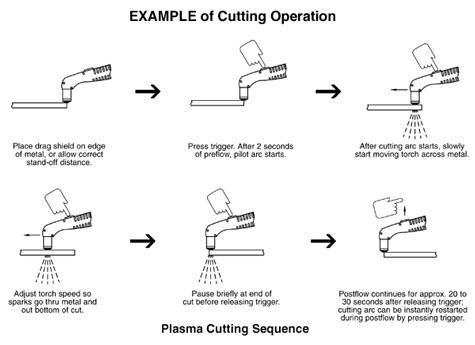
Setup and Calibration
Proper setup and calibration are crucial for effective plasma cutting. Here are some key steps:
1. Ground Clamp Connection: Attach the ground clamp to a clean, rust-free part of the metal. Grind off any rust or paint to ensure a good electrical connection.
2. Cable Inspection: Regularly check your cables for wear and tear. Replace any damaged cables to maintain optimal electrical flow.
3. Amperage Settings: Start with a high amperage setting and make a few practice cuts. Adjust the amperage based on your travel speed and the thickness of the material. Too high an amperage or slow speed can cause excessive heat and dross build-up.
Maintaining Proper Distance
Keeping the right distance between the plasma torch and the workpiece is essential for clean cuts.
1. Standoff Distance: Maintain a standoff distance of 1/16 to 1/8 inch. Using a drag shield can help maintain this distance consistently.
2. Torch Angle: Keep the torch perpendicular to the workpiece. An angled torch can lead to uneven cuts and increased consumable wear
Consistent Cutting Speed
Maintaining a consistent cutting speed is key to achieving quality cuts.
1. Practice Movements: Before starting a cut, practice your movements along the cutting path. This helps ensure smooth and continuous cuts without stops and starts, which can cause irregularities.
2. Adjust Speed for Material Thickness: Faster speeds are better for thinner materials, while thicker materials may require slower, more controlled movements. Adjust your speed to ensure the cutting sparks emerge from the bottom of the workpiece.
Safety Measures
Safety is paramount when operating a plasma cutter, here are some safety tips:
1. Wear Protective Gear: Always wear appropriate safety gear, including eye protection, gloves, and long sleeves to protect against sparks and heat.
2. Ventilation: Ensure your workspace is well-ventilated to avoid inhaling harmful fumes generated during the cutting process
3. Fire Safety: Keep flammable materials away from the cutting area. Have a fire extinguisher nearby in case of emergencies.
Additional Basic Tips
Consider these tips to improve your plasma-cutting experience further:
1. Consumable Management: Regularly check and replace consumables such as nozzles and electrodes. Worn consumables can reduce cut quality and increase the likelihood of torch failure.
2. Sample Cuts: Make sample cuts on the same type of material you’ll be working with to ensure the settings are correct and the cut quality is optimal
3. Proper Storage: Store your plasma cutter and consumables in a dry, clean area to prevent rust and damage. Proper storage extends the life of your equipment.
4. Cutting Guides: Use cutting guides like straight edges or templates to achieve straight and precise cuts. Guides help maintain a steady hand and improve cut quality.
5. Air Quality: Ensure your air supply is clean and dry. Moisture in the air can cause issues with the plasma cutter’s performance and reduce the lifespan of consumables.
Maintenance of Plasma Cutters
Proper maintenance of plasma cutters is essential to ensure their longevity and optimal performance. Regular inspection, cleaning, and appropriate storage can prevent costly repairs and downtime. Here are key practices for maintaining your plasma cutter:
Regular Inspection
Regular inspection is crucial for identifying wear and tear before it leads to significant issues. Here are some inspection tips:
- Check Consumables: Inspect the electrode, nozzle, and shield cap for wear. Replacing these parts before they are too worn out can prevent damage to the torch and ensure consistent cutting quality.
- Inspect Cables and Connections: Regularly check the cables and connections for signs of wear, fraying, or loose connections. Damaged cables can affect performance and pose safety risks.
- Examine the Ground Clamp: Ensure the ground clamp is secure and makes good contact with the workpiece. A good ground connection can lead to consistent cuts and increased consumable wear.
- Monitor the Air Supply: Check the air filter and ensure it is clean. Contaminated air can damage the torch and affect cutting quality. Replace filters as needed to maintain clean airflow.
Cleaning and Storage
Cleaning and proper storage of the plasma cutter can significantly extend its lifespan. Follow these guidelines:
- Clean the Torch: After each use, clean the torch to remove any metal dust and debris. Use a soft brush or compressed air to clean the inside of the torch head and remove any build-up on the electrode and nozzle.
- Store Consumables Properly: Keep consumables in a clean, dry place to prevent contamination and corrosion. Organize them in a way that allows you to identify and access the parts you need easily.
- Maintain the Air Compressor: Ensure the air compressor used with the plasma cutter is well-maintained. Drain the moisture from the air tank regularly and check the oil level if it is an oil-lubricated compressor.
Protect the Plasma Cutter
- Store the plasma cutter in a dry, dust-free environment.
- Use a cover to protect it from dust and debris when not in use.
- Avoid storing it in damp or corrosive environments, as moisture can damage electronic components.
Additional Maintenance Tips
- Use Quality Consumables: Investing in high-quality consumables can improve cutting performance and extend the life of your plasma cutter. Cheaper consumables may wear out faster and cause more frequent replacements.
- Monitor Duty Cycle: Be mindful of the plasma cutter’s duty cycle. Allow the machine to cool down after heavy use to prevent overheating and damage to internal components.
- Software Updates: Ensure that your plasma cutter has current software or firmware. Manufacturers often release updates that can improve performance and fix bugs.
Final Thoughts
Plasma cutting is an efficient and versatile method for cutting various metals. By selecting the right cutter, maintaining it properly, and following best practices, you can achieve high-quality cuts and extend the life of your equipment. Regular inspections, cleaning, and using the correct settings will ensure consistent performance and safety. Investing time in understanding your plasma cutter’s capabilities and maintenance needs will improve productivity and cost savings.
FAQs
What materials can be cut with a plasma cutter?
Plasma cutters can cut various metals, including steel, stainless steel, aluminum, copper, brass, and more. The process is effective for thin and thick materials, making it versatile for different applications.
How do I choose the right plasma cutter for my needs?
Consider the material type and thickness you often cut, the required cutting speed, and the cutter’s duty cycle. Additionally, consider portability, power supply options, and the machine’s overall size and weight
What safety measures should be taken while using a plasma cutter?
Always wear appropriate safety gear, such as gloves, eye protection, and long-sleeve clothing. Ensure proper ventilation to avoid inhaling fumes, and keep flammable materials away from the cutting area
How often should I replace plasma cutter consumables?
Replace consumables like electrodes and nozzles when you notice a drop in cutting quality or increased wear. Regular inspection of these parts helps maintain optimal performance and prevents damage to the torch.